Cooling iron is a pivotal step in numerous applications, ranging from metalworking and foundries to everyday cooking. This process not only influences the mechanical properties of iron but also determines its suitability for specific uses.
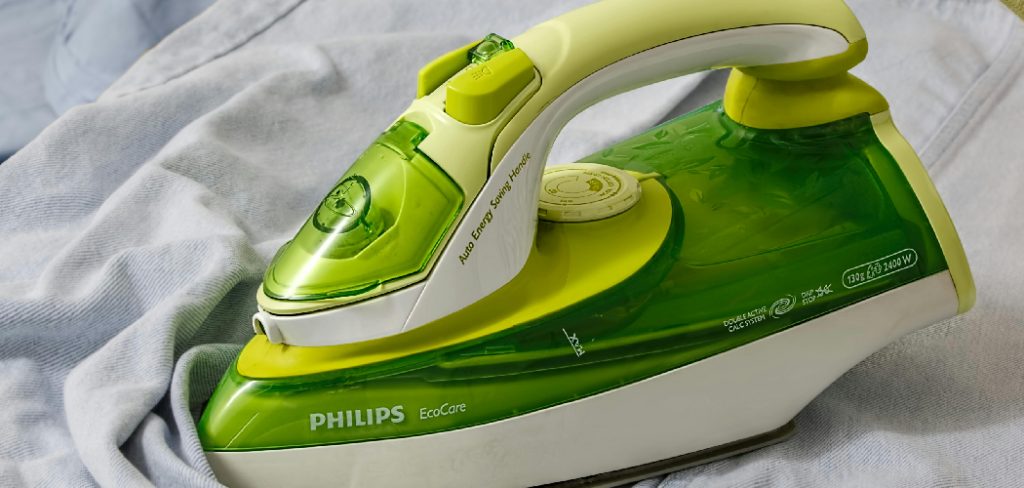
Whether in a foundry casting large components or a kitchen maintaining cast iron cookware, controlling the cooling process is crucial to achieving desired properties such as strength, hardness, and durability. How to cool iron effectively varies according to the type of iron and the intended use, making it essential to understand the underlying principles and methods.
This article explores the different techniques and strategies employed in cooling iron, providing insights into how these practices optimize performance and longevity. By mastering these cooling methods, professionals and hobbyists alike can ensure that iron products meet high standards of functionality and resilience.
Understanding the Cooling Process of Iron
The Science Behind Iron Cooling
Cooling iron involves fundamental principles of heat transfer, including conduction, convection, and radiation. Conduction refers to the transfer of heat within the metal itself, while convection involves the movement of heat through surrounding fluids like air or water. Radiation, though less significant in metal-cooling processes, contributes as heat is emitted from the iron’s surface.
The rate at which iron cools plays a crucial role in determining its final microstructure and mechanical properties. Rapid cooling can lead to a harder, more brittle iron, while slower cooling yields a softer, more ductile material. Understanding these principles aids in selecting the appropriate cooling method for specific applications.
Factors Affecting the Cooling Rate of Iron
Several factors influence the cooling rate of iron, each impacting the metal’s ultimate characteristics. The thickness of the iron is a primary factor; thicker sections require more time to cool, which can lead to differential cooling and potential thermal stresses. The chosen cooling method, whether air, water, or oil, significantly affects the rate and uniformity of heat removal.

Additionally, ambient temperature plays a role, with cooler environments accelerating the cooling process. Different types of iron, such as cast iron and wrought iron, have varying cooling requirements due to their distinct microstructures and compositions, necessitating tailored approaches for optimal results.
How to Cool Iron: Methods of Cooling Iron
Air Cooling
Air cooling is the simplest and most common method for cooling small iron pieces. This technique allows iron to cool naturally in the open air, providing a moderate cooling rate. It is widely employed in casting processes and for crafting tools, where intricate control over the cooling rate is often unrequired.
The primary advantages of air cooling include its simplicity and the absence of additional cooling agents. However, this method offers limited control over the final hardness and mechanical properties, potentially leading to inconsistencies in more demanding applications.
Water Quenching
Water quenching is when iron is rapidly cooled by submerging it in water. This method is particularly effective in increasing hardness, as the swift removal of heat prevents certain microstructures from forming during slower cooling processes. Water quenching is commonly recommended for steel alloys, especially in blacksmithing and tool-making applications, where enhanced surface hardness is desired.
However, the rapid quenching process also raises the risk of brittleness, which can result in materials cracking or warping if not performed carefully. The choice of using water quenching should account for the alloy’s composition and anticipated stresses, ensuring that these potential drawbacks do not compromise the integrity of the finished product.
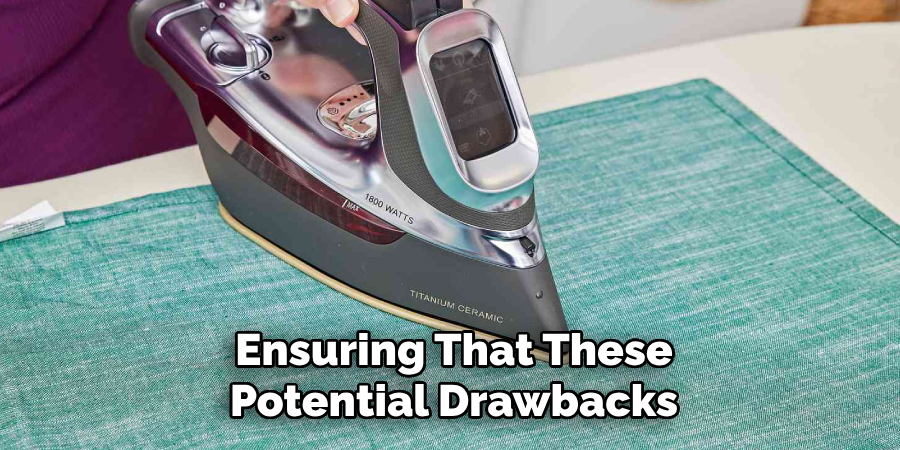
Oil Quenching
Oil quenching differs from water quenching by providing a slower and more controlled cooling process, which is especially beneficial for reducing the risks associated with rapid heat removal, like cracking or warping. The oil medium introduces a gentler heat transfer rate, enabling iron and steel to gradually reach desired mechanical properties without sudden structural changes.
This method is often utilized in heat-treating applications, particularly for components that require precision in maintaining their form, such as engine parts or high-strength tools. The results of oil quenching yield a balanced combination of toughness and hardness, catering well to components subjected to high-stress environments.
How to Cool Iron: Cooling Iron in a Foundry
In foundries, cooling iron is an essential part of the casting process, significantly influencing the quality and properties of the final product. The cooling phase begins the moment molten iron is poured into molds. In this setting, attaining a controlled cooling rate is crucial to prevent defects such as warping, cracking, or uneven mechanical properties.
The environment within the foundry, including ambient temperature and humidity, can impact the cooling process substantially. Therefore, foundries often employ meticulously designed cooling systems that can regulate these variables to achieve consistent results. Moreover, advanced monitoring technologies may be implemented to track the cooling curve and make real-time adjustments, ensuring that each cast meets the required specifications.
This precision in the cooling process is necessary for producing large components, where even slight variations can lead to significant performance discrepancies. Foundries must also tailor their cooling strategies based on the type of iron being used, as different compositions—such as ductile iron or gray iron—react differently to cooling, affecting their brittleness, strength, and ductility.
By understanding and controlling the dynamics of iron cooling, foundries can create castings that are not only functional but also high-performing and reliable over their operational lifespan.
Cooling Cast Iron in Molds
Cooling cast iron in molds is a critical step that hinges on the mold’s material and thickness. The ability of the mold material to absorb and dissipate heat effectively determines the cooling rate, affecting the cast iron’s final attributes. Thickness plays a pivotal role, where thicker molds can slow the cooling process, allowing for a more uniform solidification. This control helps prevent internal stresses and structural weaknesses in the finished cast.
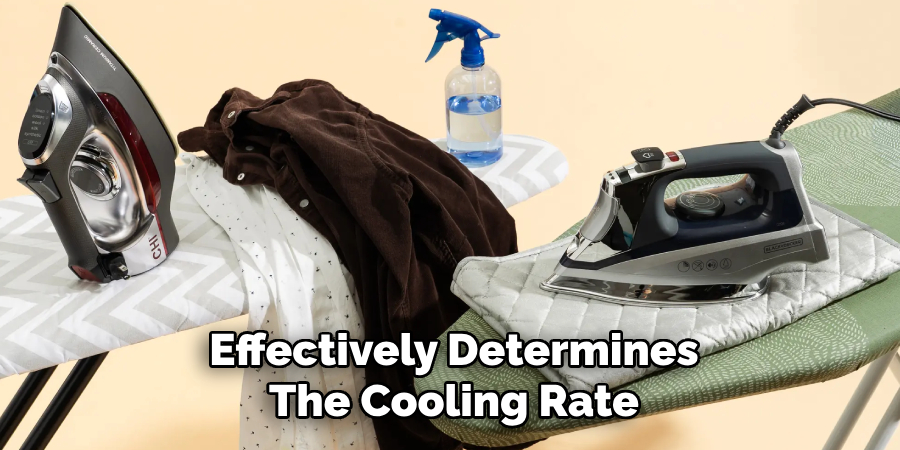
Casting sand plays an integral role in regulating cooling rates for cast iron, serving as an insulating layer that aids in uniform temperature reduction. The sand’s consistency and compactness are carefully managed to counteract potential defects like shrinkage and cracks, ensuring the iron sets have maximum integrity.
Cooling Iron for Forging and Casting
When cooling iron for forging, a gradual reduction in temperature is vital to circumvent cracking or induced stress within the metal. This slow process allows the iron to transition smoothly from a malleable to a solid state, preserving its structural coherence and promoting better durability.
Forging operations often employ controlled environments, such as heat treatment ovens, to control precise temperature throughout the cooling phase. These settings offer flexibility in altering cooling rates to match specific alloy requirements, thus optimizing the mechanical properties for the intended application.
Post-cooling treatments, like annealing, further refine the final product by relieving stress and enhancing workability. Annealing involves reheating the cooled iron and slowly reducing its temperature, which softens the material and improves its ductility, making it more amenable to further shaping and strengthening.
Cooling Iron for Hardness and Durability
Cooling iron to enhance its hardness and durability is pivotal in many industrial applications. Increased hardness is typically accomplished through quenching, which involves rapid cooling that alters the metal’s microstructure to increase wear resistance and lifespan.
The choice of cooling medium can significantly impact the final properties of the iron, with common options including water, oil, and air, each offering different heat extraction rates. Water quenching is particularly effective for achieving high hardness, although it carries a risk of brittleness if not meticulously controlled. In contrast, oil and air offer gentler cooling rates, balancing hardness and toughness.
Precisely controlling cooling strategies enables industries to produce components that maintain structural integrity under stress, such as high-performance tools and critical machinery parts. Furthermore, understanding the type of iron and its alloy composition is crucial, as this dictates the specific cooling approach needed to optimize mechanical properties.
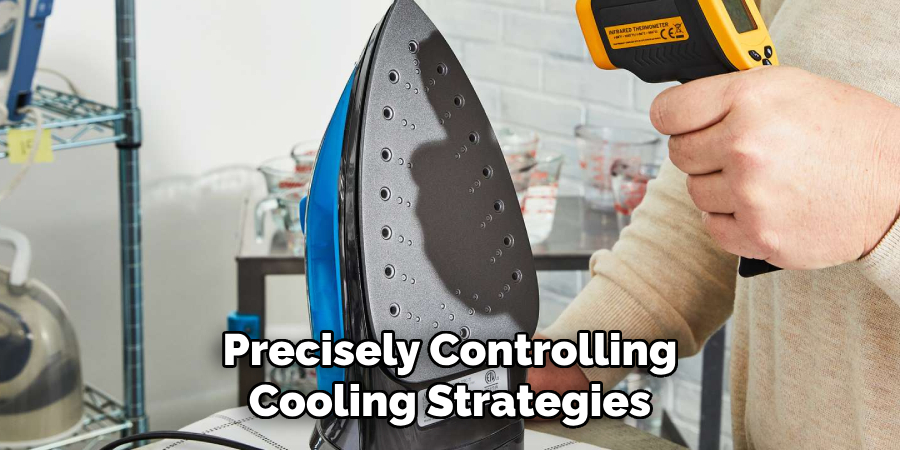
Hardening Iron Through Cooling
Rapid cooling, or quenching, hardens iron by transforming its internal structure, specifically through martensite formation. This phase change enhances the metal’s hardness and strength, making it more resistant to wear and deformation. Martensitic transformation is especially valuable in applications where durability is critical, such as the manufacturing of tools, machinery parts, and weapons.
By rapidly reducing the temperature of heated iron, quenching locks the dislocated atomic structure in place, resulting in significantly increased hardness compared to slower cooling methods.
Tempering Iron After Quenching
Tempering is a crucial step following quenching to address the inherent brittleness introduced by rapid cooling. The process involves reheating the quenched iron to a specific temperature, which allows some of the internal stresses to be released without losing all the hardness gained.
This controlled reheating restores ductility and toughness, creating a more versatile and structurally sound material. In practice, tempering adjusts the balance between hardness and flexibility to suit the intended application of the metal. After reaching the desired temperature, the iron is allowed to cool at a controlled rate, ensuring the optimized harmony of mechanical properties.
Cooling Techniques for Different Types of Iron
Cooling Cast Iron
Cooling cast iron is a delicate process that influences the formation of graphite, directly impacting the iron’s strength and texture. To manage this, the cooling process often involves slow cooling in casting sand or controlled cooling in a furnace. Slow cooling in the sand effectively moderates the solidification rate, allowing carbon to form free flakes of graphite rather than carbides.
This results in a softer, machinable form of cast iron known as gray iron. Alternatively, using a furnace provides precise temperature control, ensuring the homogeneity of the structure and improving mechanical properties.
Cooling Wrought Iron
When cooling wrought iron during forging, a slower process is crucial to maintaining its fibrous structure, which is inherent to its strength and ductility. Gradual temperature reduction allows the slag fibers within the iron to redistribute uniformly, avoiding stress concentrations that could lead to fractures.
Controlled cooling thus preserves the malleability of wrought iron, making it ideal for applications requiring high pliability and durability. This practice ensures wrought iron products remain ductile and resilient, which is essential for their traditional ornamental and structural uses.
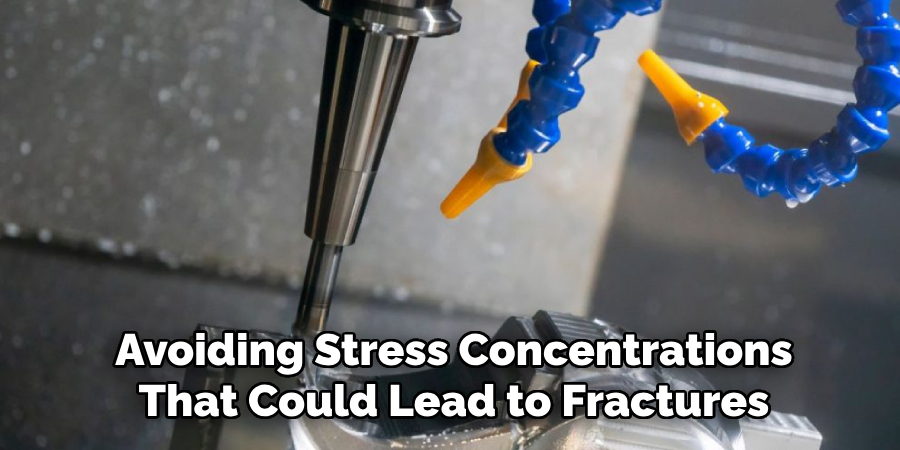
Cooling Steel Alloys
Specific cooling methods are tailored to steel alloys’ unique compositions and desired end properties. The diversity of steel alloys, from carbon steels to stainless steels, requires varying cooling rates to achieve optimal hardness, toughness, and corrosion resistance. Techniques include air cooling for high-carbon steels to prevent warping and oil quenching for alloyed steels to balance hardness with durability.
Common Issues in Cooling Iron and Solutions
Cracking and Warping
Cracking and warping are prevalent issues in cooling iron, often resulting from rapid cooling, uneven thickness, and improper handling. Rapid cooling, or quenching, can introduce severe thermal stresses, leading to cracks or structural distortions. Uneven thickness in iron components can cause differential cooling rates, exacerbating these stresses and resulting in warping.
Also, improper cooling handling can apply unnecessary mechanical stress, leading to deformation. It’s crucial to employ gradual cooling techniques that minimize stress to prevent such issues. Choosing the appropriate quenching method tailored to the specific type of iron and its end use is essential. Allowing adequate rest periods post-cooling also helps in stress relaxation and structural stabilization.
Uneven Hardness
Achieving uniform hardness across an iron surface can be challenging, often due to inconsistent quenching and uncontrolled cooling rates. These factors can lead to variations in microstructure, resulting in uneven distribution of hardness and brittleness. To ensure consistent hardness, it is vital to employ even quenching methods that provide uniform heat extraction across the entire surface of the iron component.
Controlled cooling rates are equally important, as they promote a uniform microstructure transformation throughout the material. Implementing advanced monitoring techniques during the cooling process helps in achieving the desired uniform hardness, enhancing overall durability and performance.
Cooling Iron for Cooking
Cooling Cast Iron Cookware
Allowing cast iron cookware to cool naturally after use is crucial to maintain its integrity and longevity. Rapid cooling methods, like submerging hot pans in cold water, should be avoided, as they can lead to warping or cracking due to sudden thermal shock.
By letting cast iron cool slowly, the cookware retains its seasoning—a vital layer that provides a non-stick surface and prevents rust. Proper cooling practices preserve the natural oils infused into the iron, ensuring the cookware remains effective and functional for everyday use.
Cooling Iron Grills and Pans
When it comes to cooling iron grills and pans, patience is key. After cooking, allow the equipment to rest at room temperature, enabling even distribution of residual heat and preventing localized stress.
Avoiding quick temperature changes is essential because exposing hot iron to cold environments can cause structural damage and diminish its performance over time. Embracing these best practices extends the life of your cooking tools and guarantees consistent cooking results while maintaining the culinary quality of the meals prepared.

Conclusion
Understanding how to cool iron effectively is paramount for enhancing the quality, durability, and functionality of iron products. The cooling methods vary significantly across different types of iron, from slow processes for cast and wrought iron to precise quenching techniques for steel alloys.
Each approach influences the mechanical properties, securing the desired balance between hardness and ductility. Consistently applying proper cooling practices ensures iron components remain free from defects such as cracking and warping. As a final tip, always consider the specific type of iron and its intended use when deciding on the best cooling method to achieve optimal results.
Edmund Sumlin is a skilled author for Metal Fixes, bringing 6 years of expertise in crafting a wide range of metal fixtures. With a strong background in metalwork, Edmund’s knowledge spans various types of fixtures, from decorative pieces to functional hardware, blending precision with creativity. His passion for metalworking and design has made him a trusted resource in the industry.
Professional Focus:
- Expert in Metal Fixtures : Edmund aesthetic specializes in creating durable and innovative metal fixtures, offering both appeal and functionality. His work reflects a deep understanding of metalworking techniques and materials.
- Sustainability Advocate : He is dedicated to using sustainable practices, ensuring that every fixture is crafted with eco-friendly methods while maintaining high-quality standards.
In his writing for Metal Fixes, Edmund provides valuable insights into the latest trends, techniques, and practical advice for those passionate about metal fixtures, whether they are professionals or DIY enthusiasts. His focus on combining artistry with engineering helps others discover the true potential of metal in design.