Ready to become an overhead welding master? With a few simple steps, you can easily upgrade your welding skillset and begin applying them in more diverse and challenging situations. Overhead welding is a great way to enhance the strength of various projects, such as aircraft or car parts repair, bridge building, or creating artistic pieces for display.
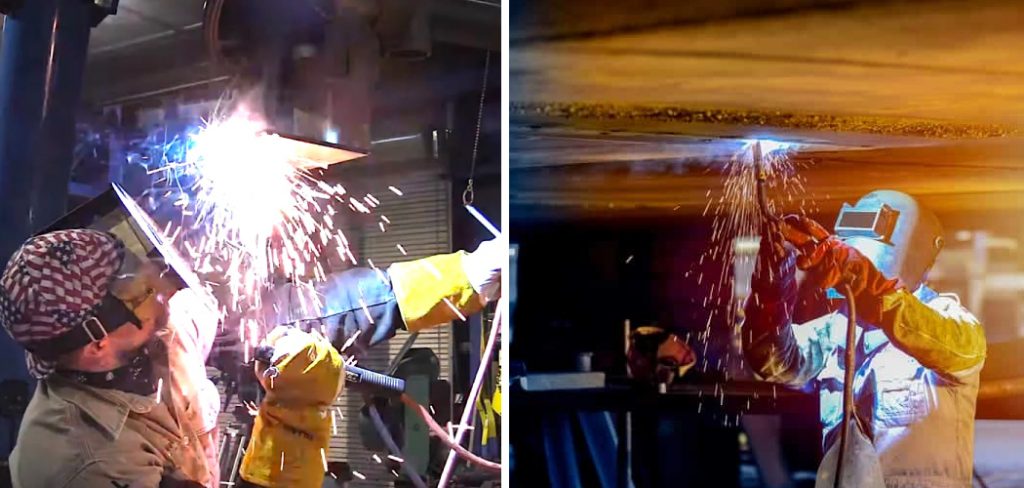
Whether you’re brand new to the art of welding or just looking to brush up on basic skills like overhead joint composition or safety aspects associated with high metal temperatures, this post on how to weld overhead will provide you with all the information you need before getting started. Let’s dive in!
What is Overhead Welding?
Overhead welding is a type of welding where the welder operates above their head level, joining two pieces of metal that are placed horizontally or vertically. It requires special techniques and equipment compared to other types of welding, as the welder must maintain control over the molten metal and ensure proper penetration and deposition. This method is widely used in construction, fabrication, and repair work.
11 Step-by-step Guidelines on How to Weld Overhead
Step 1: Gather the Necessary Equipment
Before you begin, make sure you have all the necessary equipment for overhead welding. This includes a welding machine, protective gear (such as gloves, helmet, and apron), electrodes or filler material, and any other tools required to prepare the joint. It is important to have everything ready before starting the welding process.
Step 2: Prepare the Work Area
Make sure your work area is clean and free of any flammable materials. Also, check for proper ventilation to avoid inhaling harmful fumes while welding. If necessary, set up a ventilation system or wear a respirator.
You should also position your workpiece at a comfortable height and angle to ensure you have good visibility and control over the welding process. But be sure not to compromise your safety for comfort. It is also a good idea to have a fire extinguisher nearby, just in case.
Step 3: Choose the Right Electrode
Selecting the right electrode is crucial for successful overhead welding. Generally, low-hydrogen electrodes are recommended as they have better penetration and deposit metal more effectively compared to other types of electrodes.
It is important to choose the appropriate electrode size and amperage as well, which can be determined by consulting with a certified welder or referring to the manufacturer’s recommendations.
Step 4: Clean The Workpiece
Before welding, make sure that all surfaces of the workpiece are clean and free of any contaminants such as oil, rust, or paint. Any impurities can affect the welding process and lead to weak or incomplete welds. You can clean the surface with a wire brush or grinder, depending on the thickness and type of material. You should also ensure that the edges of the joint are properly prepared for welding.
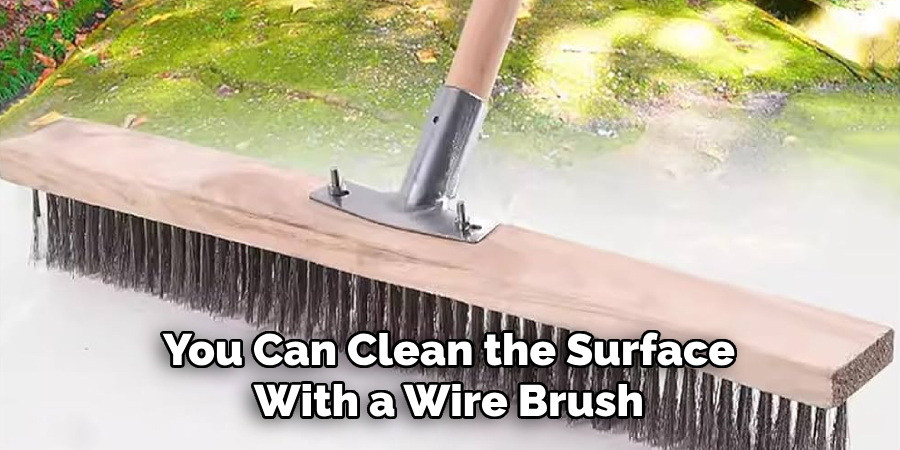
Step 5: Position Yourself and Your Equipment
For overhead welding, it is important to position yourself and your equipment in a way that allows you to reach the workpiece comfortably. Securely attach your electrode holder or torch clamp to the welder’s cable to avoid any accidents.
Make sure you have a good grip on the electrode holder or torch clamp to maintain control over the welding process. Otherwise, it can result in poor-quality welds or cause injuries.
Step 6: Strike an Arc
Once you are ready to begin welding, carefully strike an arc by touching the electrode to the workpiece and then quickly pulling it away. This will create a small spark that will ignite the arc. You should be able to see the molten metal pooling at the start of the weld.
If you are using a MIG or TIG welder, refer to your equipment’s manual for specific instructions on how to strike an arc. You can also practice by striking an arc on a scrap piece of metal before starting the actual welding.

Step 7: Control the Arc Length
Maintaining proper arc length is crucial for overhead welding. You should keep the end of the electrode within 1/8 inch from the workpiece while welding. This will ensure that the arc remains stable and prevents any molten metal from dripping onto your skin or protective gear.
It also helps in achieving proper penetration and deposition of filler material. You can adjust the arc length by moving closer or further away from the workpiece.
Step 8: Move Slowly
Overhead welding requires slow and steady movements to maintain control over the molten metal. You should move the electrode or torch at a steady pace along the joint, making sure to maintain proper arc length and angle. This allows for effective penetration and uniform deposition of filler material, resulting in strong welds. If you move too quickly, it can lead to weak or incomplete welds.
Step 9: Watch Out for Drips
While welding, always be aware of any molten metal that may drip from the workpiece. It is important to wear protective gear and position yourself in a way that minimizes the chances of getting burned.
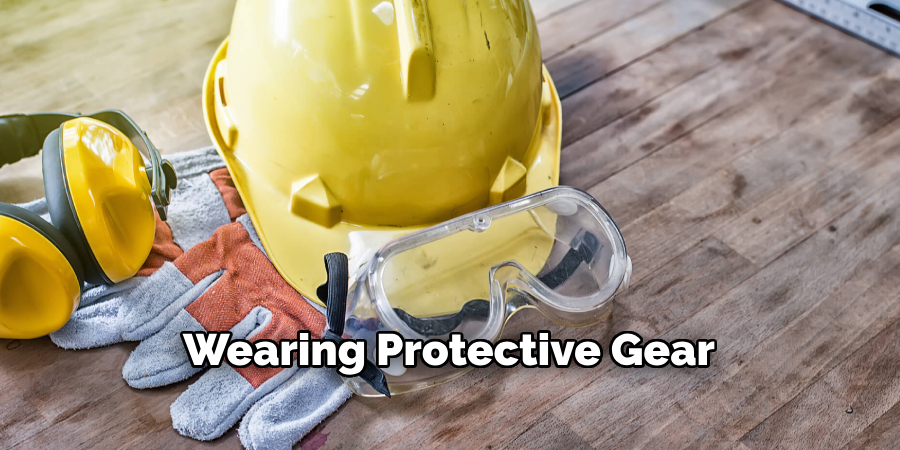
If you notice any drips, you can quickly move the electrode or torch away from that area and then continue welding. However, if you are unable to maintain control over the molten metal, it may be necessary to stop and restart the weld.
Step 10: Use the Backstepping Technique
Backstepping is a technique used in overhead welding where you start at one end of the joint and then work your way back to the starting point. This helps in controlling the heat buildup and prevents excessive distortion of the workpiece. You should continue this technique until you reach the end of the joint, making sure to maintain proper arc length and angle.
Step 11: Finish Strong
As you approach the end of the weld, make sure to finish strong by maintaining control over the molten metal until the end of the joint. You can then slowly remove the electrode or torch and allow the weld to cool down before handling it. Once cooled, check for any defects or imperfections in the weld and make necessary adjustments for future welds.
Following these step-by-step guidelines on how to weld overhead can help you successfully weld overhead and achieve strong, reliable welds. Remember to always prioritize safety and seek professional guidance if needed. With practice and patience, you will become more comfortable with this challenging yet essential welding technique. So go ahead and put your skills to the test!
Frequently Asked Questions
Q: Can I Use Any Type of Electrode for Overhead Welding?
A: It is recommended to use low-hydrogen electrodes for overhead welding as they provide better penetration and deposit metal more effectively. However, it is important to consult with a certified welder or refer to the manufacturer’s recommendations to determine the appropriate electrode size and amperage for your specific project.
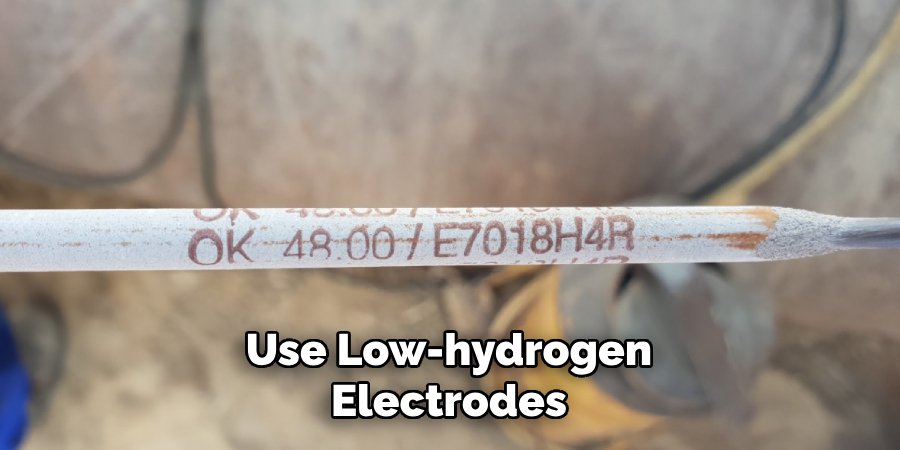
Q: What Should I Do If I Notice Drips While Overhead Welding?
A: If you notice any molten metal dripping from the workpiece, quickly move the electrode or torch away from that area and continue welding. However, if you are unable to maintain control over the molten metal, it may be necessary to stop and restart the weld. Prioritizing safety and wearing proper protective gear can help minimize the risk of getting burned.
Q: What is the Backstepping Technique in Overhead Welding?
A: The backstepping technique involves starting at one end of the joint and working your way back to the starting point, controlling the heat buildup and minimizing distortion of the workpiece. It is recommended to use this technique for overhead welding to achieve strong and uniform welds.
Q: How Can I Check for Defects or Imperfections in the Weld?
A: Once the weld has cooled down, visually inspect it for any defects or imperfections such as cracks, undercutting, or incomplete fusion. You can also use non-destructive testing methods such as ultrasonic testing to check for any internal defects.
If you notice any issues, make necessary adjustments and practice to improve your welding skills. Overall, it is important to continuously monitor and evaluate your welds for quality assurance. So go ahead and put your skills to the test!
Conclusion
In conclusion, learning how to weld overhead is a valuable skill to have when it comes to metalworking and repair projects. By following the steps outlined in this blog post – determining what type of overhead welding you are doing, gathering the necessary equipment, and ensuring your safety before beginning – you can begin successfully welding overhead and even take on more complex projects.
With practice, preparation, and caution, you can quickly become proficient at welding in this position. Let today be the day that you learn something new that will stay with you for years; make it one more checked-off step in becoming an expert welder. Don’t hesitate – pick up those safety goggles and get ready to put some sparks into your welding journey!
Edmund Sumlin is a skilled author for Metal Fixes, bringing 6 years of expertise in crafting a wide range of metal fixtures. With a strong background in metalwork, Edmund’s knowledge spans various types of fixtures, from decorative pieces to functional hardware, blending precision with creativity. His passion for metalworking and design has made him a trusted resource in the industry.
Professional Focus:
- Expert in Metal Fixtures : Edmund aesthetic specializes in creating durable and innovative metal fixtures, offering both appeal and functionality. His work reflects a deep understanding of metalworking techniques and materials.
- Sustainability Advocate : He is dedicated to using sustainable practices, ensuring that every fixture is crafted with eco-friendly methods while maintaining high-quality standards.
In his writing for Metal Fixes, Edmund provides valuable insights into the latest trends, techniques, and practical advice for those passionate about metal fixtures, whether they are professionals or DIY enthusiasts. His focus on combining artistry with engineering helps others discover the true potential of metal in design.