Anodizing aluminum is a popular electrochemical process used to enhance the metal’s durability and aesthetic appeal. Black anodizing, in particular, offers a sleek finish while providing excellent resistance to corrosion and wear. This process how to black anodize aluminum involves several key steps, including surface preparation, anodizing in an acidic bath, and dyeing to achieve the desired color.
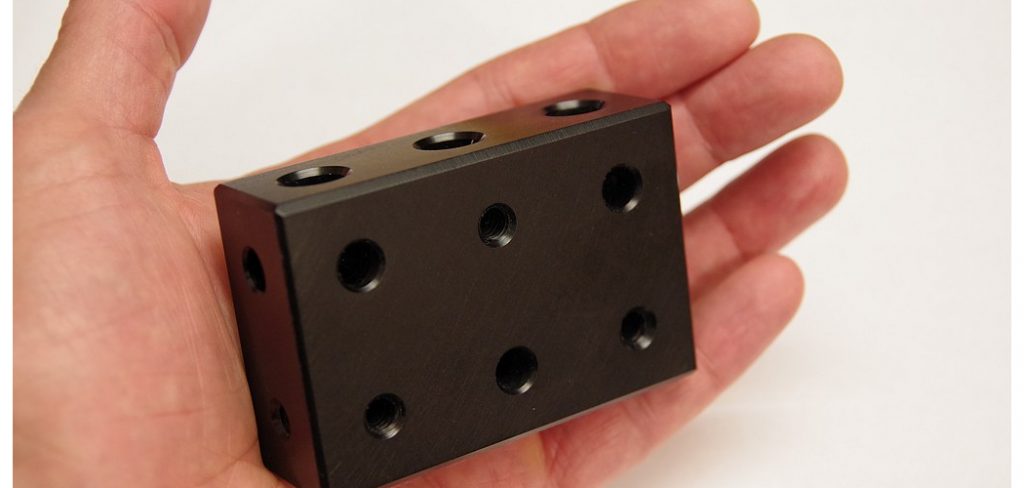
The result is a durable and attractive black coating that is widely used in various industries, from aerospace to consumer electronics. Understanding the fundamentals of black anodizing can empower enthusiasts and professionals alike to bring their aluminum projects to new heights of style and endurance.
Why Black Anodize?
Black anodizing offers several advantages that make it a preferred choice in numerous applications. One of the primary reasons is its ability to significantly enhance the corrosion resistance of aluminum, making it ideal for products exposed to harsh environmental conditions. In addition to this protective quality, the black anodized finish is sought after for its aesthetic appeal. The sleek, dark surface is not only visually striking but also provides a professional look, making it a favorite in the consumer electronics and automotive industries.
Furthermore, the anodized layer is integral to the metal, which means it won’t chip or peel like paint, ensuring long-lasting performance. This combination of functional and aesthetic properties makes black anodizing a valued process in various industrial and commercial sectors.
Things to Consider Before Black Anodizing Aluminum
Type of Alloy:
Different types of aluminum alloys can affect the outcome of the process. It’s essential to use the right grade for optimal results. The 5000 and 6000 series, which are commonly used in structural applications, are recommended for black anodizing due to their high silicon content. This ensures a consistent and uniform finish.
Surface Preparation:
Surface preparation is crucial in achieving a successful black anodized finish. Any impurities or surface defects can affect the adhesion of the anodized layer and result in an uneven appearance. Thorough cleaning and proper degreasing are necessary before proceeding with the anodizing process.
Dyeing Options:
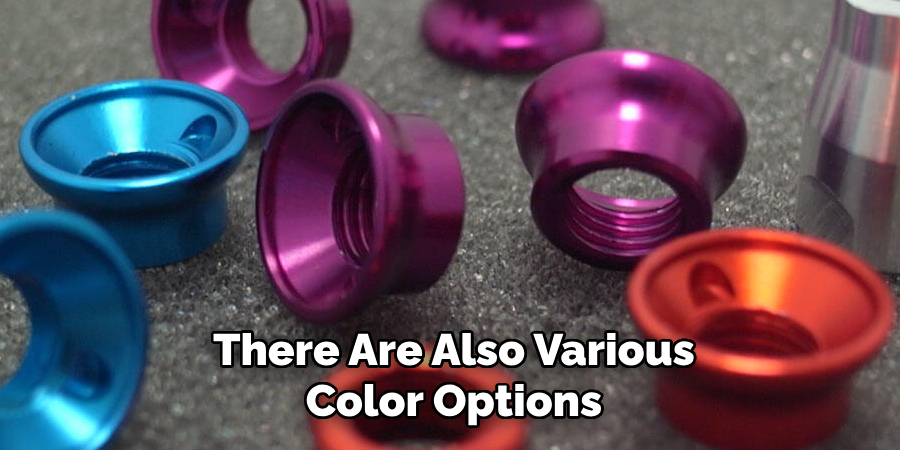
While basic black dye is widely available, there are also various color options that can be achieved through dyeing after the anodizing process. Some dyes even offer UV-resistant properties, making them suitable for outdoor applications. It’s essential to research and choose the appropriate dye for your project.
8 Step-by-step Guidelines on How to Black Anodize Aluminum
Step 1: Surface Preparation
The first step in the black anodizing process is surface preparation, which is critical for achieving a high-quality finish. Begin by thoroughly cleaning the aluminum surface to remove any dirt, grease, or contaminants. This can be done using a mild alkaline detergent and water, followed by rinsing and drying the material.
Next, inspect the surface for imperfections such as scratches or pits. These should be addressed through mechanical polishing or etching to ensure the surface is smooth and uniform. Proper surface preparation not only enhances the adhesion and appearance of the anodized layer but also contributes to the overall durability and performance of the final product.
Step 2: Etching
After the surface preparation, the next step in the black anodizing process is etching the aluminum. This step involves immersing the aluminum parts in an acid solution, typically made of sodium hydroxide, to remove a thin layer of the metal surface. The etching process helps to clean the aluminum of any residual oxides and create a uniform texture that is ideal for anodizing. It also enhances the adhesion of the anodized layer by creating a surface profile that promotes better bonding.
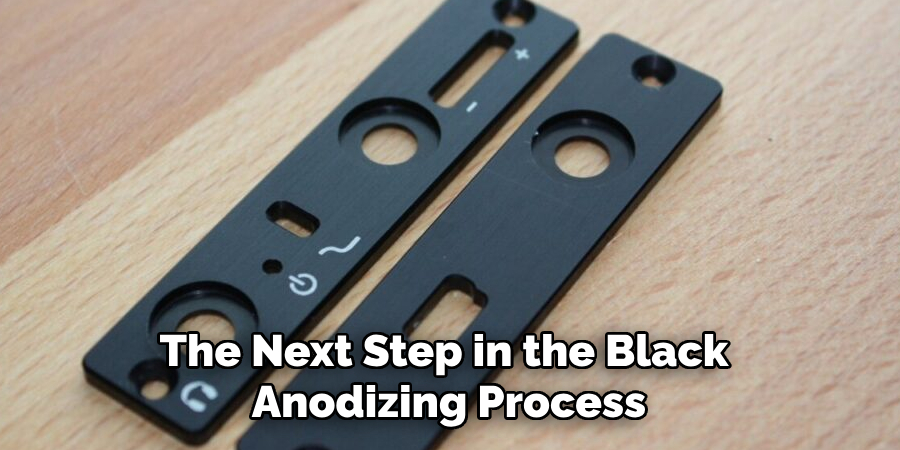
It is crucial to monitor the etching duration carefully—a precise balance ensures the removal of surface irregularities without compromising the structural integrity of the aluminum. Following the etching, thoroughly rinse the aluminum to neutralize the acid and remove any residues that could impact subsequent anodizing steps. This step sets the foundation for a smooth and durable anodized finish.
Step 3: Anodizing
After etching and rinsing, the next step is anodizing the aluminum in a sulfuric acid bath. The anodizing process involves passing an electrical current through the material while it’s immersed in the acid solution. This forms a layer of aluminum oxide on the surface that will eventually become the anodized coating.
The voltage and duration of this process depend on various factors such as alloy type, desired thickness, and intended application. It’s essential to precisely control these parameters to achieve consistent results and avoid defects such as burning or pitting.
Step 4: Sealing
Once the desired thickness of the anodic layer is achieved, it’s vital to seal the pores of the oxide layer to prevent water or other corrosive substances from seeping in. This process is typically done by immersing the aluminum parts in a hot water bath, which causes the anodized layer to swell and seal. Alternatively, a chemical sealing agent can also be used for more specialized applications.
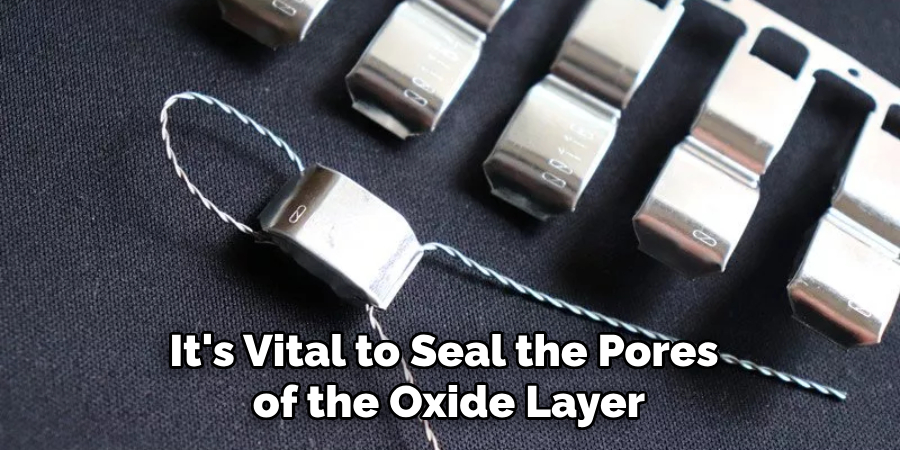
You can also choose to dye the anodized layer at this stage, which involves immersing the aluminum in a heated bath of colored dye. The porous anodic layer absorbs the dye, resulting in a vibrant and long-lasting color.
Step 5: Rinse and Dry
After sealing and dyeing (if desired), thoroughly rinse the aluminum parts to remove any excess dye or sealing agent. This will prevent streaks or discoloration from forming on the final product.
Next, dry the parts completely, making sure there is no moisture left on the surface. Any remaining water can cause defects or discoloration in the anodized finish.
Step 6: Quality Check
Before proceeding to the final step, it’s crucial to conduct a thorough quality check. This includes inspecting the surface for any defects, measuring the anodic layer thickness, and checking for color consistency (if dyed). Any issues should be addressed before moving on to the next step.
The quality check also ensures that the anodized layer has formed correctly and adhered to the surface, providing optimal durability and performance.
Step 7: Optional Post-treatment
Depending on the intended application, there are various post-treatment processes that can be done after black anodizing aluminum. These include impregnation with a sealant or wax for added corrosion resistance, painting or printing for customization, and mechanical finishing for additional texture.
But, for most applications, the anodized layer itself provides sufficient protection and aesthetic appeal.
Step 8: Final Inspection
The final step in the black anodizing process is a final inspection to ensure that all steps have been completed correctly. This includes checking for any defects or inconsistencies and verifying that the desired specifications have been met. Once everything is confirmed to be satisfactory, your black anodized aluminum parts are ready for use!
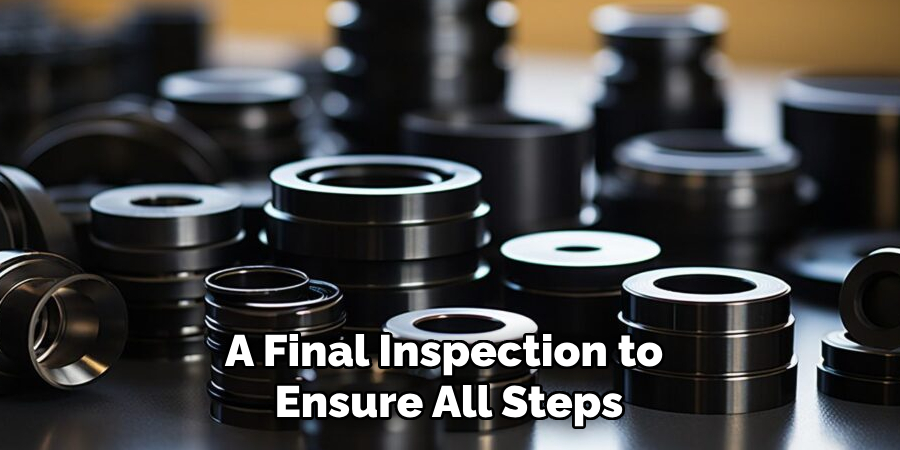
Following these step-by-step guidelines on how to black anodize aluminum will help you achieve a high-quality and long-lasting black anodized finish on aluminum. Remember to always follow safety precautions when handling chemicals, and consult with professionals if you are unsure about any aspect of the process. Happy anodizing!
Frequently Asked Questions
Q: What is the Purpose of Black Anodizing Aluminum?
A: Black anodizing aluminum provides a durable and attractive finish that can resist corrosion, wear, and fading. It also offers customization options through dyeing or post-treatment processes. Additionally, the anodized layer can enhance the adhesion of paint or other coatings for added protection or decoration.
Q: Can Any Aluminum Alloy Be Black Anodized?
A: Yes, most aluminum alloys can be anodized, but certain alloys may require special processes or precautions. For example, high silicon content in some castings may result in a dark gray finish instead of a true black. Consult with professionals to determine the best approach for your specific alloy.
Q: Is Black Anodized Aluminum Environmentally Friendly?
A: Yes, the anodizing process itself is environmentally friendly as it does not involve any toxic substances. The anodic layer also provides a protective barrier that can extend the life of aluminum products, reducing waste and the need for replacements. Additionally, the dye used in black anodizing is typically eco-friendly and non-toxic.
Q: How do I Care for Black Anodized Aluminum?
A: To maintain the appearance and durability of black anodized aluminum, it’s essential to avoid harsh chemicals or abrasive cleaners. Instead, use mild soap and water or specialized cleaners designed for anodized surfaces. Regularly inspect the surface for any damage or wear and promptly address anodized layer defects to prevent corrosion.
Conclusion
Black anodizing aluminum provides an exceptional blend of aesthetic appeal and robust performance, making it an ideal finish for a wide range of applications. By following the detailed steps on how to black anodize aluminum in the anodizing process, one can ensure high-quality results that enhance the durability and visual attractiveness of aluminum products. The process not only improves resistance to corrosion and wear but also offers opportunities for customization through coloring and post-treatment techniques.
As a sustainable and effective method, black anodizing contributes to the longevity of aluminum products while minimizing environmental impact. Whether for industrial use or decorative purposes, black anodized aluminum stands out as a reliable and versatile material choice.
Edmund Sumlin is a skilled author for Metal Fixes, bringing 6 years of expertise in crafting a wide range of metal fixtures. With a strong background in metalwork, Edmund’s knowledge spans various types of fixtures, from decorative pieces to functional hardware, blending precision with creativity. His passion for metalworking and design has made him a trusted resource in the industry.
Professional Focus:
- Expert in Metal Fixtures : Edmund aesthetic specializes in creating durable and innovative metal fixtures, offering both appeal and functionality. His work reflects a deep understanding of metalworking techniques and materials.
- Sustainability Advocate : He is dedicated to using sustainable practices, ensuring that every fixture is crafted with eco-friendly methods while maintaining high-quality standards.
In his writing for Metal Fixes, Edmund provides valuable insights into the latest trends, techniques, and practical advice for those passionate about metal fixtures, whether they are professionals or DIY enthusiasts. His focus on combining artistry with engineering helps others discover the true potential of metal in design.