Adhering metal to plastic can seem challenging due to the differing properties of these materials. However, with the right tools and techniques, creating a strong bond between metal and plastic is entirely achievable. This guide will walk you through how to adhere metal to plastic. Whether you’re undertaking a DIY project or working on a professional application, understanding the compatibility of materials and the types of adhesives available is crucial in achieving a durable and long-lasting bond.
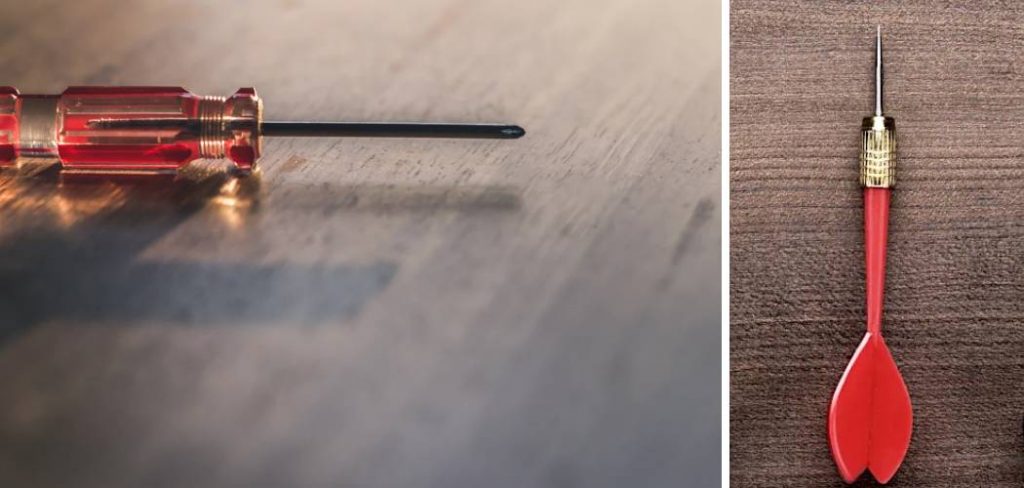
Why Metal Needs to Be Adhered to Plastic
There are numerous applications where adhering metal to plastic is essential, ranging from everyday consumer products to industrial uses. In the automotive industry, for example, metal components often need to be integrated with plastic parts to create a robust yet lightweight structure that improves fuel efficiency. In electronics, plastic casings might require metal inserts for structural support or electrical conductivity. The versatility and distinct properties of both materials allow for innovative design solutions where the durability of metal and the flexibility and aesthetic appeal of plastic are combined. This integration enhances the functionality, performance, and longevity of many products, making the process of bonding these materials highly valuable.
Tools and Materials Needed
To successfully adhere metal to plastic, you will need a few essential tools and materials. Here’s a list to get you started:
- Adhesive: An epoxy or a specialized adhesive for metal and plastic, such as cyanoacrylate or polyurethane-based glues.
- Sandpaper: Medium-grit sandpaper for roughening surfaces to enhance bonding.
- Cleaning Supplies: Isopropyl alcohol or a mild detergent for cleaning the surfaces before adhesion.
- Applicator: A small brush or applicator tip for precise application of the adhesive.
- Clamps or Weights: To hold the materials together firmly as the adhesive sets.
- Protective Gear: Gloves and safety goggles to protect your hands and eyes while working with adhesives and tools.
Choosing the Right Adhesive for the Job
Selecting the appropriate adhesive is critical to ensuring a successful bond between metal and plastic. There are several types of adhesives to consider, each with unique properties suited to different applications. Epoxy adhesives are among the most popular choices due to their high strength and durability, making them suitable for heavy-duty applications. Cyanoacrylate adhesives, also known as super glues, provide quick bonding and are ideal for projects requiring an immediate hold, though not as resilient under high stress as epoxies.
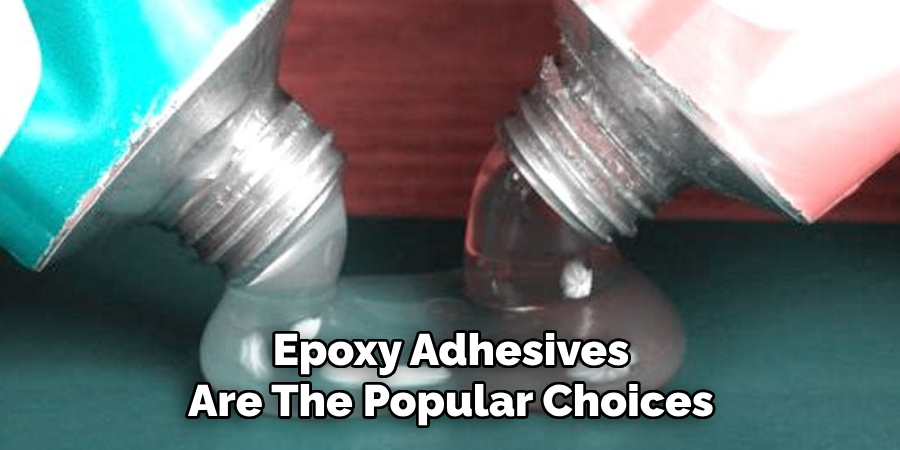
Polyurethane-based adhesives offer strong flexibility and can withstand environmental fluctuations, making them a good choice for outdoor applications. When choosing an adhesive, it’s important to consider factors such as the environmental conditions the bond will be exposed to, the types of forces the bond will need to endure, and the specific properties of the metal and plastic being adhered. Testing the adhesive on a small area before full application can also help ensure compatibility and optimal results.
10 Effective Methods for How to Adhere Metal to Plastic
Whether you’re a DIY enthusiast, manufacturer, or engineer, knowing how to effectively bond metal to plastic can greatly expand your project possibilities. From crafting intricate models to assembling robust industrial components, the ability to adhere these two materials can be a game-changer. In this listicle, we explore ten proven methods for achieving strong, reliable adhesion between metal and plastic.
1. Epoxy Adhesives
Epoxy adhesives are known for their strong bonding capabilities and versatility. Comprised of a resin and a hardener, epoxies create a durable bond that can withstand high levels of stress and environmental factors. This makes them ideal for use in both DIY projects and industrial applications. For best results, ensure the surfaces are clean and slightly roughened before application.
2. Super Glue (Cyanoacrylate)
Super glue offers a quick and convenient solution for smaller projects requiring instant adhesion. While it forms a strong bond on smooth surfaces, it’s important to note that super glue may not be suitable for high-impact applications. For optimal results, use a little pressure when applying the glue to form a tight bond between the materials.
3. Acrylic Adhesives
Acrylic adhesives provide excellent impact resistance and durability, making them suitable for outdoor applications. These adhesives cure quickly and can bond a variety of surfaces, including metals and plastics. They are often used in the automotive and construction industries for tasks requiring a robust, long-lasting hold.
4. Polyurethane Adhesives
Polyurethane adhesives are flexible and resistant to water, oils, and chemicals, making them perfect for dynamic environments. They offer moderate bonding strength and can accommodate slight movements between bonded surfaces. This feature is particularly useful in applications where thermal expansion might cause stress.
5. Hot Melt Glue
Hot melt glue is a great option for temporary bonds, crafting projects, or where flexibility is needed. Applied with a glue gun, hot melt glue cools and solidifies quickly. However, it may not hold up under high temperatures or significant stress, so it’s best reserved for low-impact applications.
6. Silicone Adhesives
Silicone adhesives are valued for their flexibility, temperature resistance, and ability to bond non-porous surfaces. These properties make them ideal for sealing gaps and joints in environments subject to moisture and temperature changes. When bonding metal to plastic, silicone adhesives often act as both a glue and a sealant.
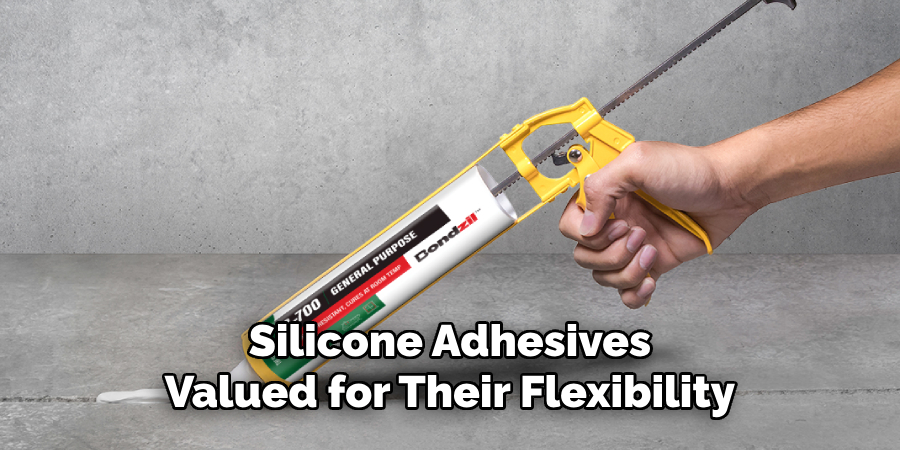
7. Double-Sided Tape
Double-sided tape provides an easy-to-use alternative for adhering metal to plastic without the mess of liquid adhesives. Industrial-grade tapes offer strong adhesion and can be used in applications where aesthetics are important. However, they may not be suitable for heavy-duty purposes.
8. Plastic Welding
For those with the right equipment, plastic welding offers a permanent and robust solution. This technique involves melting the surfaces together using heat or friction. While highly effective, plastic welding requires precision and skill to avoid damaging the materials.
9. Mechanical Fasteners
Mechanical fasteners such as bolts, screws, and rivets provide a reliable method for securing metal to plastic. While they don’t technically “adhere” the materials, they ensure a strong, removable bond. Mechanical fasteners are particularly useful when dealing with thicker materials or when a strong bond is required.
10. Surface Treatment Techniques
In some cases, enhancing the surface characteristics of the metal or plastic can improve adhesion. Treatments like plasma or corona treatment can increase surface energy, thereby enhancing adhesive performance. While often used in industrial settings, these methods can be applied to DIY projects with proper equipment.
Maintenance and Upkeep
Proper maintenance and upkeep of the adhesive bond between metal and plastic are crucial to ensure long-lasting performance and reliability. Regularly inspecting the bonded area for signs of wear, such as cracking or peeling, can help identify potential issues before they become significant problems.
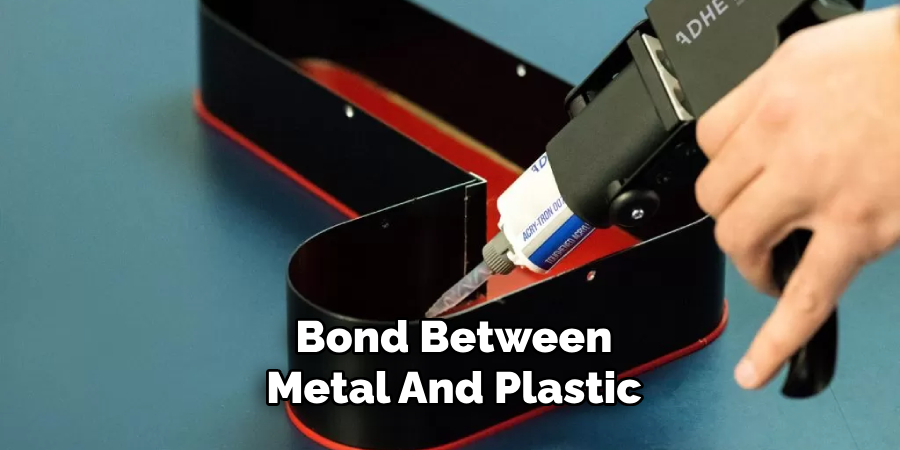
Environmental conditions like humidity and temperature fluctuations can impact the integrity of certain adhesives, so taking measures to protect the materials from extreme conditions can prolong the life of the bond. Cleaning the bonded surfaces with compatible cleaning agents can prevent dirt and debris accumulation, which can also affect adhesion over time.
Troubleshooting Common Issues
When working to adhere metal to plastic, several common issues may arise, potentially affecting the strength or durability of the bond. Identifying and troubleshooting these issues promptly can prevent small problems from escalating and ensure a successful outcome. Here are some frequent challenges and their solutions:
- Poor Adhesion: If the adhesive bond seems weak, check whether the surfaces were properly prepared before application. Cleaning the materials thoroughly and roughening them slightly can significantly improve adhesion. Ensure that the adhesive used is suitable for both materials and the conditions they will face.
- Bond Failure Under Stress: If the bond breaks when subjected to stress, it may be necessary to select a stronger adhesive or use mechanical fasteners in conjunction with adhesive solutions. Consider the environment and choose adhesives that can withstand the specific stresses anticipated, such as heat or movement.
- Incomplete Bonding: This can occur if the adhesive does not cure properly. Review the adhesive’s instructions to confirm that the cure time, temperature, and environmental conditions align with the recommended guidelines. If the issue persists, re-evaluate the compatibility of the adhesive with both materials.
- Environmental Degradation: Exposure to extreme weather conditions can deteriorate the bond. If warping, softening, or cracking is observed, opt for adhesives specifically designed to resist environmental changes. Ensuring proper sealing and protection around the bond can mitigate these effects.
- Material Incompatibility: Some plastics or metals may have surface characteristics that resist bonding. In these cases, treating the surfaces with primers or surface energy enhancers, like plasma treatments, can improve adhesion.
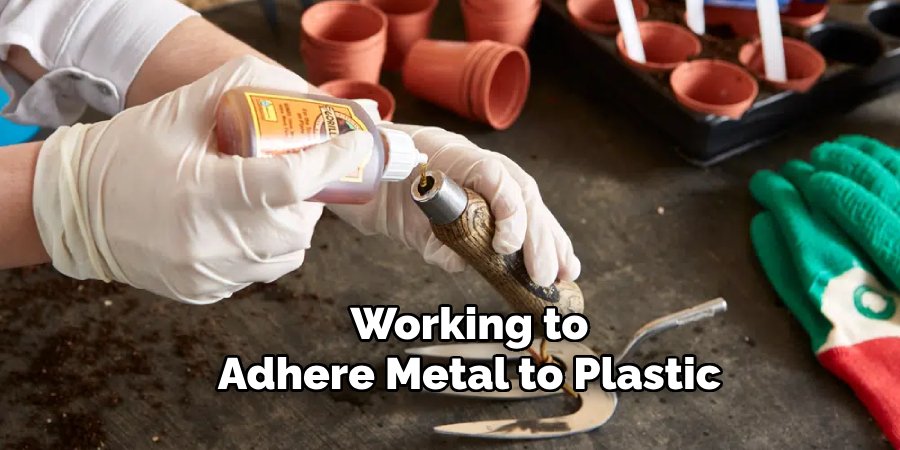
By addressing these issues through careful selection of adhesives, thorough surface preparation, and adhering to recommended curing practices, most bonding challenges can be effectively resolved
Conclusion
Successfully bonding metal to plastic involves careful consideration of the materials, the application environment, and the type of adhesive or bonding method used. By understanding the properties of each adhesive option—from glues and tapes to mechanical fasteners and plastic welding—it’s possible to select the most appropriate solution for your specific needs.
Ensuring proper surface preparation and adhering to best practices for curing and maintenance can significantly enhance the durability and performance of the bond. Thanks for reading our blog post on how to adhere metal to plastic! We hope you found it helpful and informative.
Edmund Sumlin is a skilled author for Metal Fixes, bringing 6 years of expertise in crafting a wide range of metal fixtures. With a strong background in metalwork, Edmund’s knowledge spans various types of fixtures, from decorative pieces to functional hardware, blending precision with creativity. His passion for metalworking and design has made him a trusted resource in the industry.
Professional Focus:
- Expert in Metal Fixtures : Edmund aesthetic specializes in creating durable and innovative metal fixtures, offering both appeal and functionality. His work reflects a deep understanding of metalworking techniques and materials.
- Sustainability Advocate : He is dedicated to using sustainable practices, ensuring that every fixture is crafted with eco-friendly methods while maintaining high-quality standards.
In his writing for Metal Fixes, Edmund provides valuable insights into the latest trends, techniques, and practical advice for those passionate about metal fixtures, whether they are professionals or DIY enthusiasts. His focus on combining artistry with engineering helps others discover the true potential of metal in design.