Are you a professional welder looking to improve the quality of your work? Finding ways to reduce weld spatter can be an ongoing challenge. However with the proper techniques and tools, it’s possible to increase efficiency and product durability while minimizing waste.
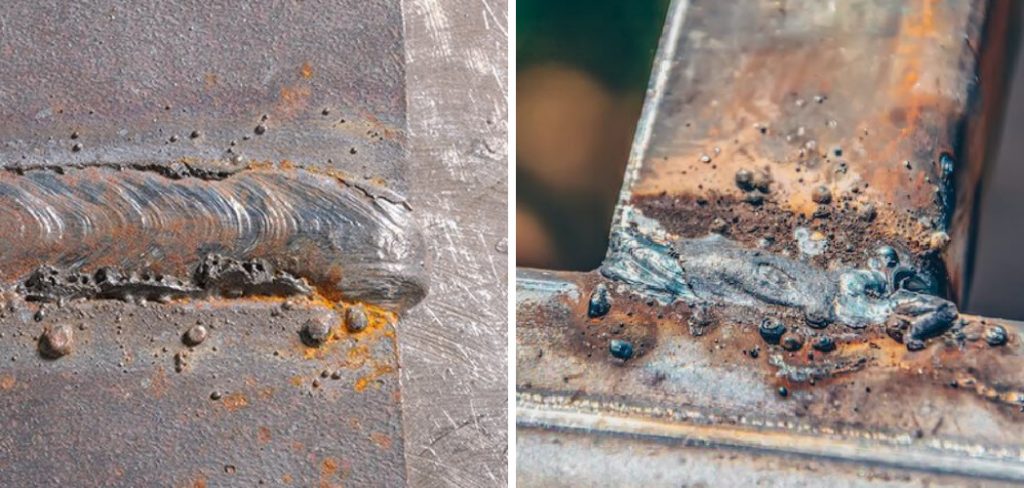
Reducing weld spatter not only improves the appearance of your welds but also reduces the time and effort required for cleanup. Additionally, excessive spatter can cause issues with porosity and cracking, leading to weaker welds. With that in mind, let’s explore some tips for reducing weld spatter.
In this blog post, you’ll discover some innovative solutions for reducing weld spatter that will take your welding projects to the next level! Keep reading to learn more about how to reduce weld spatter.
What Causes Weld Spatter?
Before we dive into the solutions, let’s first understand what causes weld spatter. When welding, molten metal from the electrode and base material can splatter and solidify on the surface of your final product. This is commonly known as weld spatter.
Weld spatter occurs due to high voltage, improper shielding gas, and incorrect wire feed speed. It can also be caused by a buildup of dirt, rust, or oil on the surface of the materials being welded. Understanding these causes will help you pinpoint the source of your spatter and take appropriate measures to reduce it.
What Will You Need?
To reduce weld spatter, you’ll need the right tools and equipment. Here are some essential items to have on hand:
- A high-quality welding machine with adjustable voltage settings.
- Clean, rust-free materials to be welded.
- Properly functioning welding accessories include a torch, wire feeder, and contact tip.
- Adequate safety gear, including gloves, helmets, and protective clothing.
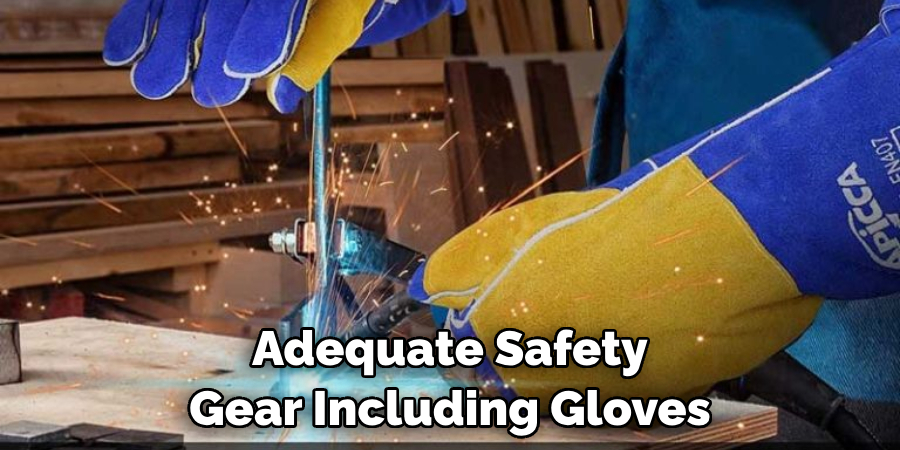
Now that we have the necessary tools let’s explore some practical solutions for reducing weld spatter.
10 Easy Steps on How to Reduce Weld Spatter
Step 1. Use the Right Shielding Gas:
Selecting the right shielding gas can significantly reduce weld spatter. An argon-CO2 mix is often recommended for lower levels of spatter. Make sure to choose the right gas mixture depending on the type of metal you’re welding.
Step 2. Correct Wire Feed Speed:
The wire feed speed plays a crucial role in controlling weld spatter. If the speed is too high, it can lead to excessive spatter. On the other hand, if the speed is too slow, it can cause an unstable arc, also leading to a spatter. You can find the optimal balance that produces a smooth, spatter-free weld by fine-tuning the wire feed speed. Experiment with different speeds until you achieve the desired results.
Step 3. Maintain Proper Voltage:
Voltage is another essential parameter that influences weld spatter. High voltage often results in increased spatter. Therefore, adjusting your welding machine to the correct voltage setting for the job at hand is crucial. Remember, the ideal voltage can vary depending on the type of metal, its thickness, and the welding position. Refer to your machine’s user manual or a trusted welding guide for the recommended voltage settings.
Step 4. Keep Your Materials Clean:
Ensuring that your materials are clean before welding is an effective way to reduce spatter. Oil, rust, and dirt on the surface of your materials can lead to an unstable arc, causing spatter. Therefore, cleaning your materials thoroughly before beginning your welding process is crucial. A wire brush or a grinder can be used for this purpose. Remember, the cleaner your materials, the smoother and more spatter-free your weld will be.
Step 5. Use Anti-Spatter Spray:
Anti-spatter spray can be an effective aid in controlling weld spatter. This spray forms a protective layer on the surface of your materials, preventing spatter from sticking to it. Before starting welding, spray the anti-spatter coating on the welding area and torch nozzle. The anti-spatter spray not only helps to reduce spatter but also makes the post-welding cleanup process much more manageable.
Step 6. Regularly Check and Replace Consumables:
Your welding torch and its consumables play a pivotal role in reducing spatter. Worn out contact tips, liners, and diffusers can cause an unstable arc, leading to more spatter. Therefore, regularly inspect these components and replace them as needed. Using high-quality consumables can also make a significant difference in controlling spatter.
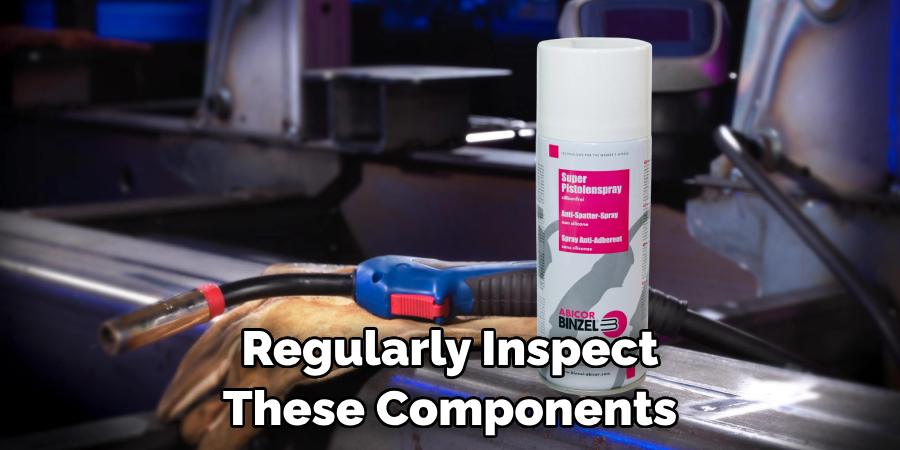
Step 7. Ensure Proper Stick-Out Distance:
The stick-out distance, or the length of the wire sticking out of your torch, directly impacts the amount of weld spatter. If the stick-out is too long, it can cause a weak arc and increased spatter.
On the other hand, if it’s too short, it can lead to a powerful arc and more spatter. As a rule of thumb, the ideal stick-out distance is usually the same as your wire diameter. Ensuring the proper stick-out distance can significantly help in reducing weld spatter.
Step 8. Adopt Correct Welding Techniques:
The technique you use to weld can also affect the amount of spatter. For example, push techniques often produce less spatter compared to pull methods. Try different welding techniques to see which provides you with the least spatter. Remember, practice makes perfect. The more you weld, the better you’ll become at controlling spatter.
Step 9. Utilize a Spatter Shield:
A spatter shield is a tool that can be highly effective in reducing weld spatter. It works by shielding the area around the weld from excess spatter, thus ensuring a cleaner weld and reducing cleanup time.
Before welding, position the spatter shield close to the welding zone to protect the nearby areas. Remember to adjust the shield as you move along the weld to protect the surrounding areas continually. A spatter shield is a simple and practical way to control weld spatter.
Step 10. Regular Maintenance of Welding Equipment:
To reduce weld spatter, keeping your welding equipment in optimal condition is crucial. Regular maintenance includes cleaning the machine, checking for any physical damages, ensuring all parts’ proper functioning, and replacing worn-out components.
A well-maintained welding machine will provide a stable arc and controlled temperature, which are fundamental factors in reducing weld spatter. Keeping your equipment in top shape not only helps minimize weld spatter but also prolongs the life of your machine, making it a win-win situation.

Following these ten steps, you can significantly reduce weld spatter and achieve smooth, clean welds. Remember to practice and experiment with different techniques until you find the right balance for your welding process.
5 Additional Tips and Tricks
- Use a Good Quality Welding Wire: A high-quality welding wire with a consistent diameter can significantly reduce spatter. Make sure to choose the right type for your material and welding process.
- Maintain Proper Wire Stick-Out: Wire stick-out length can impact the amount of spatter. Always ensure the wire is short enough, with the ideal length typically being 1/4 to 1/2 inch.
- Adjust Voltage and Amperage Settings: Fine-tuning your voltage and amperage can reduce spatter. Always experiment with settings within the manufacturer’s recommended range.
- Regularly Clean Your MIG Gun: Ensure your MIG gun is free from any buildup of spatter or debris. This reduces spatter and enhances the overall efficiency of your welding process.
- Check the Gas Flow Rate: Insufficient gas flow can lead to an increase in the spatter. Ensure that the gas flow rate is appropriate for your welding process.
With these additional tips and tricks, you can better manage and reduce weld spatter during your welding projects.
5 Things You Should Avoid
- Using Dirty Materials: Dirt, rust, or paint on your welding materials can cause excess spatter. Always clean your materials before you begin welding.
- Incorrect Wire Feed Speed: Running your wire feed too fast or too slow can increase spatter. It’s essential to find the right balance to ensure cleaner welding.
- Overusing Anti-Spatter Spray: While it’s a quick fix, excessive use of anti-spatter spray can impact the quality of your welds. Use it sparingly and focus on other preventive methods.
- Ignoring Regular Maintenance: Failing to maintain your welding equipment can contribute to increased spatter. Regularly check for worn-out parts or issues that might affect your welding process.
- Skipping Safety Measures: Weld spatter can be harmful. Avoid neglecting safety measures like welding helmets, gloves, and aprons to protect yourself from flying spatter. Remember, safety comes first!
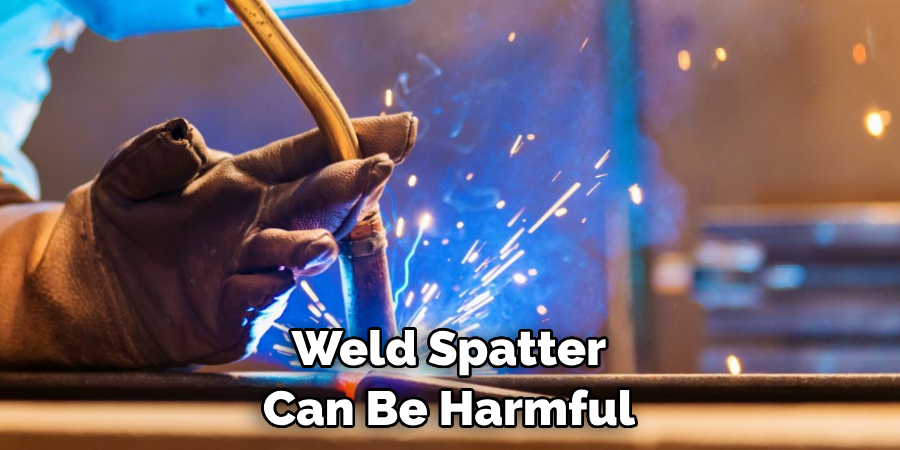
Avoiding these common mistakes can go a long way toward reducing weld spatter and making your welding process smoother and more efficient.
Conclusion
In conclusion, weld spatter can be both inconvenient and difficult to reduce. However, some techniques and products can help you efficiently take control of the situation. With proper preparation before welding, utilizing proven anti-spatter treatment products, and using the correct shielding gas, you will be well on your way to eliminating weld spatter in no time. Taking these steps will save you time and a substantial amount of money in the long run.
Hopefully, the article on how to reduce weld spatter has given you valuable insights and practical tips to achieve a cleaner and more efficient welding process. Remember always to prioritize safety, practice different techniques, and regularly maintain your welding equipment.
So take advantage of these tips today and enjoy a more effective and efficient welding experience! Happy welding!
Edmund Sumlin is a skilled author for Metal Fixes, bringing 6 years of expertise in crafting a wide range of metal fixtures. With a strong background in metalwork, Edmund’s knowledge spans various types of fixtures, from decorative pieces to functional hardware, blending precision with creativity. His passion for metalworking and design has made him a trusted resource in the industry.
Professional Focus:
- Expert in Metal Fixtures : Edmund aesthetic specializes in creating durable and innovative metal fixtures, offering both appeal and functionality. His work reflects a deep understanding of metalworking techniques and materials.
- Sustainability Advocate : He is dedicated to using sustainable practices, ensuring that every fixture is crafted with eco-friendly methods while maintaining high-quality standards.
In his writing for Metal Fixes, Edmund provides valuable insights into the latest trends, techniques, and practical advice for those passionate about metal fixtures, whether they are professionals or DIY enthusiasts. His focus on combining artistry with engineering helps others discover the true potential of metal in design.