When it comes to working with aluminum, selecting the appropriate adhesive and technique is crucial for achieving strong and reliable bonds. Aluminum is widely used in various industries due to its lightweight and durable nature. However, its smooth surface and naturally occurring oxide layer can present challenges in bonding.
This guide will explore how to glue aluminum, ensuring successful applications in both commercial and DIY projects. Whether you’re repairing a broken item or assembling new structures, understanding the process of gluing aluminum will help you achieve the desired results.
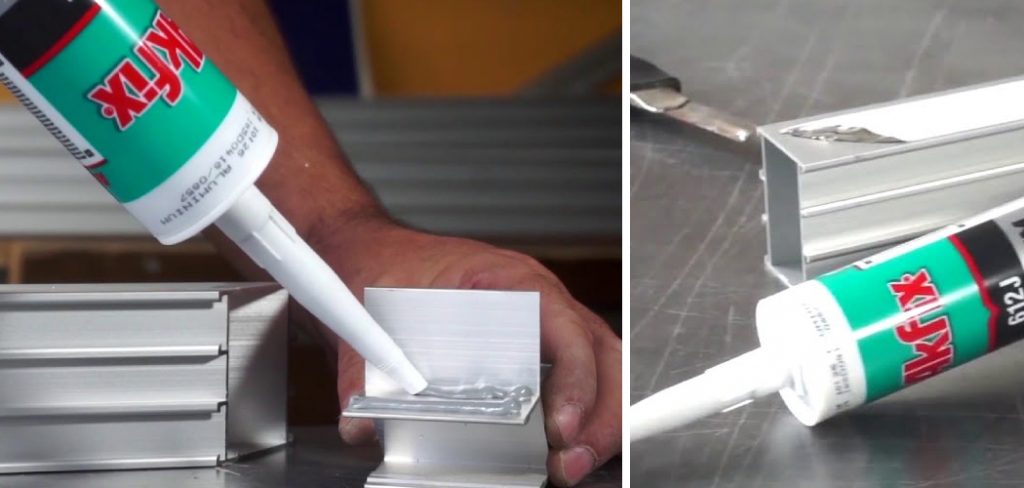
Why Glue Aluminum?
Gluing aluminum offers several advantages, making it a preferred choice in many applications where traditional fastening methods might be less effective. One of the primary reasons to use adhesives is the ability to create seamless and aesthetically pleasing joints without the need for visible screws or bolts. This is particularly beneficial in industries such as automotive, aerospace, and electronics,
where weight reduction and streamlined design are essential. Adhesive bonding also helps in distributing stress evenly across the joint, reducing the risk of mechanical failure. Additionally, using adhesives can protect the aluminum from potential damage caused by drilling holes for fasteners, which can compromise the material’s integrity. By opting for adhesive bonding, one can achieve reliable, durable, and visually appealing results.
Why Traditional Adhesives May Not Work Well on Aluminum
Traditional adhesives often struggle to bond effectively with aluminum due to a few inherent characteristics of the metal. Firstly, aluminum has a very smooth surface, which can hinder the ability of adhesives to grip and create a strong bond. Additionally, aluminum quickly forms a thin oxide layer when exposed to air, which can act as a barrier,
preventing adhesives from adhering properly to the metal beneath. This oxide layer is constantly reforming, making it challenging for traditional adhesives to maintain a durable bond over time. As a result, specialized adhesives designed for metal bonding are often required to ensure a reliable and long-lasting bond when working with aluminum.
10 Methods How to Glue Aluminum
1. Clean the Surface Thoroughly
The first and most important step in gluing aluminum is to ensure the surface is completely clean. Aluminum surfaces often have oils, dust, and dirt that can weaken the bond. Use a degreaser, like acetone or isopropyl alcohol, to clean the surface thoroughly. Apply the cleaner with a lint-free cloth and wipe away all contaminants. For the best results, repeat the cleaning process a couple of times, as even a slight residue can reduce the adhesive’s effectiveness. Once cleaned, avoid touching the area to keep it free of oils from your skin.
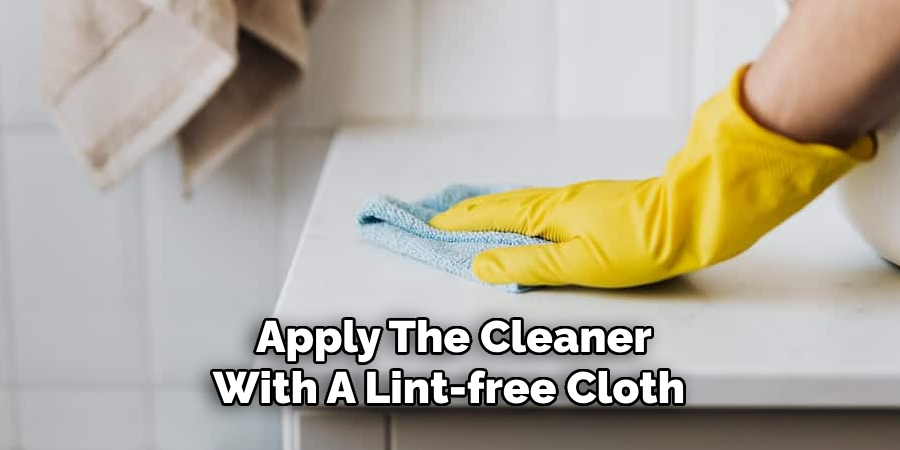
2. Sand the Aluminum Surface for Better Adhesion
Due to aluminum’s smooth surface, it’s helpful to create some texture before gluing. Use fine-grit sandpaper (120-220 grit) to sand the area lightly, creating a rougher surface for the adhesive to grip. Sanding also removes the aluminum oxide layer, which can prevent adhesives from bonding effectively. Be sure to sand in even strokes and wipe away the dust with a clean cloth afterward. This extra step improves adhesive performance and increases the overall strength of the bond.
3. Choose the Right Adhesive
Not all adhesives work well with aluminum, so selecting the right one is crucial. Epoxy adhesives, polyurethane, and specialized metal adhesives are ideal for bonding aluminum. Epoxies, in particular, create strong, durable bonds with aluminum and are suitable for heavy-duty applications. For lighter bonds or temporary attachments, cyanoacrylate (super glue) may be sufficient. Read the product label to ensure the adhesive is compatible with aluminum and the environment in which it will be used (e.g., waterproof, heat-resistant, etc.).
4. Use a Two-Part Epoxy for Strong Bonds
Two-part epoxies are an excellent choice for gluing aluminum when a strong, permanent bond is needed. Two-part epoxies consist of a resin and a hardener, which must be mixed before application. This combination creates a chemical reaction that forms a hard, durable bond. After mixing, apply the epoxy to both surfaces and press them together firmly. Epoxies can take anywhere from a few minutes to several hours to fully cure, so check the manufacturer’s instructions for drying times. This method is ideal for applications requiring high strength.
5. Try a High-Strength Polyurethane Adhesive
Polyurethane adhesives are another reliable option for bonding aluminum, as they expand slightly when curing, filling any small gaps between surfaces. This adhesive type is waterproof and weather-resistant, making it suitable for outdoor and high-humidity environments. Apply a thin layer of polyurethane adhesive to one surface, press the two pieces of aluminum together, and clamp them for the recommended curing time. Polyurethane is versatile and bonds well with many materials, providing a flexible but durable bond.
6. Use a Clamping System to Ensure Firm Contact
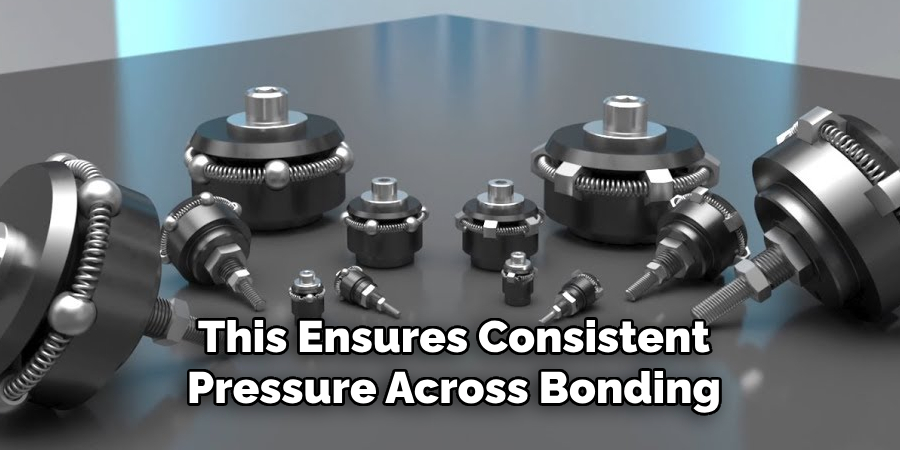
For best results when gluing aluminum, use clamps to hold the pieces together while the adhesive cures. Aluminum surfaces can separate if not held firmly, especially when using thick adhesives like epoxy or polyurethane. Apply the adhesive and then place clamps around the edges or across the entire surface, depending on the size of your project. This ensures consistent pressure across the bonding area and prevents gaps that can weaken the joint. Leave the clamps on for the recommended curing time to achieve maximum strength.
7. Consider Using a Primer for Enhanced Adhesion
When working with aluminum, applying a primer specifically designed for metal can improve adhesive performance. Metal primers create a bonding layer that enhances the adhesive’s grip, particularly with difficult surfaces like aluminum. Spray or brush on a thin layer of metal primer and allow it to dry completely before applying the adhesive. This method is especially useful if you are using adhesives like epoxy or polyurethane, as it ensures a stronger, longer-lasting bond.
8. Try Instant Adhesives for Small Projects
For small, quick repairs, instant adhesives like cyanoacrylate (super glue) are convenient for gluing aluminum. These adhesives bond almost instantly and require minimal setup. Simply apply a small amount to one surface and press the aluminum pieces together. Hold them firmly for a few seconds until the bond sets. While cyanoacrylate isn’t as strong as epoxy or polyurethane for heavy-duty projects, it’s ideal for lightweight aluminum items and minor fixes where speed is a priority.
9. Apply Adhesive Tape for Easy and Clean Bonding
Double-sided adhesive tapes designed for metal surfaces are another option for bonding aluminum. These tapes are ideal for situations where traditional adhesives might be messy or difficult to apply. Metal bonding tapes are available in various strengths, with some rated for industrial applications. Clean the surface thoroughly, cut the tape to size, and press it onto the aluminum. Tape adhesives provide a neat, instant bond without the need for curing or clamping, although they are generally best for light-duty applications.
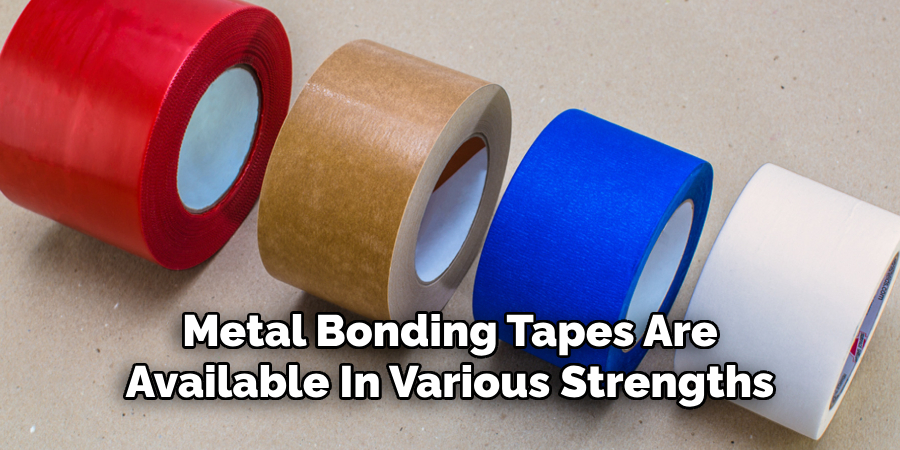
10. Allow Sufficient Curing Time for Stronger Bonds
Patience is key to ensuring a strong bond when gluing aluminum. Each adhesive has a recommended curing time, which is crucial for achieving maximum strength. Avoid disturbing or moving the pieces during curing, as even minor shifts can weaken the bond. Many epoxies require 24 hours to fully cure, while polyurethane may take longer, depending on humidity and temperature. Always refer to the manufacturer’s instructions for optimal curing conditions, and if possible, allow extra time for curing to ensure a solid, reliable bond.
Things to Consider When Gluing Aluminum
- Surface Preparation: Proper surface preparation is crucial for achieving a reliable bond. Ensure the aluminum is clean and dry before applying any adhesive. Removing any oils, dirt, or debris can prevent interference with the adhesive’s contact and effectiveness.
- Temperature and Humidity: Environmental conditions can significantly affect the curing process and the final bond strength. It’s important to check the adhesive manufacturer’s instructions regarding optimal temperature and humidity levels for application. Working in conditions outside those recommendations can lead to weak bonds.
- Load and Stress Factors: Consider the load and stress the glued joint will endure. This will help you select the most suitable adhesive for the job. Larger loads require stronger adhesives like epoxies or polyurethane, while lighter tasks may suffice with instant adhesives.
- Safety Precautions: Adhesives can contain chemicals that are harmful if inhaled or come into contact with skin. Always work in a well-ventilated area and use protective gear, such as gloves and safety glasses, to prevent injury.
- Aesthetic Considerations: For visible joints, consider how the adhesive might affect the appearance of the finished product. Some adhesives may yellow over time or leave visible residue. Choosing clear or color-matched adhesives can help maintain the aesthetic quality of your project.
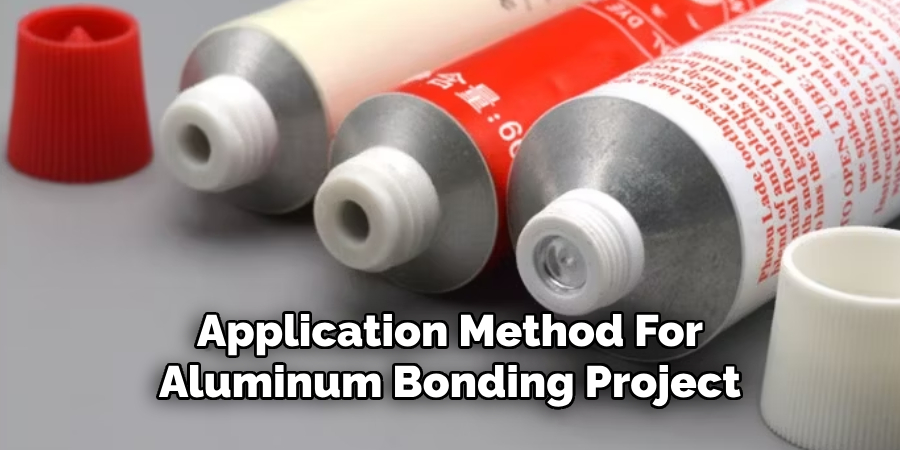
These considerations can guide you in choosing the right adhesive and application method for your aluminum bonding project, ensuring the durability and reliability of the bond.
Conclusion
In conclusion, successfully gluing aluminum requires careful consideration of the materials and techniques utilized. Proper surface preparation, including sanding and cleaning, is crucial for creating an optimal bonding surface. Selecting the right adhesive is also imperative; two-part epoxies and polyurethane adhesives offer durable and robust solutions for most projects. Thanks for reading our blog post on how to glue aluminum! We hope you found it helpful and informative.
Edmund Sumlin is a skilled author for Metal Fixes, bringing 6 years of expertise in crafting a wide range of metal fixtures. With a strong background in metalwork, Edmund’s knowledge spans various types of fixtures, from decorative pieces to functional hardware, blending precision with creativity. His passion for metalworking and design has made him a trusted resource in the industry.
Professional Focus:
- Expert in Metal Fixtures : Edmund aesthetic specializes in creating durable and innovative metal fixtures, offering both appeal and functionality. His work reflects a deep understanding of metalworking techniques and materials.
- Sustainability Advocate : He is dedicated to using sustainable practices, ensuring that every fixture is crafted with eco-friendly methods while maintaining high-quality standards.
In his writing for Metal Fixes, Edmund provides valuable insights into the latest trends, techniques, and practical advice for those passionate about metal fixtures, whether they are professionals or DIY enthusiasts. His focus on combining artistry with engineering helps others discover the true potential of metal in design.