Installing threaded inserts in metal is a crucial technique for creating durable and reusable threads in materials that are otherwise too soft to hold a thread effectively.
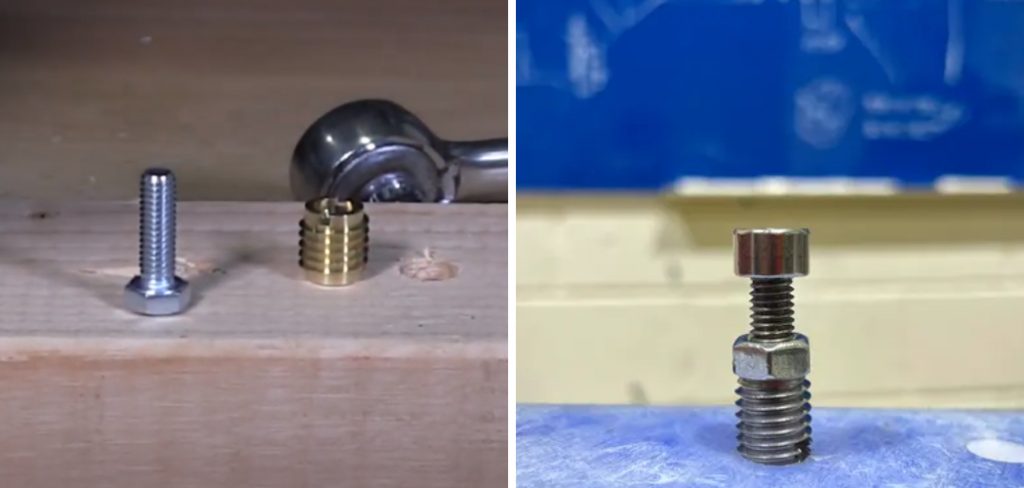
This process is widely used in various industries, including automotive, aerospace, and manufacturing, where strong, reliable connections are essential. This guide explores the key aspects of how to install threaded inserts in metal.
Threaded inserts, often made from stainless steel or brass, provide a robust solution for reinforcing threads in aluminum, magnesium, and other metals.
The installation process involves drilling a hole, tapping it to the required size, and then inserting the threaded insert using specialized tools. This ensures a secure fit and allows for the repeated removal and replacement of screws or bolts without damaging the base material.
Understanding the types of threaded inserts, such as helical and rivet nuts, and mastering the installation techniques can significantly enhance the quality and longevity of your projects.
This guide will walk you through the steps and best practices for installing threaded inserts in metal, ensuring strong and precise threads every time.
Understanding Threaded Inserts
Threaded inserts are small cylindrical metal components designed to provide strong and reliable threads in softer or weaker materials that might not hold up to continuous use. There are several types of threaded inserts, each suited for different applications and materials.
- Helical Inserts: Also known as coil inserts, these are wire coils that are wound into a helical shape. They are typically used in metals like aluminum and magnesium and help distribute the load more evenly. This reduces the risk of stress concentrations, resulting in a longer lifespan for the threads.
- Rivet Nuts: Rivet nuts, or rivnuts, are tubular rivets with internal threads. They are inserted into a pre-drilled hole and can be installed using a special tool that deforms the unthreaded portion to lock the insert in place. Rivet nuts are commonly used in thin-walled materials where there is insufficient thickness to support a thread.
- T-Nuts: These are T-shaped nuts that can be embedded into materials to create a flush, threaded surface. T-nuts are often used in woodworking but can also be applied in metalworking for certain applications.
- Press-Fit Inserts: As the name suggests, these inserts are pressed into place and do not require threading the hole beforehand. They are designed with knurled or grooved exteriors to grip firmly into the base material, making them ideal for rapid installation in high-volume production.
10 Methods How to Install Threaded Inserts in Metal
1. Selecting the Appropriate Threaded Insert
Before installation, it is essential to select the appropriate threaded insert for your specific application. Threaded inserts come in various types, including solid inserts, helical inserts, and self-tapping inserts.
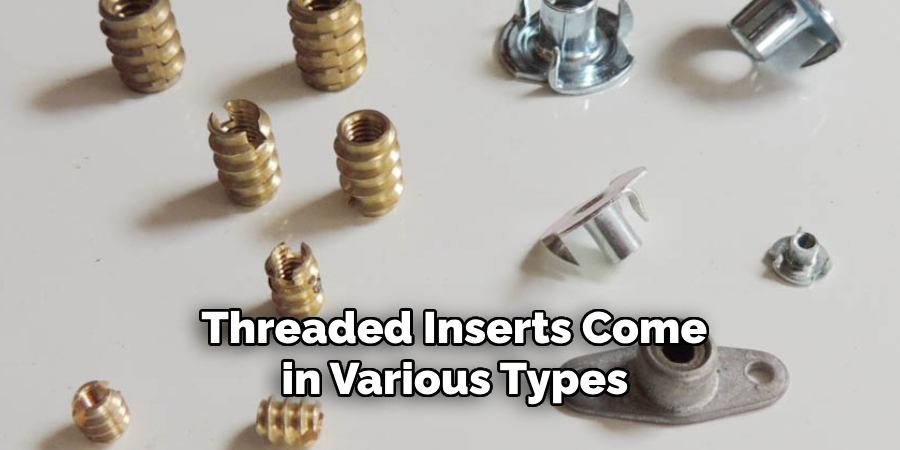
Each type is designed for different purposes and materials. Solid inserts are suitable for heavy-duty applications, helical inserts provide flexibility and vibration resistance, and self-tapping inserts are ideal for quick installations in softer metals.
Understanding the requirements of your project and the properties of the base material will guide you in choosing the right insert. Ensuring compatibility between the insert and the material is crucial for a successful installation.
2. Preparing the Installation Area
Proper preparation of the installation area is vital for ensuring a secure fit for the threaded insert. Begin by cleaning the metal surface to remove any dirt, grease, or debris. Use a wire brush or compressed air to ensure the area is free from contaminants.
If necessary, degrease the surface with a suitable solvent. For drilled holes, ensure they are free from burrs and sharp edges that could interfere with the insert. Proper preparation not only facilitates easier installation but also enhances the insert’s grip and stability, ensuring a long-lasting connection.
3. Drilling the Hole
Drilling the correct hole size is critical for the proper installation of threaded inserts. The hole diameter should match the specifications provided by the insert manufacturer.
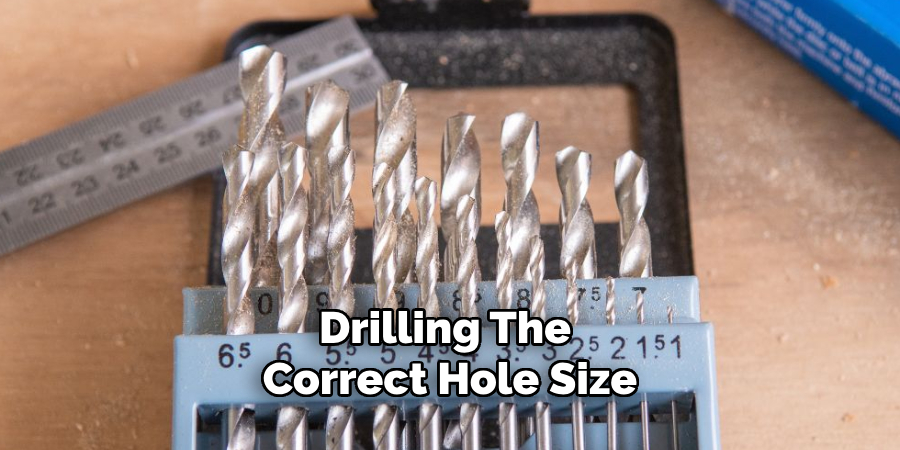
Using a drill bit that is too large or too small can compromise the insert’s effectiveness. Mark the drilling location accurately and use a center punch to create a guide point. Secure the workpiece to prevent movement and drill the hole at a consistent speed.
For deep holes, periodically withdraw the drill bit to clear chips and prevent overheating. After drilling, clean the hole thoroughly to remove any debris or metal shavings. Precise drilling ensures a snug fit and optimal performance of the threaded insert.
4. Tapping the Hole
For inserts that require tapping, such as solid or helical inserts, creating threads in the drilled hole is necessary. Select a tap that matches the insert’s external thread size. Apply cutting oil to the tap to reduce friction and heat. Begin tapping the hole by turning the tap slowly and steadily.
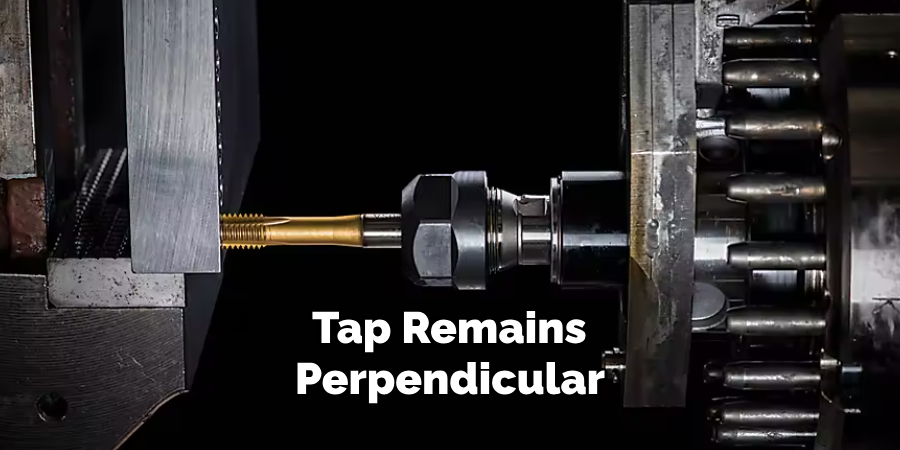
Ensure the tap remains perpendicular to the surface to avoid misalignment. Periodically reverse the tap to break and clear chips, preventing blockages and damage to the threads.
Continue until the hole is fully tapped. Properly tapped threads provide a strong grip for the insert, ensuring it remains securely in place.
5. Using an Insertion Tool
An insertion tool is often required for installing threaded inserts, especially for helical or solid inserts. These tools are designed to apply the necessary force and alignment for a secure installation. For helical inserts, use a dedicated installation tool that engages the insert’s tang.
Align the tool with the tapped hole and turn it to thread the insert into place. For solid inserts, use a press or manual insertion tool to apply consistent pressure. Ensure the insert is flush with or slightly below the surface. Using the correct insertion tool prevents damage to the insert and ensures a precise fit.
6. Using Thread Locking Compound
In applications where vibration or movement could loosen the threaded insert, using a thread locking compound provides additional security.
Apply a small amount of the compound to the external threads of the insert before installation. This adhesive helps to secure the insert in place, preventing it from backing out under stress. Be sure to use a compound compatible with the materials involved and the application’s temperature range.
Allow the compound to cure according to the manufacturer’s instructions. This method enhances the durability and reliability of the threaded connection, particularly in dynamic environments.
7. Installing Self-Tapping Inserts
Self-tapping inserts are designed to cut their own threads as they are driven into the material, eliminating the need for pre-tapping. To install self-tapping inserts, drill a pilot hole slightly smaller than the insert’s outer diameter. Align the insert with the hole and use a driver tool to screw it into place.
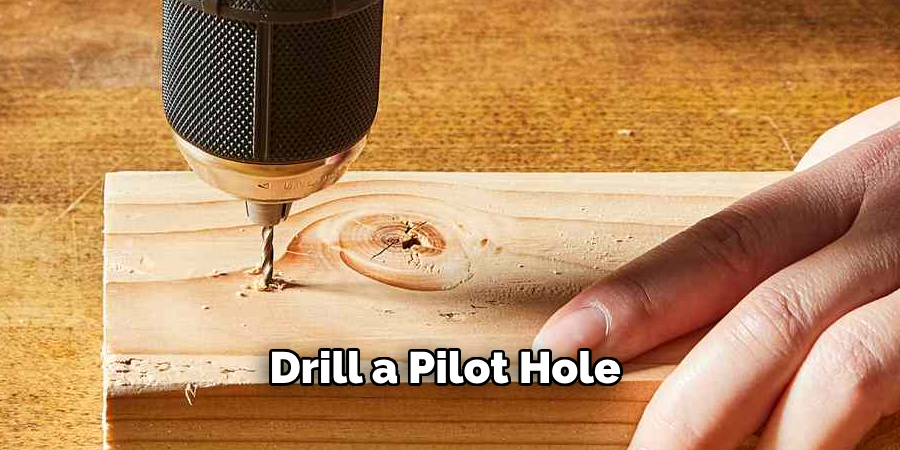
Apply steady pressure and maintain alignment to ensure the insert cuts threads evenly. This method is quick and effective, especially for softer metals where traditional tapping might be less effective. Self-tapping inserts provide strong threads and are ideal for field repairs or quick installations.
8. Using Heat for Installation
For certain types of threaded inserts, particularly those made of softer metals like aluminum, using heat can facilitate easier installation.
Heat causes the metal to expand slightly, making it easier to insert the threaded component. Use a heat gun or torch to gently warm the area around the hole. Once heated, quickly insert the threaded insert using an appropriate tool.
As the metal cools, it will contract, creating a tight grip around the insert. This method is particularly useful for tight tolerance applications or when working with materials that are difficult to machine.
9. Ensuring Proper Depth Control
Proper depth control is essential to ensure the threaded insert is seated correctly. For critical applications, use a depth stop on your drill or tapping tool to maintain consistent hole depth.
During installation, check the insert’s position frequently to avoid over-insertion or insufficient seating. For solid inserts, use a press or manual tool with depth control features.
Ensuring the correct depth not only enhances the insert’s performance but also prevents potential damage to the surrounding material. Accurate depth control is crucial for maintaining the integrity and strength of the threaded connection.
10. Verifying and Testing the Installation
After installing the threaded insert, it’s important to verify and test the installation to ensure it meets the required standards. Visually inspect the insert for proper alignment and seating.
Use a thread gauge to check the internal threads for accuracy. For critical applications, perform pull-out and torque tests to verify the insert’s strength and stability.
Document the results to ensure compliance with specifications and quality standards. Verifying and testing the installation ensures the threaded insert will perform reliably under operational conditions, providing confidence in the connection’s durability and strength.
Conclusion
Installing threaded inserts in metal requires careful preparation, the right tools, and precise techniques.
From selecting the appropriate insert and preparing the installation area to using insertion tools and verifying the installation, each step is crucial for achieving a strong and reliable threaded connection. Thanks for reading our blog post on how to install threaded inserts in metal! We hope you found it helpful and informative.
Edmund Sumlin is a skilled author for Metal Fixes, bringing 6 years of expertise in crafting a wide range of metal fixtures. With a strong background in metalwork, Edmund’s knowledge spans various types of fixtures, from decorative pieces to functional hardware, blending precision with creativity. His passion for metalworking and design has made him a trusted resource in the industry.
Professional Focus:
- Expert in Metal Fixtures : Edmund aesthetic specializes in creating durable and innovative metal fixtures, offering both appeal and functionality. His work reflects a deep understanding of metalworking techniques and materials.
- Sustainability Advocate : He is dedicated to using sustainable practices, ensuring that every fixture is crafted with eco-friendly methods while maintaining high-quality standards.
In his writing for Metal Fixes, Edmund provides valuable insights into the latest trends, techniques, and practical advice for those passionate about metal fixtures, whether they are professionals or DIY enthusiasts. His focus on combining artistry with engineering helps others discover the true potential of metal in design.