Cutting metal mesh is an essential skill in various fields, ranging from industrial to residential and commercial applications.
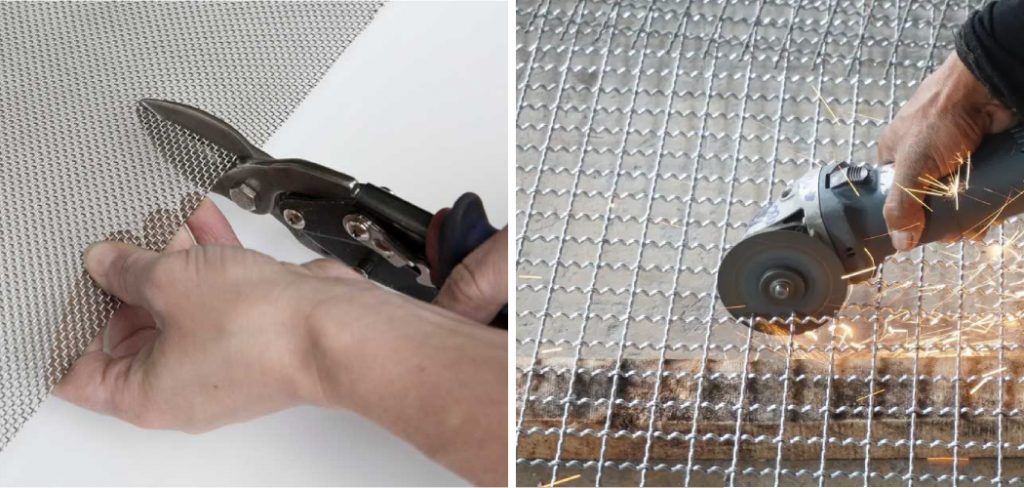
Metal mesh, known for its versatility and durability, is commonly used for filtration, reinforcement in construction, fencing, decorative elements, shelving, and partitions.
The ability to properly cut metal mesh ensures that these applications are achieved with precision and safety.
Learning how to cut metal mesh correctly not only enhances the quality of the final product but also prevents potential hazards associated with improper cutting techniques.
This guide will provide valuable insights on how to cut metal mesh efficiently and safely, ensuring that both professionals and DIY enthusiasts can accomplish their projects successfully.
Understanding Metal Mesh
Types of Metal Mesh
Metal mesh comes in various types, each serving different functions and applications. The three primary types are wire mesh, expanded metal mesh, and perforated metal mesh. Wire mesh is composed of intersecting wires that can form various patterns, such as square or diamond shapes.
It’s often used for lightweight applications due to its flexibility and ease of handling. Expanded metal mesh is a single sheet of metal that has been cut and stretched to create a mesh-like pattern. This type is known for its strength and rigidity, making it suitable for heavy-duty applications.
Perforated metal mesh features an array of holes punched through a solid sheet of metal, which can vary in size, shape, and pattern. This type is commonly used for filtration and screening purposes.
When it comes to material variations, metal mesh can be made from steel, aluminum, or stainless steel. Steel mesh is known for its strength and affordability but can be prone to rust without proper coating.
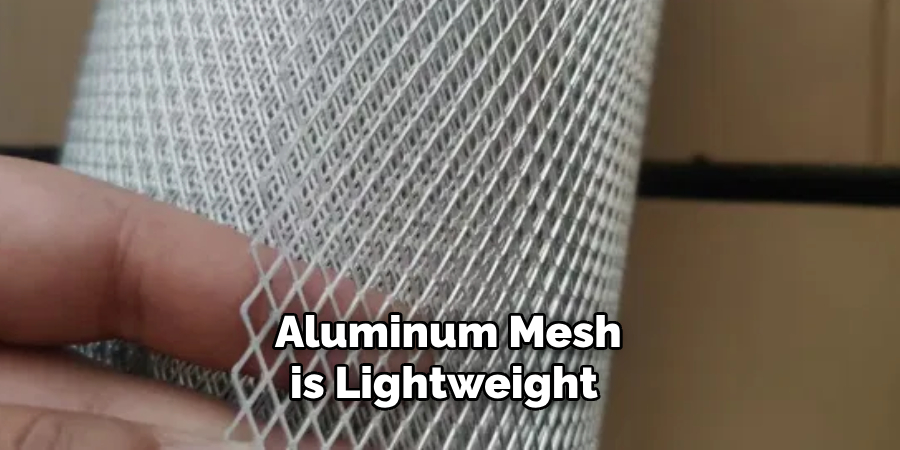
Aluminum mesh is lightweight and resistant to corrosion, making it ideal for outdoor and marine applications. Stainless steel mesh combines the strength of steel with excellent resistance to corrosion, making it a versatile choice for both indoor and outdoor uses.
Applications of Metal Mesh
Metal mesh is highly versatile and finds applications across various sectors. In industrial settings, metal mesh is commonly used for filtration and reinforcement. For instance, wire mesh can act as a filter to separate particles in liquids or gases, while expanded metal mesh often provides structural support in construction projects.
In residential applications, metal mesh serves as fencing and decorative elements. Homeowners often use wire mesh to create secure boundaries around their property or gardens.
Additionally, perforated metal mesh can be used in modern architectural designs to add aesthetic appeal to homes.
Within commercial environments, metal mesh proves useful for shelving and partitions. Businesses often utilize expanded or wire mesh for durable and ventilated storage solutions. Similarly, perforated metal mesh can create stylish yet functional partitions in offices or retail spaces, providing both privacy and an open feel.
Tools and Safety Equipment
Essential Tools
When it comes to cutting metal mesh, having the right tools is crucial to achieving precise and clean cuts. Here’s a breakdown of the essential tools you’ll need:
- Tin Snips and Aviation Snips: Tin snips, also known as tinner’s snips, are versatile hand tools designed for cutting sheet metal and thin metal mesh. They are ideal for making straight cuts but can also handle slight curves. Aviation snips, on the other hand, are more robust and are available in three types: left-cut, right-cut, and straight-cut. Each type is designed for different cutting directions, making them invaluable for more intricate cutting tasks. Aviation snips feature compound leverage, which allows for easier cutting with less effort.
- Angle Grinders: Angle grinders are powerful tools that can handle thicker and tougher metal mesh. When selecting an angle grinder, it’s essential to choose the right blade. For cutting metal mesh, a thin, abrasive cutting wheel or a diamond wheel is recommended. These blades provide clean cuts without much effort. Always ensure the blade is securely fastened before use and replace it when it becomes worn out.
- Metal Shears: Metal shears come in both manual and power-operated varieties. Manual metal shears are ideal for smaller, more flexible pieces of mesh and provide greater control over the cut. Power-operated shears, however, are perfect for larger projects and thicker materials, offering speed and efficiency. They are particularly useful in industrial applications where large quantities of metal mesh need to be cut with precision.
- Hacksaws: Hacksaws are traditional tools that can be used for cutting metal mesh, particularly when working on a budget or in situations where power tools are not accessible. The key to the effective use of a hacksaw is blade selection. Fine-toothed blades are best for cutting thin metal mesh, whereas coarser blades are suitable for thicker materials. Always ensure the blade is properly tensioned to prevent it from bending or breaking during use.
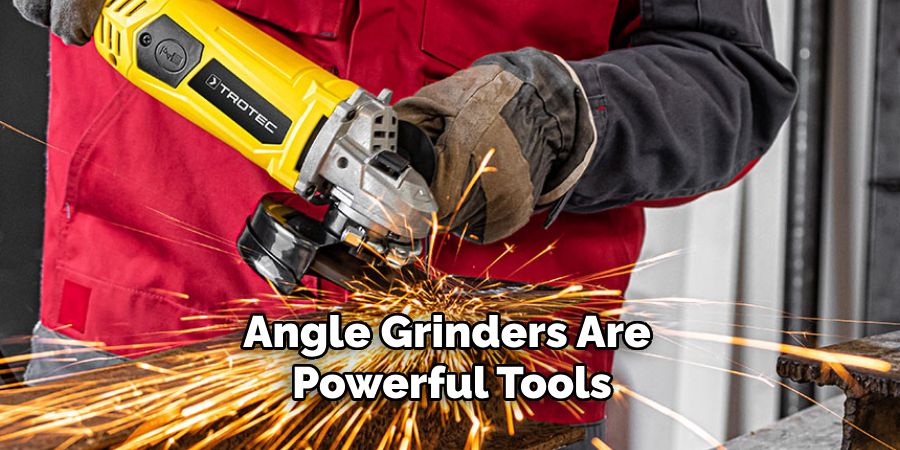
Safety Equipment
Using the right safety equipment is essential to ensure a safe cutting environment. Here are the key safety items to consider:
- Protective Gloves: Wearing protective gloves is crucial to safeguard your hands from sharp metal edges and prevent cuts and abrasions. Choose gloves made from materials like leather or Kevlar for enhanced durability and protection.
- Safety Goggles: Safety goggles shield your eyes from flying metal debris and fragments, which are common when cutting metal mesh. Ensure the goggles you select fit snugly and offer clear visibility without fogging up.
- Ear Protection: Cutting metal can be noisy, especially when using power tools like angle grinders or power shears. Ear protection, such as earplugs or earmuffs, helps prevent hearing damage and ensures a more comfortable working environment.
- Respirators: Some cutting methods, particularly those involving power tools, can generate fine metal dust and fumes. Wearing a respirator helps protect your respiratory system from inhaling these harmful particles. Ensure the respirator is rated for metal dust and fits well to provide effective filtration.
By equipping yourself with the right tools and safety gear, you’ll be well-prepared to cut metal mesh efficiently and safely.
Preparation Steps
Measuring and Marking
Accurate measurements are crucial when cutting metal mesh to ensure the final pieces fit perfectly into their intended slots. Mistakes in measuring can lead to wasted materials and time, making precision paramount.
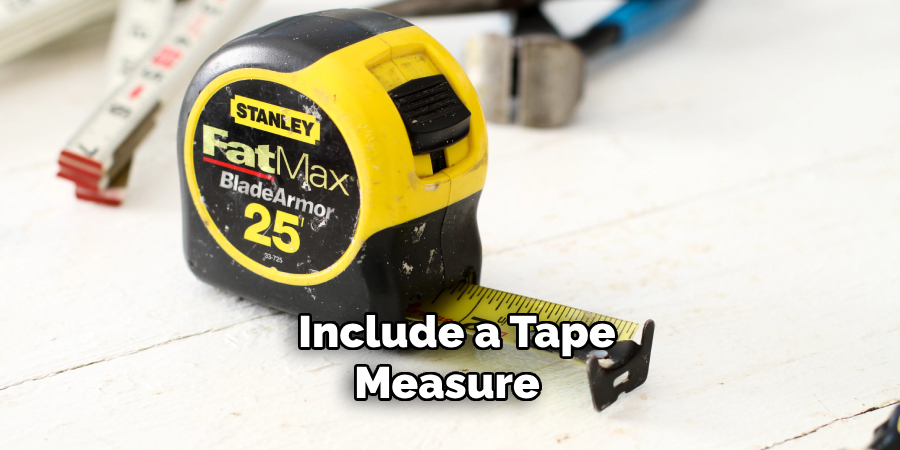
Essential tools for measuring include a tape measure and a ruler. A tape measure is flexible and can accommodate long spans of mesh, while a ruler is perfect for making smaller, more precise measurements.
After taking your measurements, marking the mesh correctly is the next vital step. For this, you can use chalk for temporary marks that can be easily adjusted or removed. Permanent markers offer clearer, more durable marks but require certainty in your measurements.
Scribes, typically used for metalwork, provide fine and accurate lines. Combining these measuring and marking tools will help you achieve the exact dimensions required for your project.
Setting Up the Work Area
Creating a stable and clean workspace is essential for precise and safe cutting of metal mesh. A clutter-free environment minimizes the risk of accidents and allows for better focus. Ensure your workbench is sturdy and at a comfortable height to make handling the mesh easier.
It’s important to securely fasten the metal mesh to prevent shifting during cutting, which can lead to uneven cuts or injuries.
Clamps are an excellent tool for holding the mesh in place and providing stability. Additionally, proper lighting is crucial for visibility, especially when marking and cutting intricate patterns.
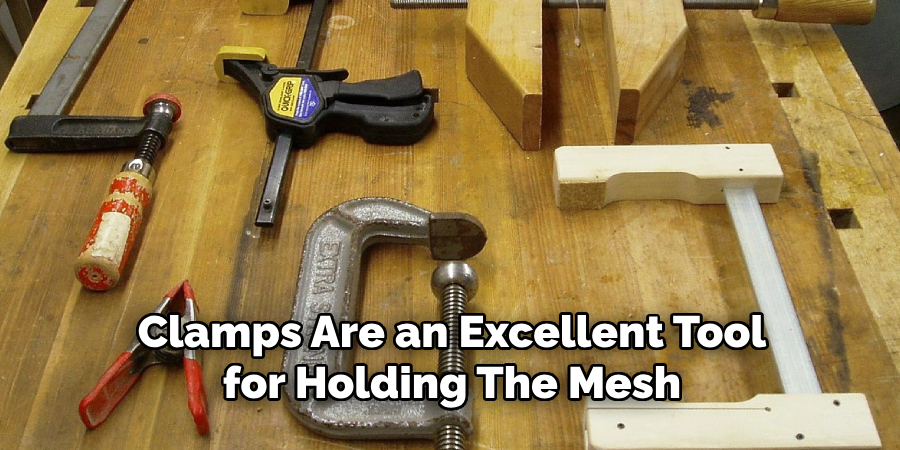
Using bright, focused lights can reduce eye strain and help you see fine details more clearly. By setting up a well-organized and well-lit work area, you can enhance both the accuracy and safety of your metal mesh cutting tasks.
How to Cut Metal Mesh: Cutting Techniques
Using Tin Snips and Aviation Snips
When using tin snips or aviation snips, start by securing your metal mesh with clamps to prevent movement. For straight cuts, use a ruler or straight edge to mark your cut line clearly.
Hold the snips with a firm grip and position the blades along the marked line. Begin cutting by applying steady pressure, ensuring the material doesn’t shift. For cutting curves, aviation snips are preferable.
Use left-cut or right-cut aviation snips depending on the direction of your curve. When making a curve, proceed slowly and make small, incremental cuts to maintain control and precision.
Regularly clean the blades to remove any metal shavings that could obstruct smooth cutting. For tighter radii, use compound leverage aviation snips for better control and reduced effort.
Cutting with an Angle Grinder
Selecting the right blade for your angle grinder is crucial. An abrasive cutting wheel or a diamond wheel is recommended for cutting metal mesh. Ensure the blade is securely fastened before starting.
Place the metal mesh on a stable surface and secure it with clamps. Wear all necessary safety gear, including gloves, goggles, ear protection, and a respirator.
Hold the angle grinder with both hands, positioning the blade against the marked cut line. Start the grinder and allow it to reach full speed before making contact with the mesh.
Apply gentle pressure and let the blade do the work to avoid overheating and warping the metal. Move slowly and steadily along the cut line for a clean finish. Regularly check the blade for wear and replace it if necessary to maintain cutting efficiency.
Using Metal Shears
Metal shears are available in manual and power-operated varieties, each suited for different applications. Manual metal shears are optimal for smaller, more flexible metal mesh pieces, providing control and precision. Position the metal mesh securely on your workbench and mark your cut lines.
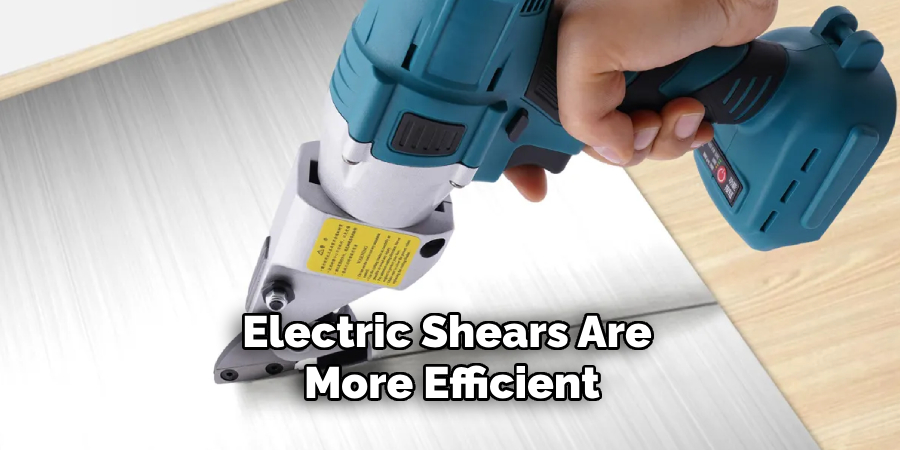
Use the shears to follow the markings, applying consistent pressure to produce clean cuts. For larger projects or thicker meshes, electric shears are more efficient. Ensure the mesh is firmly secured and follow the marked lines with the shears.
Electric shears offer speed and are especially effective for industrial-scale applications.
When cutting thicker mesh, use a slow and steady approach, allowing the tool to work through the material smoothly and prevent blade damage. Switch between manual and electric shears based on the project’s size and thickness to achieve optimal results.
By understanding and practicing these cutting techniques with each tool, you can achieve precise and efficient results for any metal mesh project.
How to Cut Metal Mesh: Advanced Cutting Methods
Plasma Cutting
Plasma cutters are high-precision tools that use an accelerated jet of hot plasma to cut through conductive materials. This process involves creating an electric arc between a nozzle and the metal, ionizing the gas, and forming plasma. Plasma cutters can slice through thick and thin metal mesh with remarkable speed and accuracy.
Pros:
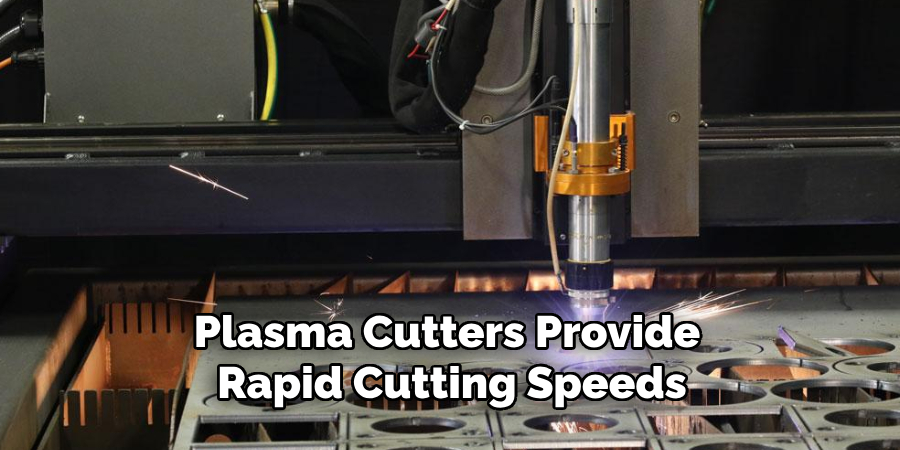
- Efficiency: Plasma cutters provide rapid cutting speeds, significantly reducing time spent on large projects.
- Versatility: They can cut through a variety of metals of different thicknesses.
- Clean Cuts: Plasma cutting leaves smooth edges, minimizing the need for additional finishing work.
Cons:
- Cost: Plasma cutters and their consumables can be expensive.
- Skill Requirement: Proper operation requires a certain level of expertise.
- Safety: Users must be cautious due to the high temperatures and potential for sparks.
Laser Cutting
Laser cutters employ a focused beam of light to melt, burn, or vaporize metal, allowing for extremely precise cuts. A laser cutter’s beam is controlled by computer numerical control (CNC), offering unparalleled accuracy for intricate designs.
Advantages:
- Precision: Laser cutters are incredibly accurate, making them ideal for detailed and complex shapes.
- Quality: Cuts made by laser cutters are clean and require minimal post-processing.
- Automation: CNC technology allows for high levels of automation, improving efficiency and consistency.
Cons:
- Initial Investment: Laser cutters are expensive, and their maintenance can add to operational costs.
- Material Limitations: While excellent for thinner materials, laser cutters may struggle with very thick meshes.
- Technical Knowledge: Operating CNC laser cutters requires technical knowledge and training.
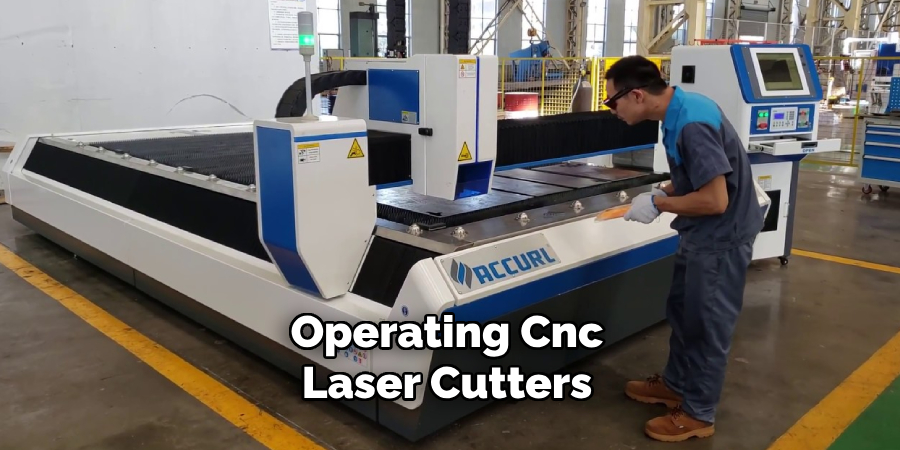
By integrating advanced tools like plasma and laser cutters into your metalwork repertoire, you can achieve precise cuts on metal mesh, bringing both efficiency and high-quality results to your projects.
Troubleshooting Common Issues
Dealing with Jagged Edges
Jagged edges can be a common issue when cutting metal mesh, often caused by dull blades, incorrect cutting angles, or improper tool selection.
Using a blade that is not sharp enough can tear the metal rather than cut it cleanly, resulting in rough edges. Additionally, cutting at an incorrect angle may cause the metal to snag, producing jagged finishes.
To smooth and finish jagged edges, start by filing them down with a metal file or sanding tool to eliminate any sharp protrusions.
For a finer finish, use progressively finer grit sandpaper. Another effective technique is to use a deburring tool, which can efficiently remove burrs and smooth out edges.
For enhanced safety and a high-quality finish, always inspect your tools before starting and maintain them regularly to ensure sharpness and precision.
Preventing Warping and Distortion
Warping and distortion of metal mesh can occur due to excessive heat or uneven pressure applied during the cutting process.
When using tools like angle grinders or plasma cutters, the intense heat generated can cause the metal to warp. Uneven clamping or improper handling can also lead to distortion, affecting the accuracy and fit of the cut pieces.
To avoid these issues, employ proper clamping techniques to hold the metal mesh securely in place on a stable, flat surface.
Utilize cooling methods such as applying water or compressed air to dissipate heat when using high-temperature cutting tools. When working with thinner mesh, consider using hand tools like tin snips to reduce heat buildup.
If warping occurs, gently realign the metal using a mallet or a vise. Ensuring correct tool choice and handling can significantly minimize the risk of warping and help maintain the integrity of your metal mesh projects.
Finishing Touches
Smoothing Edges
Ensuring smooth edges on metal mesh is essential for both safety and aesthetics. Tools commonly used for deburring include files, sandpaper, and rotary tools. Metal files come in various shapes and sizes, allowing you to choose the right one for the contours and intricacies of your mesh.
Sandpaper, especially when used in progressively finer grits, can help achieve a polished finish. Rotary tools equipped with abrasive discs or bits can efficiently handle larger areas and intricate patterns.
To achieve smooth edges, begin by using a coarse file to remove major burrs and rough spots. Follow this by sanding the edges with medium-grit sandpaper to even out the surface. For a polished finish, proceed with fine-grit sandpaper.
If using a rotary tool, maintain a consistent motion and pressure to avoid removing too much material at once. Regularly inspect your work, ensuring all edges are smooth and free of snags, enhancing both the functionality and appearance of the metal mesh.
Conclusion
In summary, this article has provided valuable insights on how to cut metal mesh effectively and safely. We’ve covered the importance of selecting the right tools and techniques to minimize issues like warping and distortion.
Properly smoothing edges was emphasized to ensure both safety and an aesthetically pleasing appearance.
Various coating methods, such as painting, powder coating, and galvanizing, were discussed to protect your metal mesh from corrosion and wear. General safety tips and emergency procedures were outlined to underscore the significance of a safety-first approach while working with metal mesh.
Mastering the proper techniques and prioritizing safety is paramount to achieving professional results.
By using the right tools and maintaining a vigilant attitude toward safety, you not only improve the quality of your projects but also create a safer working environment. We encourage you to practice continuously and refine your skills, ensuring each project is a step toward greater proficiency.
Edmund Sumlin is a skilled author for Metal Fixes, bringing 6 years of expertise in crafting a wide range of metal fixtures. With a strong background in metalwork, Edmund’s knowledge spans various types of fixtures, from decorative pieces to functional hardware, blending precision with creativity. His passion for metalworking and design has made him a trusted resource in the industry.
Professional Focus:
- Expert in Metal Fixtures : Edmund aesthetic specializes in creating durable and innovative metal fixtures, offering both appeal and functionality. His work reflects a deep understanding of metalworking techniques and materials.
- Sustainability Advocate : He is dedicated to using sustainable practices, ensuring that every fixture is crafted with eco-friendly methods while maintaining high-quality standards.
In his writing for Metal Fixes, Edmund provides valuable insights into the latest trends, techniques, and practical advice for those passionate about metal fixtures, whether they are professionals or DIY enthusiasts. His focus on combining artistry with engineering helps others discover the true potential of metal in design.