Are you looking for an affordable and durable building option? Look no further than metal buildings! These structures are becoming popular due to their strength, versatility, and cost-effectiveness. In this guide, we will take you through the steps of how to build a metal building cheap.
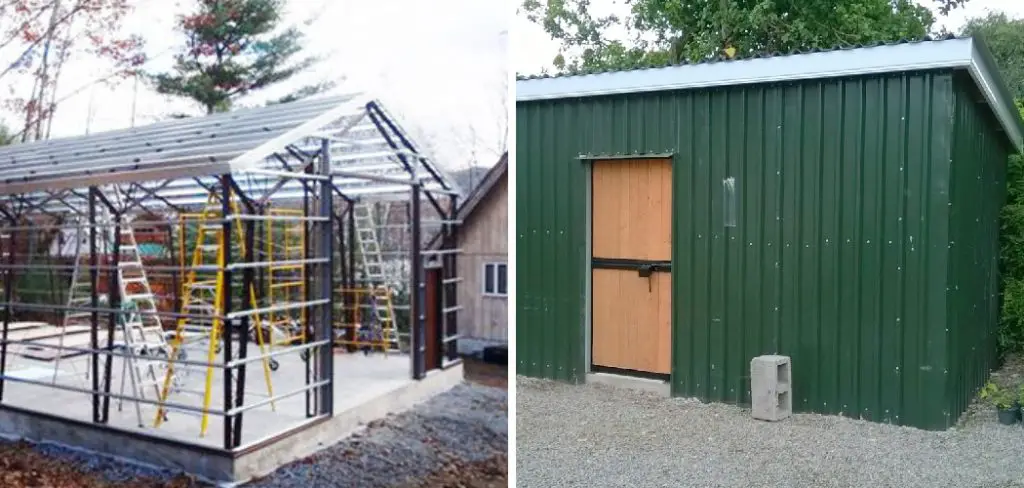
Building a metal building on a budget is a practical and efficient solution for a variety of needs, whether it’s for storage, a workshop, or even a small living space. Metal buildings are known for their durability, low maintenance, and cost-effectiveness. By opting for steel or other metal materials, you can significantly reduce construction costs while ensuring the structure stands up to the elements.
Here, we will explore various strategies and tips for building a sturdy and reliable metal building without breaking the bank.
What Will You Need?
The first step in building a metal building on a budget is selecting the right materials. Here are some factors to consider:
- Steel Vs. Other Metals: While steel is the most commonly used material for metal buildings, there are other options such as aluminum and corrugated metal. Steel is known for its strength and affordability, while aluminum is lightweight and resistant to corrosion.
- Gauge of Steel: The gauge refers to the thickness of the steel panels. A lower gauge number means thicker panels, which are stronger but also more expensive.
- Insulation: Insulation is essential in a metal building to regulate temperature and prevent condensation. It is a crucial factor to consider if you plan on using the building as a living space or for storing temperature-sensitive items.
- Additional Materials: In addition to the main structural components, you will also need roofing materials, doors, windows, and other finishing materials. These should be chosen based on your budget and the purpose of the building.
Once you have determined the materials, you will also need to prepare the site for construction. This may include clearing and leveling the land, obtaining necessary permits, and hiring a contractor if needed.
10 Easy Steps on How to Build a Metal Building Cheap
Step 1. Plan and Design Your Building
Begin by identifying the primary purpose of your metal building. Determining whether it will be used for storage, as a workshop, or as a living space will guide other design decisions, such as the size, layout, and features you need.
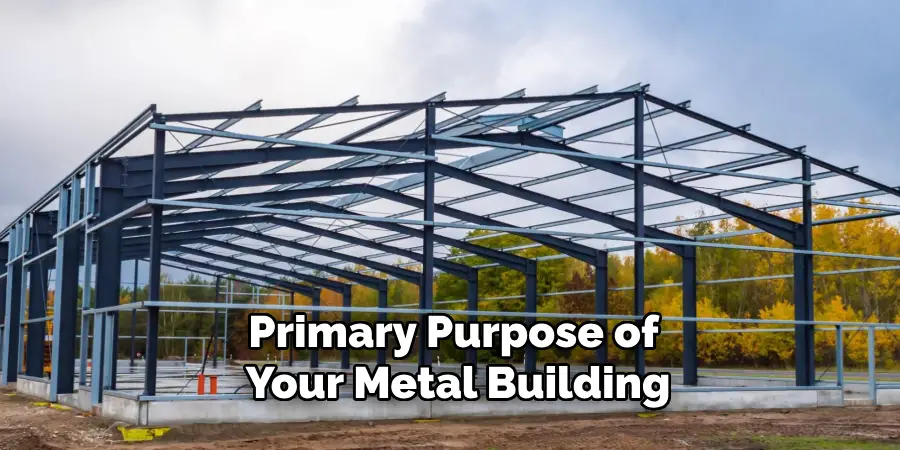
Using simple graph paper, you can sketch a basic layout that includes the dimensions and the placement of doors, windows, and internal partitions.
If your design needs are complex, consider consulting with a professional. Reaching out to a contractor or using design software can also help you create a more precise blueprint. Many metal building suppliers offer free design consultations and can provide tailored kits to match your specifications.
Step 2. Obtain Necessary Permits and Permissions
Before starting any construction, it’s essential to check with your local building authority to determine what permits and permissions are required for your project. Depending on your location, you may need a building permit, zoning approval, or other specific licenses.
Gather all the pertinent documentation, including your building plans and site layout, to submit for review. Ensuring that you comply with municipal regulations not only prevents legal issues but also guarantees that your structure adheres to safety and construction standards.
Allow sufficient time for this process, as obtaining permits can sometimes be a lengthy procedure.
Once all necessary permits and permissions are in place, you can proceed confidently with your project, knowing that it’s legally sanctioned and up to code.
Step 3. Choose the Right Kit and Supplier
Selecting the right metal building kit and supplier is crucial in ensuring you get the best value for your money. Look for reputable suppliers who offer high-quality kits with clear assembly instructions.
Compare different kits based on the materials provided, the strength and thickness of the metal panels, and any additional features that may be included, such as insulation or windows.
Request quotes from multiple suppliers and check customer reviews to gauge their reliability and the quality of their customer service.
Some suppliers may offer discounts or package deals, especially if you’re purchasing a larger or more complex kit.
By doing your homework and comparing options, you can find a kit that fits within your budget while meeting your needs for durability and functionality.
Step 4. Prepare the Building Site
Preparing the building site is a crucial step in ensuring a stable and durable metal building structure. Start by clearing the area of any debris, vegetation, or existing structures that might interfere with construction.
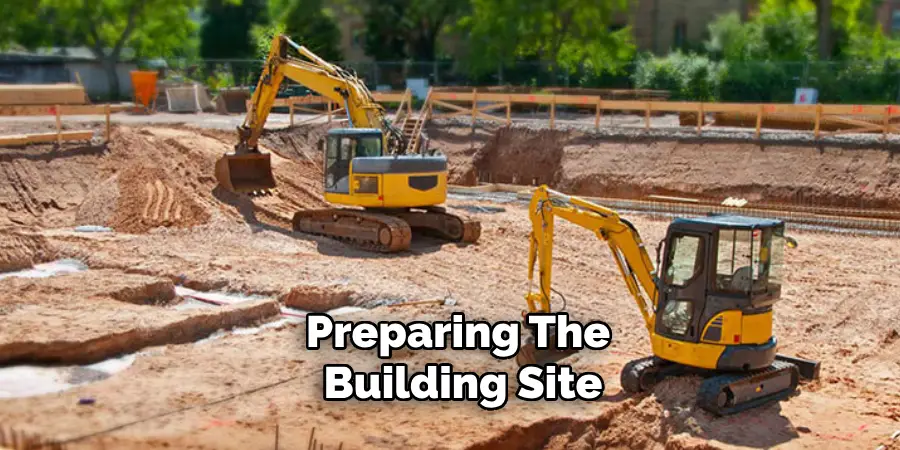
Level the ground to provide a flat and even surface for the foundation; this may require excavation or the addition of fill material to achieve the desired grade.
Next, mark the dimensions of your building on the ground using stakes and string or spray paint.
This will serve as a guide during the foundation work. Depending on your budget and the intended use of the building, you can opt for a simple gravel base, a concrete slab, or even a full basement.
If you choose a concrete slab, ensure that it is properly cured and that the anchor bolts are correctly positioned according to the building kit’s specifications.
Proper site preparation not only makes the assembly process smoother but also ensures that your metal building remains stable and secure against environmental factors like wind and moisture. This foundational work lays the groundwork—literally—for a successful construction project.
Step 5. Assemble the Frame
With your site prepared and foundation in place, it’s time to start assembling the frame of your metal building.
Begin by laying out all the components and cross-referencing them with the instruction manual to ensure you have all the necessary parts. Most metal building kits come with pre-drilled holes and prefabricated sections, making the assembly process more manageable.
Start by erecting the main support columns, ensuring they are plumb and level before securing them to the foundation.
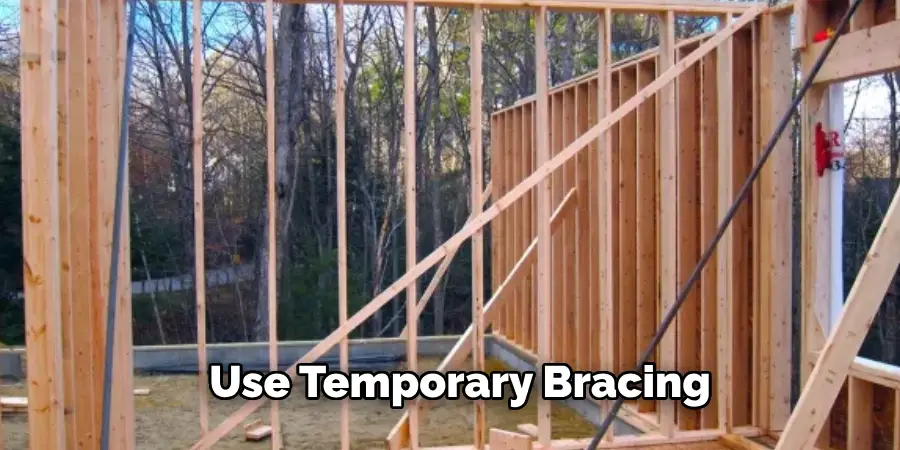
Use temporary bracing to hold the columns in place while you attach the horizontal beams and rafters. Depending on the size of your building, this may require additional hands or lifting equipment.
As you connect each section of the frame, double-check that all bolts and fasteners are tightened properly to maintain the structural integrity.
Work methodically around the entire frame, completing one section at a time. Following the manufacturer’s instructions closely will help you avoid mistakes and ensure that your building’s frame is both stable and strong.
Step 6. Install Roof and Wall Panels
Once the frame is securely in place, you can proceed to install the roof and wall panels, which will form the outer shell of your building. Start with the roof panels to provide immediate weather protection for the rest of the structure.
Begin at one end of the building and work your way to the other, ensuring each panel overlaps correctly based on the manufacturer’s guidelines. Secure them with appropriate fasteners, taking care to follow any specified spacing to ensure a tight fit.
For the wall panels, begin at a corner and work your way around the building. Like the roof panels, ensure proper overlap and alignment to create a seamless barrier against the elements.
Use the provided fasteners to attach the panels securely to the frame. It’s important to check that the panels are level and square as you go to maintain the overall integrity and appearance of the building.
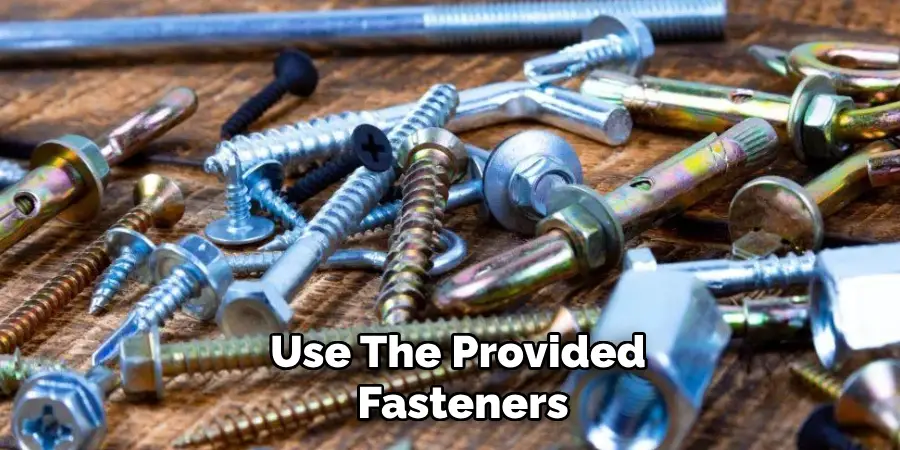
Properly installed panels not only enhance the structural strength of your building but also contribute to its aesthetic appeal, offering a neat and professional finish.
Step 7. Install Doors and Windows
After the roof and wall panels are securely in place, it’s time to install the doors and windows. Start by identifying the locations for the doors and windows as specified in your building plans. Carefully cut out the openings in the wall panels, ensuring that the cuts are precise and the edges are smooth.
Begin by installing the window frames first. Position each frame in the designated opening and secure it using the appropriate fasteners provided by the kit or as recommended by the manufacturer.
Once the frames are in place, insert the windows into the frames, ensuring they are plumb and level. Use shims if necessary to adjust the fit and prevent any gaps. Finally, seal around the edges with weatherproof caulk to prevent water and air infiltration.
Next, move on to the doors. Assemble the door frame if it isn’t already pre-assembled, then position it in the door opening. Ensure the frame is square and level before securing it to the wall panels.
Attach the door to the frame, making sure it swings open and closed smoothly. Install any door hardware, such as handles and locks, as specified by the kit instructions.
Proper installation of doors and windows not only ensures functionality but also enhances the energy efficiency and security of your metal building.
Step 8. Add Insulation
Adding insulation to your metal building is crucial for maintaining a comfortable interior environment and improving energy efficiency. Start by selecting the appropriate type of insulation for your needs, whether it’s fiberglass batts, spray foam, or rigid foam panels.
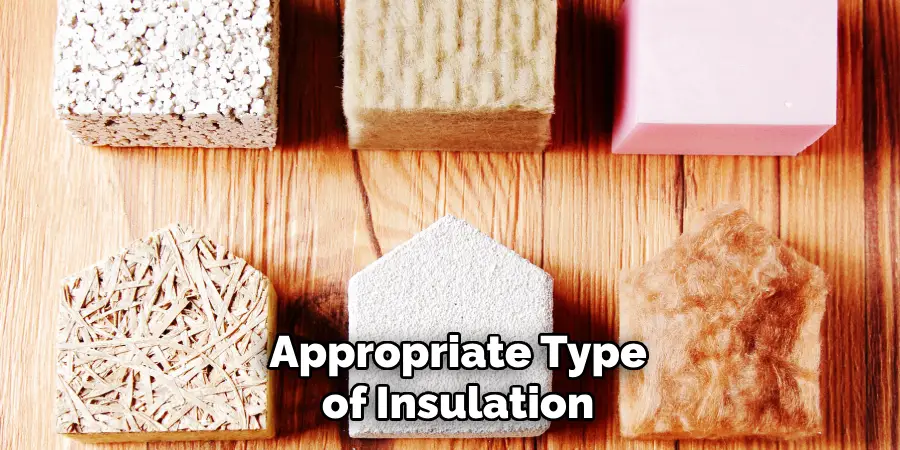
Each type has its own set of advantages, so consider factors like climate, budget, and installation ease when making your choice.
For fiberglass batts, measure and cut the insulation to fit snugly between the wall studs and roof trusses. Use a utility knife for precise cuts and ensure there are no gaps.
If you’re using spray foam insulation, carefully apply it between the studs and trusses, filling all the nooks and crannies to create an airtight seal. For rigid foam panels, secure them directly to the wall and roof surfaces using construction adhesive or special fasteners designed for foam insulation.
Once the insulation is in place, cover it with a vapor barrier to prevent moisture buildup, which can lead to mold and damage. This additional layer is especially important in regions with high humidity.
Proper insulation not only helps regulate the building’s internal temperature but also reduces energy costs by minimizing heat loss in the winter and heat gain in the summer.
Adding insulation at this step ensures that your metal building will be more comfortable and energy-efficient, contributing to the overall longevity of the structure.
Step 9. Install Electrical and Plumbing Systems
With the insulation in place, the next step is to install the electrical and plumbing systems if your metal building requires them. Begin by planning the layout of electrical wiring, outlets, switches, and lighting fixtures according to your building’s needs and local building codes.
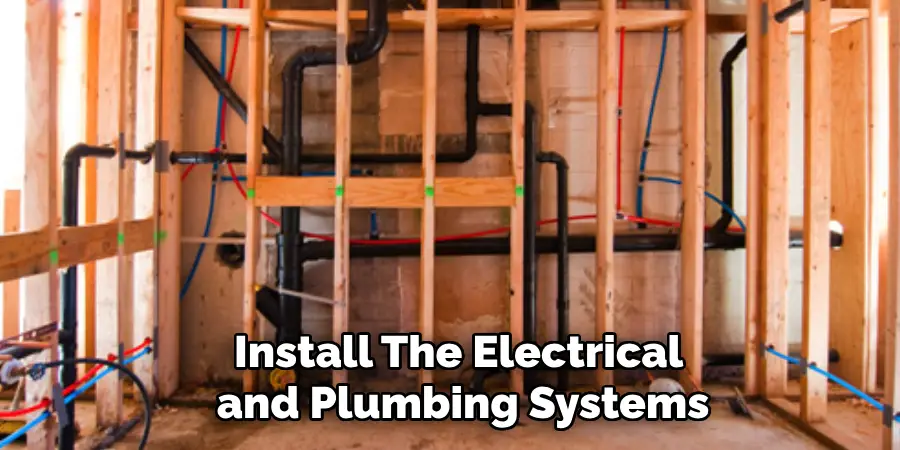
It’s recommended to consult a licensed electrician for this part of the project to ensure safety and compliance with regulations.
Run the electrical conduits and wiring through the walls and ceiling cavities, taking care to secure them properly with clips or ties. Position and install the electrical boxes for outlets and switches at appropriate heights, and mount the light fixtures as per your lighting plan.
Once the wiring is complete, attach the faceplates and make the final connections to the electrical panel.
For plumbing installations, plan the routes for water supply lines, drainage pipes, and any necessary vents. Again, consult a professional plumber to ensure that the system is installed correctly and meets local codes.
Use appropriate fittings and connectors to join the pipes and ensure that all connections are watertight to prevent leaks. Install the plumbing fixtures, such as sinks, toilets, and showers, following the manufacturer’s instructions.
Testing is a critical part of this step. Turn on the electricity and water supply to check that all systems are functioning properly. Look for any leaks in the plumbing and ensure that the electrical outlets and switches are working as expected. Address any issues immediately to avoid future problems.
Installing the electrical and plumbing systems at this stage ensures that your metal building is ready for occupancy, whether for residential, commercial, or industrial use. Proper installation is crucial for safety, functionality, and efficiency.
Step 10. Finish the Interior
With the essential systems in place, the next step is to finish the interior of your metal building. This not only completes the construction process but also enhances the building’s functionality and aesthetic appeal.
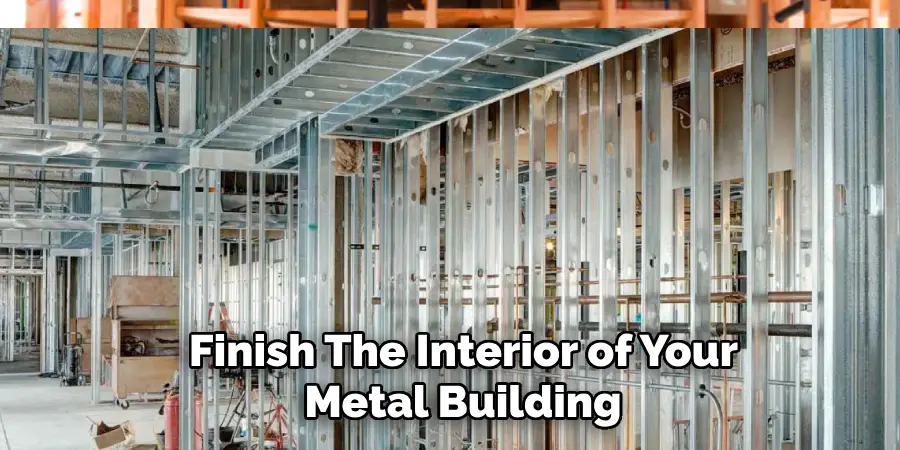
Start by covering the insulated walls with drywall or another type of paneling. Measure and cut the drywall sheets to fit the walls, securing them to the studs with drywall screws or nails.
Ensure the sheets are flush and the seams are tight; use joint tape and compound to finish the seams for a smooth surface. Once the walls are in place, move on to the ceiling, using the same method to cover the insulation and create a finished look.
After the drywall is completed, you can proceed with painting or finishing the walls with your desired type of wall covering. Select paint or wallpaper that suits the intended use of the building and reflects your personal style or business branding.
If you are painting, apply a primer first to ensure good adhesion of the paint, followed by one or two coats of the chosen color.
Next, install flooring materials suited to your needs and preferences. Options include concrete, vinyl, tile, or carpet, depending on the building’s purpose. For a durable and low-maintenance option, polished concrete or vinyl may be desirable for industrial or commercial applications.
For a more comfortable and aesthetic finish, consider carpet or hardwood flooring for residential spaces.
With the interior finishes completed, you can add fixtures and furnishings to make the space functional and comfortable. These may include shelves, cabinets, countertops, workbenches, or appliances depending on your needs.
5 Things You Should Avoid
- Compromising on Quality Materials: While it might be tempting to opt for the cheapest materials to cut costs, this can lead to serious long-term problems. Cheap materials may be prone to rust, wear, and structural failure, resulting in costly repairs or replacements down the road.
- Ignoring Insulation: Skipping insulation to save money can lead to a building that is uncomfortable to use and costly to heat or cool. Proper insulation not only improves energy efficiency but also prevents moisture buildup, which can cause mold and damage over time.
- Skipping Professional Help: While DIY projects can save money, it’s important to know when to seek professional help. Building a metal building requires specific skills, knowledge, and equipment that a layperson may not have.
- Not Considering the Purpose of the Building: When planning your metal building, it’s essential to consider its intended use. Neglecting this can result in costly modifications or additions later on. For example, if you plan to use the building for commercial purposes, it may require special permits or features that need to be included in the initial construction.
- Ignoring Local Building Codes: Every area has its own building codes and regulations that must be followed when constructing a metal building. Ignoring these can result in costly fines and delays and even the need to tear down and rebuild portions of the structure. It’s essential to research and adhere to all local building codes during the planning and construction process.
Overall, while trying to build a metal building on a budget, it’s important not to sacrifice quality and safety for cost savings.
Conclusion
How to build a metal building cheap and inexpensively involves careful planning, strategic decision-making, and a focus on maintaining quality without overspending.
By selecting cost-effective yet durable materials, prioritizing proper insulation, and knowing when to hire professionals, you can significantly reduce costs without compromising your building’s structural integrity and functionality.
Avoiding common pitfalls, such as ignoring local building codes or underestimating the building’s intended use, further ensures that your project stays within budget while meeting all necessary standards.
Ultimately, achieving an affordable metal building requires balancing costs and maintaining a high standard of workmanship, resulting in a stable, durable, and efficient space for your needs.
Edmund Sumlin is a skilled author for Metal Fixes, bringing 6 years of expertise in crafting a wide range of metal fixtures. With a strong background in metalwork, Edmund’s knowledge spans various types of fixtures, from decorative pieces to functional hardware, blending precision with creativity. His passion for metalworking and design has made him a trusted resource in the industry.
Professional Focus:
- Expert in Metal Fixtures : Edmund aesthetic specializes in creating durable and innovative metal fixtures, offering both appeal and functionality. His work reflects a deep understanding of metalworking techniques and materials.
- Sustainability Advocate : He is dedicated to using sustainable practices, ensuring that every fixture is crafted with eco-friendly methods while maintaining high-quality standards.
In his writing for Metal Fixes, Edmund provides valuable insights into the latest trends, techniques, and practical advice for those passionate about metal fixtures, whether they are professionals or DIY enthusiasts. His focus on combining artistry with engineering helps others discover the true potential of metal in design.