Are you interested in joining metal without welding? Welding can be intimidating for beginners, requiring specialized equipment and training.
How to join metal without welding can be a practical skill for many projects, whether you’re working on a hobby, a repair, or a professional task. While welding is a common technique used to fuse metal parts, it requires specific equipment and expertise.
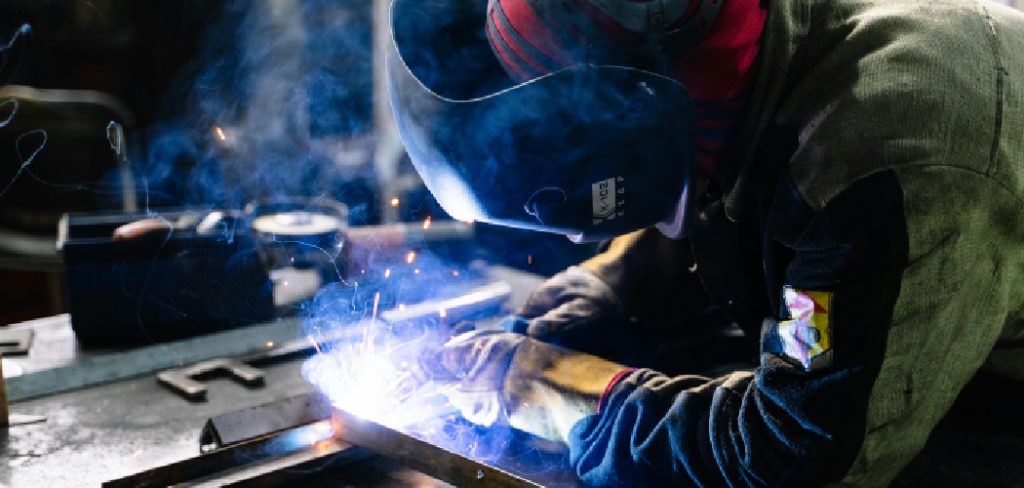
Fortunately, several alternative methods can be employed to join metal effectively and securely without the need for welding. These techniques often involve materials and tools that are more accessible to the average person, providing flexibility and convenience.
By exploring methods such as brazing, riveting, and adhesives, you can achieve strong and lasting connections for a variety of applications.
What Will You Need?
Before you begin joining metal without welding, gathering all the necessary materials and tools is essential. The required supplies may vary depending on the specific method you choose, but here are some general items that will likely be needed:
- Metal pieces to be joined
- Appropriate filler material (such as braze rods or rivets)
- Flux or adhesive (if applicable)
- Heat source (e.g., blowtorch, heat gun)
- Protective gear (e.g., safety glasses, gloves)
- Clamps or vise grips (for holding pieces in place)
Having a clear workspace with proper ventilation is also recommended, as some methods may involve fumes or smoke.
10 Easy Steps on How to Join Metal Without Welding
Step 1. Prepare the Metal Surfaces
Ensure that the metal surfaces you intend to join are clean and smooth, as any dirt, grease, or rust can severely impact the strength of the joint. Start by wiping down the metal with a degreaser or a gentle cleaning solution to remove any surface contaminants. Next, if the metal is rusty or oxidized, use a wire brush or sandpaper to clear away the top layer, revealing fresh, unblemished metal beneath.
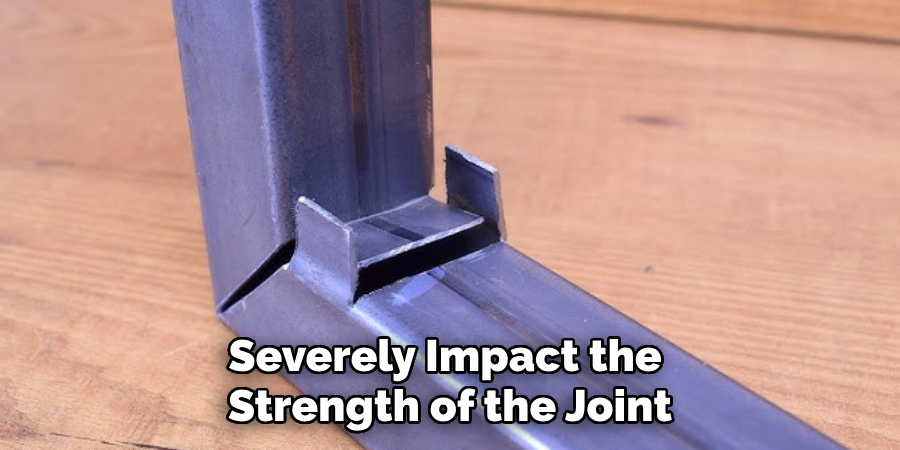
This step is crucial as it ensures the surfaces are primed to form a solid bond with the filler material or adhesive. Once cleaned and smoothed, dry the metal thoroughly to prevent any moisture from hindering the joining process. Preparing your metal properly will set a strong foundation for a successful project.
Step 2. Select the Appropriate Joining Method
Once the metal surfaces have been adequately prepared, the next step is to select the most suitable method for joining the metal. The choice of method depends on the materials at hand, the type of metals being joined, and the strength required for the finished product.
Standard methods include brazing using a filler metal that melts at a lower temperature than the base metals, riveting, which involves fastening metals with rivet pins, and using metal adhesives engineered for robust bonding applications. Consider the requirements of your project and choose a method that will provide the best balance between ease of use and the durability of the joint. Gathering materials specific to your selected method before proceeding further is also essential.
Step 3. Align the Metal Pieces
After selecting your joining method, carefully align the metal pieces to ensure a proper fit and strong connection. Position the metal parts as precisely as possible, using clamps or vise grips to hold them securely. Correct alignment is critical, as even slight misalignments can weaken the joint or cause the pieces not to fit together correctly.
Take the time to double-check the alignment from different angles, ensuring that the edges are flush and the surfaces are in full contact where the joint will be made. This careful preparation ensures that the joining process will proceed smoothly, resulting in a durable and seamless connection.
Step 4. Apply Flux or Adhesive
Depending on the chosen joining method, you may need to apply flux or adhesive to the prepared metal surfaces. If you are brazing, use flux to prevent oxidation and facilitate the flow of the filler metal. Apply the flux evenly to the joint area, ensuring complete coverage for optimal bonding. Select a product suitable for metal bonding and apply it according to the manufacturer’s instructions when using adhesives.
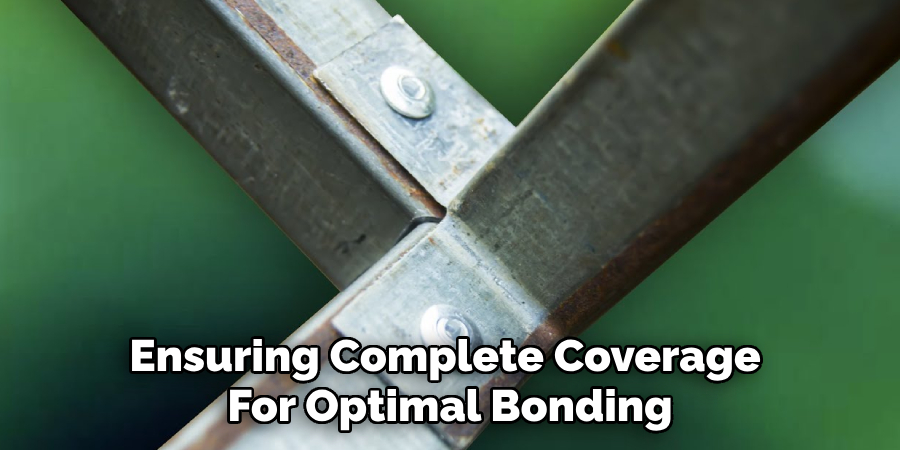
Typically, this involves covering both surfaces with a uniform layer and avoiding excess, which could affect the joint’s appearance or strength. Proper application of flux or adhesive is essential to ensure a robust and long-lasting joint, so take the time to apply it carefully and thoroughly before proceeding to the next step.
Step 5. Secure the Joint
Once the flux or adhesive has been applied and before heating or pressing begins, ensure that the metal pieces remain firmly in place. Use clamps or vise grips to hold the pieces securely, preserving the initial alignment achieved in the previous step. Ensure the clamps are tightened sufficiently to prevent movement, which is crucial for ensuring a clean and robust bond.
If you’re using an adhesive, refer to the product instructions for recommended clamping time to allow the glue to cure correctly. In the case of brazing, the heated filler metal will naturally align the pieces as it flows into the joint, but initial clamping ensures that surfaces remain in optimal contact. Securing the joint effectively at this stage is critical to a successful and durable metal connection.
Step 6. Heat the Joint (If Brazing)
For those opting for brazing as their joining method, heating the joint is essential in ensuring a solid bond. Use a blowtorch or an appropriate heat source to apply concentrated heat to the joint area, focusing on the metal pieces and the filler material. The goal is to reach a temperature where the filler metal melts and flows between the aligned metal surfaces, creating a robust connection upon cooling.
Be sure to apply the heat evenly, moving the torch in a slightly circular motion to prevent overheating one area. Pay attention to the color change in the metals, as it indicates the appropriate temperature range is achieved. Proper heating allows the filler metal to seamlessly cover the gaps, resulting in a solid, enduring joint. Once the filler metal has flowed and settled, will enable the joint to cool naturally before disturbing the setup, ensuring a durable and resilient bond forms as the filler solidifies.
Step 7. Allow the Joint to Cool
After the brazing process and heating of the joint is complete, it is imperative to let it cool down naturally. Rapid cooling, such as through immersion in water or using fans, can induce thermal shock, which may compromise the integrity of the joint or cause cracks to form.
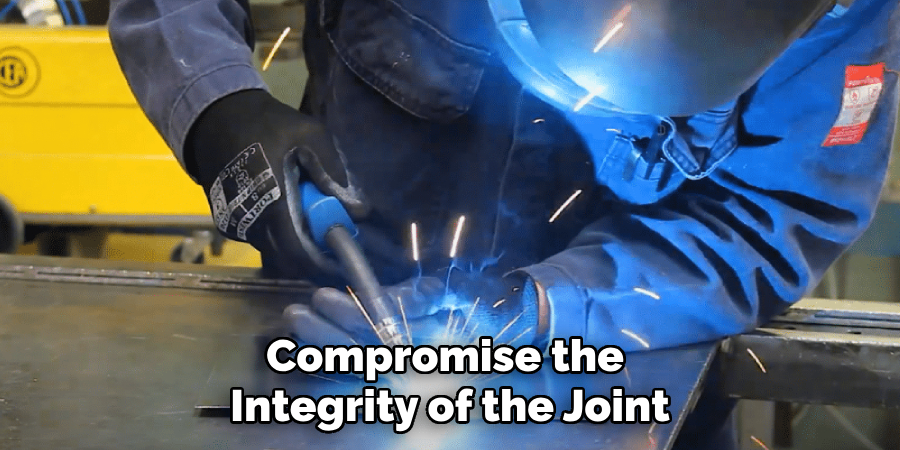
Allowing the metal to cool slowly and uniformly ensures that the filler material solidifies appropriately and that the bond between the pieces of metal remains solid and durable. During this cooling phase, do not attempt to move or adjust the metal pieces, as this could disturb the alignment or weaken the newly formed bond.
Step 8. Inspect the Joint
Once the joint has cooled completely, thoroughly inspect the connection to ensure it is solid and secure. Look for any visible gaps, misalignments, or weak spots that could indicate a faulty bond. Use a magnifying glass to scrutinize smaller areas that might not be visible to the naked eye.
Additionally, perform a gentle stress test by applying slight pressure or force to the metal pieces, ensuring they do not budge or show signs of instability. If any issues are detected, consider reheating the joint, applying additional filler material, or re-aligning the pieces as needed. A careful inspection is crucial to confirm the successful completion of the joining process and to ensure the longevity and durability of the metal project.
Step 9. Finish the Surface
After confirming a strong and secure joint, proceed to finish the surface of the metal to enhance its appearance and protect it from corrosion. Begin by cleaning the area to remove any residual flux, adhesive, or dirt that may have accumulated during the joining process. Use a wire brush or steel wool to gently polish the joint, removing any rough edges or excess filler material.
For a smoother finish, consider applying fine-grit sandpaper to blend the joint seamlessly with the rest of the metal surface. If necessary, use a suitable primer and paint to coat the metal, providing both aesthetic appeal and a protective barrier against environmental factors. Properly finishing the surface enhances the project’s visual quality and ensures its longevity and resistance to wear and tear.
Step 10. Test the Joint
With the metal surface now finished and polished, the final step is to test the joint under actual conditions or simulated scenarios. This ensures the joint can withstand the intended load and stress. Begin by applying incremental pressure to assess the joint’s strength, starting with light force and gradually increasing to simulate real-world conditions.
If applicable, use testing equipment to measure stress tolerance or perform functional tests in the environment where the metal will be used. Observe the joint for signs of fatigue, cracking, or separation during testing. If the joint passes these tests without issue, it confirms the reliability and effectiveness of the joining process.
By following these ten steps, you can achieve a strong and lasting joint between metal pieces using either brazing or adhesive methods.
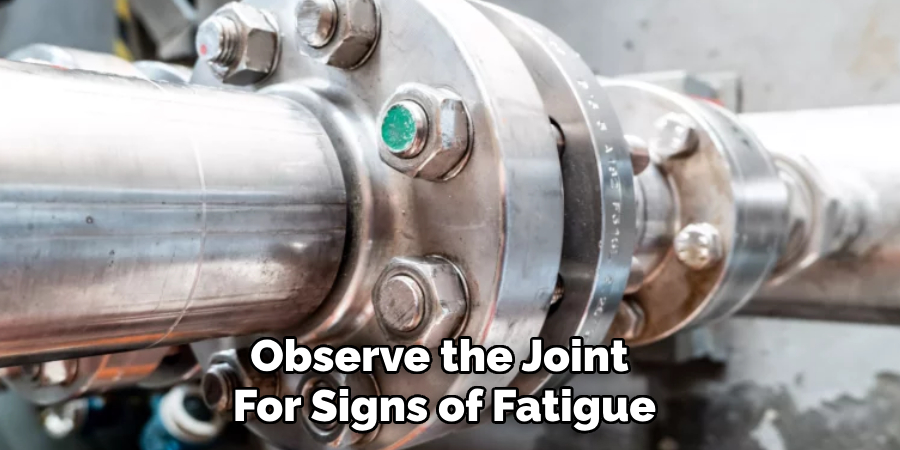
Conclusion
In conclusion, how to join metal without welding is feasible through methods such as brazing or using adhesives, each offering distinctive advantages.
These techniques allow for strong and lasting connections, mainly when extensive heat or specialized equipment for traditional welding is unavailable or suitable.
You can create durable, reliable bonds by diligently following the outlined steps—preparing the metal, ensuring proper alignment, using clamps for stabilization, applying heat or adhesives correctly, and finishing the joint carefully. These versatile methods can be adapted to different metal types and project requirements.
With attentiveness and precision, brazing and adhesive techniques serve as valuable alternatives to conventional welding, empowering professionals and DIY enthusiasts to undertake metal joining tasks confidently.
Edmund Sumlin is a skilled author for Metal Fixes, bringing 6 years of expertise in crafting a wide range of metal fixtures. With a strong background in metalwork, Edmund’s knowledge spans various types of fixtures, from decorative pieces to functional hardware, blending precision with creativity. His passion for metalworking and design has made him a trusted resource in the industry.
Professional Focus:
- Expert in Metal Fixtures : Edmund aesthetic specializes in creating durable and innovative metal fixtures, offering both appeal and functionality. His work reflects a deep understanding of metalworking techniques and materials.
- Sustainability Advocate : He is dedicated to using sustainable practices, ensuring that every fixture is crafted with eco-friendly methods while maintaining high-quality standards.
In his writing for Metal Fixes, Edmund provides valuable insights into the latest trends, techniques, and practical advice for those passionate about metal fixtures, whether they are professionals or DIY enthusiasts. His focus on combining artistry with engineering helps others discover the true potential of metal in design.