Are you planning to construct a metal building? Grounding is an essential step that should be considered during construction.
Properly grounding a metal building is essential in ensuring its safety and longevity. Grounding helps protect the structure against electrical faults and lightning strikes by providing a direct path for electrical current to dissipate safely into the earth. This process helps safeguard the building’s occupants and contents and prevents potential damage to electrical systems and equipment. When planning to ground a metal building, it is crucial to understand the electrical requirements, local codes, and necessary materials to achieve a safe and effective grounding system.

In this guide on how to ground a metal building, we will explore the steps and considerations required to ground a metal building properly.
What Will You Need?
Before beginning the grounding process, you must gather some essential items. These include:
- Copper Ground Rods: These are long metal rods, typically made of copper or galvanized steel, that serve as the building’s main grounding electrode.
- Grounding Clamps and Connectors: These devices connect the ground rod to other components within the grounding system.
- Copper Wire: This creates a low-resistance path between different grounding points.
- Hammer Drill and Bits: The hammer drill drives the ground rods into the earth, while bits are necessary for drilling holes in concrete or asphalt surfaces.
- Safety Gear: Proper safety gear, such as gloves and safety glasses, is crucial when handling grounding materials.
Once you have gathered all the necessary materials, you can begin the grounding process.
9 Easy Steps on How to Ground a Metal Building
Step 1. Plan the Layout
When planning the layout for grounding your metal building, assess the site and identify the best locations for installing the ground rods. Consider factors such as soil conditions, building structure, and the proximity to the building’s electrical panel. The standard practice is to space multiple ground rods evenly around the structure’s perimeter to ensure comprehensive grounding coverage.
Additionally, evaluate any existing underground obstacles or utilities that may interfere with the installation and adjust your layout plan accordingly. Proper planning at this stage will help streamline the installation process, minimize potential challenges, and ensure that your grounding system is efficient and compliant with local electrical codes. It is also advantageous to consult with a qualified electrician or engineer during this phase to confirm that your layout design meets all safety and code requirements.
Step 2. Install the Ground Rods
Begin by driving the copper ground rods into the earth at the pre-determined locations marked during the planning stage. Use a hammer drill with appropriate bits to penetrate hard surfaces such as concrete or asphalt, ensuring that at least eight feet of each rod is embedded into the ground for maximum effectiveness. Space the rods by your site plan, maintaining an adequate distance from each other and ensuring a consistent connection to the building’s electrical system.
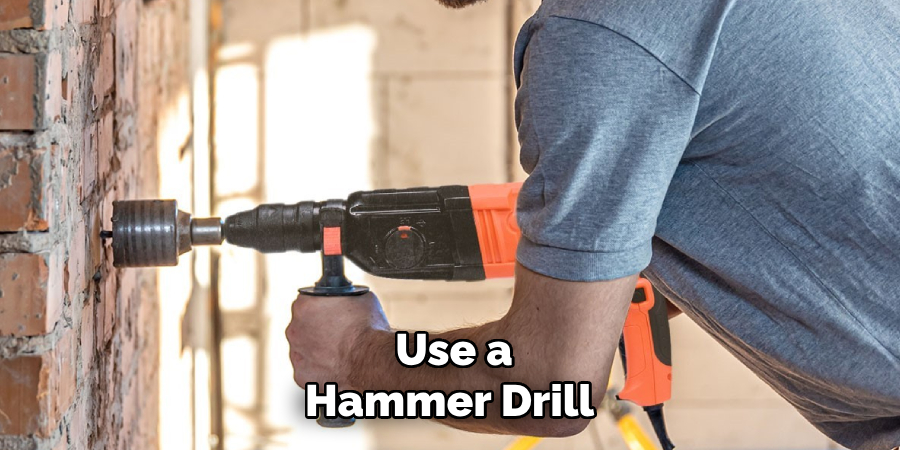
Verify that the top of each rod is slightly above ground level, as this will facilitate the secure attachment of grounding clamps and connectors. During this step, always adhere to all safety protocols, including wearing protective gear, and consult local grounding regulations to confirm compliance.
Step 3. Connect the Ground Rods to the Building
Once the ground rods are securely installed, the next step is to interconnect them with the building using copper wire. Begin by attaching grounding clamps to the exposed tops of the ground rods. Ensure that these connections are tight and secure to maintain exceptional conductivity.
Run copper wire from each ground rod to a central grounding point near the building’s main electrical panel. It’s essential to use wire-rated for outdoor use to withstand environmental conditions. When connecting the wire to the grounding point, utilize approved connectors to ensure a stable and safe connection. Ensure that the entire grounding path has minimal resistance and is free from corrosion to enhance the efficiency of the grounding system. As always, follow local electrical codes and safety guidelines when performing this task, and consider consulting a licensed electrician to verify that everything is correctly set up.
Step 4. Test the Grounding System
After all connections have been made, it is crucial to test the grounding system to confirm its effectiveness and safety. A multimeter or a specialized ground resistance tester is used to measure the resistance of the grounding system. An adequately grounded system should display a low resistance value, indicating that electricity can dissipate efficiently into the ground.
If the resistance value is higher than desired, it may suggest inadequate connections or the need for additional ground rods to achieve better conductivity. Conduct tests at various points within the system to ensure uniformity and compliance with local electrical codes. Address any detected issues promptly to enhance grounding performance. It’s advisable to carry out this testing under the guidance of a qualified electrician to guarantee accurate results and compliance with safety standards.
Step 5. Maintain the Grounding System
Maintaining the grounding system is essential to ensure its long-term effectiveness and safety. Regular inspections should be conducted to check for signs of wear or corrosion on wires, clamps, and connectors. Any oxidization or damage must be addressed promptly to prevent reduced conductivity and maintain a reliable grounding path. Ensure that all connections remain tight and that no accidental disconnections have occurred, which might compromise the system’s integrity. Additionally, evaluate the condition of the ground rods and ensure they remain securely embedded in the earth.
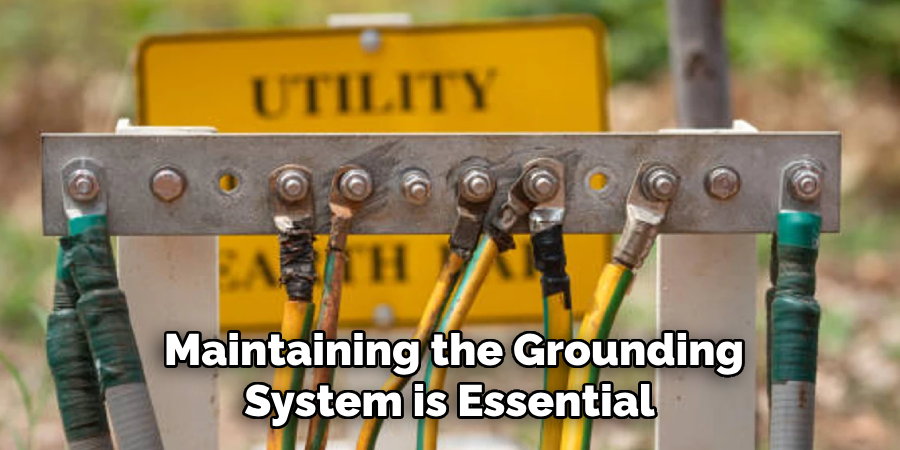
Over time, environmental factors such as soil movement or erosion could affect the positioning and effectiveness of the rods, requiring adjustments. Documentation of maintenance activities is advisable to track system performance and identify any areas needing frequent attention.
Step 6. Upgrade and Expand Grounding if Necessary
As your metal building or its electrical needs evolve, upgrading or expanding the grounding system may become necessary. With technological advancements and increased reliance on electronic devices, ensuring that your grounding system can handle additional electrical loads is vital. Begin by reassessing your building’s current grounding infrastructure in the context of its upgraded use cases or any new additions. Consider adding extra ground rods or enhancing existing connections with thicker gauge copper wire to accommodate increased electricity flow.
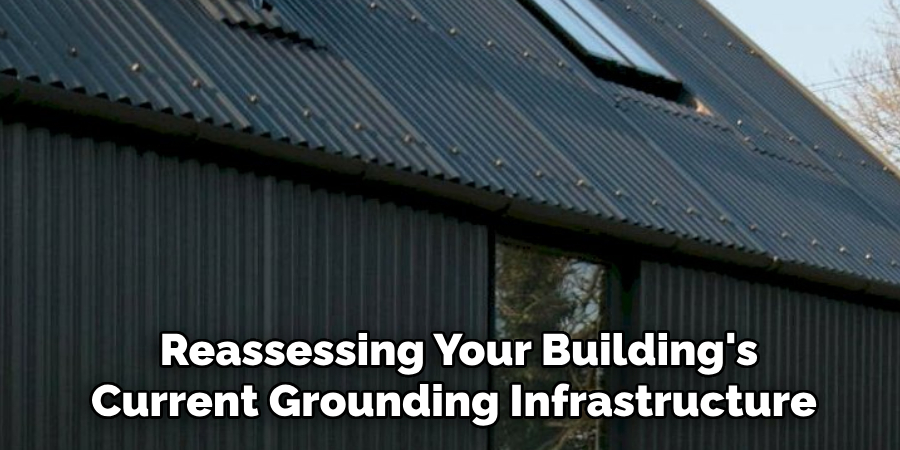
Make sure any added components are compliant with current building codes and standards. Consulting with a professional electrician during this assessment and upgrade process is crucial, as they can provide insights into new regulations and advanced grounding techniques. This proactive approach will uphold the safety and effectiveness of the grounding system, preventing potential electrical hazards.
Step 7. Document and Review Your Grounding System
Once the grounding system for your metal building is installed and tested, it’s essential to document every aspect of the setup. Create a detailed record that includes diagrams of the installation layout, specifications of materials used (such as wire gauge and length, type of ground rods, and connectors), and details of the initial testing results. This documentation serves multiple purposes: it acts as a reference for future maintenance or upgrades, provides evidence of compliance with local codes, and aids in troubleshooting potential issues. Regularly review this documentation to ensure that any changes or updates to the system are recorded promptly, maintaining an up-to-date overview of your grounding infrastructure.
Step 8. Educate Personnel on Grounding System Operations
Proper education and training of personnel involved with the metal building’s electrical systems are crucial for maintaining safety and ensuring correct system operation. Conduct training sessions to familiarize staff with the layout and function of the grounding system. Education should cover the purpose of grounding, how to recognize signs of grounding system failure, and the steps to take in the event of an electrical fault. Personnel should also be informed about the ongoing maintenance procedures and who to contact if issues arise. This knowledge will empower individuals to participate in the safe management of the building’s electrical infrastructure, minimizing risks and enhancing overall safety.
Step 9. Regularly Update Safety Protocols
As part of maintaining your metal building’s grounding system, it’s vital to regularly update safety protocols in alignment with industry standards and technological advancements. Review existing safety measures in light of new regulations and best practices to ensure they remain comprehensive and practical. Conduct periodic audits to identify potential gaps or improvements within the current safety framework. Engaging with experts or safety consultants can provide valuable insights for enhancing these protocols. Additionally, incorporate feedback from personnel interacting with the electrical systems daily, as their practical experience can highlight areas needing attention.
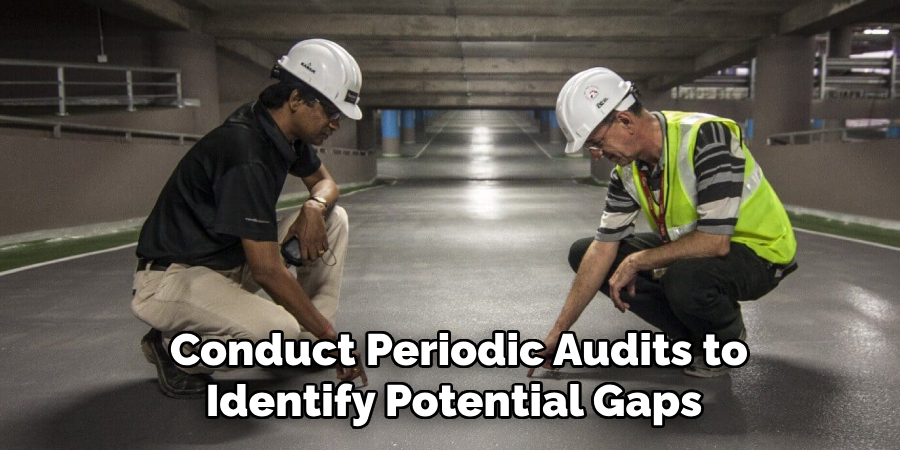
Following these steps ensures that your metal building’s grounding system is safe, effective, and compliant with industry standards.
Conclusion
How to ground a metal building is a critical component for ensuring both safety and functionality of the building’s electrical infrastructure.
Throughout this guide, we have explored essential steps, including installing ground rods, testing and verifying systems, and maintaining the grounding setup. Building owners can significantly reduce the risk of electrical faults by understanding the importance of these measures, implementing routine checks, and upgrading systems when necessary. Moreover, thorough documentation and staff education are vital in maintaining an effective grounding system.
Ensuring all procedures are aligned with the latest safety standards and regulations is not just about compliance but about fostering a secure environment for personnel and equipment.
Edmund Sumlin is a skilled author for Metal Fixes, bringing 6 years of expertise in crafting a wide range of metal fixtures. With a strong background in metalwork, Edmund’s knowledge spans various types of fixtures, from decorative pieces to functional hardware, blending precision with creativity. His passion for metalworking and design has made him a trusted resource in the industry.
Professional Focus:
- Expert in Metal Fixtures : Edmund aesthetic specializes in creating durable and innovative metal fixtures, offering both appeal and functionality. His work reflects a deep understanding of metalworking techniques and materials.
- Sustainability Advocate : He is dedicated to using sustainable practices, ensuring that every fixture is crafted with eco-friendly methods while maintaining high-quality standards.
In his writing for Metal Fixes, Edmund provides valuable insights into the latest trends, techniques, and practical advice for those passionate about metal fixtures, whether they are professionals or DIY enthusiasts. His focus on combining artistry with engineering helps others discover the true potential of metal in design.