Finishing stainless steel is a crucial process in both industrial applications and home projects, significantly impacting the material’s aesthetic and functional qualities.
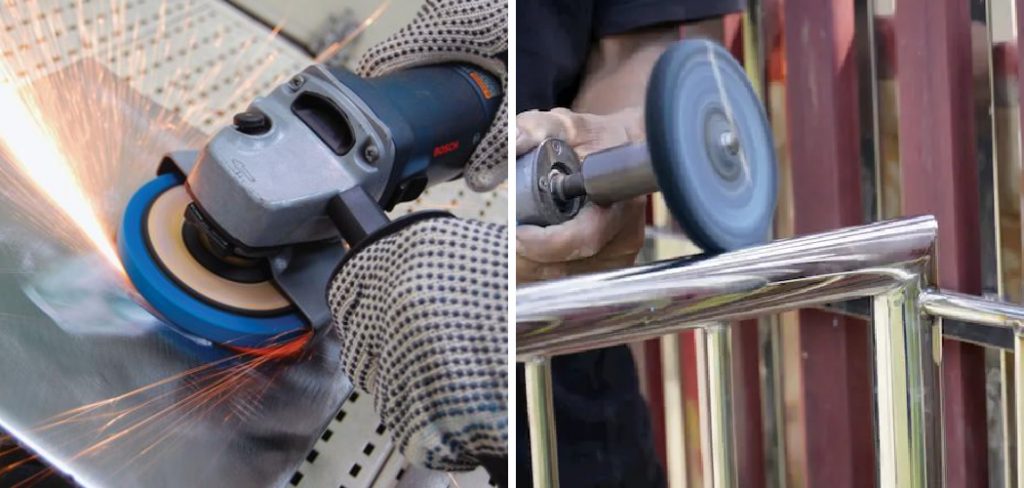
This meticulous procedure involves enhancing the surface to achieve a desired look, whether it’s a mirror-like polish for a sleek, modern appeal or a brushed finish for a subtle, understated elegance.
Beyond aesthetics, a well-executed finish can improve the steel’s resistance to corrosion, wear, and cleaning. The process encompasses several techniques on how to finish stainless steel, including grinding, polishing, buffing, and sometimes chemical treatments, each requiring specific tools and expertise.
For artisans and manufacturers alike, understanding these techniques is essential for ensuring that stainless steel not only meets design specifications but also performs optimally in its intended environment.
This guide delves into the step-by-step methods of finishing stainless steel, offering insights into the tools, materials, and best practices to achieve professional results.
Importance of Properly Finishing Stainless Steel
Properly finishing stainless steel is paramount to maximizing its numerous benefits. One of the most significant advantages is enhanced corrosion resistance. Stainless steel, by nature, is resistant to rust and tarnish; however, its susceptibility can increase in harsh environments.
A well-executed finish creates a smoother surface that limits areas where corrosive elements can accumulate, thus prolonging the material’s lifespan. Another critical aspect is hygiene, especially in industries such as food processing and healthcare, where stainless steel must be impeccably clean.
Finishing processes help eliminate crevices and microscopic grooves where bacteria could thrive, ensuring a more sanitary surface. Additionally, the mechanical properties of the steel can be improved—finishing processes reduce the risk of cracks and other irregularities that may compromise its structural integrity.
Lastly, the aesthetic appeal of a finished stainless steel piece can significantly enhance the overall design, making it more attractive and suitable for high-visibility applications. Proper finishing not only ensures that stainless steel performs its best but also contributes to its longevity and visual appeal.
Benefits of Stainless Steel Finishing
The benefits of stainless steel finishing are multifaceted, making it an essential process in both industrial and domestic applications. One of the primary advantages is aesthetic enhancement.
A polished or brushed finish can dramatically improve the appearance of stainless steel, making it suitable for high-end architectural projects, modern kitchen appliances, and decorative elements. A high-quality finish adds a refined, elegant look that underscores the material’s inherent beauty.
Improved durability is another significant benefit. Finishing processes can increase the steel’s resistance to scratches, wear, and other forms of surface damage. This not only extends the lifespan of the material but also reduces the need for frequent maintenance or replacement, ultimately saving both time and resources.
Finishing also contributes to better hygiene, which is crucial in sectors such as healthcare, food production, and hospitality. A smooth, polished surface minimizes the presence of crevices where bacteria and other contaminants could reside. This makes the stainless steel easier to clean and sanitize, thereby ensuring a higher standard of hygiene.
Additionally, enhanced corrosion resistance is a key benefit of stainless steel finishing. By creating a smoother and more uniform surface, finishing techniques help to prevent the accumulation of corrosive substances that could lead to rust and deterioration. This is especially important in environments exposed to moisture, chemicals, or extreme temperatures.
Finally, stainless steel finishing offers greater versatility. Different finishes can be applied to tailor the material’s appearance and performance to specific requirements, whether it’s a reflective mirror finish for decorative purposes or a non-reflective matte finish for functional applications. This adaptability makes stainless steel an even more valuable material for a wide range of uses.
Understanding Stainless Steel
Stainless steel is a versatile and widely used metal known for its corrosion resistance, strength, and appearance.
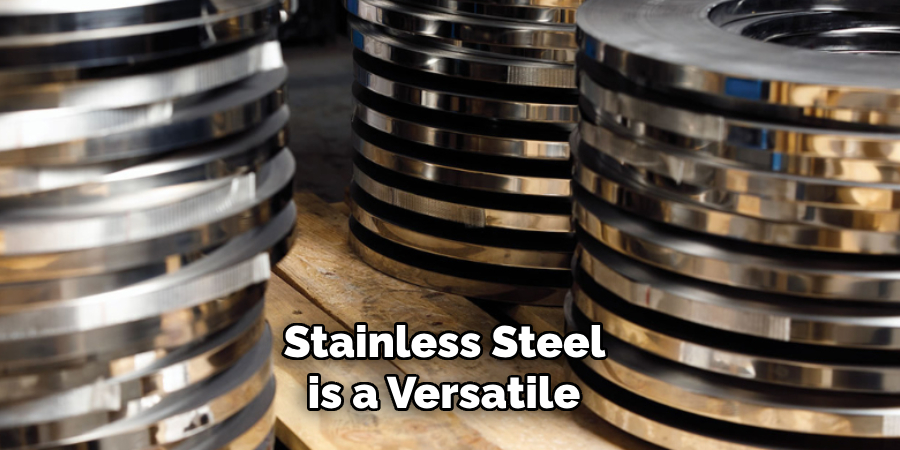
It is an alloy composed primarily of iron, with a significant amount of chromium—typically at least 10.5%—which forms a passive layer of chromium oxide on the surface. This layer is what gives stainless steel its remarkable resistance to rust and staining.
In addition to chromium, stainless steel may contain elements such as nickel, molybdenum, titanium, and others, which enhance its properties and make it suitable for a variety of applications.
There are several types of stainless steel, classified based on their crystalline structure. The most common types include austenitic, ferritic, martensitic, and duplex stainless steels. Austenitic stainless steels, which make up the largest group, are known for their excellent corrosion resistance and formability.
They are typically non-magnetic and maintain their strength at both high and low temperatures. Ferritic stainless steels are magnetic and offer good corrosion resistance and formability but are less durable in severe environments.
Martensitic stainless steels are characterized by high strength and hardness but usually differ in corrosion resistance compared to austenitic and ferritic types. Duplex stainless steels combine the advantages of both austenitic and ferritic stainless steels, offering high strength, good corrosion resistance, and enhanced weldability.
Understanding the different types and properties of stainless steel is crucial for selecting the right material for a specific application. Each type has its strengths and weaknesses, making certain varieties more suited to specific environments and uses.
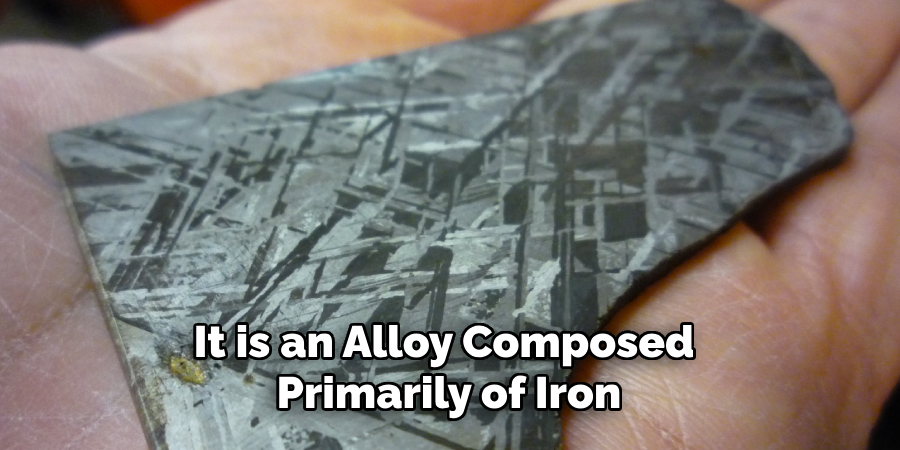
Whether for industrial machinery, kitchen utensils, architectural elements, or medical devices, the appropriate selection of stainless steel ensures optimal performance and longevity.
Types of Stainless Steel Finishes
Stainless steel finishes are varied and each type serves different aesthetic and functional purposes. Here are some common stainless steel finishes:
1. Mill Finishes
Mill finishes are the basic supply condition for stainless steels, with the finish produced by the steel mill itself. These finishes include No. 1 (hot rolled, annealed and pickled), 2D (cold rolled, annealed, pickled, and passivated), and 2B (cold rolled, annealed, pickled, passivated, and skin passed).
- No. 1: A rough and dull finish used for thick plates and other heavy-section products.
- 2D: Has a smoother, matte finish compared to No. 1 and is often used for industrial applications.
- 2B: Smooth, reflective, and the most common finish for sheet and plate material. Suitable for a wide range of applications from kitchen appliances to architectural panels.
2. Brushed Finishes
Brushed finishes provide a distinctive look with a fine pattern of parallel lines. A popular type is the No. 4 finish:
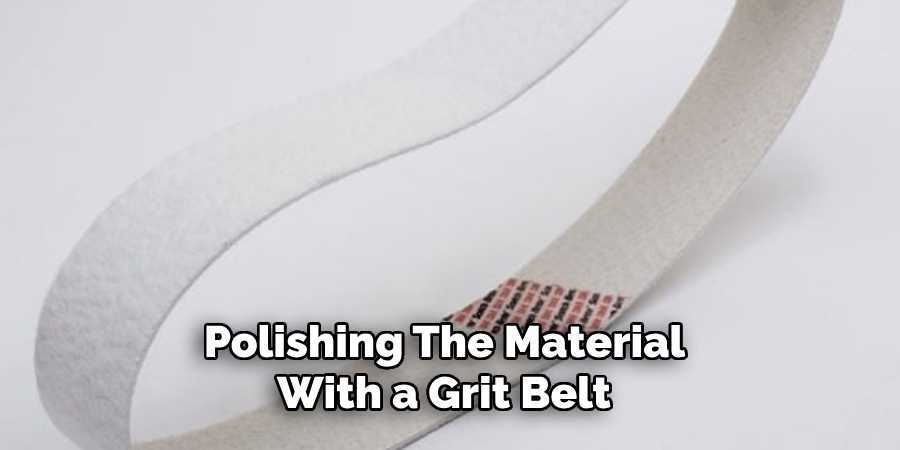
- No. 4: Achieved by polishing the material with a grit belt or wheel, followed by a number of finer grit belts or wheels to achieve a gleaming, brushed appearance. Commonly used in kitchen appliances, sanitary applications, and architectural elements.
3. Mirror Finishes
Mirror finishes are highly reflective and achieved through extensive polishing. Examples include No. 8 and Super Mirror (No. 10).
- No. 8: Also known as 8K or mirror finish, it provides a highly reflective surfaces akin to a mirror. Typically used in architectural and decorative applications where a high degree of polish is required.
- Super Mirror (No. 10): An ultra-refined variant of No. 8, offering an exceptionally smooth and bright reflection.
4. Satin Finish
Satin finishes, such as the No. 6, offer a soft, non-reflective sheen that falls between a matte and polished finish.
- No. 6: Created using tampico brushes in a medium abrasive binder, producing a soft satin finish. It’s especially suitable for residential and commercial windows, doors, and paneling.
5. Bead Blasted Finish
Bead blasted finishes are created by blasting the stainless steel surface with glass beads. This produces a non-directional, matte texture that reduces glare and improves uniformity.
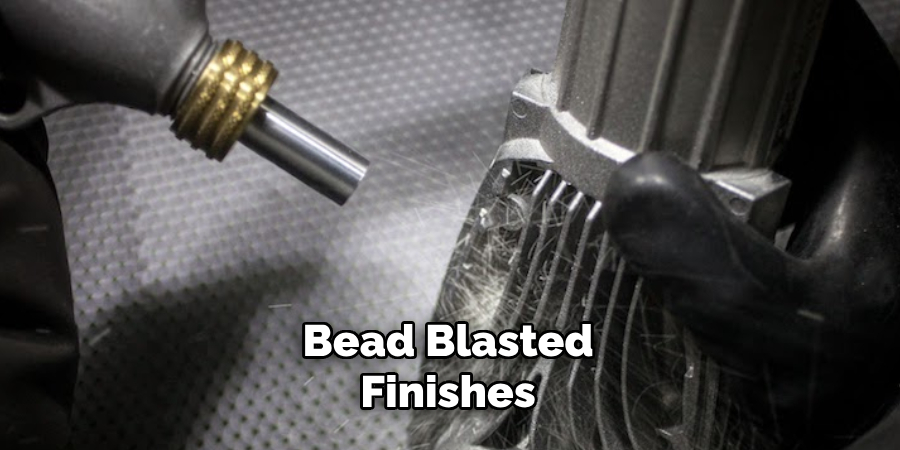
6. Electropolished Finish
Electropolishing is an electrochemical process that smooths and brightens stainless steel, offering a high gloss and enhanced corrosion resistance.
7. Custom Finishes
In addition to standard finishes, custom finishes can be created to meet unique design and performance requirements. Techniques for custom finishes might include mixing different grits, applying patterns or etches, or combining processes for a bespoke surface.
Overall, the choice of stainless steel finish depends on the intended application, desired aesthetics, and environmental demands. Each finish offers a distinct combination of visual appeal and functional attributes, making stainless steel an incredibly versatile material.
10 Methods How to Finish Stainless Steel
1. Mechanical Polishing
Mechanical polishing involves the use of abrasives and machines to smooth and finish stainless steel surfaces. This method is highly effective in achieving a mirror-like finish and is commonly employed for decorative applications. The process begins with rough grinding to remove surface imperfections, followed by successive stages of finer abrasives to achieve the desired smoothness.
The final step often involves buffing with polishing compounds to enhance the shine. Mechanical polishing not only improves the aesthetic appeal of stainless steel but also helps in reducing the risk of corrosion by eliminating surface defects where contaminants can accumulate.
2. Electrochemical Polishing
Electrochemical polishing, also known as electropolishing, is a process that uses an electrolytic solution and an electric current to remove a thin layer of metal from the stainless steel surface.
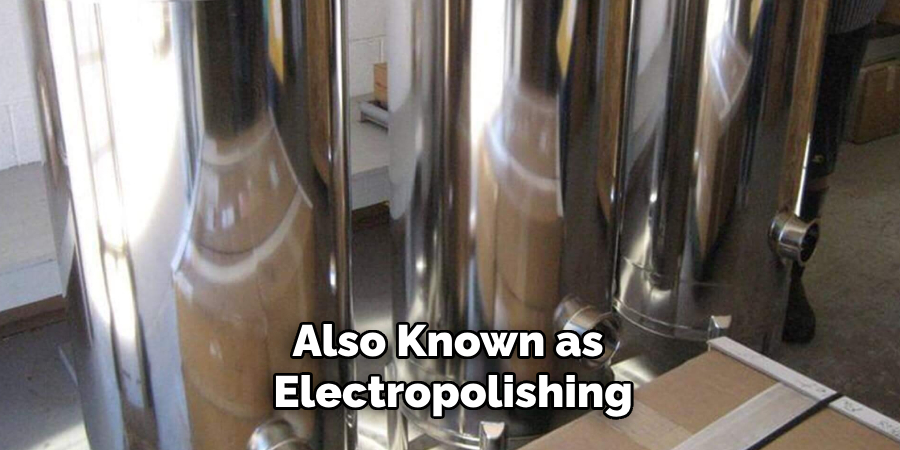
This method is particularly effective in achieving a highly reflective, smooth finish and is often used for components that require high levels of cleanliness and corrosion resistance, such as in the medical and food processing industries.
During electropolishing, the stainless steel part is submerged in an electrolyte bath, and a direct current is applied, causing metal ions to dissolve from the surface. The process preferentially removes microscopic peaks, leaving a smooth, uniform finish that enhances the material’s aesthetic and functional properties.
3. Passivation
Passivation is a chemical treatment process that enhances the corrosion resistance of stainless steel by removing free iron and other contaminants from the surface. This is achieved by immersing the stainless steel in a nitric acid or citric acid solution, which dissolves iron particles and promotes the formation of a protective oxide layer.
The passivation process is crucial for applications where stainless steel is exposed to harsh environments or requires stringent hygiene standards. By creating a passive, non-reactive surface, passivation helps to maintain the integrity and longevity of stainless steel components, making it an essential step in many finishing procedures.
4. Bead Blasting
Bead blasting is a finishing technique that involves propelling fine glass beads at high velocity onto the stainless steel surface.
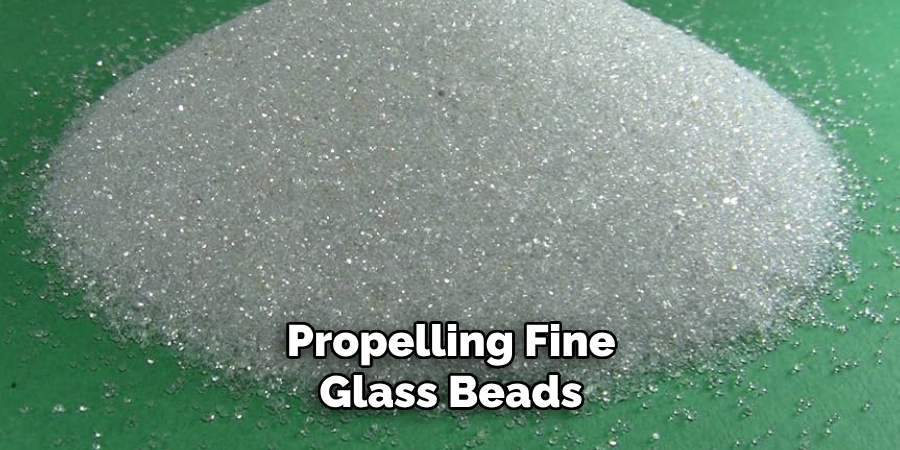
This process creates a uniform, matte finish that is both aesthetically pleasing and functional. Bead blasting is particularly effective in removing surface contaminants, oxide layers, and light burrs, making it suitable for preparing surfaces for further finishing treatments or painting.
The bead blasting process can be precisely controlled to achieve the desired texture and appearance, ranging from a soft, satin-like finish to a more pronounced, textured surface. This versatility makes bead blasting a popular choice for a wide range of industrial and decorative applications.
5. Chemical Etching
Chemical etching is a precision process that uses acid or alkali solutions to selectively remove material from the stainless steel surface, creating intricate designs, logos, or patterns.
This technique is widely used in the production of nameplates, signage, and decorative panels, where detailed and permanent markings are required. The process involves coating the stainless steel with a resist material that protects specific areas from the etching solution.
The exposed areas are then subjected to the chemical etchant, which dissolves the metal to create the desired pattern. Chemical etching provides a high level of detail and accuracy, making it ideal for complex designs and fine text.
6. Grinding and Brushing
Grinding and brushing are mechanical processes that enhance the surface texture and appearance of stainless steel. Grinding involves the use of abrasive wheels to remove surface material and achieve a smooth, even finish. This process is essential for preparing stainless steel surfaces for further finishing treatments or for achieving a specific surface roughness.
Brushing, on the other hand, uses abrasive brushes to create a distinctive, linear texture on the stainless steel surface.
The brushed finish, also known as a satin finish, is popular for its subdued, non-reflective appearance and is commonly used in architectural and interior design applications. Both grinding and brushing can be tailored to achieve the desired level of smoothness and texture.
7. Satin Finishing
Satin finishing, also known as a brushed or dull polish, creates a uniform, low-reflective surface on stainless steel.
This finish is achieved through a series of abrasive treatments that create fine, parallel lines on the metal surface. Satin finishing is prized for its ability to hide fingerprints, scratches, and other surface imperfections, making it a popular choice for high-traffic areas and functional components.
The process involves the use of abrasive belts or wheels, followed by buffing with fine abrasives to achieve the desired level of sheen. Satin finishes are commonly used in kitchen appliances, architectural elements, and automotive trim for their practical and aesthetic qualities.
8. Vibratory Finishing
Vibratory finishing is a mass finishing process that involves placing stainless steel parts in a vibrating container filled with abrasive media. The vibrations cause the parts and media to rub against each other, effectively deburring, cleaning, and polishing the surfaces.
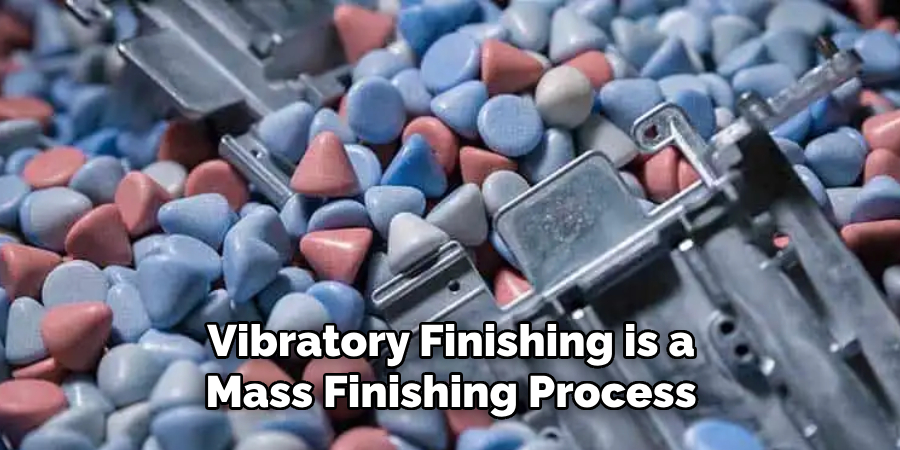
This method is particularly effective for finishing small, complex parts that are difficult to polish by hand. Vibratory finishing can be used to achieve a range of surface finishes, from smooth and shiny to matte, depending on the type of media and processing time.
The process is highly efficient and cost-effective, making it a popular choice for batch processing of industrial components.
9. Tumbling
Tumbling, similar to vibratory finishing, is a mass finishing process where stainless steel parts are placed in a rotating barrel along with abrasive media. As the barrel rotates, the parts and media collide and abrade against each other, resulting in the removal of burrs, sharp edges, and surface imperfections.
Tumbling is effective for achieving a polished, smooth finish on a variety of part shapes and sizes.
The process can be customized by selecting different types of media, such as ceramic, plastic, or steel, to achieve the desired surface finish. Tumbling is widely used in the jewelry, aerospace, and automotive industries for its ability to produce consistent, high-quality finishes on large batches of parts.
10. Electroless Plating
Electroless plating is a chemical process that deposits a metal layer on the stainless steel surface without the use of an external electric current.
This process involves immersing the stainless steel in a bath containing metal ions, reducing agents, and other chemicals that facilitate the deposition of the metal layer.
Electroless plating is used to enhance the corrosion resistance, hardness, and appearance of stainless steel. Common metals used in electroless plating include nickel, gold, and silver.
This method provides uniform coating thickness and excellent adhesion, making it suitable for precision components and complex geometries.
Electroless plating is widely used in the electronics, aerospace, and automotive industries for its ability to improve the functional and aesthetic properties of stainless steel components.
Conclusion
Finishing stainless steel is a crucial step in ensuring both its aesthetic appeal and functional performance.
Each method, from mechanical polishing to electroless plating, offers unique advantages tailored to specific applications. Mechanical polishing and electropolishing are ideal for achieving high-gloss, smooth finishes, while passivation and chemical etching enhance corrosion resistance and precision.
Bead blasting and brushing provide textured finishes suitable for decorative and functional uses. Satin finishing, vibratory finishing, and tumbling offer practical solutions for high-traffic areas and complex parts. Thanks for reading, and we hope this has given you some inspiration on how to finish stainless steel!
Edmund Sumlin is a skilled author for Metal Fixes, bringing 6 years of expertise in crafting a wide range of metal fixtures. With a strong background in metalwork, Edmund’s knowledge spans various types of fixtures, from decorative pieces to functional hardware, blending precision with creativity. His passion for metalworking and design has made him a trusted resource in the industry.
Professional Focus:
- Expert in Metal Fixtures : Edmund aesthetic specializes in creating durable and innovative metal fixtures, offering both appeal and functionality. His work reflects a deep understanding of metalworking techniques and materials.
- Sustainability Advocate : He is dedicated to using sustainable practices, ensuring that every fixture is crafted with eco-friendly methods while maintaining high-quality standards.
In his writing for Metal Fixes, Edmund provides valuable insights into the latest trends, techniques, and practical advice for those passionate about metal fixtures, whether they are professionals or DIY enthusiasts. His focus on combining artistry with engineering helps others discover the true potential of metal in design.