Are you a fan of DIY projects that involve metal? Are you wondering how to braze cast iron for your latest project? Brazing is an invaluable skill when it comes to welding and repairing metal. It can be used on different types of metals, including copper, brass, nickel alloys, cast iron and more. It’s essential to become familiar with the process if you want to add extra strength or repair to metals.
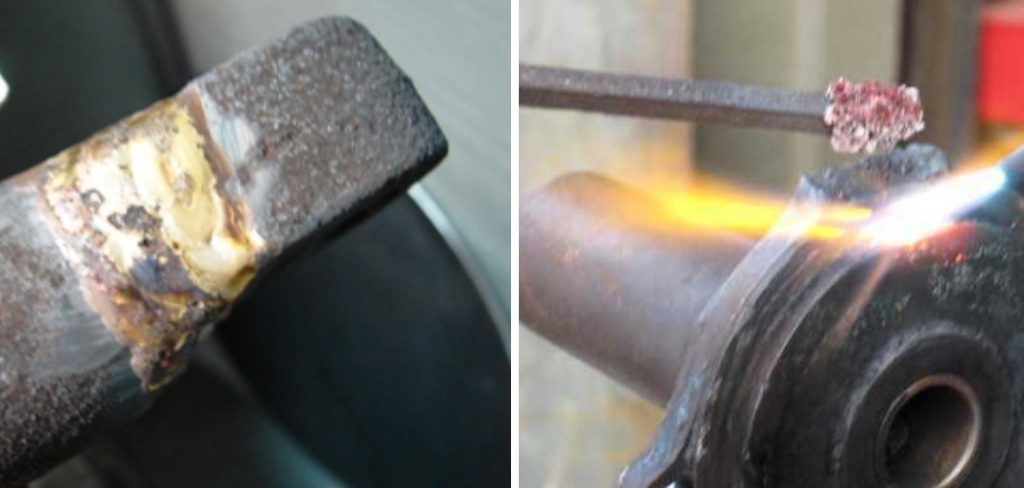
Cast iron is a popular choice of metal due to its strength, durability, and resistance to corrosion. However, it can be a tricky metal to work with due to its high carbon content. Brazing cast iron requires specific techniques and materials to achieve a strong bond between the pieces being joined.
Read on as we discuss the basics of brazing cast iron and provide you with essential tips.
What Will You Need?
Before you get started, here are some of the tools and materials you’ll need to braze cast iron:
- A propane or oxy-acetylene torch
- Flux (a chemical cleaning agent to remove impurities)
- Brazing rods (alloys that will melt at lower temperatures than the base metal)
- Protective gear (gloves, goggles, and a welding helmet)
- A wire brush (for cleaning the metal surfaces before brazing)
- Clamps or other tools to hold the pieces in place during the process
Once you have gathered your materials, let’s look at the steps involved in brazing cast iron.
10 Easy Steps on How to Braze Cast Iron
Step 1: Clean and Prepare the Surface
The first step is crucial for achieving a solid bond between the two cast iron pieces. Use a wire brush to clean the surface of any rust, dirt, or debris. Ensure that the surfaces are completely free of grease, oil, and other contaminants.
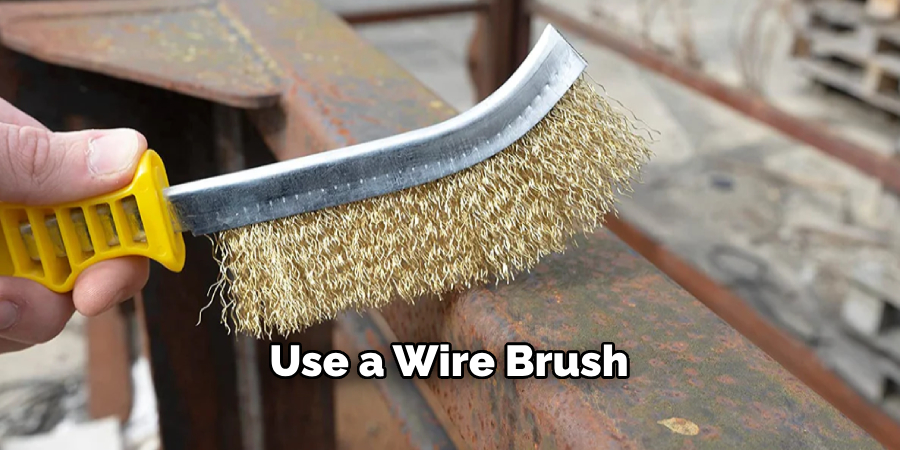
Step 2: Apply the Flux
After properly cleaning the surfaces, it’s time to apply the flux. Apply a generous amount on both surfaces of the cast iron pieces you want to join. The flux works as a barrier to oxygen, preventing the formation of oxides that could weaken the bond. It also helps the brazing alloy to flow smoothly over the pieces, ensuring a solid and secure joint.
Step 3: Assemble your Pieces
The next step is the arrangement of your pieces. Position the cast iron pieces as you want them to be joined using your clamps or other tools. Make sure they are steady and secure, as this will ensure a clean and precise brazing process. Remember, the brazing joint will only be as good as the setup, so take your time to get this right.
Step 4: Heat the Assembly
Now it’s time to start the heating process. Heat the joint area of the cast iron pieces using your propane or oxy-acetylene torch. This needs to be done slowly and evenly to prevent cracking due to thermal shock.
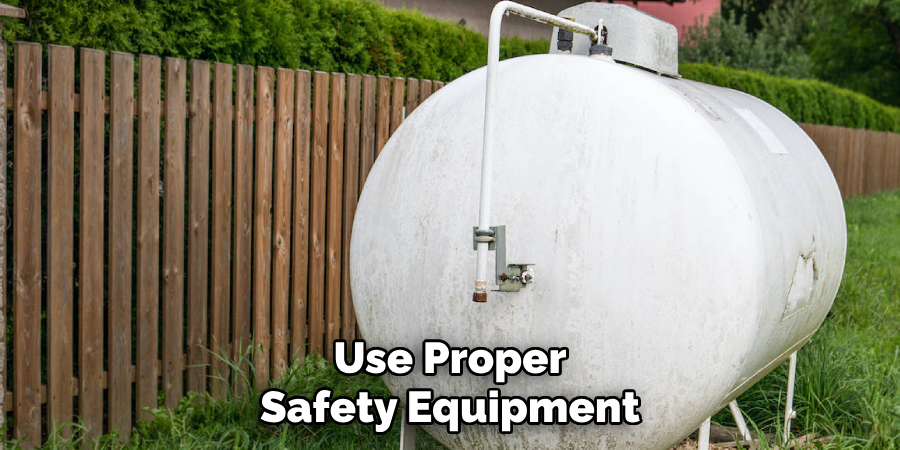
The aim here is to get the metal hot enough so that the brazing rod can melt and flow into the joint, but not so hot that the cast iron itself starts to melt. Look for the metal to take on a dull red glow – once you see this, you’re ready for the next step.
Step 5: Apply the Brazing Rod
With the assembly heated to the necessary temperature, touch the end of your brazing rod to the joint. The heat of the metal will melt the rod, and capillary action will draw the molten alloy into the joint.
It’s important to avoid applying the torch directly to the brazing rod; this could cause it to drip onto the surface, leading to a weaker joint. Instead, focus on heating the base metal and let its heat melt the brazing rod.
Step 6: Let it Cool
After applying the brazing rod to the joint, the next step is to let the assembly cool down naturally. It’s important to refrain from hastening the process by dunking the assembly into water or applying air. Rapid cooling may cause the metal to contract too quickly, resulting in a weak joint or possible cracks in the cast iron. Allow it to cool slowly and naturally for the strongest possible bond.
Step 7: Check the Joint
Once your assembly has cooled down, check the joint to ensure the brazing process is successful. Inspect the brazed joint and surrounding areas for any signs of fractures or gaps.
The brazing material should have filled the gap between the cast iron pieces entirely and smoothly. If you find any faults or missed spots, you may need to repeat the process to ensure a secure and durable bond.
Step 8: Clean the Brazed Joint
After confirming a successful brazing, the next step involves cleaning the joint. Use a wire brush or sandpaper to remove flux residues and any discoloration caused by the heating process.
Cleaning the joint not only improves its appearance but it also allows for a more thorough inspection of the brazing. If holes or cracks appear that were not previously visible, you may need to re-braze the joint.
Step 9: Apply a Protective Finish
Once you’re satisfied with the strength and integrity of your brazed joint, it’s time to apply a protective finish. This step, while optional, can significantly enhance the lifespan and appearance of your brazed cast iron.
Depending on your preference, you can opt for paint, a clear coat, or a corrosion-resistant finish. Make sure to follow the instructions provided by the finish manufacturer to ensure optimal results.
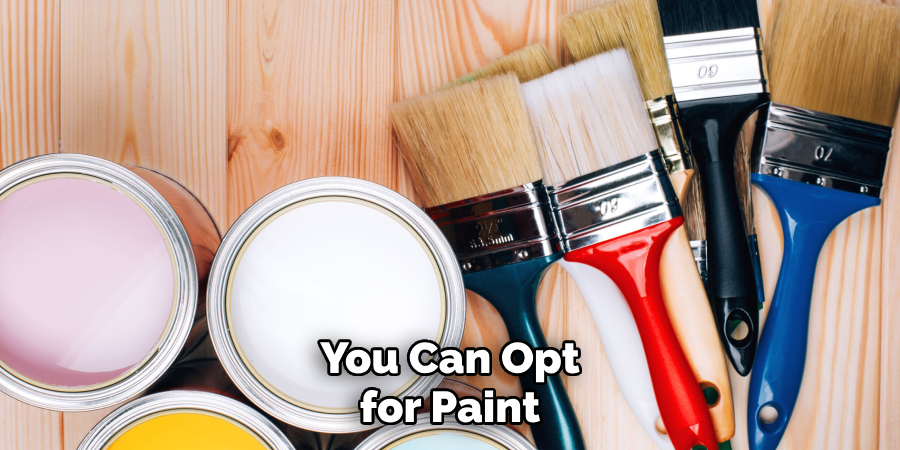
Step 10: Maintenance and Care
Lastly, remember that good maintenance and care are crucial for ensuring the longevity of your brazed cast iron pieces. Regularly check the joint for any signs of wear or corrosion.
If the piece is exposed to harsh weather conditions or heavy use, it might need a new protective finish application or occasional re-brazing. Good maintenance habits will keep your brazed cast iron strong and durable for years.
By following these simple steps, you can confidently learn how to braze cast iron and create strong bonds for various projects.
5 Additional Tips and Tricks
- Safety First: Always wear protective gear when brazing cast iron. This includes wearing heat-resistant gloves, safety goggles, and a welding helmet to protect you from sparks, heat, and intense light.
- Practice Makes Perfect: As with any skill, practice is critical to mastering brazing. Start with some scrap pieces of cast iron to get comfortable with the process before moving on to your project.
- Proper Ventilation: Brazing can generate harmful fumes if inhaled. Ensure you work in a well-ventilated area or use a fume extraction system to remove the fumes from the air.
- Cleanliness is Crucial: The cleaner your cast iron pieces are, the better the brazing rod will adhere. Take your time in the cleaning process to ensure the best possible bond.
- Patience is a Virtue: Don’t rush the cooling process. Let the assembly cool naturally to prevent the formation of weak spots or cracks in your joint.
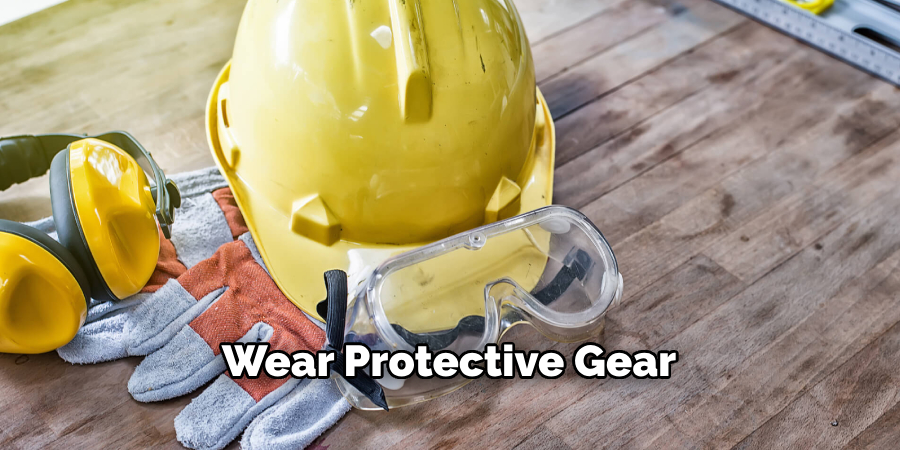
With these tips and tricks in mind, you can easily tackle your next cast iron brazing project.
5 Things You Should Avoid
- Avoid Rapid Heating: Rapidly heating the cast iron can lead to thermal shock, causing the material to crack or warp. Heat the assembly slowly and evenly to ensure proper brazing.
- Avoid Applying Direct Flame to Brazing Rod: Direct application of the torch flame to the brazing rod can cause it to drip, leading to an irregular joint. Instead, focus on heating the base metal and let its heat melt the brazing rod.
- Don’t Rush the Cooling Process: Hastening the cooling process can lead to a weak joint or possible cracks in the cast iron. Allow the assembly to cool naturally.
- Avoid Neglecting Safety Measures: Never overlook your safety when brazing. Always use appropriate safety gear and work in a well-ventilated area.
- Don’t Use the Wrong Type of Brazing Rod: Different types of cast iron require different types of brazing rods. Make sure to use the appropriate rod for your specific project to ensure a solid and durable bond.
By avoiding these common mistakes, you can ensure a successful and durable brazing process for your cast iron pieces.
Conclusion
To successfully breeze cast iron, being patient and taking your time is important. Remember that brazing requires you to start heating the studs before the filler metal melts and slowly move down to ensure both pieces are thoroughly heated through. Always refer to specific directions for the torch to ensure a secure connection between all parts.
Additionally, consider employing a heat shield or an extended flange over projected areas as an added precautionary measure. While success in brazing cast iron may come with some trial-and-error experimentation, having clear guidelines and instructions in place will always give you better control and precision than if your approach was utterly freehand.
Hopefully, the article on how to braze cast iron has helped you understand the process and give you the confidence to tackle your next project. With proper technique, patience, and attention to safety measures, you can create strong and durable bonds in your cast iron pieces. Happy brazing!
Edmund Sumlin is a skilled author for Metal Fixes, bringing 6 years of expertise in crafting a wide range of metal fixtures. With a strong background in metalwork, Edmund’s knowledge spans various types of fixtures, from decorative pieces to functional hardware, blending precision with creativity. His passion for metalworking and design has made him a trusted resource in the industry.
Professional Focus:
- Expert in Metal Fixtures : Edmund aesthetic specializes in creating durable and innovative metal fixtures, offering both appeal and functionality. His work reflects a deep understanding of metalworking techniques and materials.
- Sustainability Advocate : He is dedicated to using sustainable practices, ensuring that every fixture is crafted with eco-friendly methods while maintaining high-quality standards.
In his writing for Metal Fixes, Edmund provides valuable insights into the latest trends, techniques, and practical advice for those passionate about metal fixtures, whether they are professionals or DIY enthusiasts. His focus on combining artistry with engineering helps others discover the true potential of metal in design.