Cutting carbide requires specialized tools and techniques due to its extreme hardness and brittleness.
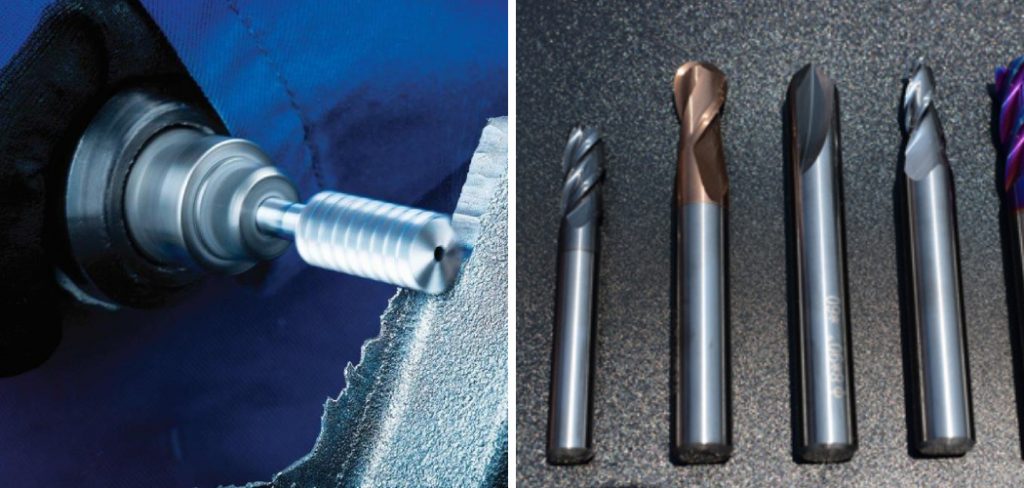
It’s widely used in industrial applications for its durability and heat resistance, making it a valuable material for cutting and drilling. However, because of its resilience, improper cutting methods can lead to tool damage or inefficient work processes.
This guide on how to cut carbide will provide a comprehensive overview of the best practices for cutting carbide efficiently and safely, ensuring that you achieve precise results and extend the life of your cutting tools.
What is Carbide?
Carbide is a composite material composed of carbon and other elements, such as titanium, tungsten, or tantalum. It’s known for its extreme hardness, ranking nine on the Mohs scale, making it one of the hardest materials used in industrial applications.
This impressive hardness allows carbide to withstand high temperatures without losing its strength, making it ideal for cutting and drilling tough materials like steel, cast iron, or stainless steel.
You may have come across the term “tungsten carbide” before, which refers to a specific type of carbide made up of tungsten and carbon. This type is commonly used in cutting tools due to its high wear resistance and ability to maintain sharp edges for extended periods.
Why is Cutting Carbide Different?
Cutting carbide requires specialized tools and techniques because of its hardness and brittleness. Traditional cutting methods, such as using high-speed steel (HSS) tools, are not suitable for carbide as they will quickly wear down and become dull due to the material’s extreme hardness.
Furthermore, improper cutting techniques can cause damage to the cutting tool or result in inaccurate cuts, leading to a waste of both time and resources. Therefore, understanding the appropriate methods for cutting carbide is crucial for achieving efficient and precise results.
Tools Needed for Cutting Carbide
To cut carbide effectively, you will need specialized tools that can handle its hardness and brittleness without breaking or chipping. Some essential tools for cutting carbide include:
Diamond-tipped Saw Blades:
These are specifically designed to cut through hard materials like carbide. The diamond particles on the blade’s edge grind through the carbide, creating a clean and precise cut.
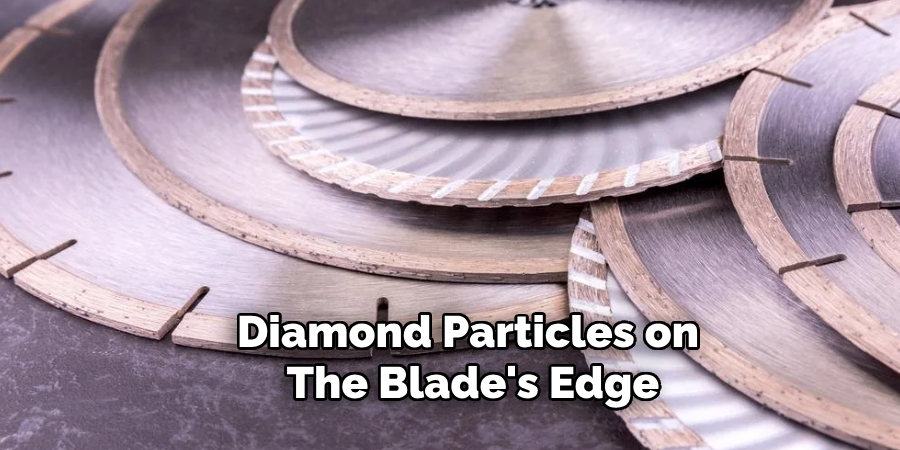
Carbide-Tipped Drill Bits:
Also known as “masonry” bits, these are designed to drill into tough materials like concrete, stone, and of course, carbide. The tip is made of tungsten carbide or titanium carbide for increased durability.
Solid Carbide End Mills:
These are used for milling operations and come in various shapes and sizes depending on the desired cutting result. They are made entirely of carbide material and can withstand high temperatures without losing their sharp edges.
8 Step-by-step Guidelines on How to Cut Carbide
Step 1: Choose the Proper Tool for the Job
Selecting the right tool is crucial when it comes to cutting carbide efficiently. The tool of choice largely depends on the specific type and shape of carbide you are working with, as well as the type of cut required.
For instance, diamond-tipped saw blades are ideal for making precise, straight cuts, while carbide-tipped drill bits are best suited for drilling holes.
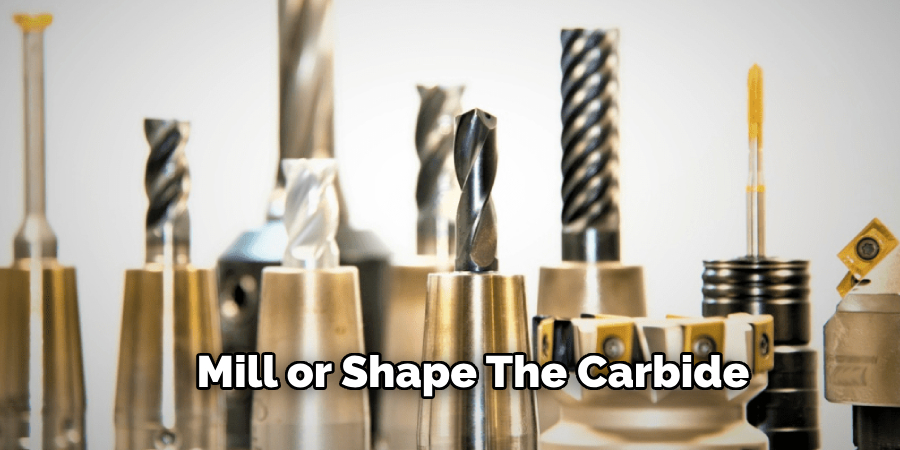
If you need to mill or shape the carbide, solid carbide end mills would be the go-to option. Ensure that any tool you select is rated for cutting carbide to prevent premature wear or breakage. Investing in high-quality tools designed for carbide will not only yield better results but also extend the lifespan of your cutting equipment.
Step 2: Wear Appropriate Safety Gear
Safety should always be your top priority when cutting carbide. Due to the hardness and brittleness of carbide, cutting it can produce sharp fragments and dust that pose risks of injury and respiratory issues.
To protect yourself, always wear safety goggles to shield your eyes from flying debris. A dust mask or respirator is essential to prevent inhalation of fine carbide particles, which can be harmful to your lungs.
Additionally, wearing cut-resistant gloves will protect your hands from sharp edges and fragments. It’s also advisable to wear long sleeves and protective clothing to shield your skin. Ensuring you have the right protective gear will help minimize the risk of injury and create a safer working environment.
Step 3: Prepare the Work Area
Before you begin cutting carbide, it’s essential to prepare your work area to ensure a smooth and safe process.
Start by cleaning the workspace to remove any debris, dust, or obstructions that could interfere with your cutting operation. A clean surface helps maintain precision and reduces the risk of accidents.
Next, secure adequate lighting to provide clear visibility of the material and tools you’re working with. Good lighting is crucial for accuracy and safety, especially when dealing with tough materials like carbide.
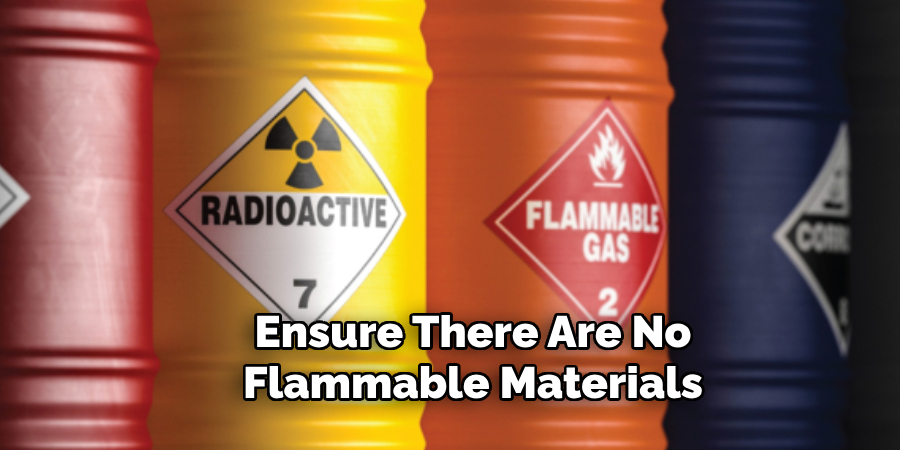
Also, ensure there are no flammable materials nearby to prevent potential hazards.
Step 4: Secure the Carbide Material
To achieve precise cuts and maintain safety, it’s essential to secure the carbide material firmly before you start cutting. Begin by placing the carbide on a stable, flat surface that can support its weight and size. Use a heavy-duty vise or clamp specifically designed for holding hard materials.
Ensure the vise or clamp is tightened adequately to prevent any movement during the cutting process, as even minor shifts can lead to inaccurate cuts or potential hazards.
Position the carbide material in such a way that it is fully supported and won’t wobble or tilt. If you’re working with a larger piece, consider using additional clamps to stabilize both ends. Double-check that the carbide is well-secured before turning on any cutting equipment.
Properly securing the material not only enhances cutting accuracy but also significantly reduces the risk of accidents caused by unexpected movements.
Step 5: Choose the Appropriate Cutting Speed and Feed Rate
The cutting speed and feed rate are critical factors that affect the efficiency and precision of your cuts. The cutting speed refers to how fast the tool is moving in relation to the material being cut, while the feed rate determines how much material is removed with each pass.
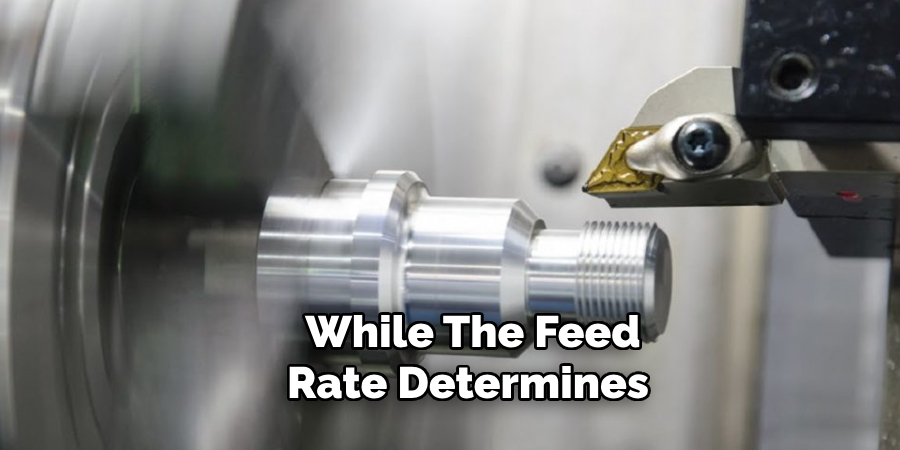
For carbide, a slower cutting speed is recommended to prevent overheating and preserve the sharpness of the tools. In contrast, a higher feed rate helps remove material efficiently without putting excessive strain on the cutting equipment.
It’s essential to find a balance between these two factors for optimal results. Always consult your tool manufacturer’s recommendations for specific cutting speeds and feed rates suitable for carbide materials.
Step 6: Use Coolants
Coolants are essential when cutting carbide to prevent overheating and preserve the integrity of the tools. Most coolants come in liquid form and can be sprayed or applied directly to the cutting area through a nozzle or drip system. The coolant helps reduce friction, dissipate heat, and lubricate the cutting surfaces for smoother operation.
Choose a coolant specifically designed for cutting carbide materials, as it will provide optimal results while extending the life of your tools. Additionally, make sure to replenish the coolant frequently to maintain its effectiveness throughout the cutting process.
Step 7: Start Cutting
Once you have properly prepared your work area and secured the carbide material, it’s time to start cutting. Depending on the type of cutting tool you’re using, begin by aligning it with the desired cut line and gently lowering it onto the surface.
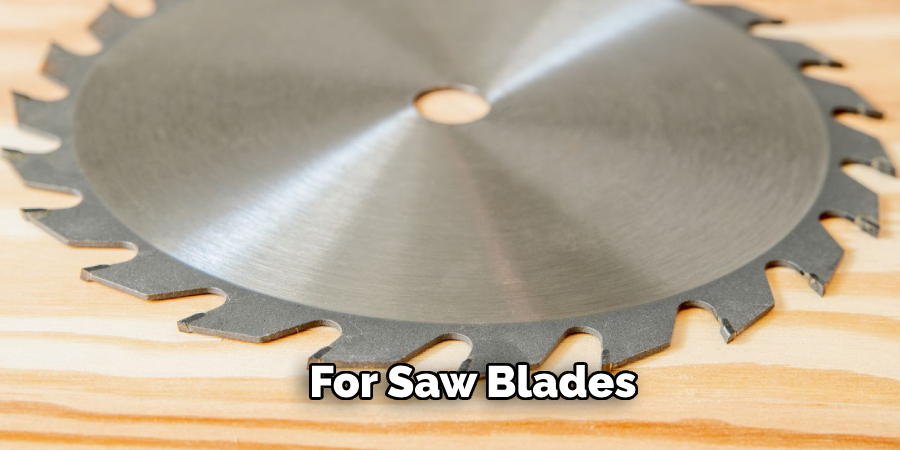
For saw blades, ensure the carbide material is securely clamped to prevent any movement or vibrations that can affect the accuracy of your cuts.
Use slow, steady movements when cutting to maintain stability and precision. Avoid forcing the tool through the material as this can lead to breakage or damage to both tools and materials.
Step 8: Inspect the Cut
After completing the cutting process, it’s crucial to carefully inspect the cut to ensure it meets the required specifications and quality standards. Start by examining the cut edges for smoothness and precision.
Look for any signs of roughness, chipping, or unevenness, which could indicate that adjustments to your cutting technique or equipment are needed.
Use a magnifying glass or a digital microscope for a closer inspection of the cut surface to identify any potential defects.
Verify that the cut dimensions align with your design specifications using precise measuring tools such as calipers or micrometers. If the cut does not meet the desired standards, you may need to perform additional finishing operations, such as grinding or polishing, to achieve the perfect result.
Following these steps on how to cut carbide when cutting carbide will not only ensure your safety and the longevity of your tools but also produce high-quality cuts that meet your specific requirements.
Remember to always prioritize safety and precision, and regularly maintain your cutting equipment for optimal performance. With proper preparation and techniques, you can achieve accurate and smooth cuts in even the toughest carbide materials. Happy cutting!
Common Issue When Cutting Carbide
Despite following the proper steps and precautions, some common issues may still arise when cutting carbide. These can include:
Overheating:
This occurs when the cutting speed is too high, causing excessive heat build-up that can damage both the tool and the material.
Chipping or Breakage:
If the feed rate is too low or there are vibrations in the cutting process, it can lead to chipping or breakage of either the tool or material.
Dulling of Tools:
The use of improper coolant or inadequate replenishing of coolant can cause the tools to become dull, affecting their cutting performance.
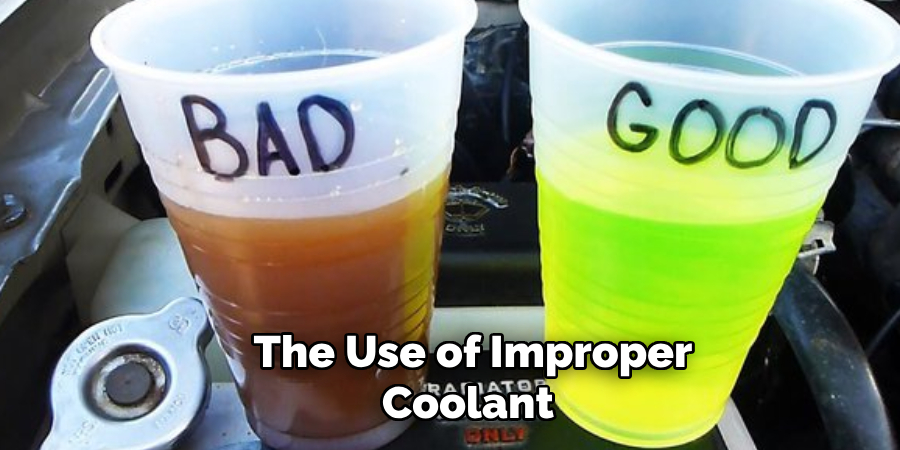
Uneven Cuts:
Poor clamping or unstable material can result in uneven cuts and imprecise dimensions.
To avoid these issues, always follow the recommended cutting parameters for carbide materials and regularly inspect and maintain your tools and equipment. If problems persist, consult a professional or seek guidance from your tool manufacturer. Happy cutting!
Safety Considerations and Environmental Impact
When working with carbide materials, it’s imperative to prioritize safety and be mindful of the environmental impact.
Proper use of personal protective equipment (PPE), such as gloves, safety goggles, and respirators, is essential to protect against dust, flying debris, and potential inhalation of harmful particles. Ensure that your work area is well-ventilated and that dust extraction systems are in place to minimize airborne particulate matter.
It’s also important to handle and dispose of carbide scrap responsibly. Carbide materials contain cobalt, which can be hazardous if not managed properly.
Ensure that all scrap and waste are collected and recycled through certified facilities that can safely process and reuse these materials. This not only helps in reducing environmental pollution but also conserves resources.
Additionally, always be cautious when using coolants, as improper disposal can lead to contamination of water sources.
Follow local regulations for the disposal of industrial coolants, and consider using biodegradable options where possible. Regular maintenance of equipment to prevent leaks and spills further contributes to a responsible and safe working environment.
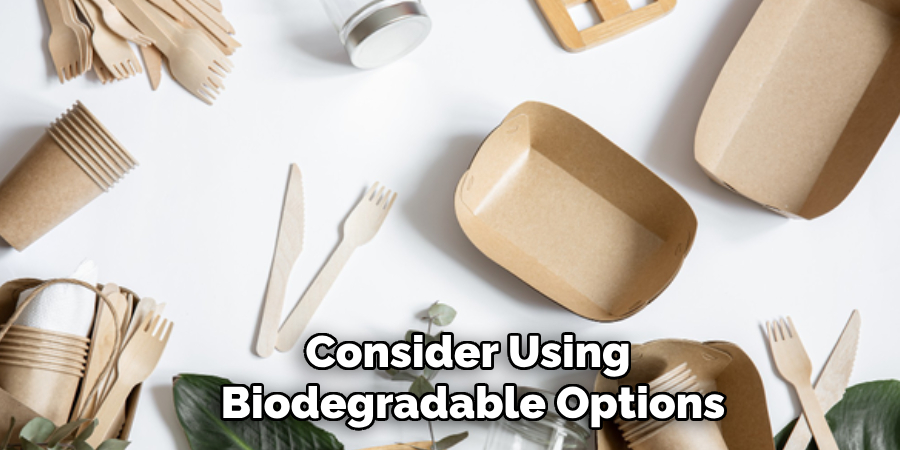
By adhering to these safety considerations and being eco-conscious, you help protect both yourself and the planet, ensuring that your cutting operations are not only efficient but also sustainable and responsible.
Do You Need to Use Professionals?
When it comes to cutting carbide, the question of whether to hire professionals often arises. The decision largely depends on the complexity of the cutting tasks, your level of experience, and the precision required for your project.
Professionals in the field come equipped with advanced machinery, specialized tools, and a wealth of expertise, allowing them to handle intricate and challenging cuts with ease. They can also help ensure that the job is done efficiently and safely, reducing the risk of tool damage or personal injury.
Additionally, professionals are well-versed in adhering to industry standards and best practices, which can be crucial for projects demanding high-quality results and tight tolerances.
Hiring experienced technicians can also be cost-effective in the long run, as it mitigates the expenses associated with potential mistakes, tool degradation, and material wastage.
However, if you possess the necessary skills, tools, and a comprehensive understanding of the cutting process, you may choose to undertake the task yourself.
Just ensure that all safety protocols are meticulously followed and that your equipment is well-maintained. Evaluating the scale and requirements of your project can help you make an informed decision on whether to engage professional services or to proceed independently.
Frequently Asked Questions
Q: What Types of Tools Are Suitable for Cutting Carbide?
A: Some common tools used for cutting carbide include carbide-tipped saw blades, diamond abrasive wheels, and high-speed steel (HSS) cutters. The choice of tool depends on the type and thickness of the carbide material being cut, as well as personal preference and availability.
Q: Can I Use Regular Coolants to Cut Carbide?
A: No, it’s not recommended to use regular coolants when cutting carbide materials.
Regular coolants may not be effective in reducing friction and dissipating heat produced during cutting, leading to overheating and damage to tools and materials. It’s best to use a coolant specifically designed for cutting hard materials like carbide.
Q: How Do I Know if My Cut is Accurate?
A: There are several ways to check the accuracy of your cut. You can use specialized measuring tools such as calipers or micrometers to compare the dimensions of your cut with your design specifications.
Additionally, inspecting the cut surface for smoothness and any signs of defects can also help determine its accuracy. If necessary, you can perform further finishing operations to achieve the desired result.
Q: Can I Cut Carbide Using Hand Tools?
A: It is not recommended to use hand tools when cutting carbide due to its hardness and abrasiveness. Hand tools may wear out quickly or become damaged, resulting in inaccurate cuts or potential hazards. It’s best to use power tools specifically designed for cutting carbide for better efficiency and safety.
Q: How Often Should I Replace My Cutting Tools?
A: The frequency of replacing cutting tools depends on various factors such as the type and thickness of the carbide material, cutting speeds, and feed rates used.
Typically, higher-quality tools with proper maintenance can last longer before needing replacement. However, it’s crucial to regularly inspect your tools for signs of wear or damage and replace them when necessary to maintain optimal performance and safety.
Overall, following manufacturer recommendations and guidelines can help determine the appropriate time to replace your cutting tools.
Additionally, frequent replacements may indicate that adjustments to the cutting process or equipment are needed for better results and longer tool life. Keep track of your tool usage and performance to make informed decisions about when to replace them.
Conclusion
Cutting carbide materials requires precision, patience, and the right equipment. By following these steps on how to cut carbide and using appropriate safety measures, you can achieve accurate cuts while ensuring your own safety.
Remember to always wear protective gear, prepare your work area properly, and use coolants for the best results.
With practice and attention to detail, you can master the art of cutting carbide materials and achieve flawless results every time. So go ahead and take on that next challenging project with confidence! Happy cutting!
Edmund Sumlin is a skilled author for Metal Fixes, bringing 6 years of expertise in crafting a wide range of metal fixtures. With a strong background in metalwork, Edmund’s knowledge spans various types of fixtures, from decorative pieces to functional hardware, blending precision with creativity. His passion for metalworking and design has made him a trusted resource in the industry.
Professional Focus:
- Expert in Metal Fixtures : Edmund aesthetic specializes in creating durable and innovative metal fixtures, offering both appeal and functionality. His work reflects a deep understanding of metalworking techniques and materials.
- Sustainability Advocate : He is dedicated to using sustainable practices, ensuring that every fixture is crafted with eco-friendly methods while maintaining high-quality standards.
In his writing for Metal Fixes, Edmund provides valuable insights into the latest trends, techniques, and practical advice for those passionate about metal fixtures, whether they are professionals or DIY enthusiasts. His focus on combining artistry with engineering helps others discover the true potential of metal in design.