Are you looking for a way to master the skill of stick welding? Have you been struggling to weld vertically? If so, then you have come to the right place. Stick welding is one of the most reliable and effective methods used in metal fabrication, but it can be tricky when trying to do a vertical weld.
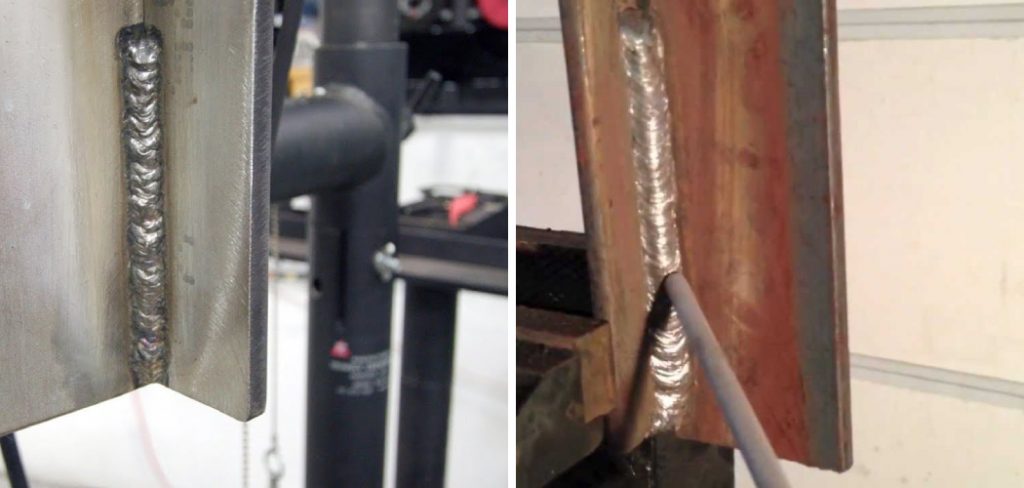
In this blog post on how to stick weld vertically, we will break down how stick welding works, its advantages and the formulae needed to make sure your verticle welding job is done correctly and safely. Keep reading for all the details on mastering the art of sticking weld vertically!
Necessary Materials
Before we dive into the steps for vertical stick welding, let’s first make sure you have all the necessary materials. Here are the items you will need:
Stick Welder:
This is a type of arc welding machine that uses a consumable electrode coated in flux to create an electric arc between the metal being welded and the electrode. A stick welder is essential for stick welding, and it comes in various sizes and power capabilities.
Electrode Holder:
This is a clamp-like device that holds the electrode securely in place while you weld. It is essential to have a good quality holder to avoid any accidents.
Welding Cable:
These are heavy-duty cables that connect the stick welder to the electrode holder. The welding cable needs to be of good quality and the right length to ensure a safe welding experience.
Welding Helmet:
The intense light produced during stick welding can cause damage to your eyes if proper precautions are not taken. A welding helmet is an essential piece of safety equipment that protects your face and neck from sparks, radiation, and heat.
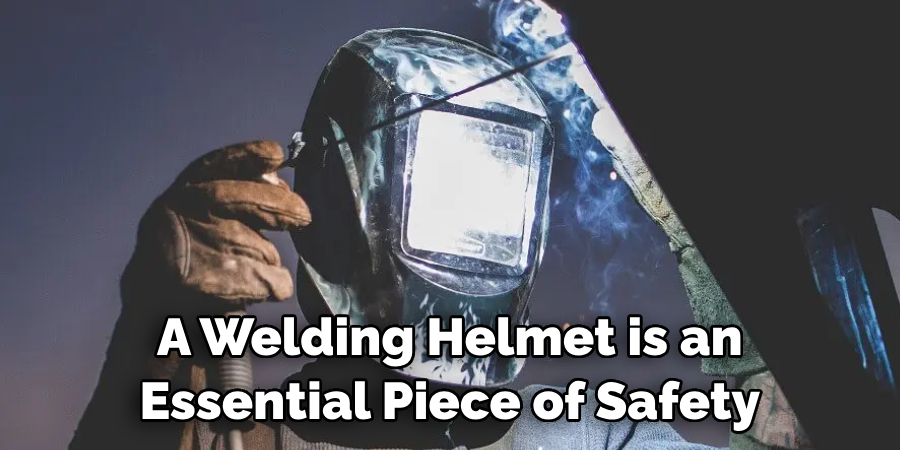
Protective Gear:
It is crucial to protect yourself with the right gear while welding. This includes a welding jacket, gloves, and boots.
Materials to Weld:
For vertical stick welding, you will need two pieces of metal that are in need of joining. Make sure the surfaces are clean and free from rust or other contaminants.
10 Step-by-step Guides on How to Stick Weld Vertically
Step 1: Prepare Your Work Area
Before you start welding, it is crucial to prepare your work area. Make sure the surface is clean and free from any flammable materials that could catch fire. Keep a fire extinguisher nearby, just in case. You should also make sure you have enough room to move around freely. It is best to work in a well-ventilated area or outdoors.
Step 2: Select the Right Electrodes
There are different types of electrodes available for stick welding, and each has its specific use. For vertical welding, you will need an electrode with high cellulose content as it creates a stable arc that is ideal for vertical welds. Make sure to read the manufacturer’s recommendations before choosing an electrode. Otherwise, you may end up with a failed weld.
Step 3: Set Up Your Welder
Once you have chosen the right electrodes, it is time to set up your welder. Make sure the power is off and that all the cables are securely connected. You should also check the welding machine’s settings to ensure they are suitable for vertical welding. It is recommended to start with a lower amperage and adjust as needed. But remember, the lower the amperage, the slower you will need to move.
Step 4: Prepare the Electrode
Before striking an arc, you must prepare your electrode. Remove any rust or debris from the end of the electrode with a wire brush. You should also check that there is enough flux coating on it; otherwise, it may not stick properly to the metal. It is also crucial to keep the electrode dry at all times, as moisture can affect its performance.
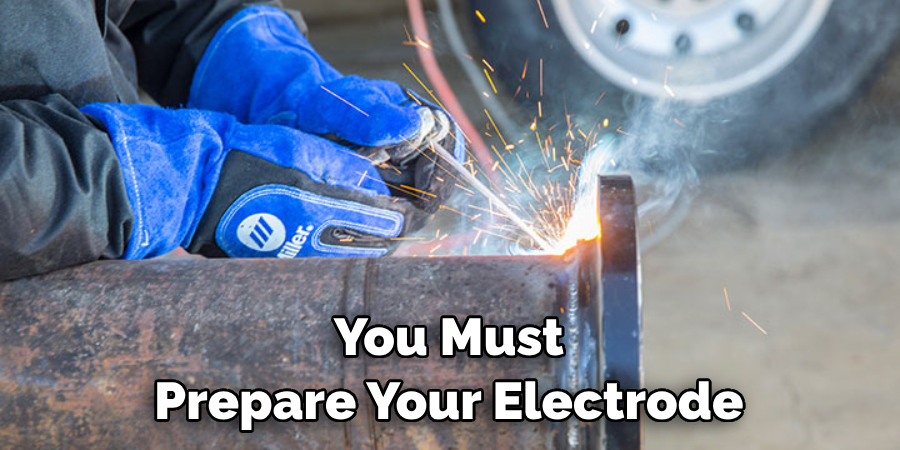
Step 5: Strike an Arc
With your electrode prepared, it is time to strike an arc. Place the electrode’s tip close to the metal’s surface and then lift it slightly until you hear a sizzling sound. Hold the electrode in this position for about two seconds, and you should see an arc form. You can then move on to the next step. This step may take a few attempts to get right, so be patient.
Step 6: Start Welding
Once you have struck an arc and the weld pool has formed, start welding by moving your electrode slowly up the metal. Remember to keep a consistent distance between the electrode and the metal for a stable arc. You should also avoid weaving or whipping motion, as this can cause the weld to fail. Instead, move in a straight line.
Step 7: Maintain Proper Arc Length
Maintaining the correct arc length is crucial for vertical welding. If the arc is too long, it will create an unstable flame and affect the quality of your weld. On the other hand, if the arc is too short, you may end up with a failed weld. A good rule of thumb is to maintain an arc length of around a quarter inch. It should also look like a pointed flame rather than a ball or cone shape. But remember, the arc length may vary depending on your electrode size and welding machine settings.
Step 8: Move Slowly
Unlike horizontal welding, vertical welding requires more control and patience. Moving too quickly or erratically can result in a failed weld. So, make sure to move slowly and steadily while maintaining the correct arc length. You should also keep an eye on the heat produced to avoid overheating your metal. However, if you notice the weld is starting to cool too quickly, you may need to increase your welding speed.
Step 9: Allow the Weld to Cool
Once you have completed your vertical weld, it is essential to allow it to cool before moving onto the next step. This will give the weld pool time to solidify, which is essential for a strong and durable weld. You can also use a heat-resistant blanket or insulation to help the weld cool down more quickly.
Step 10: Clean Up
After your weld has cooled, it is time to clean up. Use a wire brush to remove any slag or debris from the weld. You should also inspect your weld for any defects and make necessary adjustments if needed. Once the area is clean, you can move on to the next welding job or take a well-deserved break.
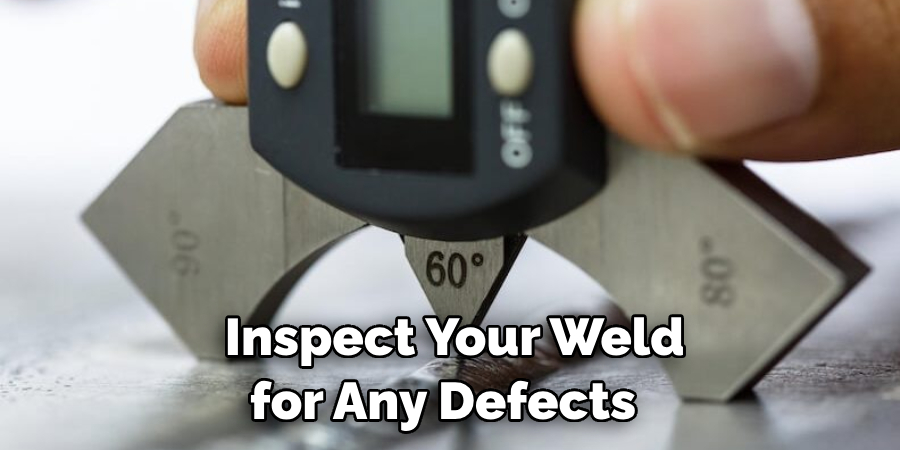
Following these ten steps on how to stick weld vertically will help you achieve a successful vertical stick weld. Remember to always prioritize safety and use the right equipment for the job.
With practice and patience, you will become a skilled vertical stick welder in no time. So, get out there and start welding! Keep improving your skills by trying different techniques and experimenting with different electrodes and welding machines.
How Much Could It Cost?
The cost of stick welding vertically may vary depending on the equipment and materials you use. A basic stick welder can range from $200 to $1000, while electrodes can cost anywhere from $10 to $50 per pack.
You will also need to consider the cost of protective gear, such as a welding helmet and jacket, which can range from $50 to $300. Additionally, the cost of electricity and gas may also factor into your overall expenses. However, with proper maintenance and care, these costs can be minimized in the long run.
Frequently Asked Questions
Q: Can I Weld Vertically With Any Type of Electrode?
A: No, for vertical stick welding, it is recommended to use an electrode with high cellulose content. It creates a stable arc and produces quality welds.
Q: Is Vertical Welding More Difficult Than Horizontal Welding?
A: Yes, vertical welding requires more control and patience compared to horizontal welding. It also takes more time to master the technique.
Q: Can I Weld Vertically in Any Position?
A: No, for vertical stick welding, you should only work in the vertical position. Attempting to weld vertically in other positions can result in a failed weld and potential safety hazards.
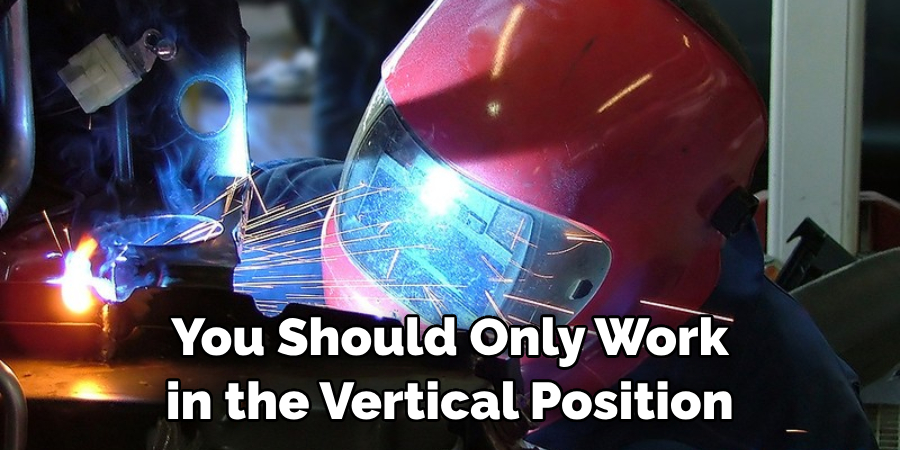
Q: Why Is Proper Arc Length Important for Vertical Welding?
A: Maintaining the correct arc length is crucial as it affects the stability of the arc and the quality of your weld. Too long or too short of an arc can result in a failed weld.
Conclusion
By now, you have worked your way through the basics of vertical stick welding. You understand what equipment you need, and why it is important to maintain the proper angles for sticking. You know some welding accessories that can make the job easier and improve the quality of your welds. You should be ready to start trying out some vertical welding projects of your own! Take your time, practice with scrap materials, and don’t be afraid to experiment.
Most importantly, wear safety equipment at all times, including a welder’s helmet and gloves.. This will enable you to tackle any future stick-welding projects with greater confidence! Thanks for reading this article on how to stick weld vertically.
Edmund Sumlin is a skilled author for Metal Fixes, bringing 6 years of expertise in crafting a wide range of metal fixtures. With a strong background in metalwork, Edmund’s knowledge spans various types of fixtures, from decorative pieces to functional hardware, blending precision with creativity. His passion for metalworking and design has made him a trusted resource in the industry.
Professional Focus:
- Expert in Metal Fixtures : Edmund aesthetic specializes in creating durable and innovative metal fixtures, offering both appeal and functionality. His work reflects a deep understanding of metalworking techniques and materials.
- Sustainability Advocate : He is dedicated to using sustainable practices, ensuring that every fixture is crafted with eco-friendly methods while maintaining high-quality standards.
In his writing for Metal Fixes, Edmund provides valuable insights into the latest trends, techniques, and practical advice for those passionate about metal fixtures, whether they are professionals or DIY enthusiasts. His focus on combining artistry with engineering helps others discover the true potential of metal in design.