Crimping steel cable is a fundamental skill in various fields, from construction and marine applications to DIY projects and rigging sports equipment.
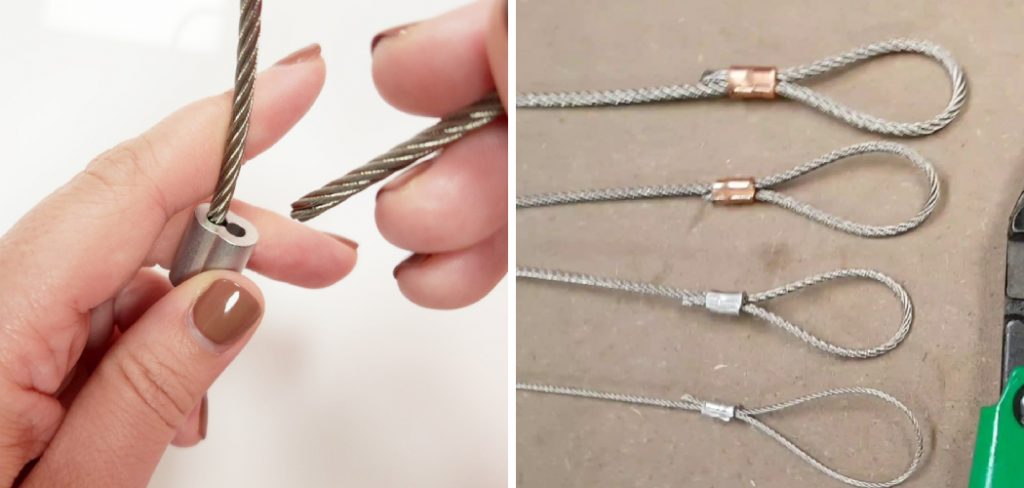
This technique involves securing a loop or fitting at the end of a steel cable using a crimping tool and appropriate fittings, ensuring a strong, reliable connection.
Proper crimping is crucial for the cable’s integrity and safety, as an improperly crimped cable can lead to failure under load, posing significant risks.
The process requires precision and the right tools, including crimping pliers, sleeves or ferrules, and often a swaging tool for heavier-duty applications. Additionally, understanding the types of steel cable and appropriate crimping methods for each can greatly influence the effectiveness and durability of the crimped connection.
This article provides a comprehensive guide on how to crimp steel cable, outlining the necessary equipment, step-by-step instructions, and key tips to ensure a secure and lasting crimp.
Importance of Properly Crimping Steel Cables
Properly crimping steel cables is vital for ensuring both the performance and safety of any application involving such cables. When done correctly, crimping forms a secure and reliable connection that can handle significant loads without slipping or failing.
This is especially important in high-stakes environments such as construction sites, maritime operations, and athletic setups, where a failure could result in serious injury, equipment damage, or financial loss.
An improperly crimped cable, on the other hand, can quickly become a weak point in a system, potentially leading to catastrophic failure.
Additionally, a well-executed crimp enhances the cable’s resistance to wear and environmental factors, extending its service life and reducing maintenance needs.
Therefore, investing time and resources in learning and executing proper crimping techniques is essential for ensuring the durability and efficacy of steel cable systems.
Benefits of Steel Cable Crimping
Crimping steel cables offers numerous benefits that make it an indispensable technique across various applications.
One of the primary advantages is the enhanced security it provides; a properly crimped cable ensures a robust connection that can withstand substantial loads without the risk of detachment or slippage.
This level of security is critical in high-stress environments such as construction, aviation, and marine operations.
Additionally, crimping helps in maintaining the structural integrity of the cable, preventing fraying and wear over time, which extends the cable’s overall lifespan. The process also contributes to the efficient distribution of load pressure along the cable, minimizing weak points and enhancing performance.
Furthermore, crimping is a versatile technique that can be used with various types of fittings and terminals, making it adaptable to diverse needs and specifications. Thus, mastering the art of steel cable crimping is beneficial for ensuring dependable, durable, and versatile cable connections.
Understanding Steel Cables
Before delving into the crimping process, it is essential to understand the basic properties and types of steel cables. Steel cables, also known as wire ropes, are composed of several strands of steel wire twisted or braided together to form a robust and flexible structure.
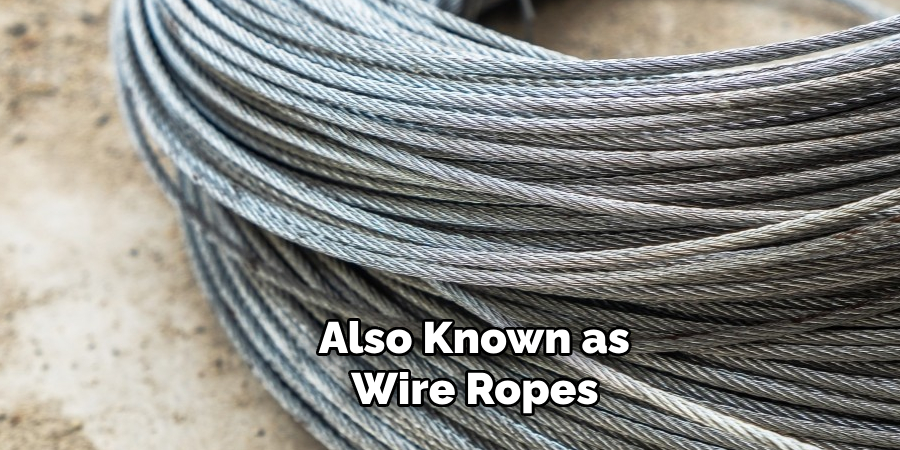
These cables are designed to handle high tensile loads, making them suitable for a wide range of heavy-duty applications.
The core of a steel cable can vary, with options such as fiber cores, wire strand cores, or independent wire rope cores, each offering distinct benefits regarding flexibility, strength, and resistance to crushing.
The type of steel used in the cable also plays a crucial role in its performance. Common materials include carbon steel, which provides good strength and durability, and stainless steel, which offers excellent corrosion resistance in harsh environments.
Additionally, steel cables come in various configurations, such as different strand patterns (e.g., 7×19, 6×36) and constructions (e.g., uncoated, galvanized, PVC-coated), each tailored for specific uses and conditions.
Steel Cable Construction and Composition
Steel cable construction and composition are fundamental aspects that determine the cable’s performance, durability, and suitability for various applications.
Steel cables are typically constructed by twisting together multiple wires to form strands, which are then helically wound around a core. This construction contributes to the cable’s overall strength, flexibility, and ability to absorb energy.
Strands and Cores
The composition of steel cables generally involves two main components: strands and cores. Strands are groups of individual wires twisted together, and multiple strands are then twisted or braided around a core to form the complete cable. The core can be made from different materials, each offering distinct advantages:
- Fiber Core (FC): Made from natural or synthetic fibers, these cores provide excellent flexibility and absorb shock loads, making them suitable for applications where the cable must endure repeated bending.
- Wire Strand Core (WSC): Composed of wire strands, this type of core offers higher strength and better resistance to crushing than fiber cores. It is commonly used in applications requiring higher tensile strength.
- Independent Wire Rope Core (IWRC): This is essentially a small wire rope that serves as the core within the larger cable. IWRC provides superior strength, stability, and resistance to abrasion, making it ideal for high-load and high-resistance applications.
Wire Materials
The type of steel used to manufacture the wires can significantly impact the cable’s properties:
- Carbon Steel: Known for its strength and durability, carbon steel is widely used in general-purpose steel cables. It offers a good balance between cost and performance.
- Stainless Steel: Provides excellent resistance to corrosion and is ideal for use in harsh environments, such as marine or chemical industries. Stainless steel cables are more expensive but offer long-term durability and maintenance benefits.
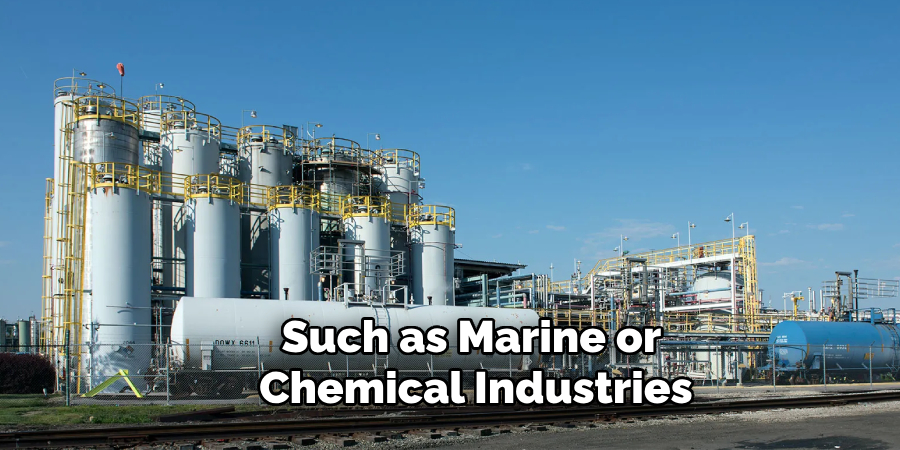
Coatings and Configurations
Steel cables are available in various coatings and configurations to enhance their performance and suitability for specific environments:
- Uncoated: Raw steel cables that offer maximum strength but are susceptible to corrosion.
- Galvanized: Zinc-coated to provide rust and corrosion resistance, making them suitable for outdoor and moist environments.
- PVC-Coated: Encased in a protective PVC layer, these cables offer additional corrosion protection, abrasion resistance, and safety for handling.
Standard Configurations
Common configurations of steel cables include different strand patterns and constructions that dictate their flexibility and load-bearing capacity:
- 7×19 Configuration: This pattern consists of seven strands, each containing nineteen wires, providing excellent flexibility and fatigue resistance. It is commonly used in aircraft control cables and other applications requiring flexibility.
- 6×36 Configuration: Contains six strands, each with thirty-six wires. This construction offers higher strength and durability, suitable for heavy lifting and load-bearing applications.
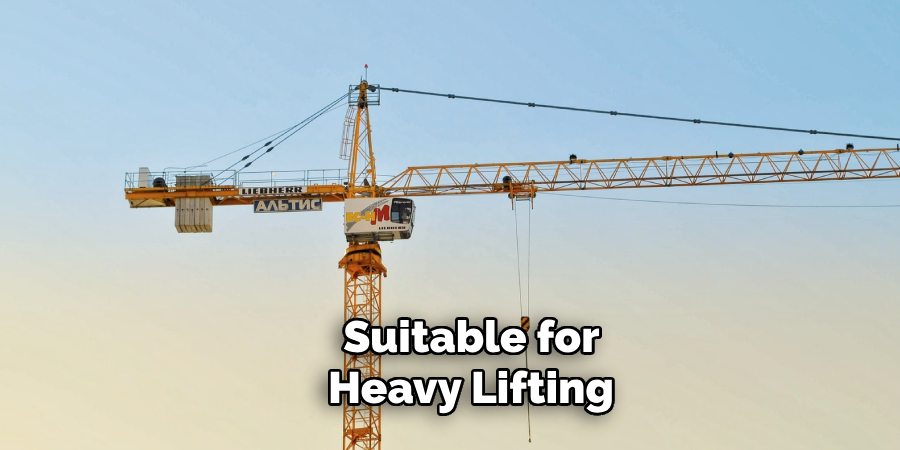
Understanding the construction and composition of steel cables is essential for selecting the right type of cable for your specific needs. This knowledge ensures that the chosen cable will meet the demands of the application, providing both safety and performance.
10 Methods How to Crimp Steel Cable
1. Hand Crimping with Manual Tools
Hand crimping with manual tools is a straightforward and accessible method for crimping steel cables.
This technique involves using hand-operated crimping pliers or crimping tools designed specifically for steel cables. The process begins by selecting the appropriate size of crimping sleeve or ferrule for the cable.
The sleeve is then positioned over the ends of the cable, which may be looped back to form an eye or end fitting. The manual crimping tool is then used to apply pressure evenly, compressing the sleeve and securing the cable ends in place.
This method is ideal for small to medium-sized cables and is commonly used in applications such as rigging, fencing, and DIY projects due to its simplicity and low cost. However, it requires physical strength and precision to ensure a secure crimp, and may not be suitable for very thick cables or high-load applications.
2. Hydraulic Crimping
Hydraulic crimping uses a hydraulic crimping tool to exert high pressure on the crimping sleeve, ensuring a strong and secure connection. This method is particularly effective for larger diameter cables or situations requiring high tensile strength.
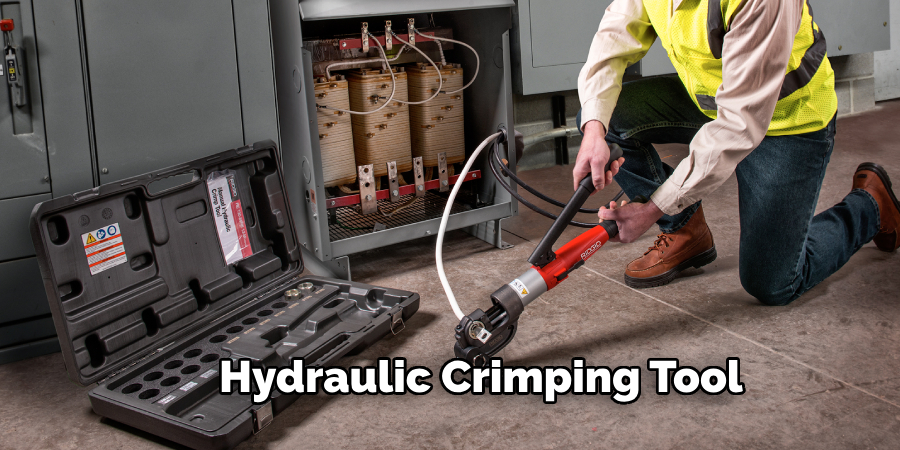
The hydraulic crimping tool typically consists of a pump (manual or electric) and a crimping head with interchangeable dies to accommodate different sleeve sizes.
The process involves placing the crimping sleeve over the cable ends, inserting the assembly into the crimping head, and operating the pump to apply hydraulic pressure.
The advantage of hydraulic crimping is its ability to generate significant force with minimal physical effort, resulting in a consistent and reliable crimp. This makes it suitable for heavy-duty applications such as construction, marine, and industrial rigging.
3. Swaging with a Swaging Machine
Swaging involves using a swaging machine to deform a metal sleeve around the steel cable, creating a secure and permanent connection. The swaging machine can be hydraulic, pneumatic, or mechanical, and is equipped with a set of dies that match the size of the sleeve and cable.
The process starts by threading the cable through the sleeve and positioning it in the swaging machine. The machine then compresses the sleeve uniformly, ensuring a tight fit.
Swaging is known for producing high-strength terminations and is commonly used in aviation, marine, and structural applications.
It offers the advantage of producing a smooth, streamlined finish that minimizes snagging and wear, making it ideal for applications where aesthetics and performance are critical.
4. Electrical Crimping
Electrical crimping utilizes electrically powered crimping tools to secure steel cable ends. These tools are designed to deliver precise and consistent pressure, reducing the risk of improper crimps and ensuring reliable performance.
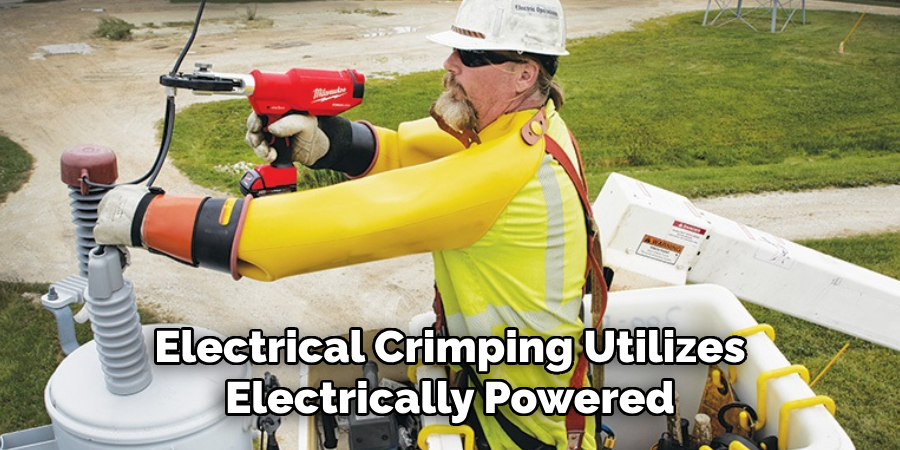
The process involves selecting the appropriate crimping die, placing the crimping sleeve over the cable ends, and using the electric crimping tool to compress the sleeve. Electrical crimping tools often feature adjustable settings and interchangeable dies to accommodate different cable sizes and sleeve types.
This method is particularly advantageous in high-volume production environments where speed and consistency are paramount.
Electrical crimping is widely used in industries such as telecommunications, automotive, and manufacturing, where reliable and efficient cable terminations are essential.
5. Nicopress Method
The Nicopress method involves using Nicopress sleeves and a corresponding hand-operated or hydraulic crimping tool to secure steel cables. Nicopress sleeves are designed with precise tolerances to ensure a tight fit and strong connection when crimped.
The process starts by threading the cable through the sleeve, creating a loop or termination as required, and then using the Nicopress tool to compress the sleeve. This method is known for its reliability and ease of use, making it popular in applications such as marine rigging, agricultural fencing, and theatrical rigging.
Nicopress tools are available in various sizes to accommodate different cable diameters, and the resulting crimps are often tested to ensure they meet specific strength requirements.
6. Flemish Eye Splicing with Crimping
Flemish eye splicing involves creating a loop at the end of a steel cable by forming an eye splice and securing it with a crimped sleeve. The process begins by unlaying the strands of the cable at the end, forming an eye, and then re-laying the strands to create a splice.
A metal sleeve is then placed over the splice, and a crimping tool is used to compress the sleeve, securing the splice in place. This method is known for its strength and reliability, as the Flemish eye splice distributes the load evenly across the cable strands.
It is commonly used in applications such as lifting, rigging, and towing, where high strength and safety are critical. The combination of the spliced eye and crimped sleeve ensures a durable and secure termination.
7. Rotary Swaging
Rotary swaging is a precision method that involves using a rotary swaging machine to compress a metal sleeve around a steel cable.
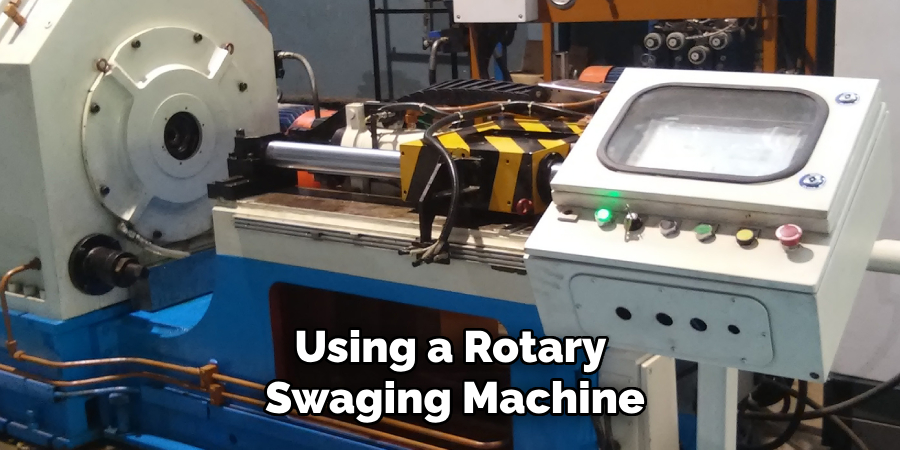
The machine uses rotating dies that hammer the sleeve uniformly, reducing its diameter and securing the cable. Rotary swaging is known for producing smooth, high-quality crimps with minimal deformation of the cable strands.
The process starts by placing the sleeve over the cable ends, inserting the assembly into the swaging machine, and activating the machine to perform the swaging. This method is particularly effective for creating compact, strong terminations and is widely used in aerospace, automotive, and industrial applications.
Rotary swaging offers the advantage of producing consistent crimps with high precision, making it ideal for critical applications where performance and reliability are essential.
8. Wire Rope Clips
Wire rope clips, also known as cable clamps, provide a simple and effective method for securing steel cables. The clips consist of a U-bolt, a saddle, and nuts, which are used to clamp the cable in place. The process involves placing the U-bolt over the cable, positioning the saddle on the opposite side, and tightening the nuts to secure the assembly.
Multiple clips are often used in tandem to ensure a secure connection. Wire rope clips are easy to install and adjust, making them ideal for temporary or adjustable connections.
They are commonly used in construction, marine, and agricultural applications for tasks such as guying, securing loads, and creating adjustable loops. While wire rope clips are versatile and convenient, it is important to follow proper installation guidelines to ensure a secure and reliable connection.
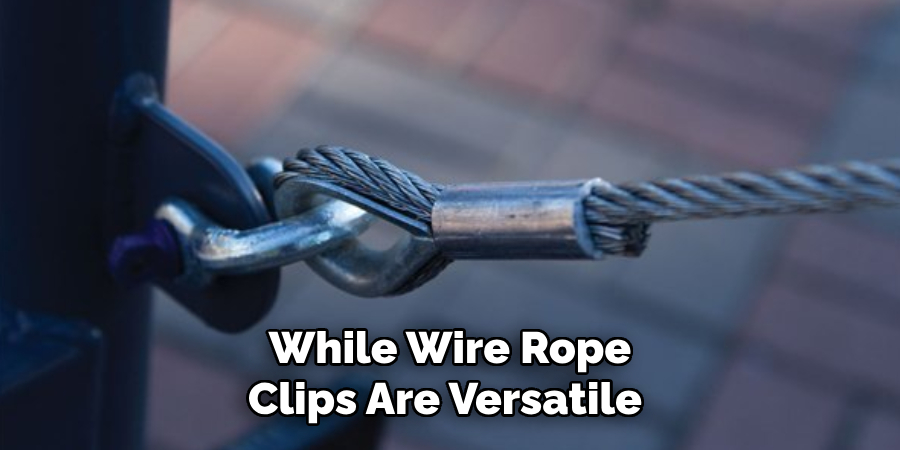
9. Combination Crimping and Welding
Combination crimping and welding involve using both mechanical crimping and welding techniques to secure steel cables. The process starts by placing a metal sleeve over the cable ends and using a crimping tool to compress the sleeve, creating an initial mechanical connection.
The sleeve is then welded to the cable, providing additional strength and security. This method is particularly effective for high-load applications where maximum strength and reliability are required.
The combination of crimping and welding ensures that the cable termination is both mechanically and metallurgically secure, reducing the risk of failure under load. This technique is commonly used in applications such as construction, heavy lifting, and industrial rigging, where safety and performance are paramount.
10. Using Swage Sockets
Swage sockets are specialized fittings used to create terminations on steel cables. The process involves inserting the cable into the swage socket and using a swaging machine to compress the socket around the cable, creating a secure and permanent connection.
Swage sockets are designed to provide high strength and reliability, making them ideal for critical applications such as lifting, towing, and structural supports. The process starts by cutting the cable to the desired length, inserting it into the swage socket, and using the swaging machine to compress the socket uniformly.
Swage sockets are available in various types, including open and closed sockets, to accommodate different application requirements. This method offers the advantage of producing strong, low-profile terminations that are both functional and aesthetically pleasing.
Conclusion
Crimping steel cables is an essential process in various industries, ensuring secure and reliable terminations for a wide range of applications. The methods discussed, from hand crimping with manual tools to using swage sockets, each offer unique advantages tailored to specific needs.
Hand crimping with manual tools provides an accessible and cost-effective solution for small to medium-sized cables, while hydraulic crimping offers the power and consistency needed for larger cables and high-load applications.
Swaging, whether with a swaging machine or through rotary swaging, ensures strong, uniform crimps suitable for critical applications. Electrical crimping and the Nicopress method bring precision and reliability to high-volume production environments.
The Flemish eye splicing method, wire rope clips, combination crimping and welding, and using swage sockets each provide specialized solutions for various use cases, from temporary adjustments to permanent, high-strength terminations. Thanks for reading, and we hope this has given you some inspiration on how to crimp steel cable!
Edmund Sumlin is a skilled author for Metal Fixes, bringing 6 years of expertise in crafting a wide range of metal fixtures. With a strong background in metalwork, Edmund’s knowledge spans various types of fixtures, from decorative pieces to functional hardware, blending precision with creativity. His passion for metalworking and design has made him a trusted resource in the industry.
Professional Focus:
- Expert in Metal Fixtures : Edmund aesthetic specializes in creating durable and innovative metal fixtures, offering both appeal and functionality. His work reflects a deep understanding of metalworking techniques and materials.
- Sustainability Advocate : He is dedicated to using sustainable practices, ensuring that every fixture is crafted with eco-friendly methods while maintaining high-quality standards.
In his writing for Metal Fixes, Edmund provides valuable insights into the latest trends, techniques, and practical advice for those passionate about metal fixtures, whether they are professionals or DIY enthusiasts. His focus on combining artistry with engineering helps others discover the true potential of metal in design.