Do you have a project that requires welding magnesium castings? If so, you’re in luck! Welding magnesium comes with several unique challenges – but it doesn’t have to be an overwhelming experience.

Magnesium casting is a standard manufacturing method for creating lightweight, high-strength parts. The material’s characteristics make it ideal for various applications, including aerospace, automotive, and medical industries.
In this blog post, we’ll explore the basics of how to weld magnesium casting successfully. From understanding metal behavior and selecting the right tools for your desired outcome to safety precautions and tips on preheating and cooling techniques – we’ve got your back.
So if you’re ready to take the plunge into welding these lightweight yet durable metals for whatever projects may arise, get comfortable because by the end of this article – you’ll know exactly what steps to take in order to get started!
What Will You Need?
Before we dive into the process of welding magnesium casting, let’s take a look at some of the essential tools and materials you’ll need for a successful weld:
- Welding Equipment: It’s essential to choose your welding equipment carefully, as certain types of welding processes may not be suitable for magnesium castings. TIG (tungsten inert gas) welding is typically the preferred method for welding magnesium. This process uses a non-consumable tungsten electrode to produce the weld and is often used for thin materials, making it ideal for magnesium castings.
- Protective Gear: Welding can be hazardous, so having the appropriate personal protective equipment (PPE) is essential. This includes a welding helmet, gloves, apron, and safety glasses to protect your eyes from harmful UV rays.
- Magnesium Filler Rod: You’ll need a compatible filler rod when welding magnesium castings. It’s essential to choose the right type of filler rod, as using an incorrect one can result in a weak weld or even damage the casting itself.
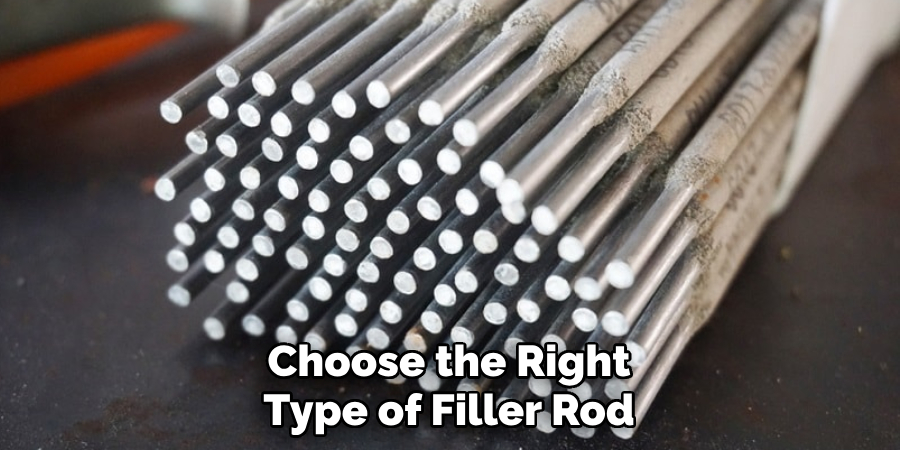
Once you have all the necessary tools and materials, it’s time to start the welding process. Keep reading to learn more about the steps in successfully welding magnesium castings.
10 Easy Steps on How to Weld Magnesium Casting
Step 1. Preparation:
Begin by thoroughly cleaning the surface of the magnesium casting that you will be welding. This step is critical as contaminants like oil, grease, or dirt can negatively affect the quality of the weld. Use a designated cleaning solution and a clean cloth to wipe the area. Once cleaned, avoid touching the area with bare hands, as skin oils can also interfere with welding.
Step 2. Preheating:
Preheating the magnesium casting can minimize the risk of cracking and improve the quality of the weld. Use a heat gun or an oven to preheat the casting to around 300-400 degrees Fahrenheit. This temperature range is typically recommended, but it might vary depending on the specific type of magnesium alloy you are working with. Ensure to heat the casting evenly to avoid any hot spots, which might result in uneven welding.
Step 3. Setting up the Welder:
Next, it’s time to set up your welding equipment. Configure your TIG welder according to the manufacturer’s instructions. Make sure you set the correct amperage for your specific magnesium casting – this can vary depending on the thickness of the material.
Too high amperage can burn through the casting, while too low may result in an ineffective weld. As a general rule of thumb, you can start with 1 amp per .001 inch of material thickness and adjust as needed. Also, prepare your filler rod by cleaning it with a designated solution to remove any potential contaminants.
Step 4. Start Welding:
Once everything is set up, you can start welding. Hold the torch in one hand and the filler rod in the other. The torch should be held at a 75 to 80-degree angle to the surface of the casting. Start by creating a small puddle of molten magnesium on the casting.
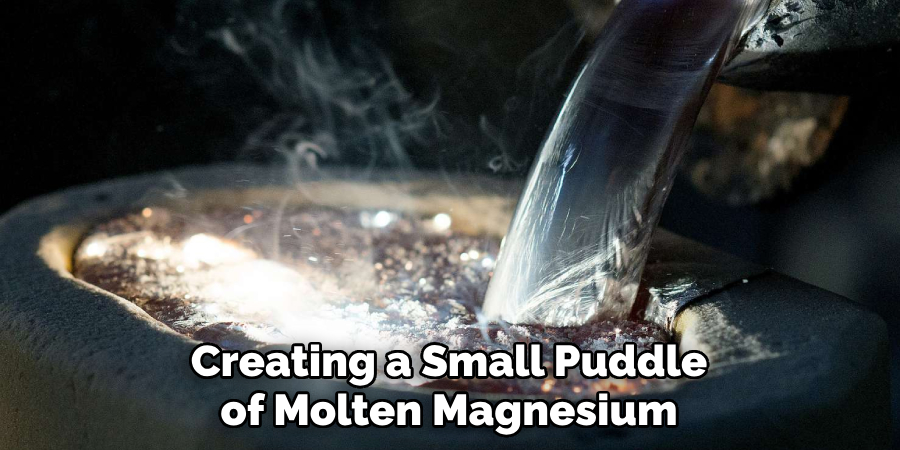
Then, dip the end of the filler rod into the puddle and move the torch along the seam to create the weld. Ensure a steady pace, allowing the molten pool to solidify behind the torch and create a smooth, clean weld. Always remember that practice is key to mastering this skill.
Step 5. Cooling Process:
After you have finished welding, allowing the magnesium casting to cool down properly is critical. Rapid cooling can cause the weld to crack due to thermal stress. Instead, let the casting cool naturally at room temperature. If you’re in a rush, you can use a heat-resistant blanket to slow the cooling process.
Avoid using water or other cooling aids as they may cause the weld to shrink too quickly and lead to cracking. Once the casting is completely cooled, you can proceed to the next steps of post-processing, such as grinding or polishing if needed.
Step 6. Post-Welding Inspection:
Once the casting has cooled down completely, it’s time to inspect your weld. Look for inconsistencies or imperfections, such as porosity, cracks, or lack of fusion. This step is essential as any defects can compromise the strength and durability of the weld.
You may use a magnifying glass or a dye penetrant inspection method for a detailed examination. If you find any defects, you must grind out the flawed area and re-weld it. Remember to clean the area thoroughly before re-welding.
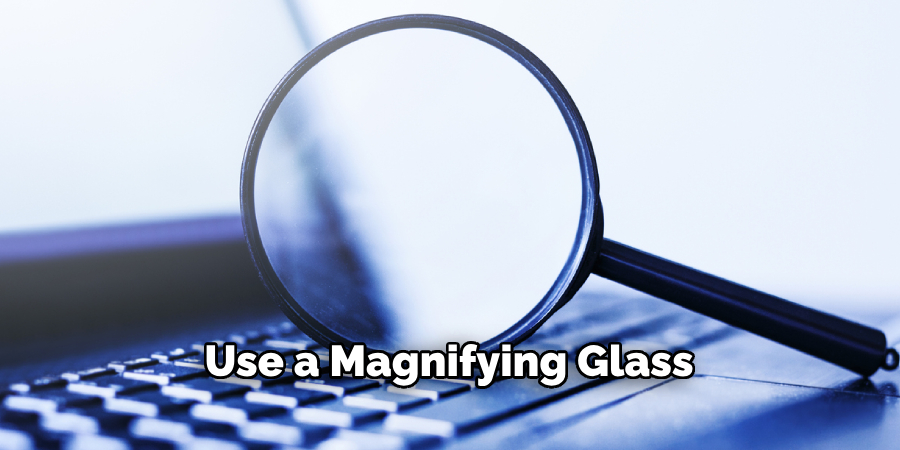
Step 7. Post-Welding Cleaning:
After your inspection, cleaning the welded area is necessary to remove any residues or contaminants that may have accumulated during the welding process. Use a stainless steel brush designed explicitly for magnesium to avoid cross-contamination with other metals. Brush in the direction of the weld to preserve the weld profile.
After brushing, clean the area with a damp cloth to remove any loose particles. This step will ensure your weld is clean and ready for any further processing or finishing touches.
Step 8. Post-Welding Treatment:
After cleaning, you may opt for a post-weld treatment depending on the needs of your project. Post-weld treatments can include stress relieving, heat treatment, or a protective coating. Stress relieving helps to reduce the residual stresses in the weld area that can lead to cracking over time.
Heat treating can improve the mechanical properties of the weld, enhancing its strength and hardness. If you choose to apply a protective coating, it can help prevent corrosion and enhance the weld’s overall appearance. Always remember the type of post-weld treatment selected should align with the intended use of the magnesium casting.
Step 9. Final Inspection and Testing:
Conduct a final weld inspection once all the post-weld treatments have been completed. This includes a visual examination to check the overall quality and uniformity of the weld, as well as more rigorous testing methods to validate the durability and strength of the weld.
Non-destructive testing (NDT) methods like ultrasonic testing or X-ray testing can detect any internal flaws or defects that are not visible to the naked eye. Ensure that the weld meets all the requirements for your specific application. Any issues discovered should be addressed promptly to prevent future problems.
Step 10. Maintenance and Care:
Post-weld care is as essential as the welding process itself. Ensure regular inspections and maintenance to prolong the life of the weld. For preventative measures, keep the weld clean and free from contaminants that might lead to corrosion.
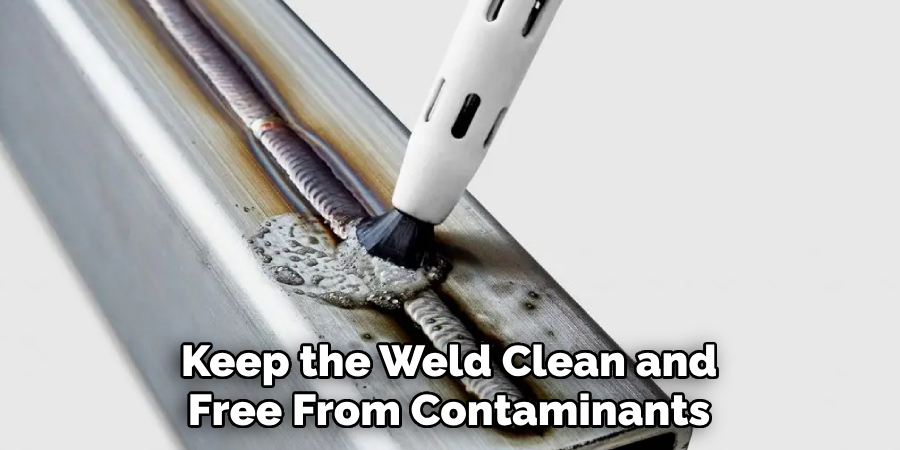
If the welded magnesium casting will be stored for an extended period, consider using a protective coating like quality wax or paint to preserve it. If any signs of damage or wear are noticed upon inspection, appropriate action should be taken immediately to rectify the issue. Remember, proper maintenance and care can significantly enhance the longevity and performance of the welded magnesium casting.
Following these steps gives you the knowledge and skills to weld magnesium castings effectively.
5 Things You Should Avoid
- Avoid Contamination: Be sure to avoid any form of contamination during welding. Even a small amount of foreign material can cause a poor-quality weld or even fail the weld.
- Avoid Incorrect Filler Material: Using the wrong type of filler material can drastically affect the quality and strength of your weld. Ensure you are using a filler material designed explicitly for magnesium.
- Avoid Overheating: With magnesium’s low melting point, overheating can easily occur. Overheating can warp the casting, making the weld weak and potentially dangerous.
- Avoid Uncontrolled Welding Speed: An unsteady welding speed can lead to defects like craters or cracks in the weld. Maintain a steady, controlled speed throughout the process.
- Neglecting Post-Weld Cleaning: Neglecting to clean after welding can lead to oxidation and corrosion over time, weakening the weld. Always ensure meticulous cleaning post-weld.
Avoiding these common mistakes can significantly improve the quality of your welding and the longevity of your magnesium casting.
Conclusion
In conclusion, how to weld magnesium casting is a complex but rewarding process. Aiming for high-quality welds requires practice and patience. However, if done correctly, the outcome can be far superior to any other welding type.
Learning how to weld colored magnesium castings requires not only comprehension of the principles and techniques that go into welding in general but also specialized knowledge about each type of welding technique you will need to use with different kinds of magnesium alloy you come across.
As such, it’s essential to take the advice given in this article seriously to produce a safe and successful weld. If all else fails or if you need clarification on something related to welding, seek out help from experienced professionals who can walk you through their more advanced techniques.
With diligence, a thorough understanding of the craft, and safety guidelines, your next project involving magnesium casting will undoubtedly be both satisfying and successful!
Edmund Sumlin is a skilled author for Metal Fixes, bringing 6 years of expertise in crafting a wide range of metal fixtures. With a strong background in metalwork, Edmund’s knowledge spans various types of fixtures, from decorative pieces to functional hardware, blending precision with creativity. His passion for metalworking and design has made him a trusted resource in the industry.
Professional Focus:
- Expert in Metal Fixtures : Edmund aesthetic specializes in creating durable and innovative metal fixtures, offering both appeal and functionality. His work reflects a deep understanding of metalworking techniques and materials.
- Sustainability Advocate : He is dedicated to using sustainable practices, ensuring that every fixture is crafted with eco-friendly methods while maintaining high-quality standards.
In his writing for Metal Fixes, Edmund provides valuable insights into the latest trends, techniques, and practical advice for those passionate about metal fixtures, whether they are professionals or DIY enthusiasts. His focus on combining artistry with engineering helps others discover the true potential of metal in design.