Angle iron is a versatile structural material widely used in construction, fabrication, and even decorative projects. Its L-shaped design provides excellent strength and support, making it a popular choice for building frames, brackets, or supports. There are many reasons one might need to learn how to bend angle iron, such as for custom projects requiring specific angles, structural adjustments to fit particular spaces, or creating aesthetic designs that add a unique touch to a piece.
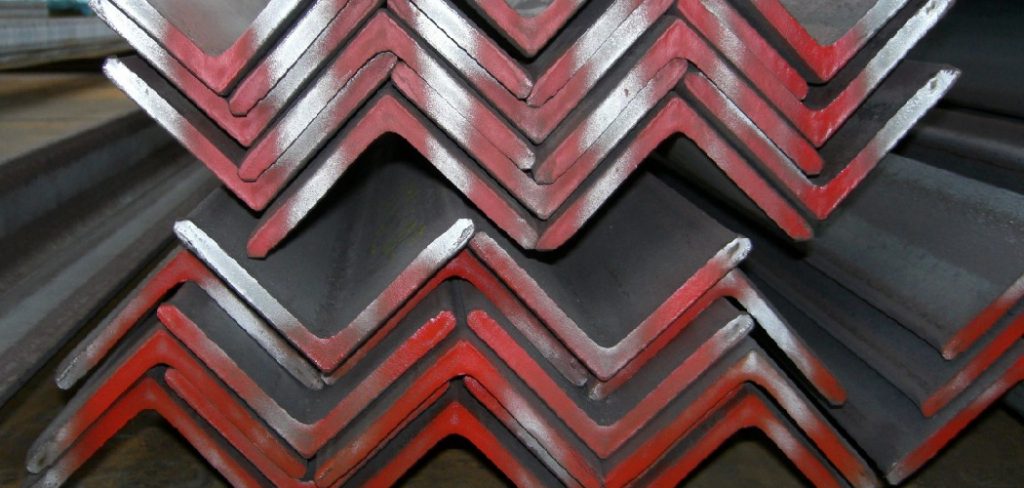
However, bending angle iron must be undertaken with care to avoid weakening or damaging the material, which could compromise its structural integrity. This article aims to guide readers through safe and effective methods for how to bend angle iron, ensuring that each project is executed with precision and confidence, whether employing traditional methods, using specialized tools, or exploring innovative techniques.
Understanding the Properties of Angle Iron
Structural Characteristics
Angle iron is characterized by its distinct L-shape, where two legs converge at a 90-degree angle, offering a robust and supportive edge. This configuration provides excellent load-bearing capabilities and is commonly used in frameworks and structural support systems. The versatility of angle iron is further enhanced by the variety of materials from which it is made. Mild steel angle iron is highly popular for its strength and affordability, while stainless steel offers increased durability and resistance to corrosion, making it suitable for outdoor and marine applications. Aluminum angle iron is another option, valued for its lightweight nature and ease of workability, especially in projects where weight is a consideration.
Challenges of Bending Angle Iron
Bending angle iron poses specific challenges, primarily due to the risk of cracking, distortion, or weakening of the material. The L-shaped design can make achieving a uniform bend more complex, and care must be taken to maintain structural integrity during the process. The thickness and composition of the angle iron significantly influence its bendability. Thicker materials are more difficult to bend and may require specialized equipment to achieve the desired angle without compromising the material’s strength. Meanwhile, the type of metal—whether mild steel, stainless steel, or aluminum—also impacts the methods and conditions under which bending should be performed to prevent material degradation.
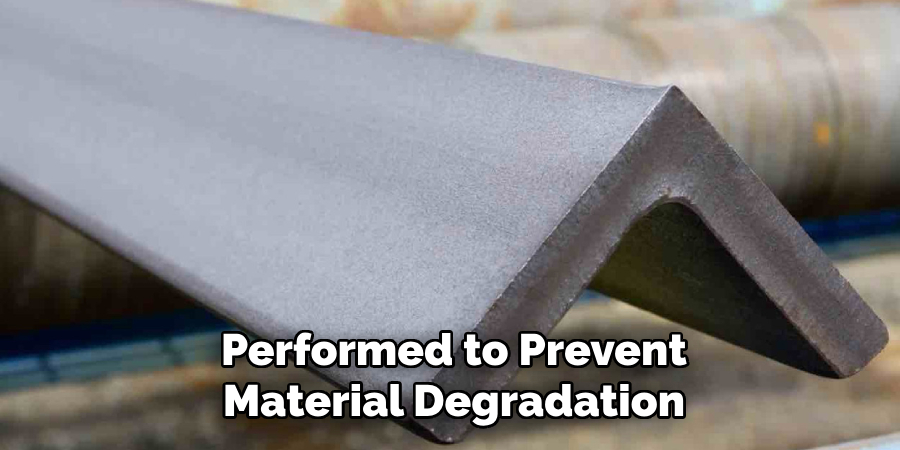
Tools and Equipment Needed to Bend Angle Iron
Essential Tools
Several essential tools are required to successfully bend angle iron to ensure precision and safety. Angle grinders are useful for smoothing out edges and preparing the material for bending. Clamps are crucial for stabilizing the angle iron and preventing movement. A heat source, such as a torch or forge, is necessary when applying heat for manual bending. Measuring tools help achieve accurate bends by allowing precise angle adjustments. Additionally, specialized bending equipment like hydraulic presses, angle benders, and manual bending jigs provide added control and efficiency, making them valuable assets in more complex bending tasks.
Safety Gear and Workspace Setup
Safety should be a top priority when bending angle iron. Protective gloves and safety glasses are necessary to safeguard against sharp edges, sparks, and hot surfaces. A clear, well-lit workspace enhances visibility and reduces the risk of accidents. Stabilizing the angle iron ensures precise and safe bending, requiring firm positioning with clamps or vices. An organized workspace also facilitates easy access to all needed tools, allowing for smoother workflow and minimizing the potential for mishaps. By maintaining a clean, prepared environment, operators can focus on the bending process and achieve the best possible results.
Preparing Angle Iron for Bending
Measuring and Marking
Achieving an accurate bend in angle iron begins with precise measurement and marking. Using a tape measure, carefully measure the length from the start of the angle iron to the desired bend point. Mark this location clearly with chalk or a marker, ensuring visibility during bending. It’s essential to account for the bend radius when marking, as this affects the final dimensions of the piece. Furthermore, consider the material’s stretch on the outer surface during bending, potentially altering the overall length. Accurately marking your bend point while accounting for these factors is crucial for maintaining precision in your project.
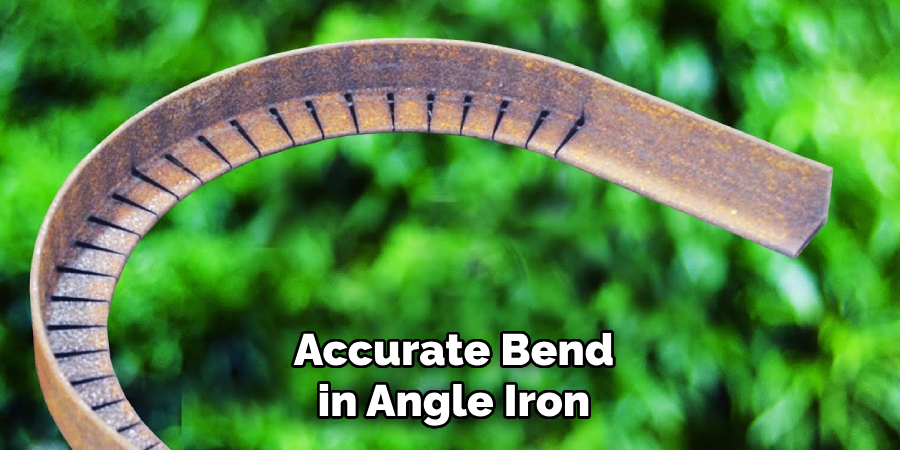
Pre-Bend Preparation
Before proceeding to bend, preparing the angle iron is critical to achieving a smooth and precise bend. One effective technique for softening the metal is applying heat to the intended bend area using a torch, which makes the iron more malleable and reduces the risk of cracking. Additionally, ensure the angle iron is thoroughly cleaned and free of rust or debris, as these imperfections can compromise bending accuracy and weaken the structure. Cleaning the surface also allows for a more uniform application of heat and pressure, facilitating a smoother bending process and improving the reliability and strength of the final product.
How to Bend Angle Iron: Methods for Bending Angle Iron
Using a Hydraulic Press
Hydraulic presses offer a precise and controlled method for bending angle iron, particularly when handling thicker materials that require consistent pressure. Here’s a step-by-step guide to achieving accurate bends:
- Secure the angle iron: Place the angle iron in the hydraulic press, ensuring the bend point is properly aligned and centered with the press’s ram. Secure it firmly to prevent any movement during the pressing process.
- Apply steady pressure: Slowly engage the press to apply consistent pressure on the bend point. Guide the press carefully to achieve the desired angle without sudden movements that could cause distortion.
- Check the angle regularly: Continuously monitor the bending progress to prevent over-bending. Release pressure intermittently to check the angle, making additional adjustments to reach the precise measurement.
The hydraulic press is advantageous because it can provide uniform pressure, which is crucial for maintaining angle accuracy. It is especially useful when working with thicker materials that manual methods may struggle to bend effectively.
Manual Bending with Heat
Manual bending with heat can be straightforward for those without access to a hydraulic press. Here’s how to do it:
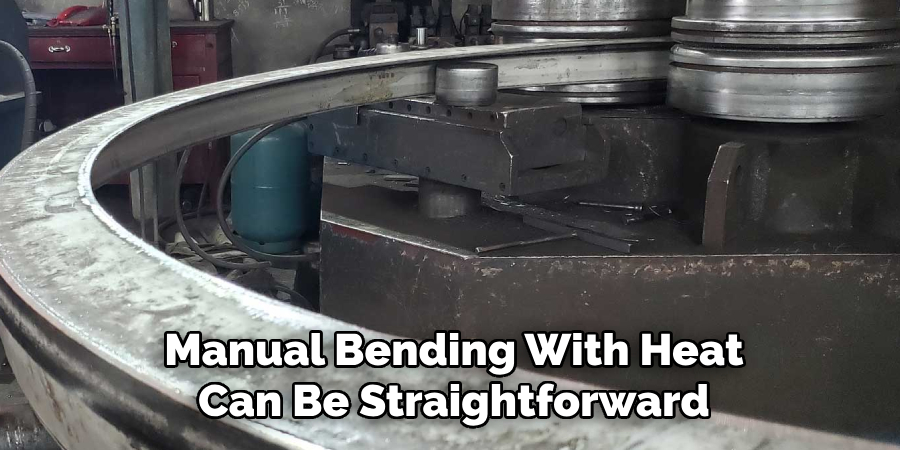
- Heat the bend area: Use a torch or forge to apply an even distribution of heat along the intended bend area until the metal reaches a red-hot state. Consistent heating is key to ensuring pliability without damaging the iron.
- Secure the angle iron: Place the heated angle iron in a vise or bending jig, ensuring it is securely held to facilitate effective bending. Proper securing prevents slippage that might lead to inaccuracies in the bend.
- Use a hammer or bending tool: With the metal heated, employ a hammer or specialized bending tool to gradually bend the angle iron to the desired angle. Apply uniform force to ensure an even bend.
After bending, allow the metal to cool naturally, regularly checking the angle to ensure it aligns with project specifications. Cooling advice includes placing the iron in a controlled environment to avoid rapid temperature changes that might affect the material’s integrity.
How to Bend Angle Iron: Bending Without Heat
Cold Bending Techniques
Cold bending is viable for shaping thinner or more flexible angle iron without heat. This technique relies primarily on brute force or mechanical assistance. For simple bends, using a pair of heavy-duty pliers or a manual bending jig can offer sufficient leverage to achieve the desired angle. Alternatively, a rolling device can create smooth, consistent bends as it gradually shapes the material without sharp transitions. These methods are particularly well-suited for projects requiring quick adjustments or when working with materials that respond readily to pressure.
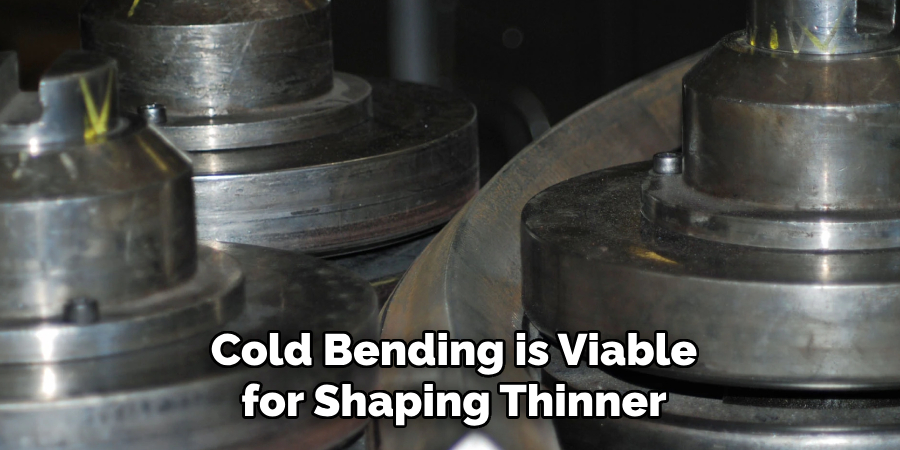
Limitations of Cold Bending
While cold bending techniques provide a convenient method for certain applications, they have inherent limitations. One major risk is the potential for cracking or distortion when bending thicker or less malleable materials. The absence of heat means the metal’s structural integrity is more likely to be compromised under pressure. To minimize damage, applying slow, steady force throughout the bending process is crucial. By doing so, you can mitigate the chances of creating unintended stresses or fractures within the iron, thus maintaining the reliability and accuracy of the final product.
Troubleshooting and Adjustments
Addressing Over-Bending
Correcting over-bends involves carefully reversing the bending process to achieve the desired angle. If an over-bend occurs, gradually apply force in the opposite direction using a hydraulic press or manual tools, ensuring even pressure distribution to avoid damaging the material. Utilizing heat during this adjustment can also help. Apply controlled heat to the over-bend area to soften the metal slightly, allowing for more precise corrections without jeopardizing the angle iron’s integrity.
Preventing Common Issues
To avoid warping, uneven bends, or cracks, monitoring alignment and applying force gradually during the bending process is crucial. Always ensure the angle iron is securely clamped and aligned correctly before application. Incremental pressure helps maintain control, reducing the risk of unwanted distortions. Additionally, regularly inspect the workpiece and adjust techniques to maintain consistency and accuracy throughout your project.
Applications of Bent Angle Iron
Real-World Uses
Bent angle iron is versatile in various industries, from construction to creative endeavors. Construction is common in frames and brackets, providing structural support and stability. In-home improvement projects, angle iron is frequently used to fabricate sleek furniture designs or sturdy railings. Meanwhile, artists and creators leverage its structural properties for innovative art projects, where precision and stability are key to executing intricate designs.
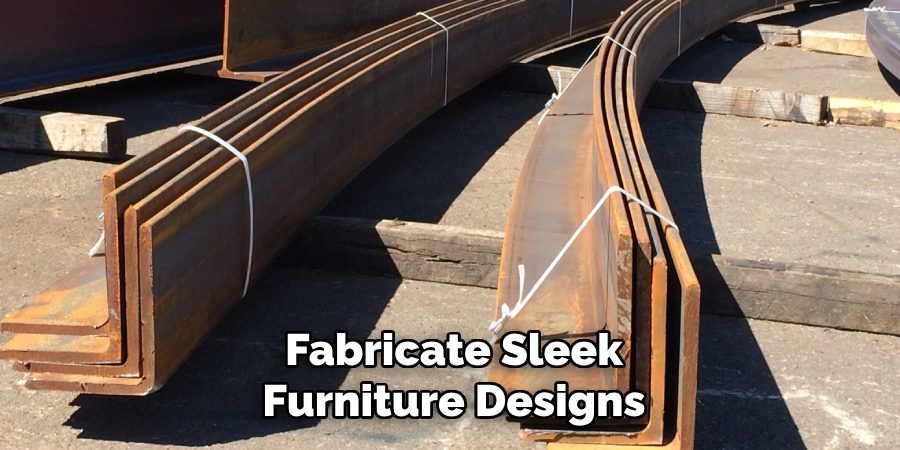
Importance of Precision
Precision in bending angle iron is essential as it directly influences the strength and aesthetic quality of the completed work. Accurate bends ensure that the structural integrity of the framing or bracket remains intact, preventing weak points that can lead to failures. Similarly, precise bends are crucial in enhancing the visual appeal of furniture and art pieces, where even minor inaccuracies can detract from the overall design and finish of the project.
Conclusion
Mastering three key methods is essential to understanding how to bend angle iron: using a hydraulic press for uniform pressure, manual bending with heat for flexibility in shaping, and cold bending for simpler tasks. Preparation is crucial, as it involves selecting the right tools and adhering to safety measures to prevent injuries and ensure accuracy. Practicing on scrap pieces is highly recommended to refine techniques before tackling final projects. Such practice builds confidence and reduces errors, allowing for precise, reliable results in your bending endeavors.
Edmund Sumlin is a skilled author for Metal Fixes, bringing 6 years of expertise in crafting a wide range of metal fixtures. With a strong background in metalwork, Edmund’s knowledge spans various types of fixtures, from decorative pieces to functional hardware, blending precision with creativity. His passion for metalworking and design has made him a trusted resource in the industry.
Professional Focus:
- Expert in Metal Fixtures : Edmund aesthetic specializes in creating durable and innovative metal fixtures, offering both appeal and functionality. His work reflects a deep understanding of metalworking techniques and materials.
- Sustainability Advocate : He is dedicated to using sustainable practices, ensuring that every fixture is crafted with eco-friendly methods while maintaining high-quality standards.
In his writing for Metal Fixes, Edmund provides valuable insights into the latest trends, techniques, and practical advice for those passionate about metal fixtures, whether they are professionals or DIY enthusiasts. His focus on combining artistry with engineering helps others discover the true potential of metal in design.