Are you a welder looking to learn how to weld pot metal? Look no further. This guide will give you all the information you need to weld pot metal successfully.
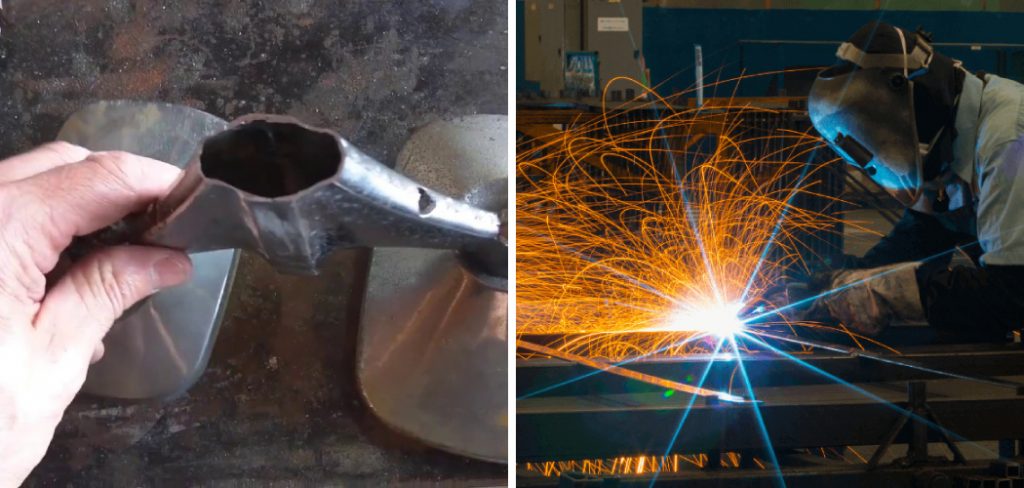
If you’ve ever wanted to learn how to weld a pot metal, you’re in the right place! With a little effort and dedication, anyone can master the art of welding pot metal. It takes patience and practice, but have no fear – this blog post will cover all the basics so that you can learn to weld quickly and efficiently. We’ll start with some general information about pot metal before diving into several techniques for achieving success in your projects.
By the end of this blog post, you should know everything there is to know about welding pot metal!
What Will You Need?
Before we start, let’s review the tools and materials you’ll need to weld pot metal. These include:
- A welding machine (MIG or TIG)
- Protective gear (welding helmet, gloves, apron, etc.)
- Pot metal filler rod
- Wire brush for cleaning
- Grinding tool for finishing
Ensure you have all these items on hand before beginning your welding project.
10 Easy Steps on How to Weld Pot Metal
Step 1. Preparation:
Start by cleaning the area of the pot metal that you plan to weld. Use your wire brush to remove any dirt, grease, or rust. This step is crucial as a clean welding surface will result in a stronger and more secure weld.
Step 2. Preheating:
Preheating the pot metal is a critical step before starting the welding process. Use a heat gun or a torch to weld the area gradually. This step helps prevent metal cracking due to sudden temperature changes during welding. Remember not to overheat, as it may cause the metal to warp or melt.
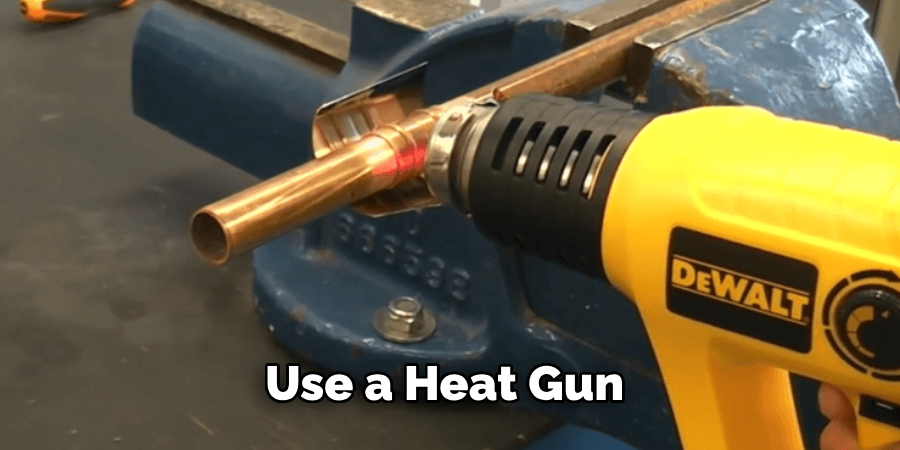
Step 3. Applying the Filler:
Once the metal is adequately heated, it’s time to apply the filler rod. Hold the filler rod in one hand and the torch in the other. Slowly feed the filler rod into the joint while moving the torch along the joint line. This step will require a steady hand and concentration to ensure a clean and efficient weld.
Step 4. Welding:
At this point, you can begin welding. Ignite your welding torch and adjust its flame to an appropriate size. Now, get into a comfortable position and start welding along the joint. Make sure to fuse at a steady pace, not too fast or too slow, to ensure an even heat distribution. Permanently weld in small sections to avoid overheating the pot metal, which can cause it to warp or melt. Maintain focus to ensure the welding bead forms a smooth line along the joint.
Step 5. Cooling Down:
After you finish welding, letting the pot metal cool down naturally is essential. Rapid cooling might introduce stress into the metal, leading to potential cracks. To ensure the weld’s integrity, avoid touching or moving the welded piece until it has cooled down completely. Remember, patience is essential during this step.
Step 6. Inspection:
After the pot metal has cooled down, it’s time for inspection. Check the welded joint for imperfections, such as cracks, porosity, or inconsistencies in the weld bead. A well-executed weld should be smooth and uniform, with no visible defects. You should grind down the problematic area and re-weld it if you notice any issues. Always remember quality is key in welding, and it’s better to take your time and get it right than to rush and end up with a subpar weld.
Step 7. Grinding and Smoothing:
The next step involves grinding and smoothing the welded joint. Use a grinding tool to remove any excess material from the weld. This will help in creating a smooth and flat surface. Always remember to wear protective gear during this process to prevent any injuries. Grinding not only improves the appearance of the weld but also prepares the surface for the final finishing.
Step 8. Final Finishing:
After grinding, the final step is to finish the weld. You can use fine-grit sandpaper to make the surface even smoother. After sanding, wash the welded area with soap and water to remove any residual grinding dust and pat dry. Applying a layer of clear lacquer or paint can further protect the weld and provide a polished look. Take your time with this step. A quality finish is the sign of a well-done welding job.
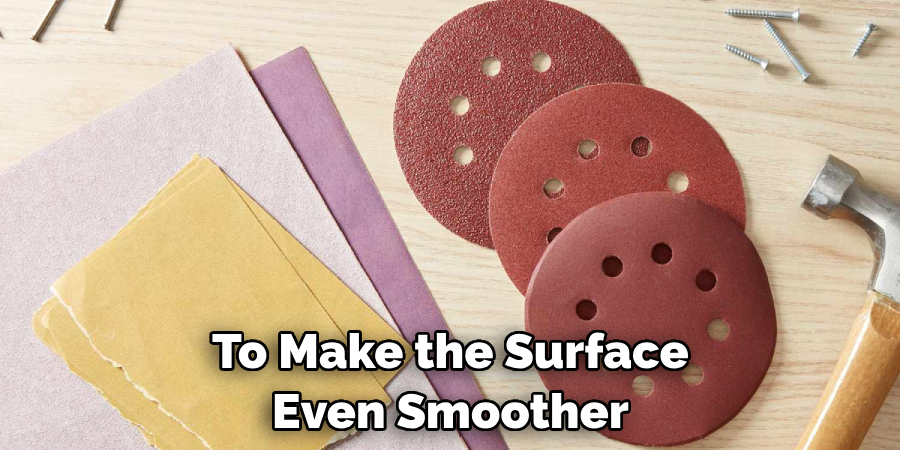
Step 9. Post-Welding Inspection:
Once the finishing is done, perform another inspection. Look for any signs of cracks or defects that might have developed during the grinding or finishing process. If everything looks good, then congratulations! You’ve successfully welded pot metal.
Step 10. Clean-up:
Lastly, always remember to clean up your workspace. Put away all your tools and equipment, discard waste materials, and ensure your workspace is safe and ready for your next welding project. Proper clean-up and maintenance of your workspace can significantly improve your overall welding efficiency and safety.
By following these ten simple steps, you can successfully weld pot metal and create beautiful projects with this versatile material.
5 Additional Tips and Tricks
Tip 1. Practice Makes Perfect:
As with any skill, the more you practice welding pot metal, the better you will become. Start with simple projects and gradually take on more complex ones as your confidence and skill level increase.
Tip 2. Safety First:
Never compromise on safety. Always wear the appropriate protective gear, including a welding helmet, gloves, and apron. It’s also essential to have proper ventilation in your workspace to avoid inhaling any harmful fumes.
Tip 3. Choose the Right Filler Rod:
Different types of pot metal may require other filler rods for successful welding. Research and select the appropriate filler rod for your specific project.
Tip 4. Seek Professional Help if Needed:
If you encounter any difficulties while welding pot metal, don’t hesitate to seek professional help. It’s always better to ask for guidance rather than risk damaging your project or causing harm to yourself.
Tip 5. Experiment with Different Techniques and Tools:
Welding is an art, and everyone has their own style and techniques. Feel free to try out different tools and techniques to find what works best for you. Remember, there’s always room for improvement, so keep practicing and learning new things.
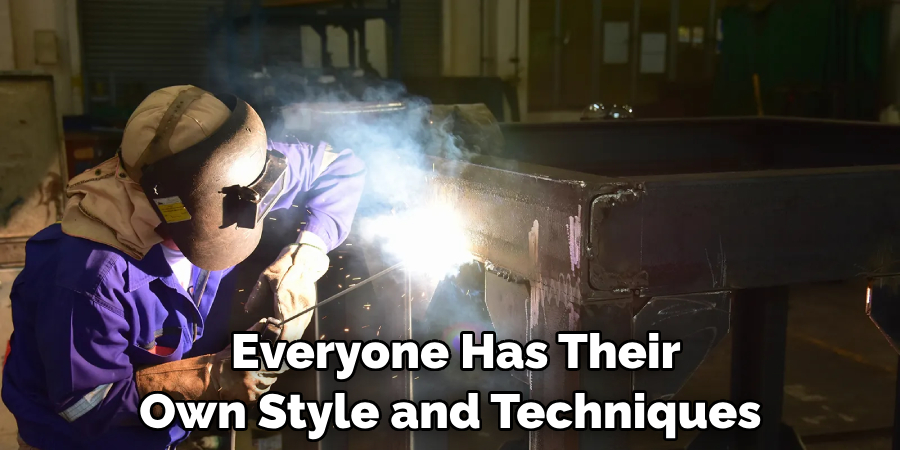
With these additional tips and tricks, you can elevate your welding skills and confidently tackle any pot metal project that comes your way.
5 Things You Should Avoid
Thing 1. Rushing the Process:
Avoid rushing through the steps of welding pot metal. Each phase requires careful attention and patience to ensure a high-quality result.
Thing 2. Welding without Proper Ventilation:
Only weld in a space with proper ventilation. Welding can release harmful fumes that, if inhaled, can lead to severe health issues. Always ensure you are working in a well-ventilated area or use a professional fume extraction system.
Thing 3. Ignoring Safety Measures:
Always prioritize safety. Ignoring safety measures such as not wearing protective gear or neglecting to keep a fire extinguisher on hand can lead to severe injuries. Follow all safety protocols to ensure a safe working environment.
Thing 4. Using Incorrect Filler Material:
Using the right filler material can lead to strong joints or even damage the pot metal. Make sure to select the right filler rod that is compatible with the pot metal you are working on.
Thing 5. Disregarding Inspection:
Pay attention to the inspection phase. It is crucial to thoroughly inspect the weld for any defects or inconsistencies before and after the grinding and finishing process. Overlooking this step can result in subpar welds and compromise the integrity of your project.
By avoiding these things, you can ensure a successful and safe welding experience with pot metal. With practice and the right techniques, you can master the art of welding this unique material and create beautiful projects that will last for years.
What Glue Works on Pot Metal?
If you don’t have a welding setup, or your pot metal project is small and delicate, glue might be a better option. However, not all adhesives are suitable for pot metal due to their unique composition. Here are some of the best glues that can effectively bond pot metal:
- Epoxy: This strong adhesive creates a chemical bond between two surfaces, making it a reliable choice for pot metal. Epoxy comes in different formulas, so choose one suitable for metals.
- Cyanoacrylate (super glue): This fast-drying adhesive can create a strong bond between pot metal and other materials. However, there may be better options for larger or heavier pieces as it can become brittle over time.
- Polyurethane: This adhesive is known for its strength and flexibility, making it suitable for bonding pot metal. It also has excellent resistance to heat and chemicals.
- Polyvinyl acetate (PVA) glue: Also known as wood glue, PVA glue can be a suitable option for smaller pot metal projects. It forms a strong bond and dries clear, making it ideal for visible joints.
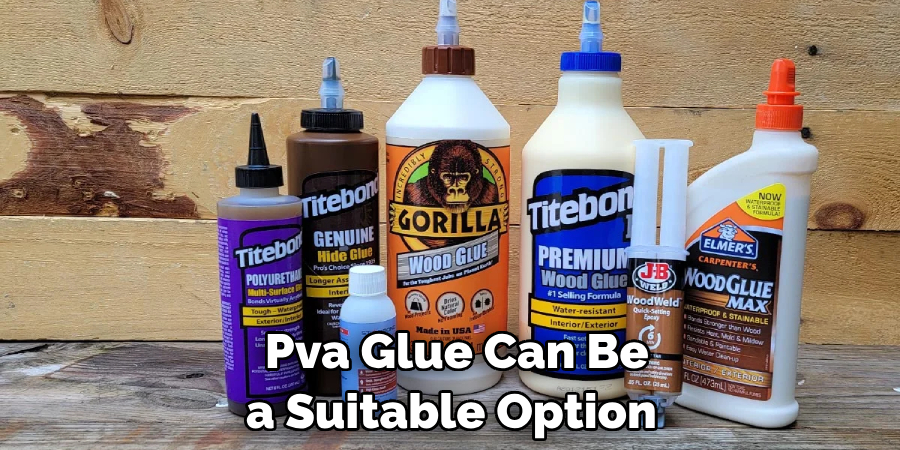
It’s essential to follow the instructions on the glue packaging carefully and allow enough time for the adhesive to cure before handling or putting stress on the bonded pieces.
Conclusion
In conclusion, how to weld pot metal requires a delicate touch and a great skill to complete the project correctly. With the proper knowledge and resources, pot metal can be successfully welded and used for various tasks.
However, if you haven’t done this type of welding before, practice on scrap pieces of metal first before attempting something more ambitious. Additionally, it’s essential to ensure you have the proper safety gear, including safety goggles, protective clothing, and a respirator when welding pot metal.
As a reminder, always take safety precautions when working with material like this! Lastly, patience is critical to success in pot metal welding, as it takes years of practice and dedication to master.
So get out there and start practicing – with enough diligence, you’ll soon find yourself creating beautiful welds with pot metal in no time!
Edmund Sumlin is a skilled author for Metal Fixes, bringing 6 years of expertise in crafting a wide range of metal fixtures. With a strong background in metalwork, Edmund’s knowledge spans various types of fixtures, from decorative pieces to functional hardware, blending precision with creativity. His passion for metalworking and design has made him a trusted resource in the industry.
Professional Focus:
- Expert in Metal Fixtures : Edmund aesthetic specializes in creating durable and innovative metal fixtures, offering both appeal and functionality. His work reflects a deep understanding of metalworking techniques and materials.
- Sustainability Advocate : He is dedicated to using sustainable practices, ensuring that every fixture is crafted with eco-friendly methods while maintaining high-quality standards.
In his writing for Metal Fixes, Edmund provides valuable insights into the latest trends, techniques, and practical advice for those passionate about metal fixtures, whether they are professionals or DIY enthusiasts. His focus on combining artistry with engineering helps others discover the true potential of metal in design.