Industrial irons are vital tools in many manufacturing and textile settings, designed to withstand heavy-duty usage and provide consistent results. However, like any machinery, they can encounter issues over time that may affect their performance.
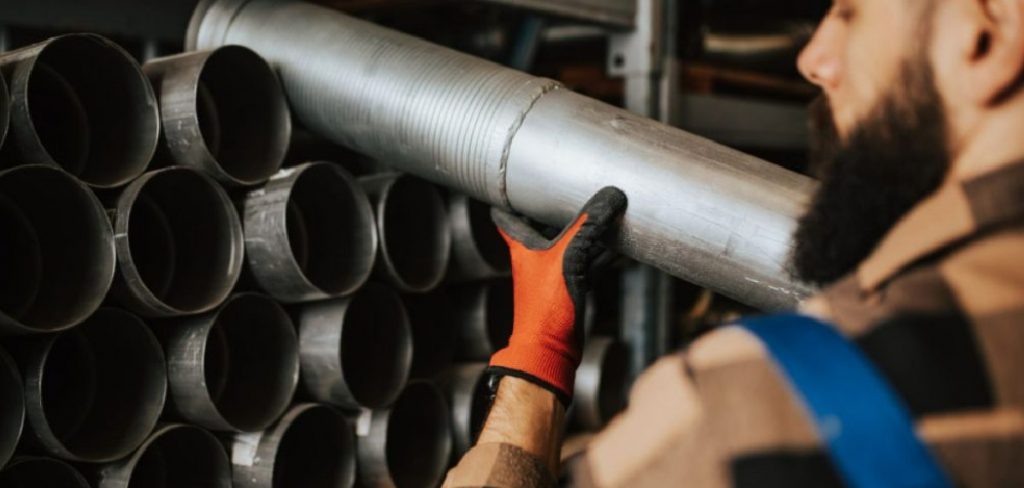
This guide will walk you through the most common problems with industrial irons, offering step-by-step instructions on how to fix industrial iron. Whether you’re dealing with inconsistent heat, steam malfunctions, or electrical problems, understanding the basics of industrial iron maintenance can save time and reduce downtime, ensuring your operations run smoothly.
Importance of Timely Repairs
Timely repairs of industrial irons are crucial in maintaining the efficiency and productivity of manufacturing operations. Addressing issues as they arise prevents minor problems from escalating into significant breakdowns that can halt production completely.
Regular maintenance and prompt repair work not only extend the lifespan of the machinery but also ensure consistent performance and quality output. Additionally, timely repairs contribute to workplace safety by reducing the risk of equipment malfunctions that could lead to accidents. By proactively servicing industrial irons, businesses can minimize downtime, optimize operational flow, and safeguard their investments in high-quality equipment.
Common Problems with Industrial Irons
Industrial irons, being pivotal in manufacturing and textile industries, can develop several issues that may hinder their performance. One frequent problem is inconsistent heat levels, where the iron fails to maintain a steady temperature, leading to uneven pressing results. This could be due to a faulty thermostat or heating element. Another common issue is steam malfunction, which can occur if the steam holes become clogged with mineral deposits or if there’s a problem with the water reservoir or pump system.
Electrical problems also arise occasionally, often related to wear and tear of wiring or faulty connections. Additionally, mechanical parts like levers and knobs can become stiff or unresponsive due to prolonged use without proper lubrication. Recognizing these common problems early and addressing them with appropriate repair or maintenance can prevent more severe issues from developing.
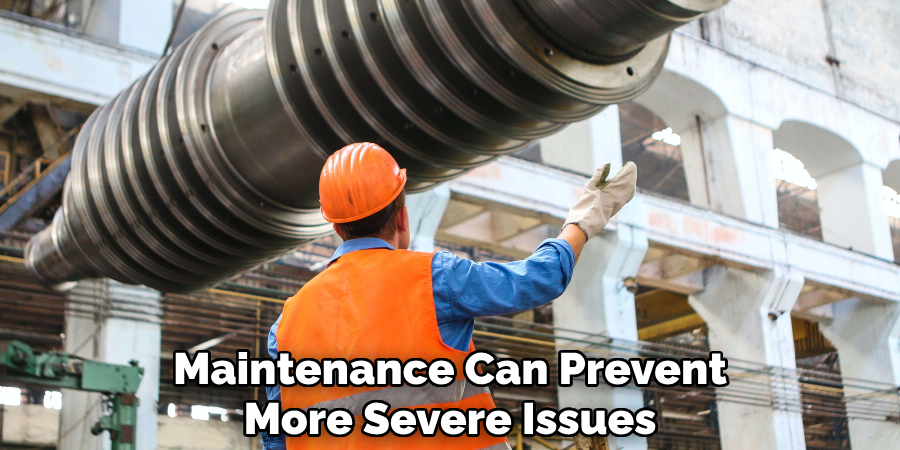
Tools and Materials Needed
Before starting any maintenance or repair work on industrial irons, it is essential to gather the necessary tools and materials. This ensures the process is smooth and efficient, minimizing the risk of damage or injury. Here is a list of recommended items:
- Screwdrivers (Phillips and flathead): For opening the iron’s casing and accessing internal components.
- Multimeter: To test electrical connections and diagnose potential wiring issues.
- Thermal paste: Useful for replacing or enhancing the heat-transfer capabilities of the iron’s heating elements.
- Cleaning brush or needle: To clean and unclog steam holes from mineral deposits.
- Lubricant: For mechanical parts that have become stiff over time due to lack of lubrication.
- Replacement parts: Such as thermostats, heating elements, or wiring, based on the diagnosed issues.
- Safety gear: Including gloves and safety goggles, to protect against electrical hazards and sharp tools.
Having these tools and materials on hand will equip you to efficiently address the most common problems encountered with industrial irons, ensuring a quicker return to full operational capacity.
10 Effective Methods on How to Fix Industrial Iron
1. Assess and Clean External Parts
Dust and debris can accumulate, hindering the performance of your machine. Regularly inspect the exterior and clean areas like vents and filters. Removing these obstructions ensures efficient airflow, preventing potential overheating.
2. Check Electrical Connections
Loose or corroded electrical connections are common culprits for malfunction. Conduct regular inspections using a multimeter to ensure all connections are tight and corrosion-free. Replacing worn-out wires can prevent costly electrical failures, enhancing safety and equipment longevity.
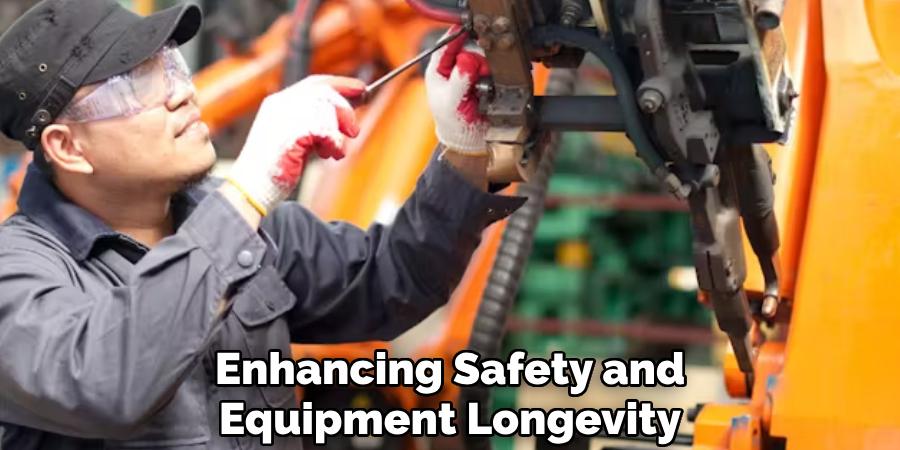
3. Monitor Temperature Controls
Industrial irons rely on precise temperature settings for optimal results. Frequently verify the accuracy of temperature controls. Use a pyrometer to check the actual heat against the set temperature, and recalibrate if necessary to maintain quality standards in your operations.
4. Inspect the Heating Element
A malfunctioning heating element can severely affect performance. Signs of failure include inconsistent heat patterns or unresponsive temperature settings. Use an ohmmeter to test the element’s resistance. If readings fall outside the manufacturer’s spec, replacement is necessary to restore efficiency.
5. Lubricate Moving Parts
To minimize friction and wear, apply appropriate lubricants to pivotal moving components. This simple step reduces wear and extends the lifespan of the machine. Select lubrication products based on your manufacturer’s guidelines to avoid damaging parts.
6. Adjust the Pressure Mechanism
Proper pressure settings are essential for ensuring quality outcomes. Regularly inspect and adjust the pressure settings to meet specific material demands. This can help avoid warping or inefficient processing, maintaining the integrity of materials handled.
7. Conduct Routine Software Updates
For machines featuring digital controls, ensure software and firmware are up-to-date. This can resolve bugs and bring enhanced operational features. Staying updated not only aligns machines with current technology standards but also optimizes their performance.
8. Analyze Feed and Exit Systems
Issues with material feeding or retrieval can create bottlenecks. Routinely check rollers, belts, and guides for wear or misalignment. Correctly adjusted and maintained feeding systems ensure smooth operation and uniform results in production.
9. Replace Worn Out Components
Halt unexpected downtimes by replacing parts as they show wear. Look out for signs such as cracks, rust, or brittleness, especially under heavy-use equipment. Keeping a stock of essential components, like bearings and gaskets, can reduce wait times in critical scenarios.
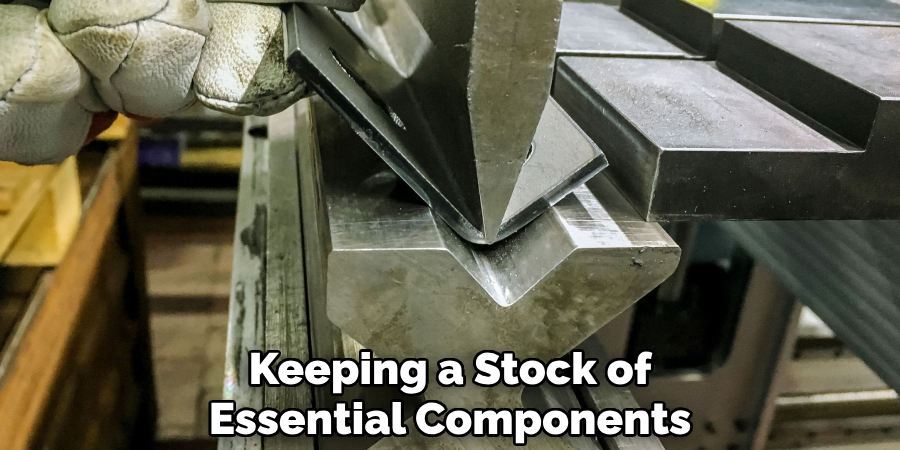
10. Schedule Regular Professional Maintenance
Even for seasoned DIY enthusiasts or industrial technicians, leveraging professional maintenance services can uncover underlying issues not immediately visible. Scheduled expert evaluations prolong machine life, fitting seamlessly with periodic checks and timely repairs.
Maintenance and Upkeep
Regular maintenance and upkeep play a crucial role in extending the lifespan of industrial irons and ensuring they operate at peak efficiency. By establishing a routine maintenance schedule, potential problems can be identified and rectified before they escalate. Begin by creating a maintenance log to track each inspection and any repairs conducted.
This log proves invaluable in identifying patterns of recurring issues or components needing frequent attention. Additionally, train personnel in handling basic maintenance tasks, such as cleaning or lubrication, to minimize reliance on external services for minor issues. Periodically, conduct comprehensive inspections to assess the condition of all mechanical, electrical, and thermal components.
Moreover, stay updated with manufacturer recommendations and updates that may enhance machine performance. Finally, ensure all safety protocols are adhered to during maintenance activities, safeguarding both the equipment and operators. By prioritizing consistent care and attention, a culture of operational excellence and safety is fostered, resulting in reduced downtime and optimized productivity.
Troubleshooting Common Issues
Even with routine maintenance, industrial irons might encounter various operational issues. Here are some common problems and the steps to troubleshoot them effectively:
- Iron Not Heating: If the iron fails to heat, first check the power supply and ensure it is adequately connected. Inspect the thermostat and heating element for signs of wear or damage. Use a multimeter to test the wiring and electrical connections.
- Water Leaks: Water leaks may arise from cracked water tanks or seals. Examine the water reservoir for any visible cracks and replace damaged components. Check that all seals and gaskets are intact and properly fitted to prevent leakage.
- Inconsistent Steam Output: Variation in steam levels often relates to blocked steam vents. Use a cleaning brush or needle to clear mineral deposits from the steam holes. Decalcify the iron using a vinegar-water solution to dissolve accumulated deposits further.
- Sticking to Fabric: If the iron sticks to fabric, the soleplate might be dirty or damaged. Clean the soleplate using a suitable cleaning agent and inspect it for scratches or residue buildup. Consider replacing it if damage is severe.
- Irregular Temperature Fluctuations: Unstable temperature readings can lead to fabric damage. Check and recalibrate the thermostat or sensors if necessary. Ensure the heating element is functioning within the specified range by using an ohmmeter.
By understanding these common issues and addressing them promptly, users can maintain the optimal performance of their industrial irons and reduce the likelihood of long-term damage.
When to Contact a Professional
While many issues with industrial irons can be resolved through routine maintenance and troubleshooting, certain situations necessitate professional intervention. Complex electrical problems, such as persistent short circuits or erratic power failures, require the expertise of a qualified technician to safely diagnose and repair. Additionally, if an iron consistently underperforms even after regular maintenance, it may indicate an underlying issue that needs professional evaluation.
Persistent leaks, especially those stemming from deep within the iron’s components, or irreparable damage to vital parts, should also be assessed by a specialist. Furthermore, when new components must be installed or advanced updates and calibrations are needed, professional service can ensure proper integration and prevent potential breakdowns. In these cases, seeking professional support not only restores the equipment’s functionality but also minimizes downtime and safeguards against further complications.
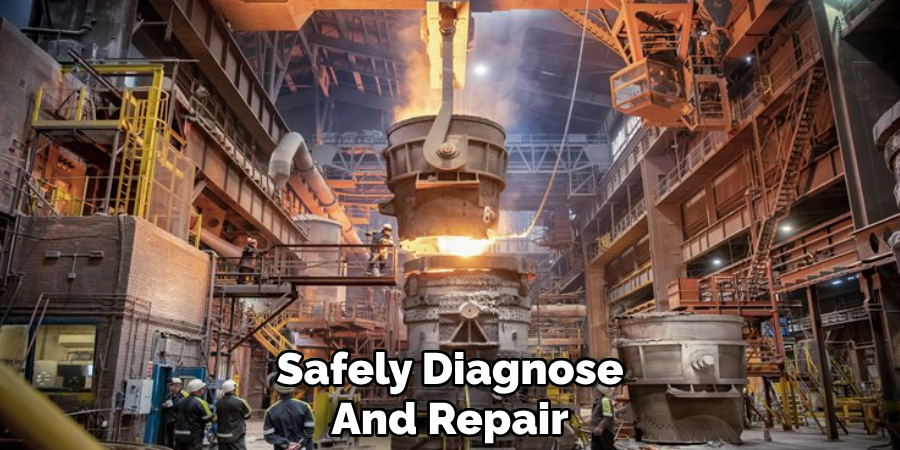
Conclusion
Maintaining industrial irons requires a proactive approach that integrates regular maintenance, troubleshooting, and professional assistance when necessary. By adhering to scheduled maintenance routines and addressing common operational issues quickly, businesses can significantly extend the lifespan of their equipment while ensuring efficient and safe operation.
Training personnel to conduct basic maintenance tasks contributes to a culture of diligence and readiness, reducing dependence on external services for minor issues. In recognizing the limit of internal troubleshooting and knowing when to seek professional help, organizations can prevent small issues from escalating into costly repairs. Thanks for reading, and we hope this has given you some inspiration on how to fix industrial iron!
Edmund Sumlin is a skilled author for Metal Fixes, bringing 6 years of expertise in crafting a wide range of metal fixtures. With a strong background in metalwork, Edmund’s knowledge spans various types of fixtures, from decorative pieces to functional hardware, blending precision with creativity. His passion for metalworking and design has made him a trusted resource in the industry.
Professional Focus:
- Expert in Metal Fixtures : Edmund aesthetic specializes in creating durable and innovative metal fixtures, offering both appeal and functionality. His work reflects a deep understanding of metalworking techniques and materials.
- Sustainability Advocate : He is dedicated to using sustainable practices, ensuring that every fixture is crafted with eco-friendly methods while maintaining high-quality standards.
In his writing for Metal Fixes, Edmund provides valuable insights into the latest trends, techniques, and practical advice for those passionate about metal fixtures, whether they are professionals or DIY enthusiasts. His focus on combining artistry with engineering helps others discover the true potential of metal in design.