Are you looking to create some cool metal designs by bending metal sheets? Look no further! Here we will discuss the steps on how to heat and bend metal, as well as some safety precautions you should take.
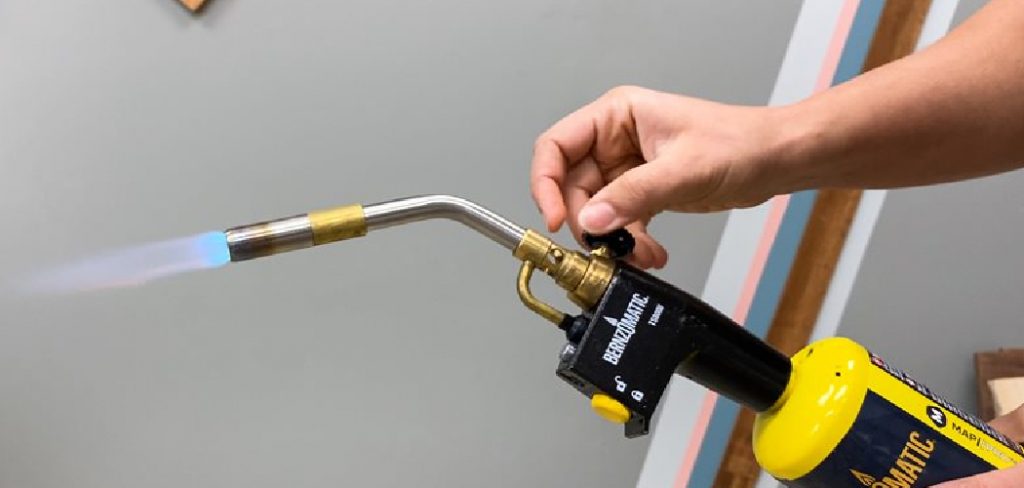
Bending metal is fundamental in various industries, from construction to art. The process involves heating the metal until it becomes malleable and can be bent into the desired shape without breaking. Understanding the properties of different metals and the appropriate heating techniques is crucial for achieving precise results.
This guide will provide an overview of the tools needed, the types of metal suitable for bending, and step-by-step instructions on safely and efficiently heating and bending metal. Whether you’re a seasoned professional or a hobbyist, mastering this technique can open up creative possibilities.
What Will You Need?
Before we dive into heating and bending metal, let’s ensure you have all the necessary tools and materials.
- Metal: The type of metal will depend on your project and desired outcome. Generally, malleable metals at room temperature, such as aluminum, copper, and brass, are suitable for bending.
- Heat Source: A heat source is essential for softening the metal. This can be a torch, forge, or furnace.
- Protective Gear: Safety should always be a top priority when working with hot metal. Wear protective gear like heat-resistant gloves, safety glasses, and closed-toe shoes.
- Vice or Clamp: A vice or clamp holds the metal in place while heating and bending.
- Hammers: Depending on your project, you may need a variety of hammers to shape and form the metal.
- Anvil or Metal Block: An anvil or metal block provides a solid surface for hammering and shaping the heated metal.
- Measuring Tools: Accurate measurements are essential for precise bends. Have a ruler, protractor, and other measuring tools handy.
9 Easy Steps on How to Heat and Bend Metal
Step 1. Choose the Right Metal:
Selecting the appropriate metal for your project is crucial, as different metals exhibit varying malleability and strength. Consider factors such as the thickness, hardness, and ultimate purpose of your finished piece. For instance, softer metals like aluminum and copper are suitable for projects requiring intricate bends and shapes due to their flexibility.
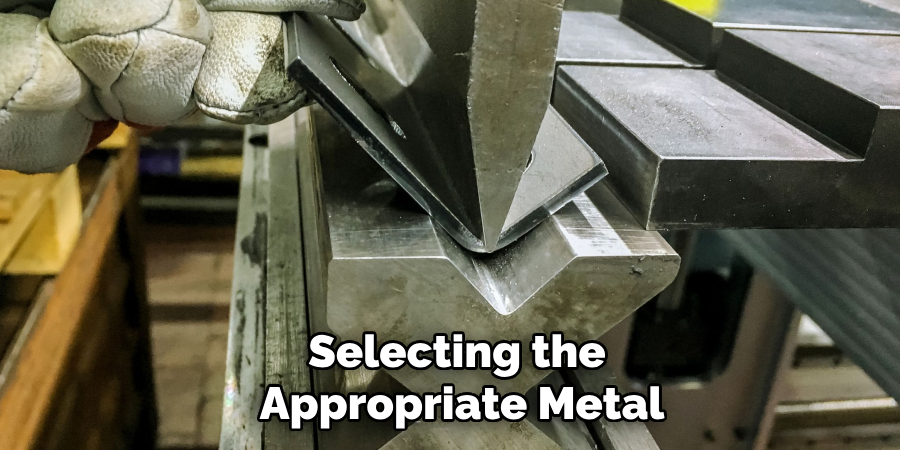
On the other hand, if your project needs to withstand substantial stress or weight, you may opt for more vital metals, considering that they may require more heat and effort to bend.
Additionally, consider the metal’s melting point and how it interacts with your available heat source, ensuring you can achieve the desired temperature for adequate bending. Understanding these characteristics beforehand will help avoid potential issues during the bending process, ensuring the smooth and efficient execution of your creative vision.
Step 2. Set Up Your Workspace:
Creating a safe and organized workspace is vital when working with metal. Begin by clearing the area of any flammable materials and ensuring you have adequate ventilation to deal with any fumes produced during the heating process.
Arrange all necessary tools and materials within easy reach, including your heat source, vice or clamp, and protective gear. It’s essential to have a designated spot for cooling the heated metal, such as a bucket of water or a metal cooling rack. Consider placing a fire extinguisher nearby as a precautionary measure.
A well-prepared workspace promotes safety and facilitates efficiency and precision in your metalworking projects.
Step 3. Secure the Metal Piece:
Once your workspace is set up and you have selected the suitable metal for your project, it’s time to secure the metal piece for heating. Use a clamp or vice to firmly hold the metal, ensuring it won’t slip or move during the heating and bending. Position the metal so that the bent area is accessible and unsupported, preventing any obstruction when you’re ready to apply heat.
Properly securing your metal is essential to maintain safety and accuracy as you proceed to heat and eventually bend the metal into its desired shape. Ensure the vice or clamp is tightened sufficiently, taking care not to damage the metal surface, and you’re ready to move on to the next steps in your project.
Step 4. Heat the Metal:
With the metal securely in place, the next step is to heat it to the appropriate temperature for bending. Using your chosen heat source, such as a torch or forge, apply heat evenly across the section of the metal you intend to bend. The key is to maintain a consistent temperature to ensure uniform malleability.
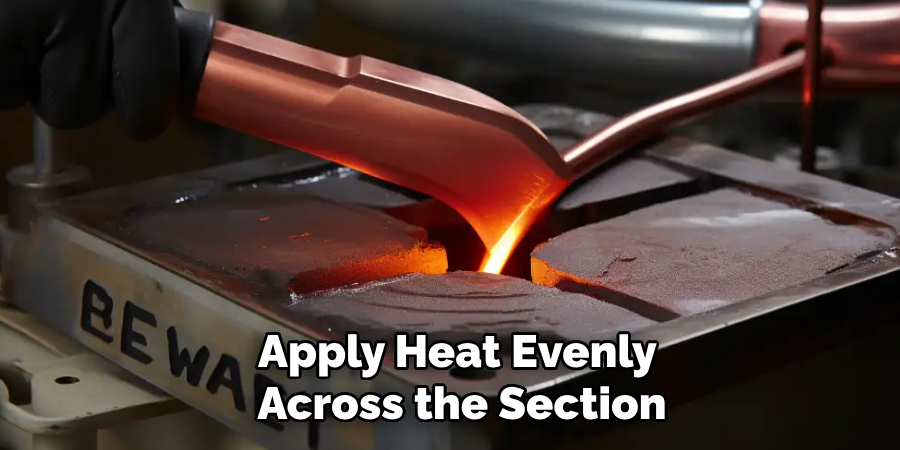
Keep an eye on the color of the metal; a reddish glow often indicates that it has reached the necessary temperature for bending. Be cautious not to overheat, as this can weaken the metal or cause it to melt. Continue applying heat until the metal becomes sufficiently pliable and malleable for bending.
Always use protective gear during this process to prevent burns or injuries. Once the metal is ready, carefully proceed to the bending step to shape it according to your project requirements.
Step 5. Bend the Metal:
Once the metal reaches the required heat and malleability level, carefully bend it into the desired shape. Applying steady pressure to manipulate the heated metal using appropriate tools, such as hammers or bending jigs.
For accurate results, follow the pre-measured angles and curves determined earlier. Take your time to ensure precision, as hurried or excessive force can lead to unwanted deformations or fractures in the metal.
If the metal begins to cool and becomes difficult to bend, reapply the heat following the same careful approach. Patience and consistent pressure will yield the best outcomes, allowing you to shape the metal effectively and bring your creative vision to life.
Step 6. Cool the Metal:
After successfully bending the metal to the desired shape, it’s crucial to cool it properly to set the bend and ensure it retains its new form. Carefully move the heated metal to the designated cooling area, such as a bucket of water or a metal cooling rack. Submerge or place the metal in the cooling medium, allowing it to cool evenly and gradually.
This step is vital to avoid introducing stress or cracks in the metal caused by rapid temperature changes. Depending on the type of metal and thickness, cooling times may vary. Be sure to handle the metal with protective gloves even after cooling, as it may still be warm. Proper cooling solidifies the results of your work, ensuring the stability and durability of your project.
Step 7. Finish and Polish the Metal:
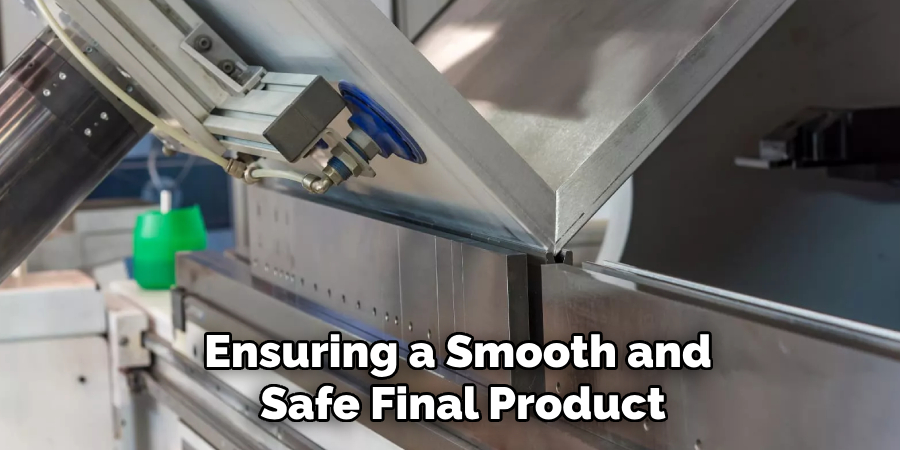
Once the metal has completely cooled and you have inspected it for any necessary adjustments, it’s time to finish and polish your project. This step involves smoothing out rough edges, eliminating surface imperfections, and achieving the desired finish for aesthetic or functional purposes.
Begin by using files or sandpaper to gently remove burrs and sharp edges, ensuring a smooth and safe final product. Depending on the type of metal and your project requirements, you may also opt for mechanical or chemical polishing techniques to enhance the metal’s shine and appearance.
Finishing touches not only improve the look of the metal but also contribute to its durability and resistance to corrosion.
Step 8. Apply a Protective Coating:
To extend the longevity and maintain the appearance of your metalwork, consider applying a protective coating once the finishing touches are complete. This step helps shield the metal from environmental factors such as moisture, air, and chemicals that can lead to corrosion or tarnishing over time.
Depending on your project’s needs and the type of metal, options for protective coatings include paint, lacquer, wax, or a specialized metal sealant. Choose a coating suitable for the intended use of your project—whether it’s for indoor or outdoor exposure.
Ensure the metal surface is clean and dust-free before application to achieve an even and effective layer. Applying a protective coating enhances the metal’s durability and ensures it maintains its aesthetic appeal for years to come.
Step 9. Inspect and Maintain the Metalwork:
The final step in your metalworking project is to conduct a thorough inspection and establish a maintenance routine for your finished piece. Begin by examining the metalwork for any imperfections or unexpected outcomes that might have occurred during the creation process.
Look for scratches, uneven sections, or incomplete coatings requiring touch-ups. Regular maintenance is crucial to preserve the integrity and appearance of your metalwork over time. Depending on the type of metal and its exposure to different environmental conditions, schedule periodic cleanings and reapplications of protective coatings to prevent corrosion and wear.
By following these nine essential steps, you can successfully bend and shape metal for a variety of projects.
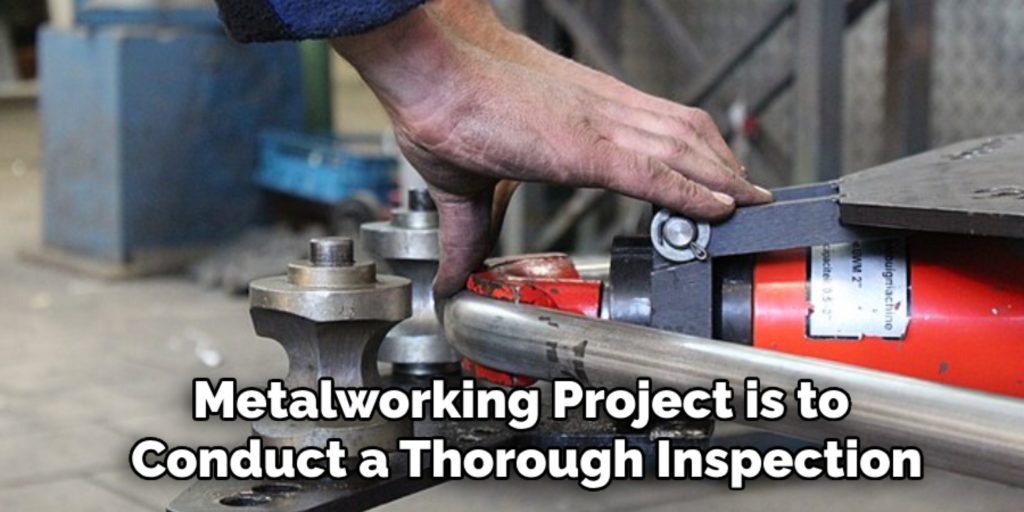
Conclusion
How to heat and bend metal is an intricate process that requires careful attention to detail, the right equipment, and a methodical approach.
You ensure precision and safety throughout the procedure by following the outlined steps—selecting the right metal, preparing your work area, applying heat evenly, and using appropriate tools for bending.
Cooling, finishing, and protecting the metal further enhance the quality and longevity of your project. Additionally, regular inspections and maintenance are key to preserving the integrity of your metalwork.
With practice and patience, mastering these techniques allows you to transform raw metal into finely crafted pieces, highlighting both technical skill and creativity.
Edmund Sumlin is a skilled author for Metal Fixes, bringing 6 years of expertise in crafting a wide range of metal fixtures. With a strong background in metalwork, Edmund’s knowledge spans various types of fixtures, from decorative pieces to functional hardware, blending precision with creativity. His passion for metalworking and design has made him a trusted resource in the industry.
Professional Focus:
- Expert in Metal Fixtures : Edmund aesthetic specializes in creating durable and innovative metal fixtures, offering both appeal and functionality. His work reflects a deep understanding of metalworking techniques and materials.
- Sustainability Advocate : He is dedicated to using sustainable practices, ensuring that every fixture is crafted with eco-friendly methods while maintaining high-quality standards.
In his writing for Metal Fixes, Edmund provides valuable insights into the latest trends, techniques, and practical advice for those passionate about metal fixtures, whether they are professionals or DIY enthusiasts. His focus on combining artistry with engineering helps others discover the true potential of metal in design.