Welding cast iron to steel is a complex task due to the distinct characteristics of these metals. Cast iron, with its high carbon content, is prone to cracking during the cooling process. In contrast, steel’s relatively low carbon content and flexibility require careful handling to ensure a solid joint. Welding these dissimilar metals involves overcoming their differing thermal properties and accommodating their unique cooling requirements. Common applications of this welding technique can be found in machinery repair, where the robust nature of cast iron is essential, as well as in structural welding and custom metal fabrication, where the strength and versatility of steel are desired.
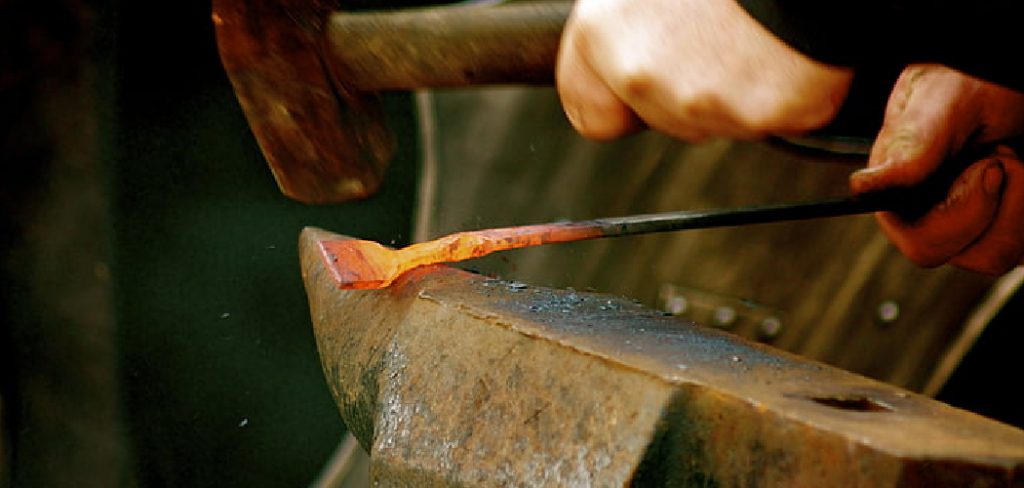
This article aims to offer a comprehensive guide on how to weld cast iron to steel, providing step-by-step instructions and practical tips to navigate the challenges presented by these materials, ensuring a successful and durable weld.
Understanding the Properties of Cast Iron and Steel
Characteristics of Cast Iron
Cast iron is renowned for its high carbon content, which contributes to its strength but also makes it notoriously brittle. This brittleness poses a significant challenge during welding, as it increases the risk of cracking, especially during cooling. Cast iron requires a controlled cooling process to mitigate these risks. The different types of cast iron—such as gray iron, ductile iron, and white iron—each have distinct properties that affect how they weld. Gray iron is the most common and is known for its machinability, while ductile iron offers better impact resistance. Despite its hardness, white iron is the least weldable due to its brittleness. These variations must be understood to anticipate their impact on welding outcomes.
Characteristics of Steel
In contrast to cast iron, steel typically has a lower carbon content, which grants it greater flexibility and durability. This flexibility is advantageous in welding applications, as steel can absorb stress without fracturing easily. However, welding steel to cast iron presents compatibility issues because of the differing thermal properties. Steel heats and cools at a different rate than cast iron, which can lead to thermal stresses at the joint. Understanding these differences is essential to effectively manage the thermal cycling during the welding process, ensuring that the structural integrity of both metals is maintained in the final weld.
Tools and Materials Needed for Welding
Welding Equipment and Consumables
When welding cast iron to steel, selecting the right equipment and consumables is crucial for achieving a successful joint. A stick welder (SMAW) or a MIG welder are commonly used machines for this process. The choice between them depends on the specific project requirements and the welder’s skill level. Electrodes play a vital role, including nickel-based rods, cast iron electrodes, or specialty rods designed for welding dissimilar metals. Each electrode type has properties tailored to accommodate the unique characteristics of cast iron and steel, ensuring a strong bond and minimizing the risk of cracks.
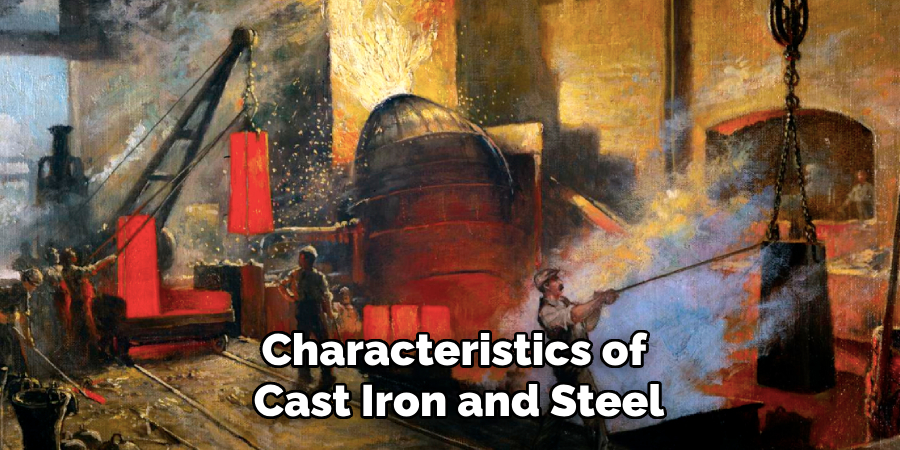
Safety Gear and Workspace Setup
Ensuring safety during the welding process is paramount, necessitating the use of appropriate protective gear. A welding helmet protects the face and eyes from harmful UV and infrared light, while gloves and fire-resistant clothing shield the skin from sparks and heat. Additionally, it is essential to set up a clean and well-ventilated workspace. Proper ventilation helps to prevent the accumulation of hazardous fumes and ensures that the materials remain uncontaminated during the weld. This preparation enhances the welder’s safety and contributes to the final weld’s quality and durability.
Preparing the Metals for Welding
Cleaning the Surfaces
Ensuring that both cast iron and steel surfaces are clean is a vital step in the welding preparation process. Any presence of rust, paint, grease, or dirt can interfere with weld adhesion and compromise the quality of the joint. Using a wire brush or grinder effectively removes these contaminants, resulting in a clean and smooth surface. This cleanliness is crucial as it allows for better penetration and bonding of the weld, minimizing the risk of defects. Taking the time to clean the surfaces thoroughly enhances the overall durability and integrity of the welded joint.
Preheating the Metals
Preheating the metals, particularly cast iron, is an essential technique to reduce the risk of cracking during welding. Due to cast iron’s brittleness, abrupt temperature changes can lead to cracks as it cools. Preheating helps to evenly distribute heat, alleviating thermal stresses and reducing the likelihood of cracking. The recommended preheating temperature range for cast iron is between 500°F and 1200°F, depending on the thickness and composition of the material. Common tools for preheating include a torch or a furnace, which can effectively raise the temperature to the desired level, ensuring a smoother welding process and a more robust final joint.
How to Weld Cast Iron to Steel: Welding Techniques for Cast Iron and Steel
Tack Welding the Pieces Together
Tack welding is crucial in stabilizing the joint before performing the full weld. Securing the pieces with tack welds prevents movement or shifting during the main welding process. Begin by placing small tack welds at evenly spaced intervals across the joint. This distribution ensures balanced stability and helps maintain alignment, reducing the potential for distortion or warping. Careful planning of tack weld placement can significantly enhance the joint’s integrity, creating a stable foundation for the subsequent main weld.
Performing the Main Weld
Executing the main weld requires precision and technique to accommodate the differing properties of cast iron and steel. First, use short weld beads, which help minimize heat concentration and reduce the risk of cracking. Excessive heat can exacerbate cast iron brittleness, so controlling the thermal input is vital. Allow each weld bead to cool slightly before proceeding to the next, preventing overheating and ensuring even heat distribution. To further balance heat accumulation, alternate welding locations across the joint.
Moving from one side to another helps manage thermal stresses and prevent warping. Recommended welding patterns include a staggered approach, where welds are performed sequentially, non-linearly, promoting a uniform bond. Attention to these details during welding will contribute to a successful and enduring connection between the cast iron and steel components.
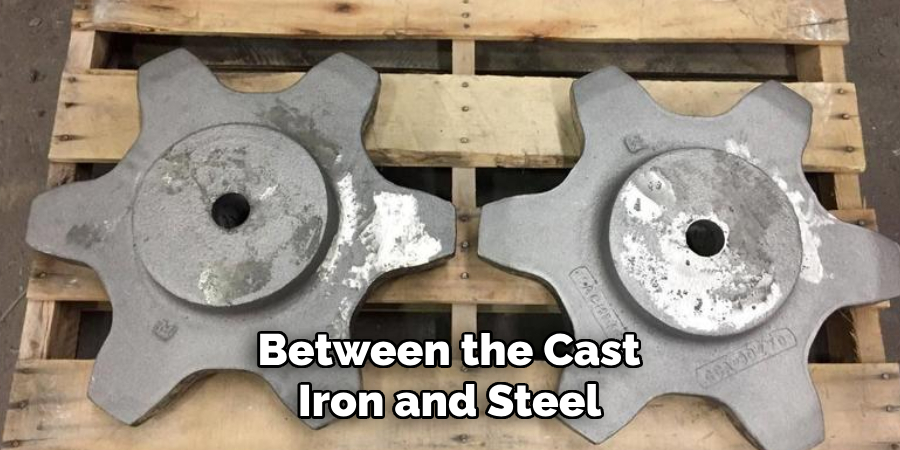
Cooling and Post-Weld Treatment
Controlled Cooling
Controlled cooling is critical after welding cast iron to steel to avoid thermal shock and subsequent cracking. Rapid temperature changes can exacerbate cast iron’s inherent brittleness, leading to fractures within the joint. To mitigate these risks, the welded piece should cool slowly and uniformly. Techniques such as covering the joint with an insulating blanket or burying it in sand or ash can help maintain a consistent cooling rate by retaining heat and preventing quick dissipation. This gradual cooling process enhances the joint’s structural integrity and reduces residual stresses.
Post-Weld Stress Relief
Post-weld stress relief is essential for cast iron components to alleviate internal stresses formed during the welding process. If left unchecked, these stresses could compromise the joint’s durability and lead to premature failure over time. One effective method for stress-relieving involves reheating the welded area to a lower temperature, typically between 600°F and 800°F, followed by gradual cooling. This reheating allows the metal to relax and realign its internal structure, facilitating stress dissipation. Implementing these stress-relief techniques strengthens the overall bond between cast iron and steel, ensuring longevity and resilience in the welded assembly.
Troubleshooting Common Issues
Addressing Cracking in Cast Iron
Cracking in cast iron during or after welding is a common issue due to its natural brittleness and sensitivity to temperature changes. Causes of cracks include inadequate preheating, rapid cooling, or excessive heat during the welding process. To prevent these issues, it’s vital to maintain uniform heat distribution and avoid abrupt temperature shifts. Employing controlled cooling techniques, such as insulated blankets, can significantly reduce the risk of cracking. If cracks do occur, re-welding processes may involve grinding out the affected area to ensure a clean surface, followed by carefully reapplying weld beads.
Alternatively, using specialized welding rods and techniques designed for cast iron can help mitigate the risk of recurring cracks.
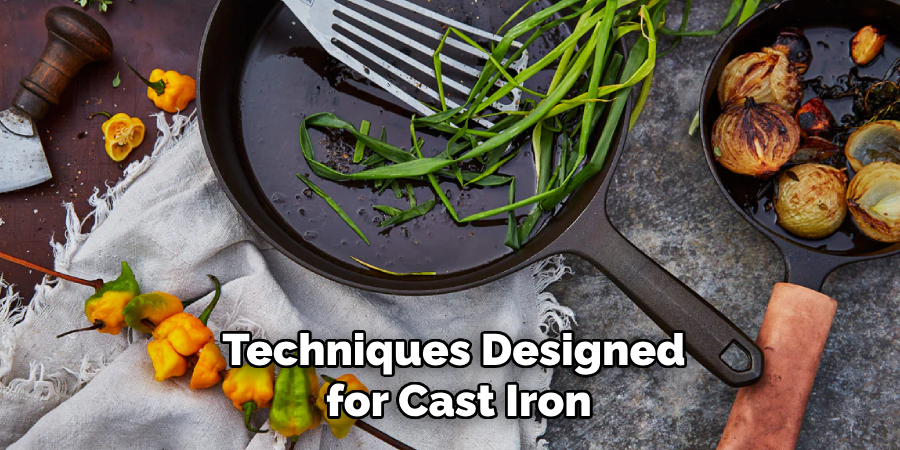
Avoiding Weak Welds
Ensuring strong welds between cast iron and steel requires careful attention to welding techniques, electrode selection, and heat management. Proper technique involves using short, controlled weld beads and allowing sufficient cooling time between passes to balance thermal input. Electrode choice is crucial; opting for ones specifically suited for the materials in question will increase weld strength. Managing heat by alternating welding locations across the joint helps prevent overheating and distribution imbalances. Attention to these factors not only enhances the integrity of the weld but also minimizes the potential for weak connections that could compromise the durability of the joint.
Practical Applications of Cast Iron to Steel Welding
Examples of Real-World Applications
Welding cast iron to steel finds practical applications in a variety of industries. In automotive manufacturing and repair, this technique is commonly used to repair engine parts, providing an effective solution to address wear and damage while maintaining the integrity of components. It is employed to join structural components in construction, offering a robust and flexible assembly option. Moreover, cast iron to steel welding is invaluable in custom metalwork, allowing for intricate designs that capitalize on the distinct properties of each material.
Benefits of Welding Dissimilar Metals
The ability to weld dissimilar metals such as cast iron and steel brings numerous advantages. One significant benefit is cost savings, as it facilitates repairing and reusing existing parts instead of replacing them. Additionally, this method can extend the life of machinery by ensuring reliable repairs and reinforcing structural elements. Furthermore, welding dissimilar metals offers greater flexibility in design, allowing engineers and designers to leverage the unique characteristics of each metal for optimized project outcomes.
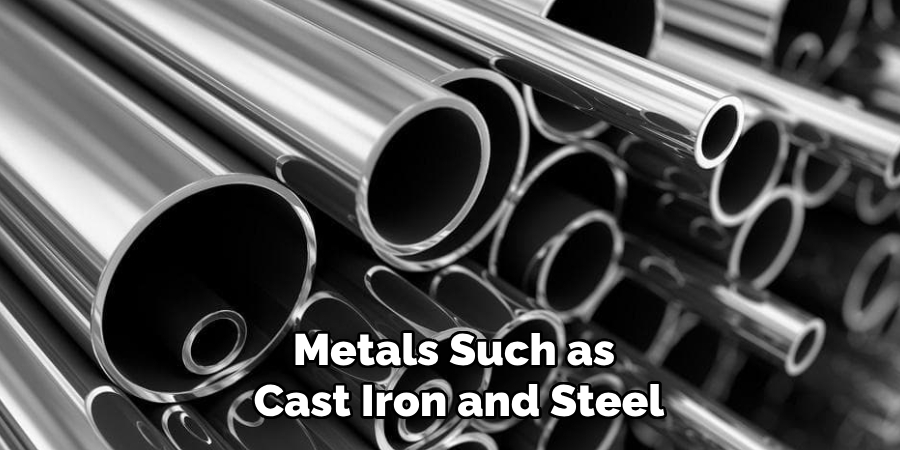
Conclusion
Mastering the process of how to weld cast iron to steel requires understanding the intricate challenges posed by their differing properties. Ensuring successful welds involves meticulous preparation, precise heat control, and thorough post-weld treatment. These steps address the brittleness and temperature sensitivity inherent in cast iron. Welders can achieve durable joints by implementing controlled heat application and stress relief techniques. Continuous practice and adherence to safety guidelines are crucial for refining skills and achieving consistent results. This approach enhances the quality of work and promotes safety in welding environments.
Edmund Sumlin is a skilled author for Metal Fixes, bringing 6 years of expertise in crafting a wide range of metal fixtures. With a strong background in metalwork, Edmund’s knowledge spans various types of fixtures, from decorative pieces to functional hardware, blending precision with creativity. His passion for metalworking and design has made him a trusted resource in the industry.
Professional Focus:
- Expert in Metal Fixtures : Edmund aesthetic specializes in creating durable and innovative metal fixtures, offering both appeal and functionality. His work reflects a deep understanding of metalworking techniques and materials.
- Sustainability Advocate : He is dedicated to using sustainable practices, ensuring that every fixture is crafted with eco-friendly methods while maintaining high-quality standards.
In his writing for Metal Fixes, Edmund provides valuable insights into the latest trends, techniques, and practical advice for those passionate about metal fixtures, whether they are professionals or DIY enthusiasts. His focus on combining artistry with engineering helps others discover the true potential of metal in design.