How to cut expanded metal is a crucial skill for numerous construction, industrial, and DIY projects.
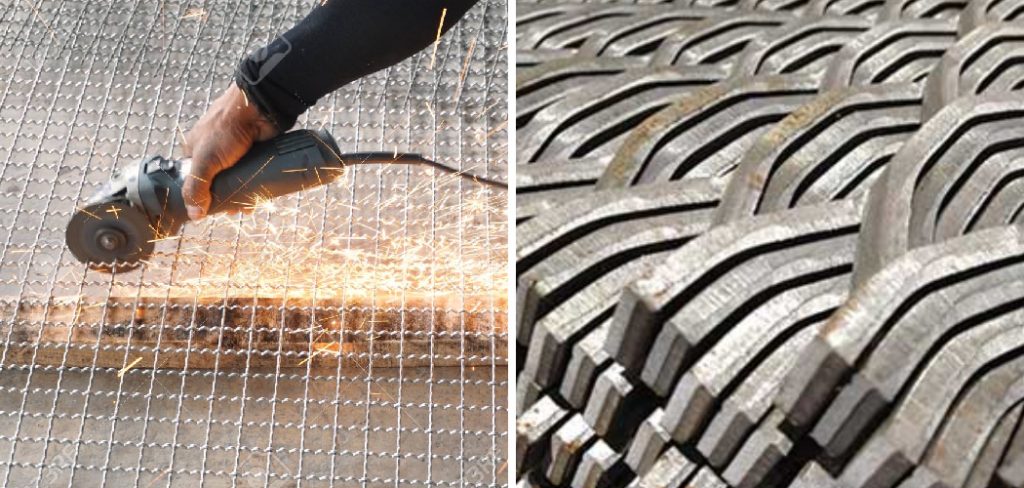
Expanded metal, characterized by its mesh-like structure, is frequently utilized in construction for reinforcement, ventilation grilles, and balustrades. In industrial contexts, it serves as durable flooring, walkways, and robust fencing.
DIY enthusiasts often employ expanded metal in creating custom furniture, shelving units, and decorative accents. Mastery in cutting this versatile material ensures that each project achieves a precision fit, enhancing both functionality and aesthetic appeal.
Accurate cutting eliminates material waste, reduces the risk of structural weaknesses, and ensures that the final product aligns perfectly with design specifications.
Understanding the best practices for cutting expanded metal not only optimizes the outcome but also contributes to the safety of the person performing the task. This guide will delve into the techniques and tools required to cut expanded metal efficiently and safely.
Understanding Expanded Metal
Types of Expanded Metal
Expanded metal comes in various materials, each offering unique benefits tailored to specific applications. The most common materials include steel, aluminum, and stainless steel. Steel is renowned for its strength and durability, making it ideal for heavy-duty industrial applications and construction projects.
Aluminum, being lighter and resistant to corrosion, is often preferred for applications where weight and environmental factors are critical, such as in marine or transport sectors. Stainless steel offers a balance of strength and corrosion resistance, making it suitable for both industrial and high-end architectural projects.
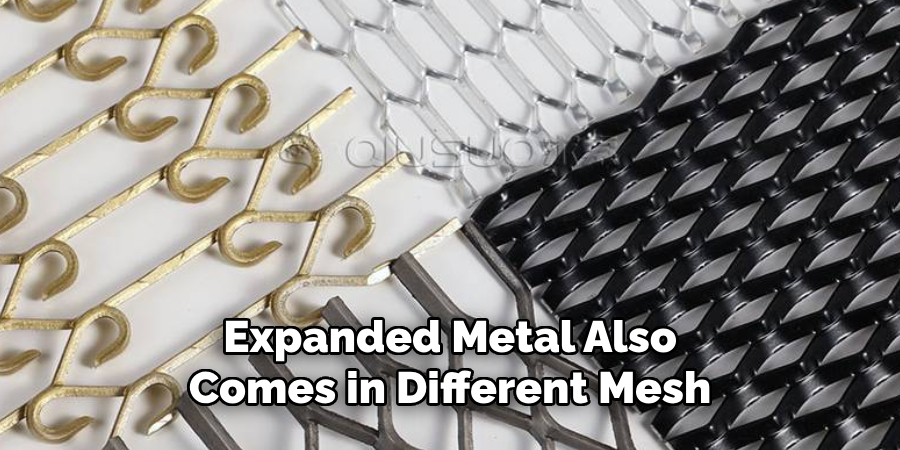
In addition to material variations, expanded metal also comes in different mesh patterns: standard (or raised) and flattened. Standard expanded metal has a raised surface, providing excellent grip and a three-dimensional appearance, which is particularly useful for walkways and ramps.
Flattened expanded metal, on the other hand, is rolled after expansion, resulting in a smooth, flat surface that is easier to handle and install, often used in applications requiring a more refined finish.
Applications of Expanded Metal
Expanded metal is incredibly versatile, finding applications across various industries due to its strength, durability, and customizability. In industrial settings, it is commonly used for flooring and walkways, providing a non-slip surface capable of withstanding heavy loads. Additionally, it is used in fencing, offering both security and visibility, making it ideal for perimeter enclosures and protective barriers.
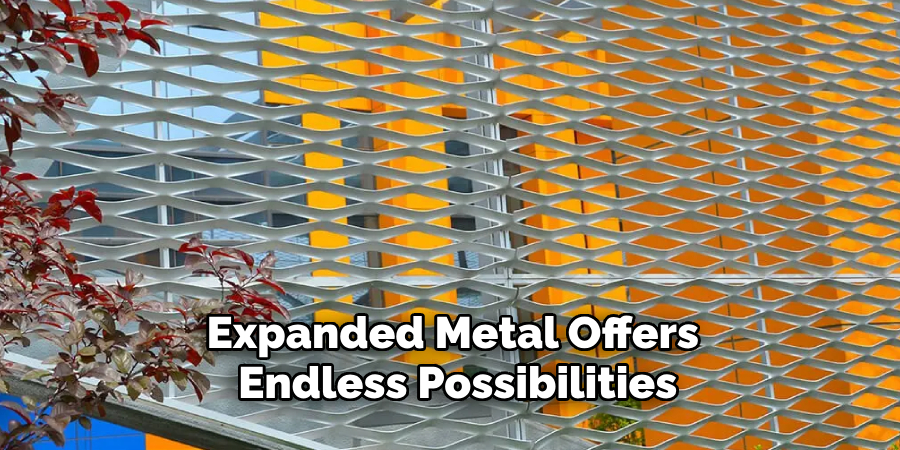
In construction, expanded metal serves as reinforcement in concrete structures, adding tensile strength and preventing cracking. It is also used in ventilation grilles and facades, promoting airflow while maintaining structural integrity. Furthermore, the decorative potential of expanded metal makes it a popular choice for architectural designs, such as modern balustrades and partitions.
Expanded metal offers endless possibilities for DIY enthusiasts. It can be used to create custom shelving units, unique pieces of furniture, or artistic decor elements. Its flexibility and affordability make it an excellent material for personal projects, allowing creativity to flourish while ensuring practicality and robustness.
Tools and Safety Equipment
Essential Tools
When it comes to cutting expanded metal, having the right tools can make all the difference in terms of precision and efficiency.
Tin Snips and Aviation Snips: These hand tools are excellent for cutting through thin sheets of expanded metal. Tin snips are similar to scissors and can handle light gauge metal, making them ideal for small-scale projects where detailed work is required.
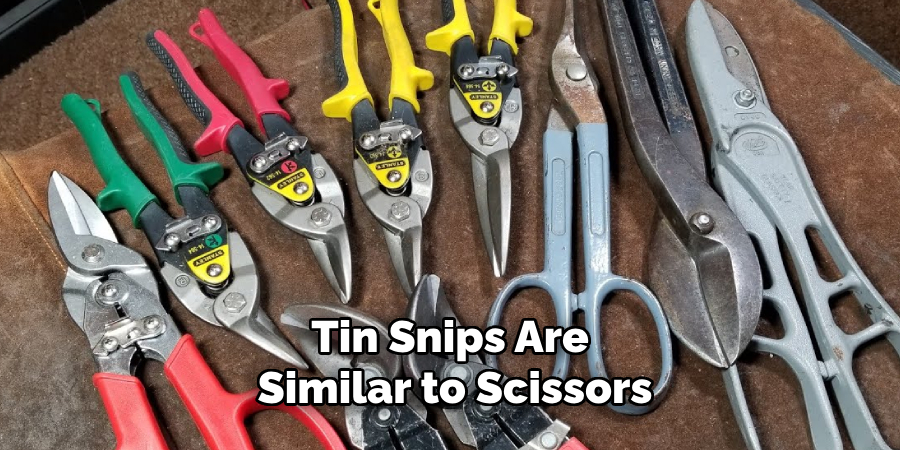
Aviation snips, also known as compound snips, offer greater leverage and are designed to cut through slightly thicker metals. They come in three types: left-cut, right-cut, and straight-cut, allowing for more complex and precise cuts.
Angle Grinder: An angle grinder fitted with an appropriate cutting disc can easily cut through thicker and more robust sheets of expanded metal. When choosing a cutting disc, it’s crucial to select one that is specifically designed for metal cutting to ensure clean cuts and prolong the life of the disc. An angle grinder can be particularly useful for larger projects where speed and power are essential.
Metal Shears: Metal shears come in both manual and power-operated versions, each with its advantages.
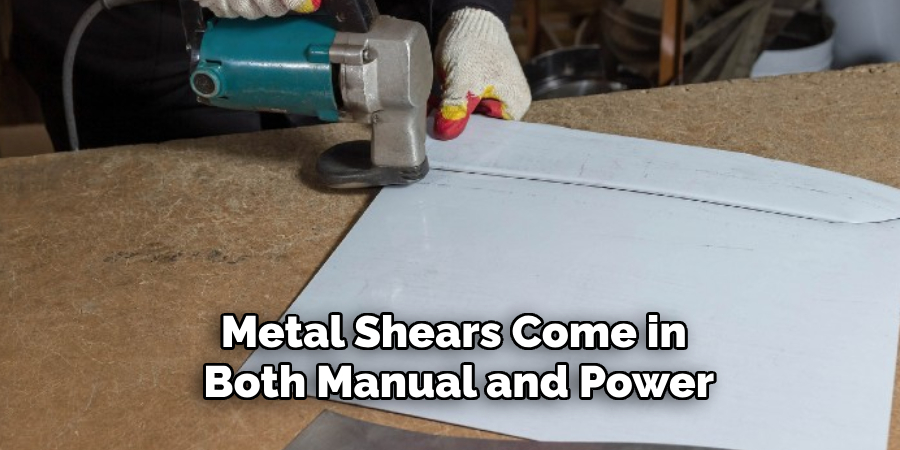
Manual shears are straightforward to use and provide great control for detailed cutting tasks. Power-operated shears, on the other hand, offer more power and can handle heavier gauge metals more efficiently. They are ideal for industrial applications where consistency and speed are required.
Hacksaw: A hacksaw equipped with the right blade can also be employed to cut expanded metal. When choosing a blade, it’s important to select one with fine teeth that are suitable for metal cutting. Hacksaws are particularly useful for making straight cuts in smaller sections or where power tools may not be practical.
By using these tools purposefully, you can achieve high-precision cuts that meet your project’s specifications and ensure an efficient workflow.
Safety Equipment
Safety should always be the top priority when cutting expanded metal. Here are some essential safety equipment items:
Protective Gloves: Wearing durable gloves protects your hands from sharp edges and flying debris. Leather or Kevlar gloves are good choices for providing both comfort and protection.
Safety Goggles: Eye protection is a must to shield your eyes from metal shards and sparks, especially when using power tools like angle grinders. Safety goggles or a face shield are highly recommended.
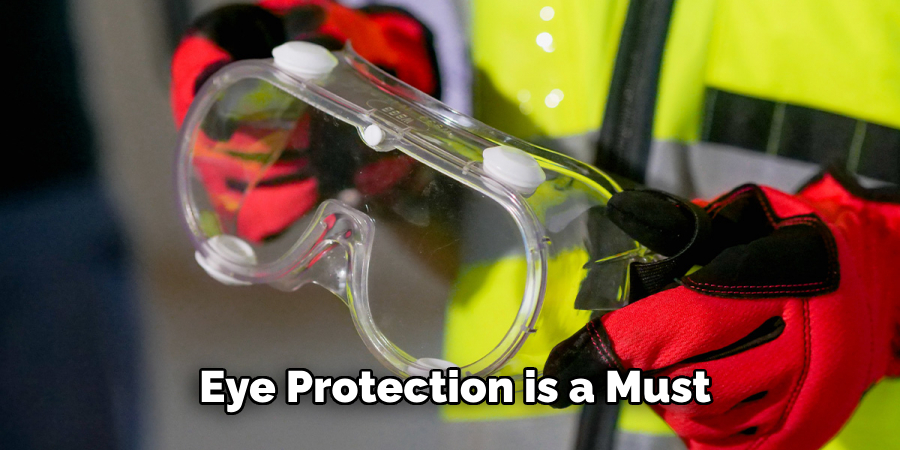
Ear Protection: Cutting metal can be noisy, particularly with power tools. Use earplugs or earmuffs to protect your hearing from prolonged exposure to loud noises.
Respirators: Certain cutting methods, such as using an angle grinder, can cause metal dust and particles to become airborne. A respirator helps to filter out these harmful particles, preventing them from being inhaled.
Having and using the appropriate safety equipment will help prevent accidents and injuries, making your cutting tasks safer and more efficient.
Preparation Steps
Measuring and Marking
Accurate measurements are crucial for ensuring the success of any project using expanded metal. Incorrect measurements can lead to wasted materials, increased costs, and ultimately, a flawed final product.
To achieve precise cuts, using reliable measuring tools such as a tape measure or ruler is essential. These tools allow you to determine the exact dimensions needed for your project, ensuring that each piece of expanded metal fits perfectly within your design specifications.
Once you have your measurements, marking the metal correctly is the next vital step. Chalk, markers, and scribes are commonly used for this purpose. Chalk and markers are particularly useful for making visible, easy-to-correct lines on the metal surface.
A scribe, on the other hand, provides a more permanent and fine line, which can be especially helpful for detailed work. By combining accurate measurements with clear markings, you can set the foundation for precise and effective cutting.
Securing the Metal
Securing the metal properly is essential for maintaining stability and safety during the cutting process.
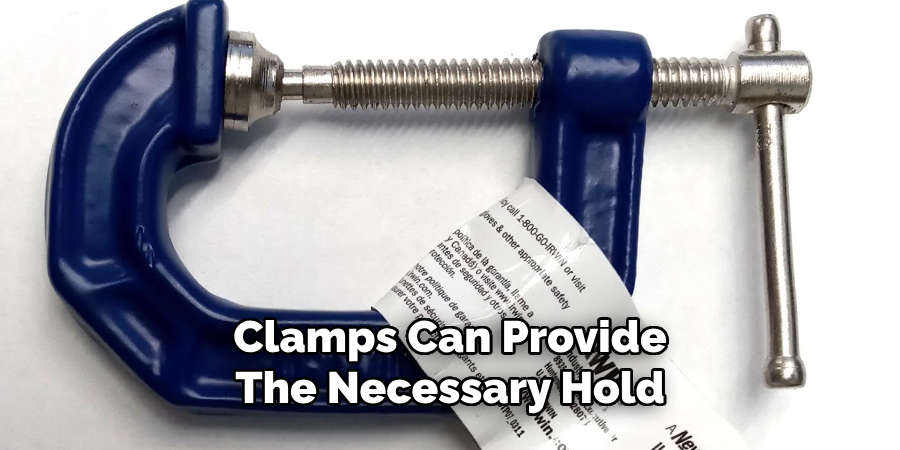
Using a vise or clamps can provide the necessary hold to keep the expanded metal in place, preventing any movement that could result in inaccurate cuts or accidents. A vise is particularly useful for smaller pieces, offering a strong, adjustable grip, while clamps can accommodate larger sheets and still provide a secure hold.
Setting up a stable and clean workspace is equally important. Ensure that your workbench is sturdy and that the surface is free from clutter and obstructions. This not only enhances your efficiency but also minimizes the risk of accidents.
Keep all tools and safety equipment within reach, and make sure the area is well-lit. By preparing your workspace and securely fastening the metal, you create a controlled environment that facilitates safe and precise cutting.
How to Cut Expanded Metal: Cutting Techniques
Using Tin Snips and Aviation Snips
Step-by-step instructions:
- Begin by wearing your protective gloves and safety goggles.
- Use a tape measure and marker to accurately measure and mark the cutting line on the expanded metal.
- Select the appropriate snips for your cut: straight-cut snips for straight lines, left- or right-cut snips for curved or angled cuts.
- Open the snips’ jaws and position them at the start of your marked line.
- Apply steady pressure to cut through the metal, closing the snips’ jaws completely with each cut.
- Continue cutting along your marked line, repositioning the snips as necessary to maintain accuracy.
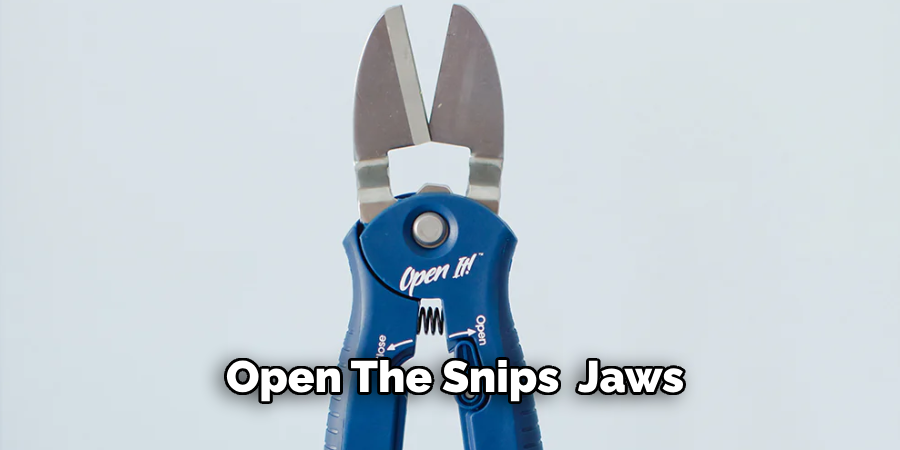
Tips for cutting straight lines and curves:
- For straight cuts, use straight-cut snips and ensure the metal is securely clamped to maintain stability.
- When cutting curves, it’s helpful to make small, incremental cuts with left- or right-cut snips, rotating the snips slightly with each cut to follow the curve accurately.
- To avoid jagged edges, make sure to cut smoothly and avoid rushing the process.
Cutting with an Angle Grinder
Disc selection and setup:
- Choose a cutting disc specifically designed for metal. Thin, abrasive discs work well for precision cuts.
- Securely attach the cutting disc to the angle grinder, following the manufacturer’s instructions.
- Ensure the metal is firmly clamped to your workbench to prevent movement during cutting.
Safety precautions and technique:
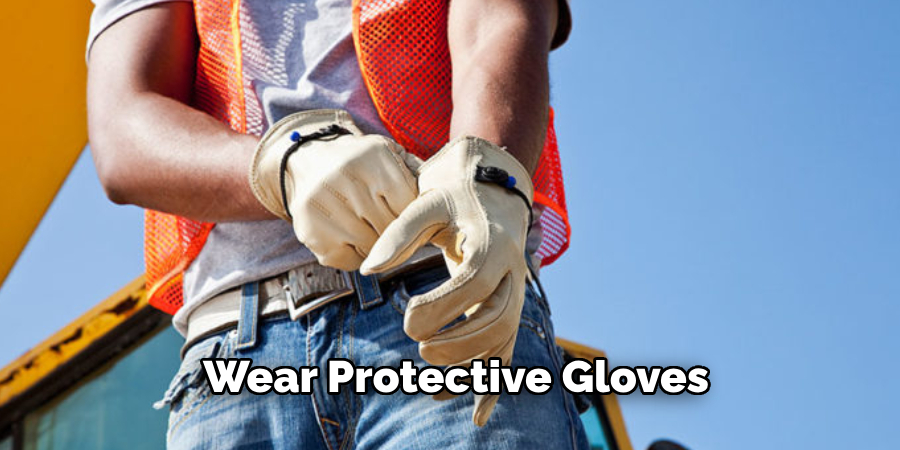
- Wear protective gloves, safety goggles, ear protection, and a respirator.
- Position the cutting disc at a right angle to the marked cutting line.
- Turn on the grinder and allow it to reach full speed before beginning the cut.
- Use a steady, controlled motion to guide the grinder along the marked line, applying light pressure to avoid overheating the disc.
- Regularly check your progress and make sure the cut is following the marked line accurately.
Using Metal Shears
Manual vs. electric shears:
Manual shears are ideal for smaller, detailed cutting tasks, providing excellent control and precision. Electric shears, on the other hand, are better suited for larger projects or thicker metals, offering more power and efficiency.
Techniques for different thicknesses of expanded metal:
- For thin, light gauge metal, manual shears can handle the task effortlessly. Keep the shears’ blades aligned with the marked line and make smooth, continuous cuts.
- Electric shears are preferable for thicker, heavier-gauge metal. Use a consistent, even motion to guide the shears along the cutting line.
- When cutting thicker metal, it may be beneficial to make a preliminary pass with the shears to score the metal before making the final cut. This technique can help ensure cleaner, more precise edges.
By selecting the right cutting technique and tools for your specific material and project requirements, you can achieve clean, accurate cuts that meet your design specifications.
How to Cut Expanded Metal: Advanced Cutting Methods
Using a Plasma Cutter
Overview of plasma cutters:
A plasma cutter is a versatile tool that uses a high-velocity jet of ionized gas (plasma) to cut through electrically conductive materials like expanded metal.
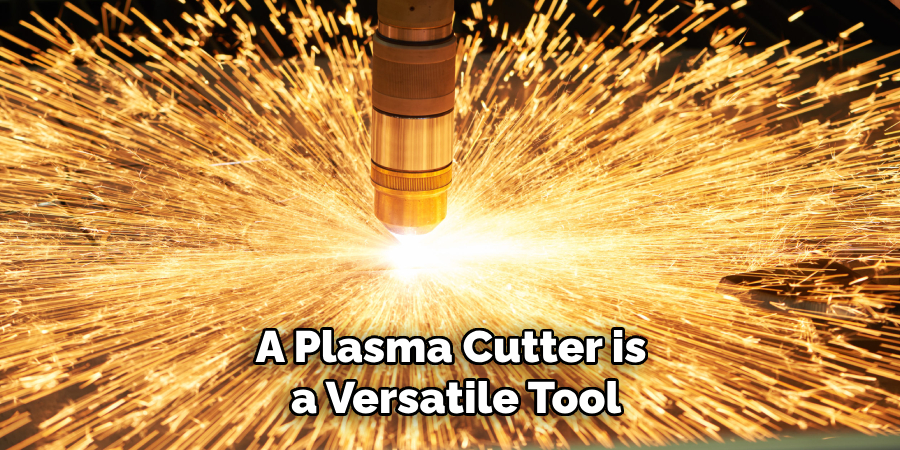
It operates by sending an electric arc through a gas that is blown through a focused nozzle, creating plasma. This plasma reaches extremely high temperatures and can cut through metal with precision and speed.
Pros and cons of using plasma cutters for expanded metal:
- Pros:
- Precision: Plasma cutters offer high levels of accuracy, making them ideal for intricate cuts.
- Speed: They can cut through metal quickly, significantly reducing project time.
- Versatility: Suitable for a wide range of materials and thicknesses.
- Cons:
- Cost: Plasma cutters can be expensive, both in initial investment and in consumables.
- Skill Required: Proper use requires training and practice.
- Safety Considerations: Plasma cutting generates sparks and fumes, necessitating robust safety precautions, including proper ventilation and protective equipment.
Using a Band Saw (150 words)
Overview of band saws for metal cutting:
A band saw is a power tool that employs a long, continuous band of toothed metal to cut through various materials. Metal-cutting band saws, equipped with appropriate blades, provide a smooth and efficient cutting experience for cutting expanded metal.
These saws are known for their ability to make precise, straight cuts and curves, depending on the blade and technique used.
Tips for cutting expanded metal with a band saw:
- Blade Selection: Use a bi-metal blade with fine teeth specifically designed for metal cutting to ensure clean cuts.
- Speed and Feed Rate: Adjust the band saws speed and feed rate according to the thickness and type of expanded metal to avoid blade damage and ensure accuracy.
- Secure the Material: Securely clamp the expanded metal to the workbench or saw table to prevent movement during the cutting process.
- Cooling and Lubrication: Apply cutting lubricant to the blade to reduce friction and heat, extending the blade’s life and improving the cut quality.
By following these tips, you can achieve precise cuts with minimal waste using a band saw.
Troubleshooting Common Issues
Dealing with Jagged Edges
Causes of jagged edges:
Jagged edges often occur due to improper cutting techniques or using dull tools. Inconsistent pressure, rapid cutting motions, and not following the marked line precisely can also contribute to uneven edges. Additionally, cutting thicker or harder metals with inadequate tools may result in rough finishes.
Techniques to smooth and finish edges:
To smooth jagged edges, use a metal file or a deburring tool along the cut edge, applying steady, even strokes. For larger projects, an angle grinder with a flap disc or a sanding drum attachment can be more efficient.
Make sure to work slowly and check your progress frequently to avoid removing too much material. Sandpaper can also be used for finer smoothing. Applying a metal sealant or paint can provide a finished look and prevent rust on the smoothed edges.
Preventing Warping and Distortion
Causes of warping:
Warping and distortion are typically caused by excessive heat generated during the cutting process, uneven pressure, or improper clamping of the material. Thinner metals are more susceptible to warping due to their reduced structural integrity when exposed to high temperatures or uneven forces.
Methods to avoid and correct distortion during cutting:
To prevent warping, use a cutting method that minimizes heat build-up, such as a cold saw or shears. Applying consistent, light pressure during cutting and ensuring the material is securely clamped can also help maintain its shape. If using a method that generates heat, like plasma cutting, pause periodically to allow the metal to cool.
If distortion occurs, gently bend the metal back into shape using a hammer and a flat surface, taking care not to damage the metal further. For more severe cases, a heat gun can be used to evenly heat the warped area before applying corrective pressure.
Finishing Touches
Smoothing Edges
Tools for deburring:
To achieve smooth edges on expanded metal, you can use various tools such as metal files, sandpaper, and rotary tools equipped with deburring attachments. Metal files are excellent for manual deburring and allow for precise control over the smoothing process. Sandpaper in various grits can be used to gradually refine the edges, starting with coarse grit and finishing with finer grits for a polished look.
Rotary tools, such as Dremel, with deburring or sanding attachments can speed up the process and are particularly useful for detailed work and hard-to-reach areas.
Techniques for achieving smooth edges:
Start by securing the metal piece to prevent movement. Run the file along the cut edge in one direction, using steady, even strokes, until the edge is smooth. For a finer finish, use sandpaper starting with a coarse grit and progressively moving to finer grits.
When using a rotary tool, hold it at a slight angle to the edge and move it in a consistent, sweeping motion. Regularly check your progress to ensure even smoothing and avoid overworking the metal.
Protecting and Coating
Importance of corrosion protection:
Protecting the finished edges of expanded metal from corrosion is crucial for extending its lifespan and maintaining its integrity.
Unprotected metal is prone to rust and degradation, especially when exposed to moisture and varying weather conditions. Adding a protective coating not only enhances the metal’s durability but also improves its appearance.
Coating methods:
Several methods can be used to coat and protect the expanded metal. Painting is a commonly used technique that provides a layer of protection while allowing for color customization. Powder coating involves applying a dry powder to the metal and curing it in an oven, resulting in a durable, high-quality finish.
Galvanizing is another effective method involving the application of a zinc coating to protect the metal from corrosion. Each of these methods offers a different level of protection and aesthetics, making them suitable for various applications and environments.
Safety Precautions
General Safety Tips
Importance of a safety-first approach:
Prioritizing safety at all times can significantly reduce the risk of accidents and injuries. A safety-first approach means being conscientious of potential hazards, preparing accordingly, and utilizing proper safety gear and techniques. This proactive mindset not only protects you but also those around you in the workplace or DIY projects.
Common hazards and how to avoid them:
Working with metal cutting tools involves inherent risks such as cuts, burns, and flying debris. To mitigate these dangers, always wear appropriate personal protective equipment (PPE) including gloves, safety goggles, and long sleeves.
Ensure your workspace is well-lit and free of clutter to prevent tripping hazards. Use tools that are in good condition and follow manufacturer guidelines for operation. Moreover, avoid distractions and take regular breaks to maintain focus and prevent fatigue-related errors.
Emergency Procedures
First aid for minor injuries:
In the event of a minor injury, such as a small cut or abrasion, promptly clean the wound with antiseptic to prevent infection and cover it with a sterile bandage.
For minor burns, cool the area under running water for at least 10 minutes and apply a burn ointment or aloe vera gel. Always keep a well-stocked first aid kit nearby when working with metal cutting tools.
Steps to take in case of serious accidents:
For more serious accidents, like deep cuts, severe burns, or significant eye injuries, immediate action is crucial. Call emergency services without delay and stay on the line for further instructions. While waiting for medical help, apply pressure to any bleeding wounds with a clean cloth to control blood loss.
If possible, move the injured person to a safe area away from potential hazards without causing further injury. Ensure that emergency contact information and procedures are easily accessible and known to all individuals in the workspace.
Conclusion
In conclusion, mastering the techniques for how to cut expanded metal effectively and safely is crucial for achieving precise results and maintaining the structural integrity of the material.
Key points covered in this article include methods to prevent and correct distortion during cutting, ensuring smooth edges using deburring tools and techniques, and the significance of applying protective coatings to prevent corrosion.
Emphasizing a safety-first approach is essential to mitigate risks associated with metal cutting, including wearing appropriate PPE and maintaining an organized workspace.
By understanding and implementing these practices, readers can confidently improve their cutting skills and achieve high-quality finishes. Continuously practicing and refining your techniques will lead to greater proficiency and satisfaction in your metalworking projects.
Edmund Sumlin is a skilled author for Metal Fixes, bringing 6 years of expertise in crafting a wide range of metal fixtures. With a strong background in metalwork, Edmund’s knowledge spans various types of fixtures, from decorative pieces to functional hardware, blending precision with creativity. His passion for metalworking and design has made him a trusted resource in the industry.
Professional Focus:
- Expert in Metal Fixtures : Edmund aesthetic specializes in creating durable and innovative metal fixtures, offering both appeal and functionality. His work reflects a deep understanding of metalworking techniques and materials.
- Sustainability Advocate : He is dedicated to using sustainable practices, ensuring that every fixture is crafted with eco-friendly methods while maintaining high-quality standards.
In his writing for Metal Fixes, Edmund provides valuable insights into the latest trends, techniques, and practical advice for those passionate about metal fixtures, whether they are professionals or DIY enthusiasts. His focus on combining artistry with engineering helps others discover the true potential of metal in design.