Are you curious about how steel is made? Look no further! This guide will walk you through the process of how to make iron into steel. Steel is a versatile and strong metal that has been used for centuries in construction, manufacturing, and more.
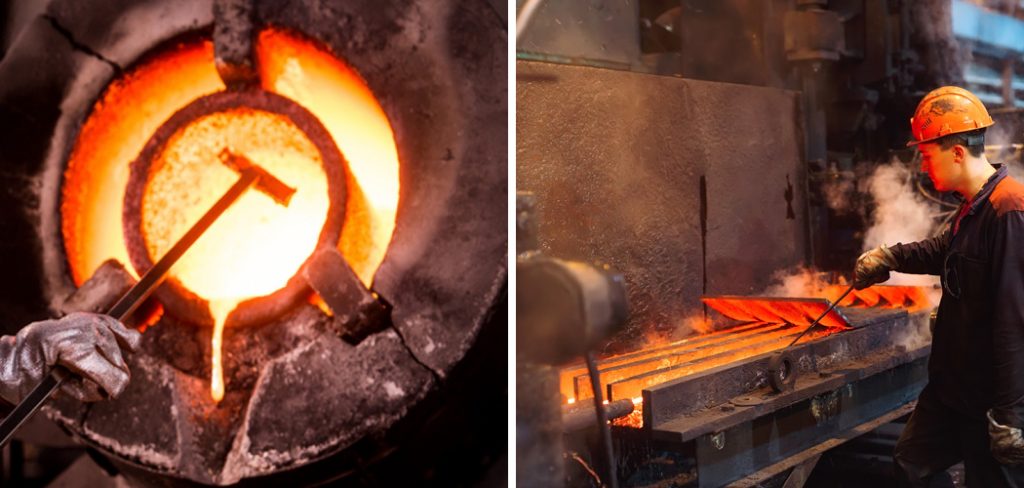
Transforming iron into steel is a process that has been foundational to industrial advancements and modern engineering.
Steel, an alloy primarily composed of iron and carbon, boasts superior strength, durability, and flexibility compared to its pure iron counterpart.
The journey from iron to steel involves intricate procedures, including the removal of impurities, the precise addition of alloying elements, and controlled cooling processes.
Understanding these steps is essential for producing high-quality steel tailored to various applications, from construction and automotive manufacturing to consumer goods and infrastructure projects.
This guide delves into the key phases of steel production and outlines the methods and technologies employed to achieve this remarkable transformation.
What are the Benefits of Making Iron Into Steel?
Before we discuss the process of making iron into steel, let’s explore why this transformation is so important. Steel has numerous advantages over pure iron, which makes it a highly sought-after material in various industries.
- Strength and Durability: As mentioned earlier, steel is much stronger and more durable than pure iron. The addition of carbon and other alloying elements strengthens the iron’s molecular structure, making it more resistant to stress and wear.
- Versatility: Steel can be produced in a wide range of grades and forms, making it suitable for various applications. From high-strength structural steel used in skyscrapers to low-carbon steel used in kitchen appliances, steel can be tailored to meet specific needs.
- Cost-Effective: While the production of steel involves complex processes, it is still a cost-effective material compared to other metals like aluminum and titanium. This is because iron, one of the main components of steel, is abundant and readily available.
- Sustainability: Steel is also a sustainable option as it can be recycled indefinitely without losing its properties. This not only reduces the need for new steel production but also helps to minimize waste and conserve natural resources.
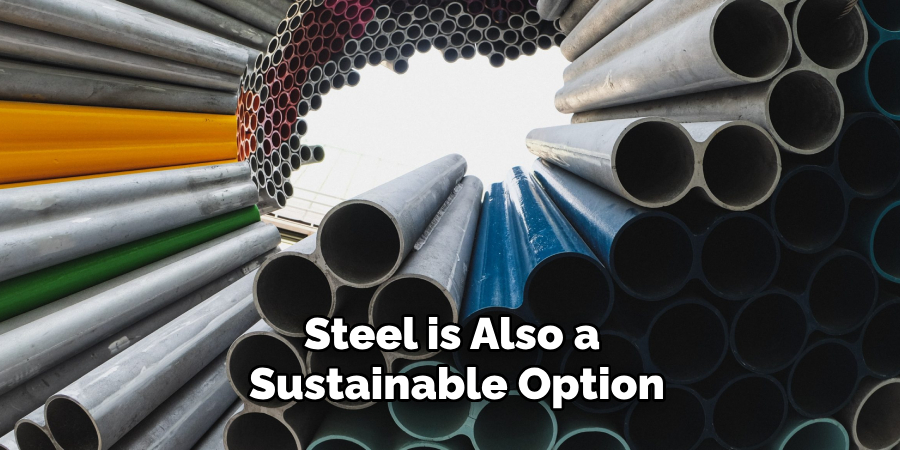
These are just a few of the many benefits of making iron into steel. Now, let’s move on to the actual process of transforming iron into this versatile and essential metal.
What Will You Need?
In order to make iron into steel, you will need the following materials and equipment:
- Iron Ore: This is the primary source of iron and can be found in abundance in various parts of the world.
- Coal or Coke: These are used as a fuel source to heat up the iron ore.
- Limestone: This acts as a fluxing agent, helping to remove impurities from the iron ore.
- Furnace: A furnace heats and melts iron ore, coal or coke, and limestone.
- Alloying Elements: These can include carbon, chromium, nickel, and other metals that are added in precise quantities to create specific grades of steel.
- Water: Water is needed for the cooling process.
- Molds and Shaping Tools: These are used to shape and form the molten steel into various products.
Now that you have everything you need, let’s dive into the steps for turning iron into steel.
10 Easy Steps on How to Make Iron Into Steel
Step 1: Extracting Iron from Ore
The first step in making iron into steel is to extract iron from iron ore. This process is known as smelting. Iron ore, which is rich in iron oxides, is usually found in the form of hematite (Fe2O3) or magnetite (Fe3O4).
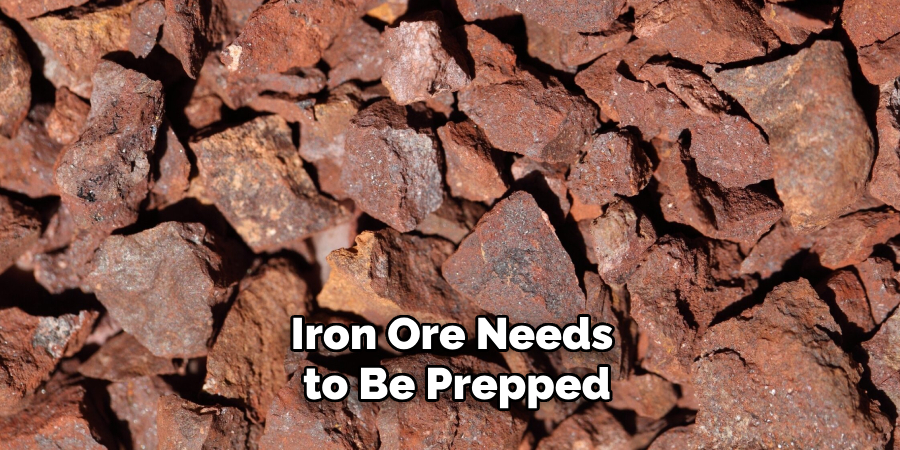
- Preparing the Iron Ore: Before smelting can begin, the iron ore needs to be prepped. This involves crushing the ore into small pieces to increase the surface area for the chemical reactions that will take place in the furnace.
- Loading the Furnace: Once the iron ore is prepared, it is loaded into a blast furnace along with coke and limestone. The blast furnace is a tall, cylindrical structure lined with heat-resistant materials. It is then heated to extremely high temperatures, reaching up to 2,000 degrees Celsius.
Step 2: Removing Impurities
As the iron ore melts in the furnace, impurities such as sulfur and phosphorous rise to the top while molten iron sinks to the bottom. These impurities are skimmed off or removed using a process called slagging.
- Adding Flux: The limestone added to the blast furnace acts as a fluxing agent, reacting with the impurities and forming a liquid slag that can easily be removed.
Step 3: Adding Alloying Elements
Once the impurities have been removed, the next step is to add alloying elements to the molten iron. These elements are carefully chosen based on the desired properties of the final steel product. The most common alloying element added is carbon, which enhances the strength and hardness of the steel.
- Introducing Carbon: Typically, carbon is introduced in amounts ranging from 0.2% to 2% of the total composition. This variation allows for the production of different grades of steel, from low-carbon steels that are more ductile to high-carbon steels that are harder and more wear-resistant.
- Other Alloying Elements: In addition to carbon, other metals such as chromium, nickel, and manganese can be added to impart specific characteristics to the steel. For example, chromium increases corrosion resistance, making the steel stainless, while nickel enhances toughness and impact resistance.
- Precisely Measuring Additions: The quantities of each alloying element must be meticulously measured and controlled to ensure the consistency and quality of the steel. This precise addition is often carried out using advanced equipment that allows for real-time monitoring and adjustment.
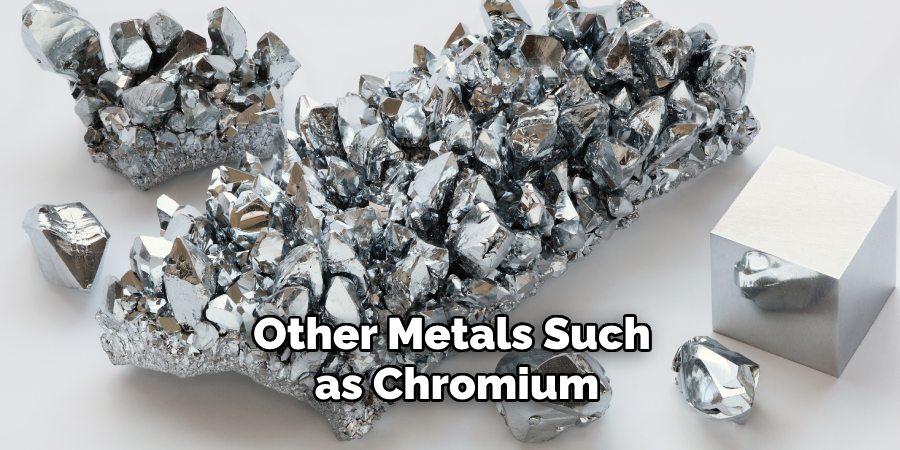
Step 4: Adjusting the Composition
After the alloying elements have been added, the composition of the molten steel must be adjusted to meet the required specifications. This is known as secondary refining or ladle metallurgy, and it involves several processes designed to fine-tune the steel’s properties.
- Desulfurization: This stage involves removing sulfur, which can cause steel to become brittle. Desulfurizing agents, such as calcium or magnesium, are added to the molten steel to bind with sulfur and remove it from the mixture.
- Deoxidation: Oxygen is another element that must be controlled, as too much oxygen can lead to the formation of oxides that weaken the steel. Deoxidizers like aluminum or silicon are added to neutralize the excess oxygen.
- Temperature Control: Maintaining the correct temperature is essential during this stage. If the molten steel becomes too cool, it can solidify prematurely, while excessive heat can cause unwanted reactions. Therefore, precise temperature control equipment is used to monitor and adjust the heat as needed.
Step 5: Pouring the Molten Steel
Once the desired composition has been achieved, the molten steel is ready to be poured. This crucial step involves transferring the molten steel from the furnace to molds or casting machines, where it will solidify into its final shape.
- Tapping the Furnace: The furnace is tapped or opened to allow the molten steel to flow out. This must be done carefully to avoid contamination or loss of material.
- Using Tundish: A tundish, a refractory-lined vessel, is often used to control the flow of molten steel from the furnace to the molds. It acts as an intermediary, ensuring a smooth and continuous transfer while catching any remaining impurities.
- Filling the Molds: The molten steel is then poured into molds of various shapes and sizes, depending on the intended use of the final product. These molds can be simple ingot molds or more complex shapes for specific applications.

Step 6: Cooling and Solidifying
After the molten steel is poured, it needs to be cooled and solidified. This process must be carefully controlled to ensure that the steel retains its desired properties and does not develop any defects.
- Initial Cooling: The filled molds are allowed to cool, causing the molten steel to begin solidifying. The rate of cooling can impact the steel’s microstructure, affecting characteristics such as grain size and overall strength.
- Controlled Cooling Methods: Techniques such as slow cooling in a controlled environment or quenching (rapid cooling) in water or oil are used depending on the type of steel being produced and its intended use.
- Heat Treatment: In some cases, additional heat treatments, such as annealing or tempering, are employed to relieve internal stresses, improve ductility, and achieve the required mechanical properties.
Step 7: Removing the Mold
Once the steel has fully solidified, it needs to be removed from the mold. This step requires careful handling to ensure that the steel retains its shape and integrity.
- Breaking the Mold: The molds, often made from materials like sand or ceramic, are broken or opened to extract the solid steel. This process is done with precision to avoid damaging the steel.
- Initial Inspection: As the steel is removed, it undergoes an initial inspection to check for any visible defects or irregularities. Any imperfections found at this stage can be addressed before proceeding to the next steps.
Step 8: Shaping and Forming
After being removed from the mold, the steel undergoes further shaping and forming processes to refine its final dimensions and surface finish.
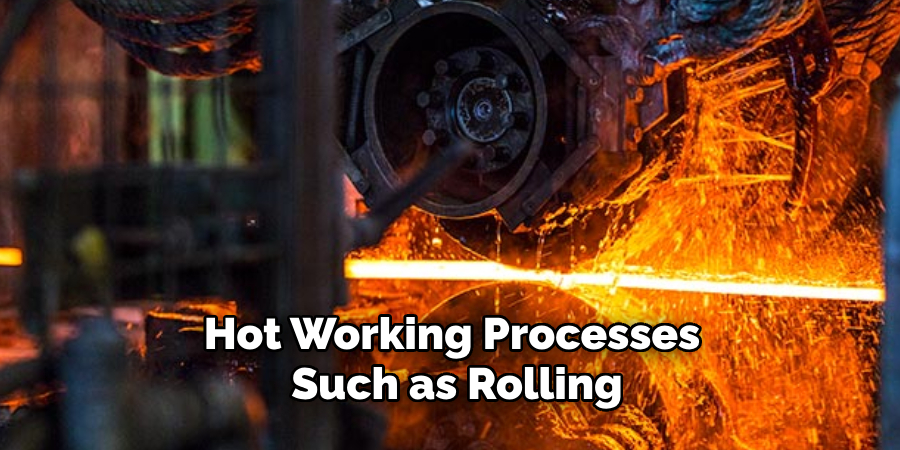
- Hot Working: At this stage, hot working processes such as rolling, forging, or extrusion are used to shape the steel while it is still at an elevated temperature. Hot working helps refine the grain structure and improve the steel’s mechanical properties.
- Cold Working: In some cases, cold working processes are employed after the initial hot working. Cold working such as cold rolling or drawing can further improve the surface finish and dimensional accuracy, as well as enhance the strength of the steel through work hardening.
Step 9: Final Treatments
The steel may undergo a series of final treatments to achieve the desired properties and prepare it for its intended application.
- Surface Treatment: Techniques such as pickling, galvanizing, or coating are applied to improve the steel’s surface quality, corrosion resistance, and aesthetic appearance.
- Heat Treatment: Additional heat treatments, such as hardening or tempering, are carried out to tailor the steel’s mechanical properties for specific applications.
- Finishing: The steel is subjected to finishing processes like machining, grinding, or polishing to achieve the desired dimensions, surface finish, and overall quality.
Step 10: Quality Control and Testing
The final step in the steel-making process involves rigorous quality control and testing to ensure that the steel meets the required standards and specifications.
- Chemical Analysis: Samples of the steel are analyzed to verify that the chemical composition is within the specified limits.
- Mechanical Testing: Tests such as tensile, hardness, and impact testing are performed to assess the steel’s mechanical properties.
- Non-Destructive Testing: Techniques such as ultrasonic, radiographic, or magnetic particle testing are used to detect any internal defects or irregularities without damaging the steel.
- Certification and Documentation: Once the steel passes all tests and inspections, it is certified and documented, ready to be shipped to customers for use in various applications.
By following these 10 steps, you can successfully transform iron into high-quality steel, ready for use in a wide range of industries and applications.
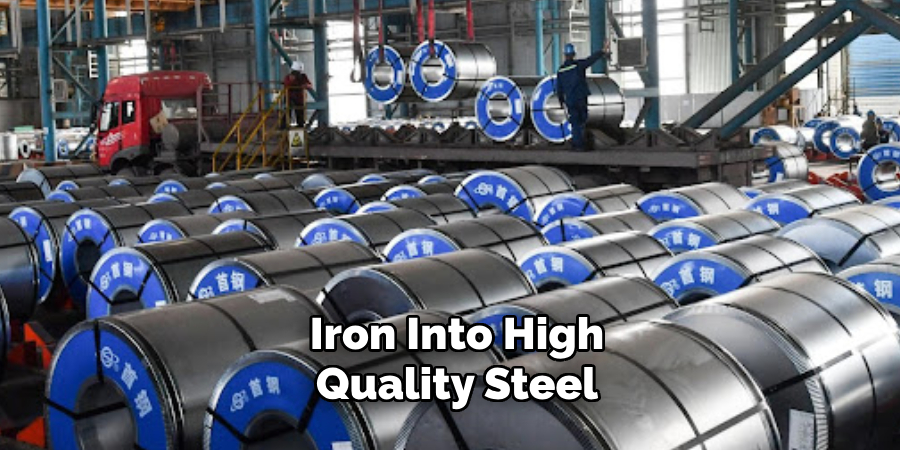
5 Additional Tips and Tricks
- Ensure Proper Temperature Control: Maintaining the ideal temperature is crucial during the steel-making process. The temperature must be high enough to remove impurities and allow for proper alloying but not so high as to damage the furnace lining or waste fuel.
- Monitor Carbon Content: The carbon content in steel is a critical factor in determining its strength and hardness. Use precise measurement tools to monitor and control the carbon level accurately throughout the process.
- Employ Secondary Metallurgy: Techniques such as vacuum degassing and ladle refining can further purify the molten steel. These processes help to remove dissolved gases and additional impurities, leading to higher-quality steel.
- Check for Inclusions: Inclusions, such as non-metallic particles, can weaken steel and decrease its quality. Regularly inspect the molten steel and use methods such as filtration or slag control to remove any inclusions.
- Use Alternative Energy Sources: Traditional steel-making processes consume a significant amount of energy, contributing to environmental issues. Consider using alternative energy sources, such as renewable energy or waste heat, to reduce the environmental impact and lower production costs. Additionally, investing in energy-efficient technologies can help conserve resources and improve overall efficiency.
By following these additional tips and tricks, steel manufacturers can produce high-quality steel efficiently while also reducing the environmental impact of their operations.
5 Things You Should Avoid
- Avoid Contaminated Raw Materials: Using raw materials that contain impurities can lead to defects in the final steel product. Always source high-quality iron ore and other inputs to ensure a purer end product.
- Neglecting Proper Maintenance: Skipping routine maintenance of equipment and furnaces can result in breakdowns and inefficiencies. Regular inspections and timely maintenance are essential to ensure smooth and effective operations.
- Overlooking Proper Alloying: Inaccurate alloying can result in steel with undesirable properties. Be meticulous in adding alloying elements to achieve the desired chemical composition and mechanical properties.
- Ignoring Environmental Regulations: Non-compliance with environmental regulations can lead to legal repercussions and damage to reputation. Adhere to all relevant environmental guidelines to ensure sustainable and responsible production practices.
- Underestimating Temperature Control: Incorrect temperature management during the steel-making process can result in poor quality steel or even cause accidents. Always monitor and control the temperature precisely to avoid any adverse outcomes.
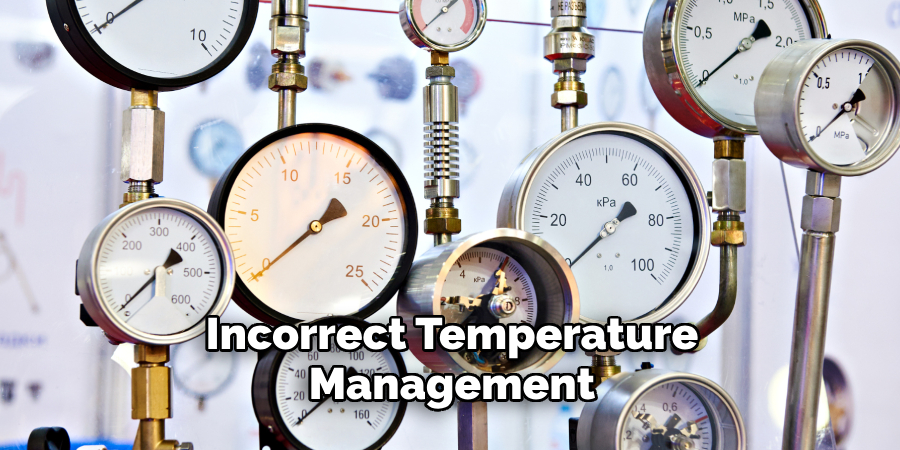
By avoiding these mistakes, steel manufacturers can improve the quality and efficiency of their operations while maintaining a positive image in the industry. Continuously reviewing and improving processes is essential to staying ahead in the competitive steel market.
Can You Turn Cast Iron Into Steel?
While both cast iron and steel are alloys of iron and carbon, they have distinct differences in their composition and properties.
Cast iron contains a higher percentage of carbon (2-4%) compared to steel (0.2-2%), making it more brittle and less malleable. Steel, on the other hand, has a lower carbon content and often includes additional alloying elements such as manganese, chromium, and nickel to enhance its properties.
Although it is not possible to directly turn cast iron into steel, various methods exist to convert it into a usable form.
One way is through decarburization, where the carbon in cast iron is reduced by heating it with oxygen or air. This results in a lower carbon content and a more malleable material, similar to steel.
Another method is to use electric arc furnaces, where scrap iron and steel are melted together with other alloying elements to create new steel. This process also allows for the control of various properties, such as carbon content, making it possible to produce different types of steel.
Conclusion
In conclusion, how to make iron into steel is a complex yet precise process that requires careful control of various factors.
The fundamental steps include the removal of impurities from iron ore, accurate monitoring of carbon content, and the addition of desired alloying elements. Techniques such as decarburization and the use of electric arc furnaces are essential in refining cast iron into different grades of steel.
Adhering to best practices, such as proper temperature control and avoiding common pitfalls, ensures the production of high-quality steel.
By leveraging advanced methods and adhering to environmental guidelines, steel manufacturers can produce durable and versatile steel products that meet industry standards.
Edmund Sumlin is a skilled author for Metal Fixes, bringing 6 years of expertise in crafting a wide range of metal fixtures. With a strong background in metalwork, Edmund’s knowledge spans various types of fixtures, from decorative pieces to functional hardware, blending precision with creativity. His passion for metalworking and design has made him a trusted resource in the industry.
Professional Focus:
- Expert in Metal Fixtures : Edmund aesthetic specializes in creating durable and innovative metal fixtures, offering both appeal and functionality. His work reflects a deep understanding of metalworking techniques and materials.
- Sustainability Advocate : He is dedicated to using sustainable practices, ensuring that every fixture is crafted with eco-friendly methods while maintaining high-quality standards.
In his writing for Metal Fixes, Edmund provides valuable insights into the latest trends, techniques, and practical advice for those passionate about metal fixtures, whether they are professionals or DIY enthusiasts. His focus on combining artistry with engineering helps others discover the true potential of metal in design.