Cutting iron balusters is a crucial step in many home renovation and design projects, particularly those involving staircases and railings.
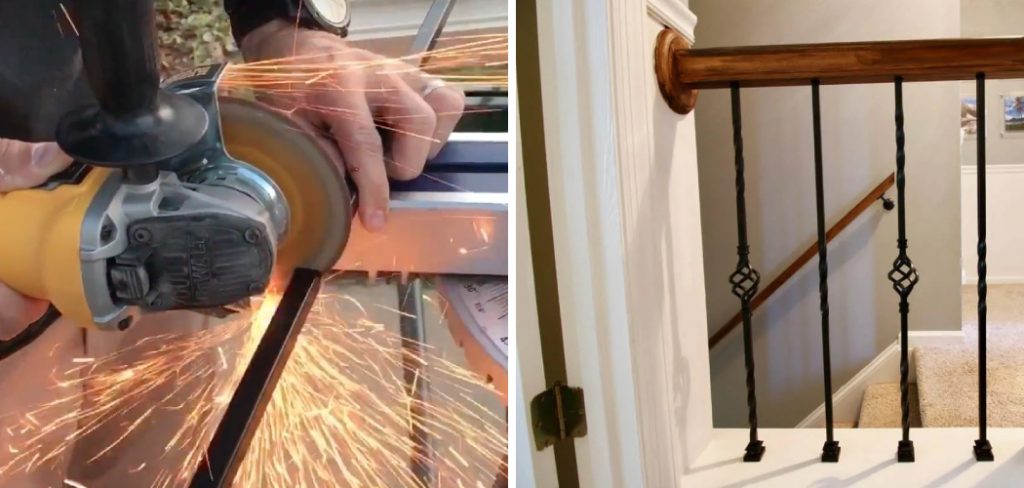
Iron balusters, known for their durability and aesthetic appeal, are commonly used in stair railings to provide support and add a decorative touch.
They come in various designs, including plain, twisted, basket, and scroll patterns, which can enhance the visual appeal of both modern and traditional homes.
Accurate cutting of iron balusters is essential to ensure they fit properly and contribute to a polished, professional appearance. Missteps in measurement or cutting can lead to fitting issues, compromising both the safety and beauty of the installation.
This guide on how to cut iron balusters will walk you through the essential steps and techniques to achieve precise cuts, ensuring your project results in a secure and visually pleasing outcome.
Understanding Iron Balusters
Types of Iron Balusters
Iron balusters are primarily crafted from two types of materials: wrought iron and cast iron. Wrought iron balusters are known for their malleability and strength, allowing for intricate and detailed designs. They are typically forged and shaped by hand, resulting in unique and customizable pieces.
Cast iron balusters, on the other hand, are created by pouring molten iron into molds. This process makes them more brittle compared to wrought iron but allows for the mass production of intricate shapes and patterns.
In terms of design variations, iron balusters come in several styles to suit various aesthetic preferences. The most basic type is the plain baluster, which offers a clean and simple look. Twisted balusters feature a helical design that adds a touch of elegance and complexity.
Basket balusters incorporate decorative elements that resemble woven baskets, adding texture and visual interest. Scroll balusters are adorned with ornate scrolling patterns, perfect for adding a classic or elaborate flair to any installation.
Applications of Iron Balusters
Iron balusters are versatile components used in various architectural applications, primarily for their structural support and aesthetic appeal.
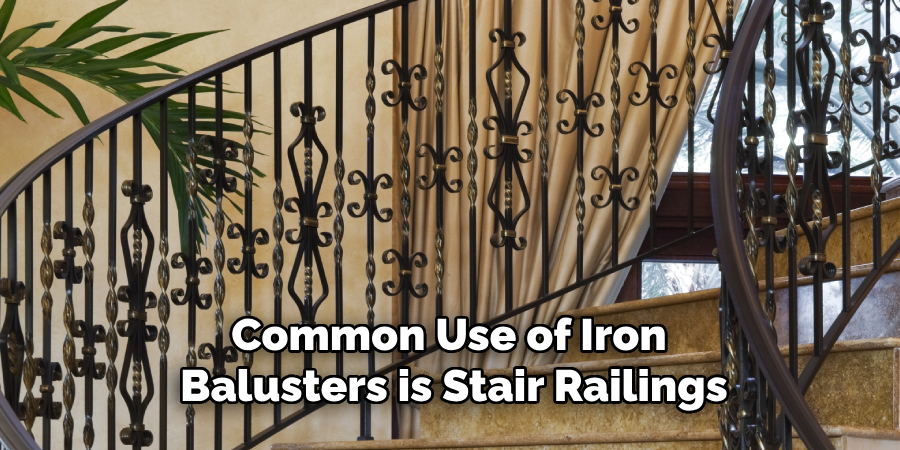
Perhaps the most common use of iron balusters is stair railings, which provide stability and enhance the visual impact of both indoor and outdoor staircases. Whether in a grand staircase or a simple basement stair, iron balusters can elevate the design from bland to extraordinary.
Another popular application of iron balusters is in balcony railings. They provide safety by preventing falls while also contributing to the architectural beauty of the building. With the right design, balcony railings fitted with iron balusters can become focal points that exude sophistication and charm.
Decorative fencing is yet another area where iron balusters shine. They combine functionality with ornamental design in garden fencing or perimeter fencing around a property. This makes them an excellent choice for homeowners looking to make a strong and stylish statement with their exterior spaces.
Tools and Safety Equipment
Essential Tools
Hacksaw: Blade Selection and Usage
A hacksaw is a handy tool for cutting iron balusters, especially for DIY enthusiasts. Selecting the right blade is crucial to achieving clean cuts. Blades with 18 to 32 teeth per inch (TPI) work well for cutting metal; a higher TPI count provides a smoother finish but can be cut more slowly.
When using a hacksaw, ensure the blade is tightly secured and the frame is robust. Maintain a steady, controlled motion to avoid jagged edges, and periodically apply cutting oil to reduce friction and enhance blade life.
Angle Grinder: Disc Types and Proper Handling
An angle grinder is another versatile tool for cutting iron balusters. The key to effective use lies in choosing the right disc type. Thin cutting discs, typically 1-2 mm, are ideal for precision work.
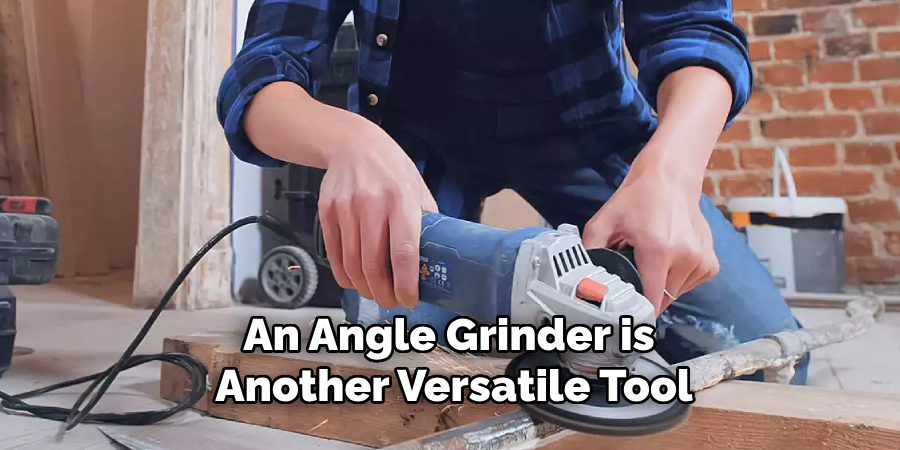
Ensure the disc is specifically rated for cutting metal. When handling an angle grinder, always use both hands to maintain control and keep the tool’s guard in place to protect yourself from sparks and debris.
Avoid pressing too hard; let the disc do the work to prevent overheating and disc damage.
Chop Saw with Metal Cutting Blade
For those tackling larger projects, a chop saw equipped with a metal cutting blade offers rapid and precise cuts. Choose a blade designed for ferrous metals, which will be robust enough to handle the hardness of iron balusters.
Setting up the chop saw correctly is essential; adjust the blade depth and angle to ensure accurate cuts. Secure the baluster firmly before cutting to prevent movement, and proceed with a steady, uniform motion through the material.
Reciprocating Saw: Blade Options and Techniques
A reciprocating saw, or Sawzall is highly effective for cutting iron balusters in tight or awkward spaces. Blade selection is critical; use bi-metal blades with a TPI suitable for metal cutting, generally between 10-14 TPI.
For best results, mark the cut line and clamp the baluster securely. Start the saw at a low speed to establish the cut, then increase the speed gradually. Employ a slight back-and-forth motion to assist the blade in cutting through the iron efficiently.
Safety Equipment
Protective Gloves
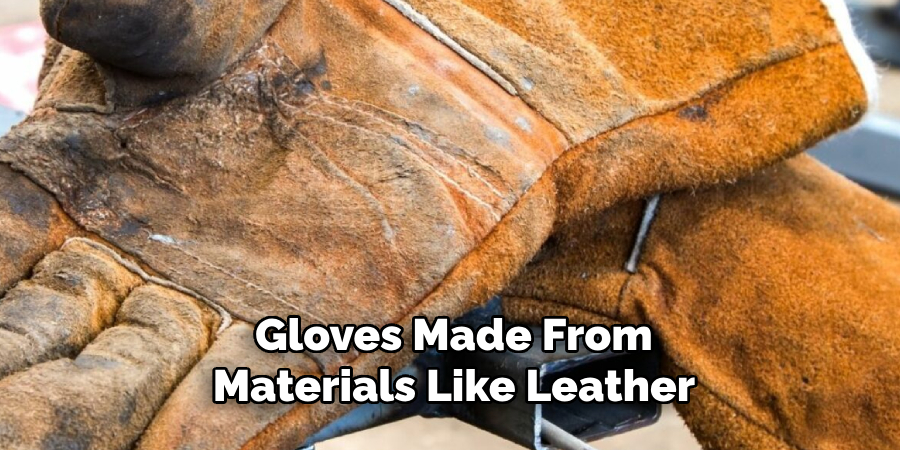
Protective gloves are essential when cutting iron balusters to prevent cuts and abrasions. Choose heavy-duty work gloves made from materials like leather or reinforced fabric, which offer both dexterity and protection.
Safety Goggles
Safety goggles are a must to shield your eyes from metal shards and dust generated during the cutting process. Ensure the goggles fit snugly and are rated for impact resistance.
Ear Protection
Cutting iron balusters can be noisy, particularly with power tools like angle grinders and chop saws. Use earplugs or earmuffs to protect your hearing from prolonged exposure to loud noise.
Respirators
For specific cutting methods, such as using an angle grinder, respirators are recommended to protect your lungs from fine metal particles and dust. Choose a respirator rated for dust and metal fumes, and ensure it fits securely to provide effective protection.
Preparation Steps
Measuring and Marking
Accurate measurements are paramount when working with iron balusters to ensure a precise fit and professional finish. Incorrect measurements can lead to wasted materials and time and can compromise the structural integrity of the installation.
To achieve precise measurements, use reliable tools such as a tape measure or a metal ruler. These tools provide the accuracy needed for detailed work.
Marking the iron balusters correctly is equally important. Use a piece of chalk or a permanent marker to draw your cut lines clearly. Chalk is a preferred choice for temporary markings, while a permanent marker is ideal for more durable and visible lines.
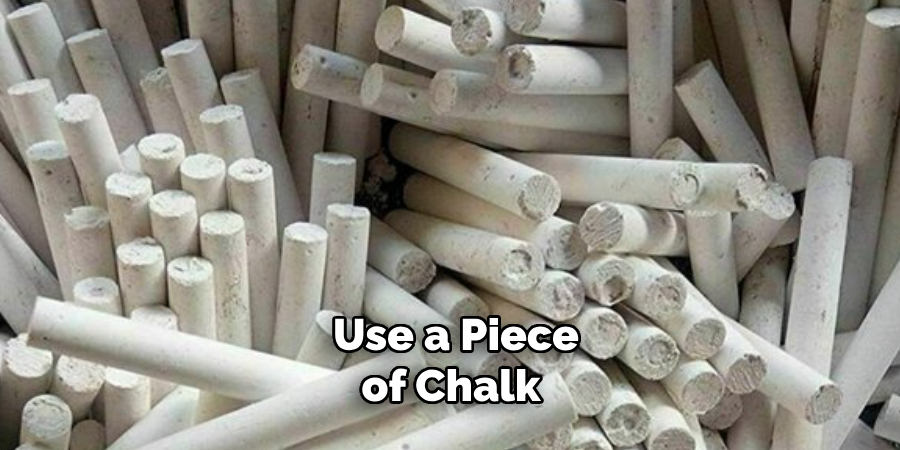
Make sure to double-check measurements before marking to avoid any errors. Having well-defined measurement and marking processes ensures a smooth cutting and installation phase, reducing the margin for mistakes and improving overall efficiency.
Securing the Baluster
Stabilizing the iron baluster is crucial for safe and accurate cutting. Using a vise is a highly recommended method for securing balusters, providing a strong and steady hold that minimizes movement and reduces the risk of accidents.
Position the baluster securely in the vise before making any cuts to prevent any slippage during the process.
If a vise is not available, there are several alternative methods to secure the baluster. Clamps are versatile and can be used to fasten the baluster to a sturdy workbench or table. Another option is to use sawhorses, placing the baluster across them and clamping it down for stability.
Regardless of the method chosen, ensuring the baluster is firmly held in place is essential for achieving clean cuts and preventing injuries. Proper stabilization techniques contribute to the safety and precision of your project.
How to Cut Iron Balusters: Cutting Techniques
Using a Hacksaw
Step-by-step Instructions
- Select a blade with 18-32 teeth per inch (TPI).
- Secure the iron baluster firmly using a vise or clamps.
- Mark the cutting line with chalk or a permanent marker.
- Place the hacksaw blade against the marked line, ensuring it is tightly secured in the frame.
- Begin sawing with steady, controlled strokes, applying minimal pressure.
- Maintain a consistent rhythm to achieve a smooth cut.
Tips for Maintaining a Straight Cut
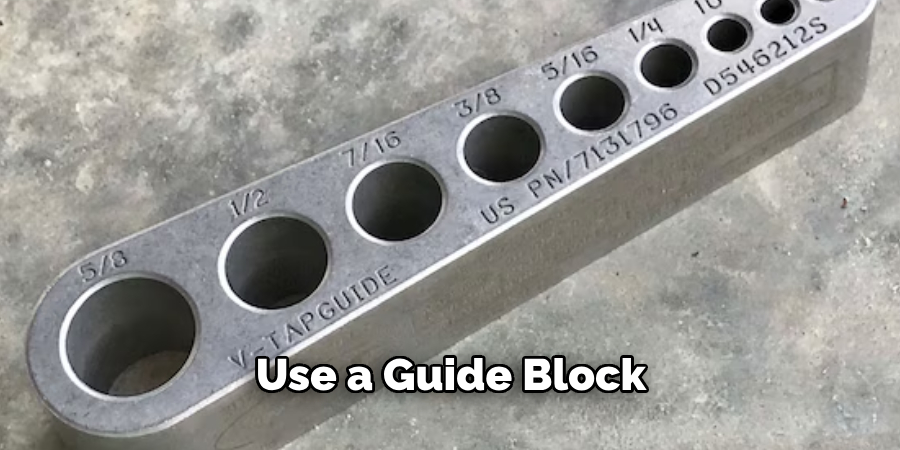
- Ensure the blade is perpendicular to the surface of the baluster at all times.
- Use a guide block or an angle jig to steer the blade straight.
- Keep the cutting surface clean and lubricate the blade periodically with cutting oil to reduce friction and enhance performance.
Cutting with an Angle Grinder
Disc Selection and Setup
- Choose a thin cutting disc, 1-2 mm thick, specifically rated for metal cutting.
- Attach the disc securely to the angle grinder and ensure the tool’s guard is in place.
Safety Precautions and Techniques
- Wear safety goggles, ear protection, gloves, and a respirator.
- Secure the iron baluster with a vise or clamps.
- Position the grinder so that the cutting disc aligns with the marked line.
- Hold the grinder firmly with both hands and switch it on.
- Let the tool reach full speed before beginning the cut.
- Use a steady, controlled motion, letting the weight of the grinder do the work.
- Avoid applying excessive pressure to prevent overheating and disc damage.
Using a Chop Saw
Blade Selection and Setup
- Choose a metal cutting blade designed for ferrous materials.
- Install the blade securely in the chop saw, ensuring it is properly aligned.
- Adjust the blade depth and angle according to your cutting requirements.
Step-by-step Instructions and Tips
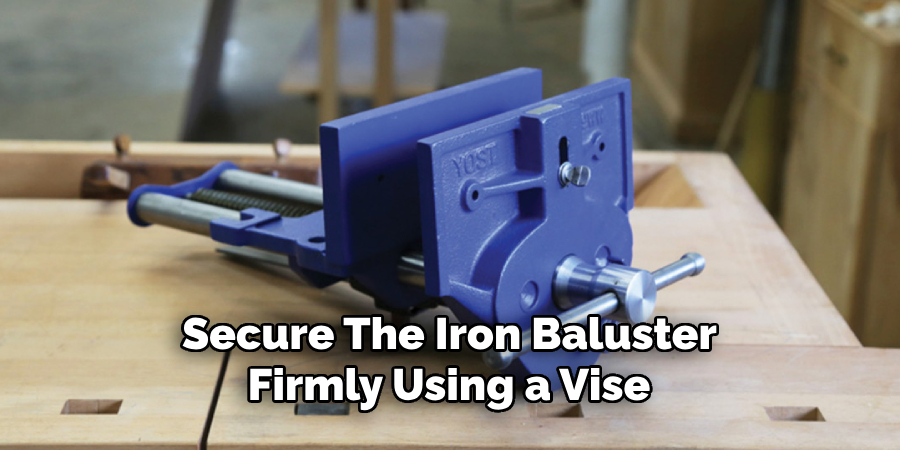
- Secure the iron baluster firmly using a vise or clamps.
- Mark the cutting line with chalk or a permanent marker.
- Align the saw blade with the marked line, ensuring the baluster is properly positioned.
- Turn on the chop saw and allow it to reach full speed.
- Lower the blade slowly and steadily through the baluster.
- Maintain a consistent feed rate without forcing the blade, allowing it to cut through the material efficiently.
- Lift the saw blade back up before turning off the tool to complete the cut safely.
How to Cut Iron Balusters: Advanced Cutting Methods
Using a Reciprocating Saw
Blade Selection and Setup
- Select a bi-metal blade with 14-18 teeth per inch (TPI), ideal for cutting iron balusters.
- Ensure the blade is securely fastened to the saw and that the saw boot is adjusted to provide the best balance and control.
- Adjust the saw’s speed setting to match the type of metal you are cutting; lower speeds reduce premature blade wear and overheating.
Techniques for Different Types of Iron Balusters
- Solid Iron Balusters:
For solid iron balusters, use a slower, controlled cutting motion to avoid overheating the blade and damaging the baluster.
- Hollow Iron Balusters:
Faster strokes can be applied when cutting hollow iron balusters, but be cautious of thin sections that may buckle. To maintain its shape, it is advisable to support the baluster from within using a wooden dowel.
- Decorative Iron Balusters:
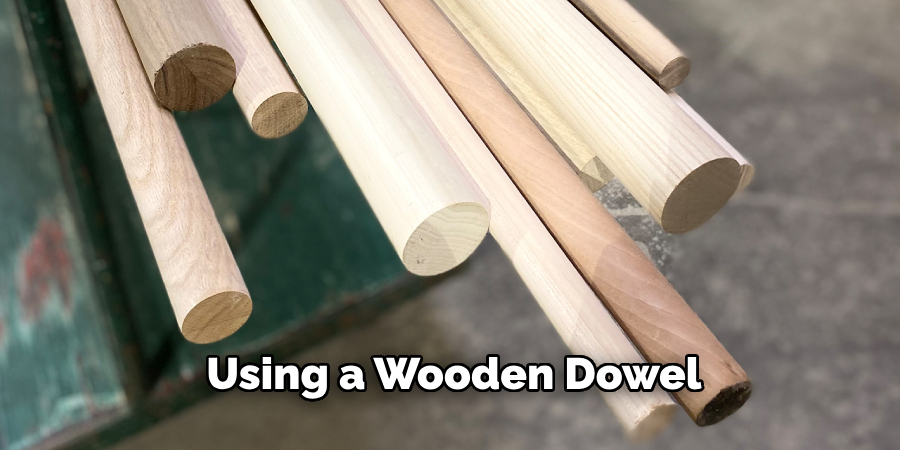
Handle intricate designs with care, using short, precise strokes. Extra attention is required to avoid damaging decorative elements.
Using a Bandsaw
Overview of Bandsaws for Cutting Metal
Bandsaws are highly effective tools for cutting iron balusters due to their continuous blade, which provides a smooth and consistent cut. They come in various sizes, with portable models available for smaller projects and larger, stationary units suitable for workshop setups.
Pros and Cons of Cutting Iron Balusters
Pros:
- Precision: Bandsaws offer high precision, making them ideal for detailed and decorative cuts.
- Smooth Cuts: The continuous blade reduces the chance of jagged edges, resulting in a cleaner finish.
- Versatility: Bandsaws can handle a range of metal thicknesses and shapes.
Cons:
- Cost: Bandsaws can be expensive, both in initial outlay and ongoing maintenance.
- Setup Time: Proper adjustment and calibration of the bandsaw are necessary, which can be time-consuming.
- Space Requirement: Stationary bandsaws require significant space, which may not be ideal for smaller workshops or job sites.
Troubleshooting Common Issues
Dealing with Jagged Edges
Causes of Jagged Edges
Jagged edges often occur when cutting iron balusters due to several factors. These include using a dull or inappropriate blade, applying excessive force during the cut, or operating the cutting tool at an incorrect speed.
Inconsistent pressure and improper stabilization of the baluster can also contribute to uneven, rough edges.
Techniques to Smooth and Finish Edges
To achieve a smooth and polished finish, begin by using a file or a metal deburring tool to remove any rough spots and burrs. For a finer finish, utilize sandpaper or a sanding disc attached to a rotary tool, progressively working from coarse to fine grit.
Applying a light coat of cutting oil during this process can enhance the smoothing action and prevent overheating. Finally, clean the edges with a soft cloth to remove any residual metal particles and oil, ensuring a professional appearance.
Preventing Warping and Distortion
Causes of Warping
Warping and distortion are common issues that occur when cutting iron balusters, often caused by excessive heat buildup during the cutting process.
Long or thin sections of the baluster are particularly susceptible. Uneven pressure and inadequate stabilization can exacerbate these problems, leading to undesirable bends or twists in the metal.
Methods to Avoid and Correct Distortion During Cutting
To prevent warping, use sharp blades and high-quality cutting discs appropriate for metal. Maintain a steady, controlled cutting speed and avoid overexerting pressure on the tool. Keeping the baluster securely clamped throughout the cutting process is crucial for maintaining its shape.
To minimize heat buildup, pause periodically to allow the metal to cool or use a cooling lubricant. If distortion does occur, gently hammer the baluster back into shape on an anvil or sturdy surface, or use a vise to slowly bend it back into the correct alignment.
Finishing Touches
Smoothing Edges
Tools for Deburring: Files, Sandpaper, Rotary Tools
To achieve professional and smooth edges on iron balusters, deburring tools are essential. Files come in various shapes and sizes, allowing you to address different contours and hard-to-reach spots on the baluster.
Sandpaper, available in a range of grits, is useful for progressively refining the edge from rough to smooth. Rotary tools equipped with sanding discs or burr bits provide an efficient means to handle intricate designs and detailed work.
Techniques for Achieving Smooth Edges
Begin the smoothing process by filing down any prominent burrs or rough spots along the cut edge of the baluster.
Use a flat or half-round file, depending on the shape of the edge, applying gentle pressure to avoid removing too much material. Next, wrap sandpaper around a block or use a sanding disc on a rotary tool to further smooth the edges.
Start with medium-grit sandpaper (e.g., 120-grit) and gradually move to finer grits (e.g., 220-grit) for a polished finish.
Ensure to sand evenly along the length of the edge to maintain a consistent profile. Rotate the baluster occasionally during the process to check for uniformity and make adjustments as needed.
Conclusion
Throughout this guide, we have covered essential techniques on how to cut iron balusters, including the importance of selecting the right cutting tools, maintaining control during the cutting process, and applying finishing touches for a professional result. Proper technique not only ensures precision but also prolongs the lifespan of your tools and materials.
We also highlighted the critical role of safety precautions, such as the use of personal protective equipment and maintaining a clean, organized workspace, to prevent accidents. Mastery in cutting, smoothing, and coating iron balusters comes with practice and dedication.
By following these guidelines and continually honing your skills, you can achieve high-quality results that enhance the aesthetic and structural integrity of your projects. Always prioritize safety and proper technique as you advance your craftsmanship in the art of cutting iron balusters.
Edmund Sumlin is a skilled author for Metal Fixes, bringing 6 years of expertise in crafting a wide range of metal fixtures. With a strong background in metalwork, Edmund’s knowledge spans various types of fixtures, from decorative pieces to functional hardware, blending precision with creativity. His passion for metalworking and design has made him a trusted resource in the industry.
Professional Focus:
- Expert in Metal Fixtures : Edmund aesthetic specializes in creating durable and innovative metal fixtures, offering both appeal and functionality. His work reflects a deep understanding of metalworking techniques and materials.
- Sustainability Advocate : He is dedicated to using sustainable practices, ensuring that every fixture is crafted with eco-friendly methods while maintaining high-quality standards.
In his writing for Metal Fixes, Edmund provides valuable insights into the latest trends, techniques, and practical advice for those passionate about metal fixtures, whether they are professionals or DIY enthusiasts. His focus on combining artistry with engineering helps others discover the true potential of metal in design.