Using a no-go gauge is essential in quality control and precision measurement, particularly in manufacturing and engineering contexts.
No-go gauges are designed to assess the tolerances of a particular object or component, ensuring they fall within specified limits. This simple yet effective tool helps identify any deviations from the desired specifications, which can prevent potential failures and maintain the consistency of production. Understanding how to use a no-go gauge correctly is crucial for ensuring that each manufactured piece meets stringent quality standards, minimizing errors and optimizing the overall production process.
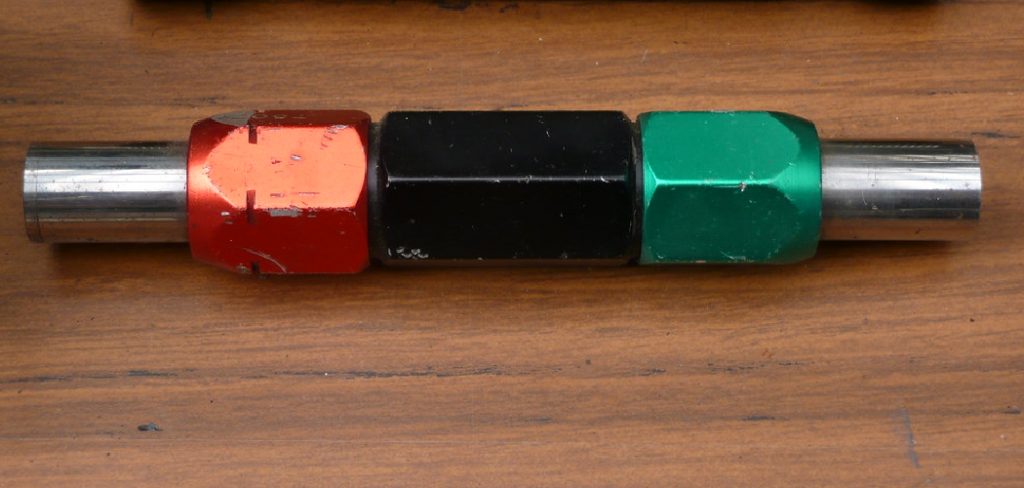
In this guide on how to use a no go gauge, we will outline the steps and best practices for effectively utilizing a no-go gauge to uphold high levels of accuracy and reliability in your measurements.
What Will You Need?
Before using a no-go gauge, you must gather a few essential items to ensure the process runs smoothly. These include:
- A no-go gauge (specifically designed for your application or industry)
- A go gauge (used in conjunction with the no-go gauge)
- The object or component being measured
- Calipers or micrometers for taking precise measurements
- Any necessary safety equipment, such as gloves and eye protection
Once you have these items ready, you can begin the process of using a no-go gauge.
10 Easy Steps on How to Use a No Go Gauge
Step 1: Inspect the No Go Gauge
Before you proceed with any measurements, it is crucial to thoroughly inspect the no-go gauge for any signs of wear or damage. Begin by examining the gauge for visible scratches, dents, or other forms of degradation that might affect its accuracy. Check that the gauge’s surface is clean and free from any debris or contaminants, as these could lead to incorrect readings. Ensure that the gauge is calibrated and its dimensions align with the specific tolerances required for your application. Proper maintenance and handling are essential, as even a small imperfection can lead to significant measurement discrepancies. If the gauge appears compromised, it is best to replace or repair it to maintain precision in your quality control processes.
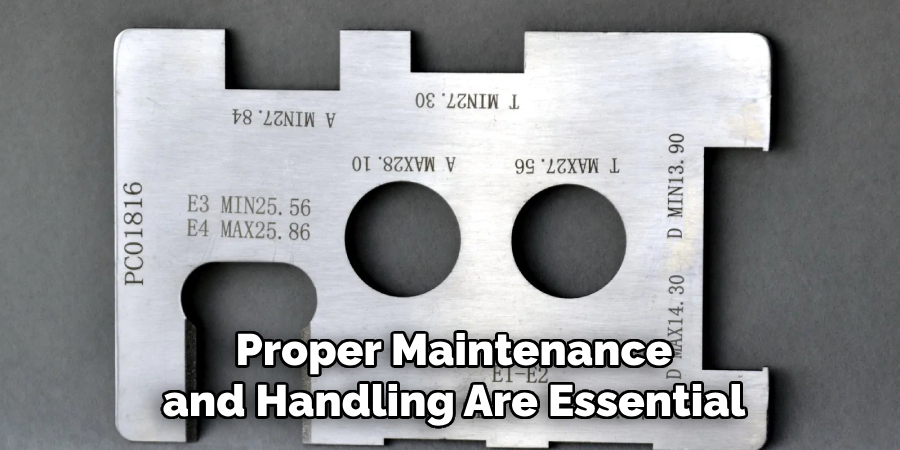
Step 2: Prepare the Object or Component
Before proceeding with the measurement process, ensure that the object or component you are testing is properly prepared. Clean the surface thoroughly to remove any dust, grease, or foreign particles that may interfere with the measurement’s accuracy. Check for any visible defects or irregularities that might affect the test results. Place the object in a stable position where it won’t move during the measurement. This preparation step is vital to achieving precise and consistent results and helps maintain the integrity of the evaluation process.
Step 3: Use the Go Gauge First
Begin the measurement process by using the go gauge on the object or component you are testing. The go gauge is designed to ensure that the component’s dimensions fall within the lower limit of the acceptable tolerance range. Gently insert or apply the go gauge to the feature being measured. If the gauge fits smoothly without any resistance or forceful effort, the component meets the minimum required specifications. Using the go gauge first serves as a preliminary check, setting the stage for the subsequent no-go gauge test to assess whether the upper tolerance limit is exceeded accurately.
Step 4: Apply the No Go Gauge
After successfully testing the component with the go gauge, use the no-go gauge to verify the upper tolerance limit. Carefully position the no-go gauge against the exact feature you tested with the go gauge. The no-go gauge should not fit or be inserted into the feature if the component’s dimensions are within the specified tolerances. If the no-go gauge can be applied with any level of ease, it suggests that the component exceeds the permissible size range and may need rejection or adjustment. This step upholds quality assurance by confirming that the component does not surpass the maximum allowable limits, thus maintaining the integrity and reliability of the production process.
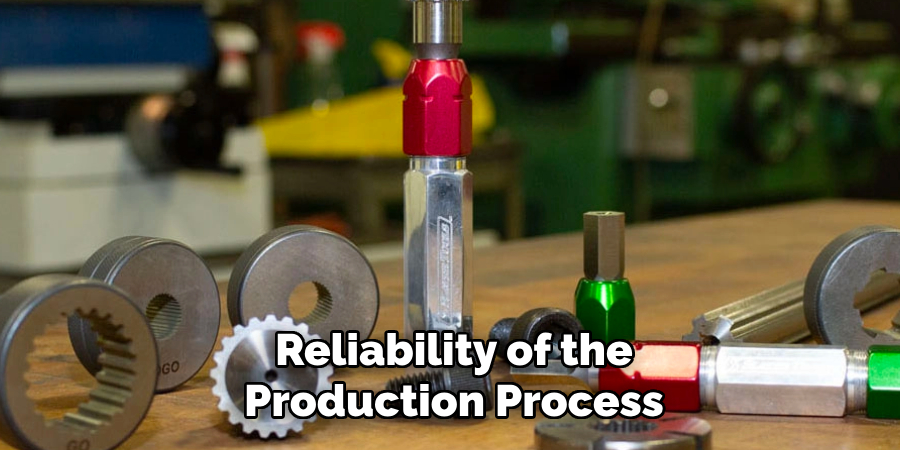
Step 5: Record Your Findings
Once you have completed the tests with both the go gauge and the no-go gauge, it is essential to document the results carefully. Record whether each component passed or failed the test and note any relevant observations or anomalies encountered during the evaluation. Accurate record-keeping helps track quality trends and provides essential data for process improvements. Ensure that all measurements and assessments are logged by your organization’s standards and quality control procedures. This documentation will serve as a valuable reference for future inspections and audits, aiding in maintaining the quality and consistency of production.
Step 6: Review Your Equipment
After completing the measurement process, it’s crucial to review the state of your equipment, including both the go and no-go gauges. Check for any signs of damage or wear that may have occurred during the usage that could impact future measurements. Clean each tool thoroughly to remove any debris or residue affecting their accuracy. Proper maintenance and storage of these tools are vital to ensuring their longevity and reliability. This review step helps prepare the equipment for subsequent use, guaranteeing that each measurement maintains the highest standard of precision and consistency within your quality control processes.
Step 7: Address Any Discrepancies
If any discrepancies are found during the measurement process, it’s essential to address them promptly. Begin by analyzing the cause of the issue, whether it originates from the component, gauges, or procedures used. Determine if the component can be adjusted or needs to be rejected due to size nonconformance. Collaborate with production teams to rectify any process-related issues that may have contributed to the inconsistency. Document all corrective actions taken, ensuring they align with quality management practices. Resolving these discrepancies early helps prevent further defects and ensures the continued reliability of the measurement process.
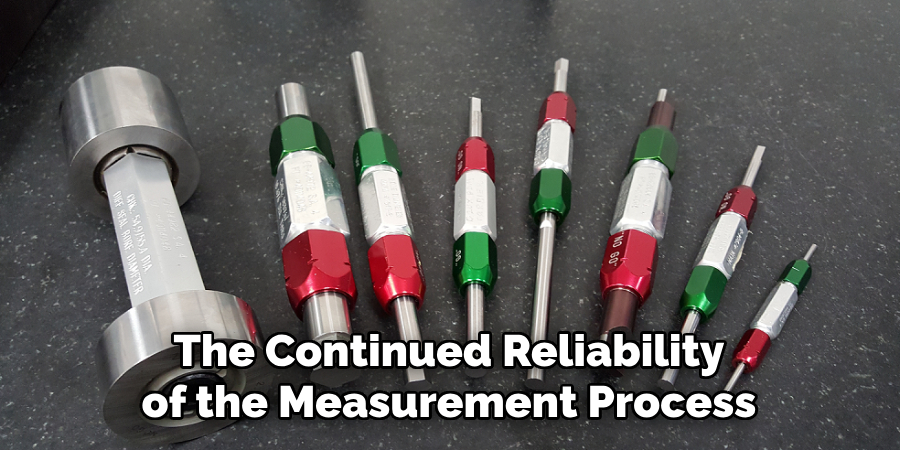
Step 8: Follow-Up with Continuous Improvement
After addressing any discrepancies, it’s essential to focus on continuous improvement to enhance the overall quality control process. Regular reviews and analyses of all recorded data should be conducted to identify recurring issues or patterns that could indicate systemic problems. Encourage feedback from employees involved in gauging and integrating their insights into refining procedures. Update training materials and methods based on new learnings or technological advancements to ensure the team can use the gauges effectively.
By fostering a culture of ongoing improvement, organizations can increase efficiency, reduce waste, and maintain high standards of product quality. This proactive approach leads to more reliable product offerings and greater customer satisfaction in the long run.
Step 9: Finalize and Implement Enhancements
Once continuous improvement initiatives are identified, the final step is implementing these enhancements into the existing quality control processes. Collaborate with the quality assurance team to prioritize which changes will have the most significant impact and devise a detailed implementation plan. This plan should include setting specific goals, assigning responsibilities, and establishing timelines for each enhancement. Ensure all team members are trained on the new procedures and that clear communication is maintained throughout the process.
By systematically integrating these improvements, the organization can bolster its quality assurance program, reduce the likelihood of future defects, and enhance overall operational efficiency. Regularly review and adjust these enhancements as needed to maintain alignment with evolving industry standards and customer expectations.
Step 10: Measure Process Effectiveness
After implementing enhancements to the quality control process, it’s crucial to measure the effectiveness of these changes. Begin by setting up key performance indicators (KPIs) that align with organizational goals and customer expectations. Monitor these KPIs regularly to assess product quality improvements, defects reduction, and overall process efficiency. Gather data from various checkpoints within the production line and evaluate the impact of implemented changes over a defined period. Engage with all stakeholders, including production, quality assurance, and customer service teams, to obtain feedback on the improvements.
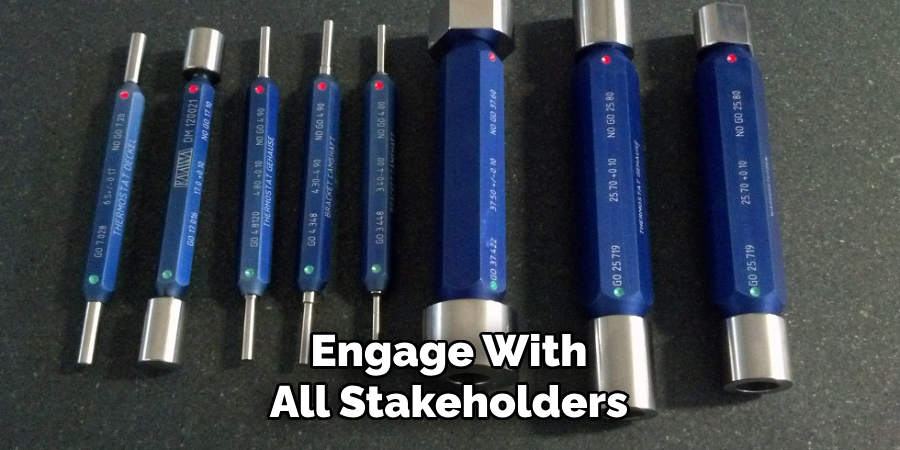
By following these ten steps, organizations can ensure that their gauging process effectively maintains the quality and reliability of their products.
5 Things You Should Avoid
- Forcing the Gauge: Never force a no-go gauge into a part. If it doesn’t fit freely, the part is likely out of tolerance, and forcing it could damage both the gauge and the component.
- Using Excessive Wear Gauges: Avoid using a worn-out no-go gauge. Regularly check for signs of wear or deformation, which could lead to inaccurate measurements.
- Neglecting Calibration: Avoid using a no-go gauge without ensuring it is properly calibrated. Regular calibration checks are essential to maintaining accuracy.
- Incorrect Application: Do not use a no-go gauge for purposes other than its intended design. Misuse can result in inaccurate readings and damage to the equipment.
- Ignoring Temperature Effects: Be cautious of using no-go gauges in environments with extreme temperatures, as these can expand or contract the material and affect readings. Always measure in conditions that meet the gauge’s specified temperature range.
Conclusion
How to use a no go gauge requires understanding its purpose and the conditions under which it should be used.
To ensure accurate measurements, always handle the gauge carefully, verify that it is calibrated, and ensure the environment is optimal for gauging—considering factors like temperature that may affect readings. Regularly inspect the gauge for wear and tear to prevent usage that could lead to erroneous outcomes.
By adhering to these guidelines, you can maintain the integrity of the gauge and the measured components, ensuring reliable and precise tolerances in your quality control processes.
Edmund Sumlin is a skilled author for Metal Fixes, bringing 6 years of expertise in crafting a wide range of metal fixtures. With a strong background in metalwork, Edmund’s knowledge spans various types of fixtures, from decorative pieces to functional hardware, blending precision with creativity. His passion for metalworking and design has made him a trusted resource in the industry.
Professional Focus:
- Expert in Metal Fixtures : Edmund aesthetic specializes in creating durable and innovative metal fixtures, offering both appeal and functionality. His work reflects a deep understanding of metalworking techniques and materials.
- Sustainability Advocate : He is dedicated to using sustainable practices, ensuring that every fixture is crafted with eco-friendly methods while maintaining high-quality standards.
In his writing for Metal Fixes, Edmund provides valuable insights into the latest trends, techniques, and practical advice for those passionate about metal fixtures, whether they are professionals or DIY enthusiasts. His focus on combining artistry with engineering helps others discover the true potential of metal in design.