Joining square tubing without welding may sound like a daunting task, but it is actually an easier process than you might think. If you’re looking for ways to join pieces of square tubing together quickly and easily, then this article is for you! We’ll explore the various methods and materials available that allow you to connect your square tubing without having to weld.
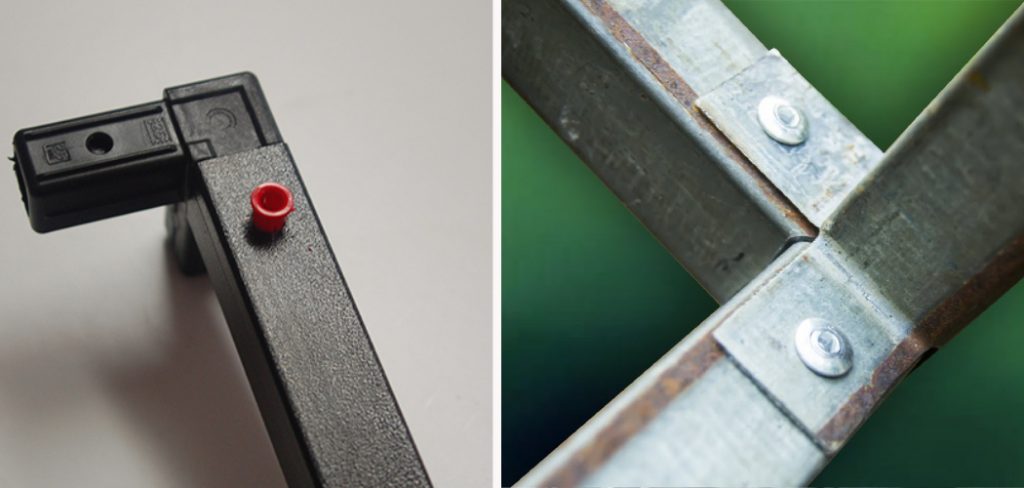
From specialized adhesives to clamps and fittings, there are several options at your disposal that will ensure a secure connection between pipes – making the entire process worry-free. Read on how to join square tubing without welding as we break down all of these joints in detail so that you can determine which one will best suit your needs!
Advantages of Joining Square Tubing Without Welding
Before we get into the specific methods, let’s quickly touch upon the advantages of joining square tubing without welding. These include:
- No need for specialized equipment or training
- Less time and effort required
- Reduced risk of damaging the material being joined
- Can easily be reversed if needed
Now, let’s explore some of the methods you can use to join square tubing without welding.
Needed Tools and Materials
Before we dive into the various methods for joining square tubing without welding, let’s first go through the tools and materials you will need. These include:
- Square Tubing
- Adhesives or Epoxy Resins
- Clamps or Fittings
- Bolts or Screws
- Drill (optional)
Now that we have a basic understanding of what we need, let’s take a closer look at the different methods for joining square tubing without welding.
10 Step-by-step Guidelines on How to Join Square Tubing Without Welding
Step 1: Measure and Cut the Square Tubing
The first step in joining square tubing without welding is to measure and cut your desired pieces of tubing. Use a measuring tape and a cutting tool such as a hacksaw to ensure precise measurements. It is important to make accurate cuts to ensure a good fit and secure joint. You can also have your local hardware store cut the tubing for you if you’re not confident in your own cutting abilities.
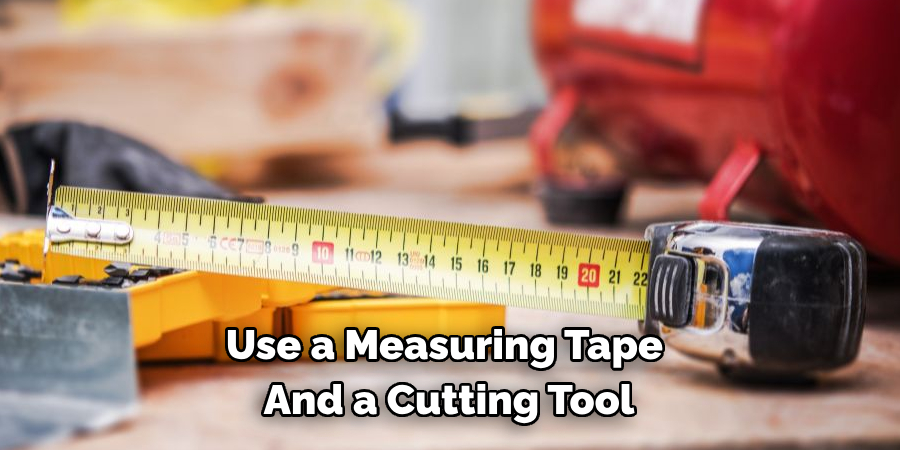
Step 2: Sand the Edges of the Cut Square Tubing
After cutting, use sandpaper to smooth out any rough edges or burrs on the cut tubing. This will create a clean surface for the adhesive to bond to. But, if you’re using pre-cut tubing, this step can be skipped. You should also clean the surface of the tubing with a degreaser to remove any oils or debris that could affect the adhesive bond. It’s important to have a clean surface for the adhesive to properly bond to. You can also use a wire brush to roughen the surface of the tubing for better adhesion.
Step 3: Choose Your Adhesive
There are various adhesives available that are specifically designed for bonding metal, such as square tubing. Some common options include epoxy resins and specialized metal adhesives. It’s important to choose an adhesive that is suitable for your specific application and has a strong bond strength. You can consult with a professional or do some research to determine the best adhesive for your project.
Step 4: Apply Adhesive
Once you have chosen your adhesive, it’s time to apply it to the surfaces that will be joined. Follow the manufacturer’s instructions for applying the adhesive, and make sure to evenly coat both surfaces. It’s important to work quickly as many adhesives have a short working time. It’s also recommended to apply the adhesive in a well-ventilated area and wear proper protective gear.
Step 5: Join the Surfaces
On a flat surface, carefully join the two pieces of square tubing together. Make sure they are aligned properly and apply pressure to ensure a tight bond. You can use clamps or weights to hold the pieces in place while the adhesive dries. This will help to prevent any movement or shifting of the tubing. Although the adhesive may have a quick dry time, it’s recommended to leave it overnight for complete bonding.
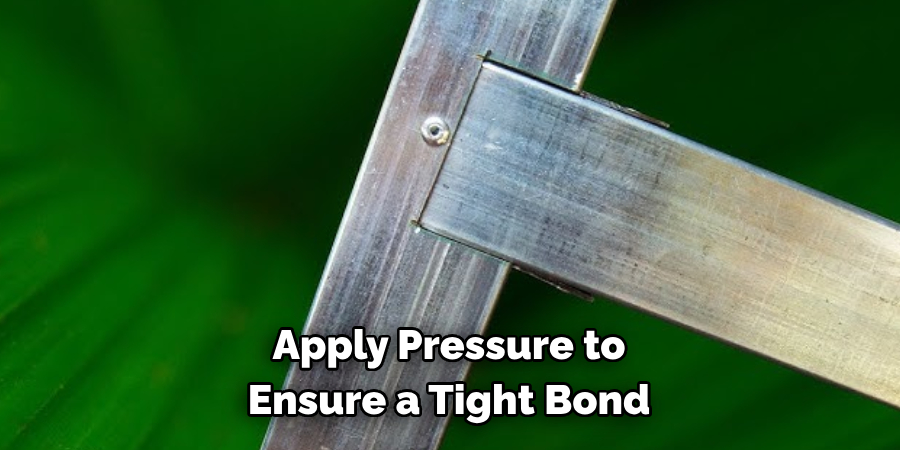
Step 6: Allow Time for Adhesive to Dry
Different adhesives have different drying times, so make sure to check the manufacturer’s instructions for the recommended drying time. It’s important to be patient and not disturb the tubing until the adhesive has fully cured. Moving or disturbing the joint too soon can cause it to weaken or fail. You can use a timer or set a reminder to ensure that you give the adhesive enough time to dry properly.
Step 7: Use Fittings or Clamps for Added Strength
If you want extra strength and stability, you can also use fittings or clamps in addition to the adhesive. This will provide added support and prevent any movement of the tubing. Just make sure to choose fittings or clamps that are suitable for the type and size of square tubing you are using. It’s also important to properly tighten and secure the fittings or clamps. You can use a wrench or pliers for this step.
Step 8: Use Bolts or Screws as an Alternative
If your project requires a more permanent joint, you can also use bolts or screws in addition to adhesives and fittings. This will create a stronger and more durable connection but will also require drilling holes in the tubing. Make sure to choose bolts or screws that are suitable for metal applications and have the proper size and thread count. It’s also important to use washers and nuts to secure the bolts or screws in place.
Step 9: Fill any Gaps with Epoxy Resin (Optional)
If there are any gaps or spaces between the joined pieces of tubing, you can use epoxy resin to fill them in. This will create a seamless connection and add extra strength to the joint. Make sure to choose an epoxy resin that is suitable for metal applications and follow the manufacturer’s instructions for proper application. You can also sand down any excess epoxy resin once it has dried for a smoother finish.
Step 10: Test and Inspect
Once your joint has fully dried and cured, it’s important to test its strength and inspect for any weak points or imperfections. You can do this by applying pressure or weight to the joint and checking for any movement or signs of failure. If the joint is solid and secure, then congratulations, you have successfully joined square tubing without welding!
Following these step-by-step guidelines on how to join square tubing without welding, you can easily join square tubing without the need for welding. Remember to always choose the appropriate tools and materials for your specific project and follow safety precautions when working with adhesives and metal. With practice and patience, you can create strong and durable joints using these methods. Happy building!
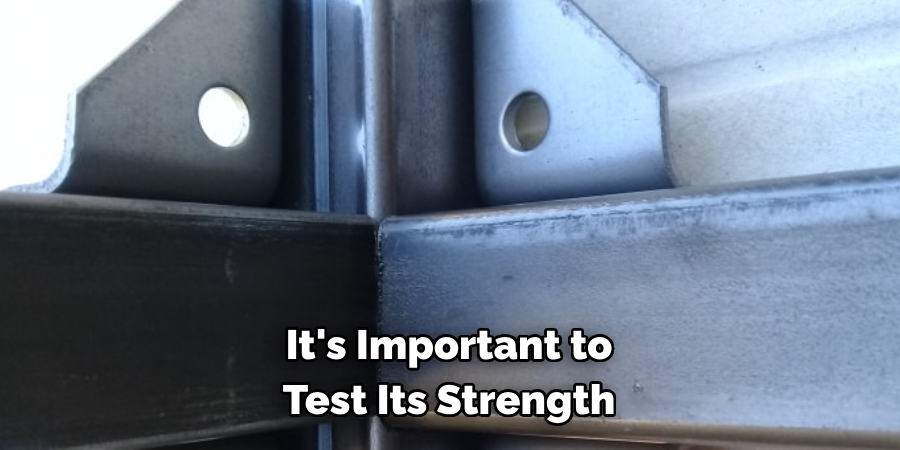
Frequently Asked Questions
Q: Is It Possible to Join Square Tubing Without Welding?
A: Yes, it is possible to join square tubing without welding. There are several methods such as using adhesives, fittings, bolts or screws that can be used to create a secure joint between two pieces of square tubing.
Q: What Adhesive Should I Use to Join Square Tubing?
A: There are various adhesives available specifically designed for bonding metal, such as square tubing. Some common options include epoxy resins and specialized metal adhesives. It’s important to choose an adhesive that is suitable for your specific application and has a strong bond strength.
Q: Is It Safe to Use Adhesives for Joining Square Tubing?
A: Yes, it is safe to use adhesives for joining square tubing as long as you follow the manufacturer’s instructions and proper safety precautions. This includes wearing protective gear and working in a well-ventilated area.
Q: How Long Does It Take for Adhesive to Dry?
A: The drying time for adhesive can vary depending on the type and brand, so it’s important to check the manufacturer’s instructions. It’s also recommended to wait at least 24 hours before putting any weight or pressure on the joined tubing to ensure a strong bond.
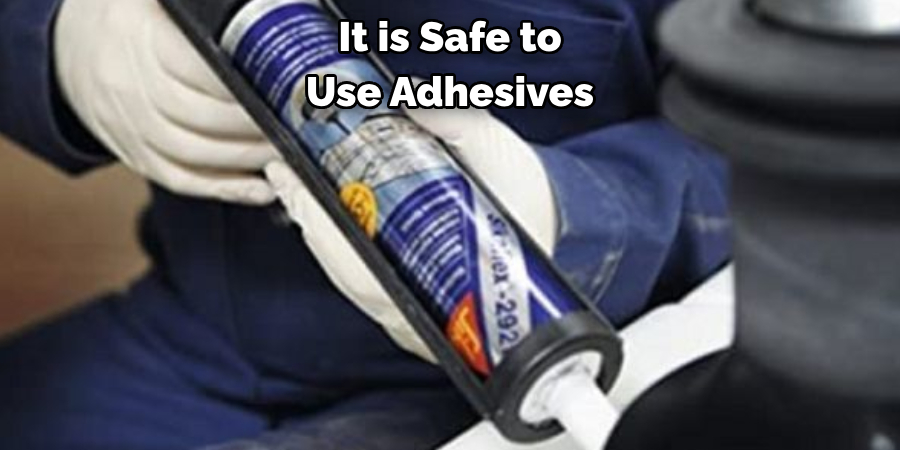
Conclusion
In conclusion, joining square tubing without welding is a simple and viable solution for a variety of practical applications. If you are looking to make structural connections with square tubing, it’s worth considering this alternative. With rivets, not only is the process quicker and cleaner, but more importantly it is incredibly safe. It requires minimal setup time and there are no extreme toxicity risks involved either in the application or the materials themselves, meaning that it has become increasingly popular over time.
Furthermore, on how to join square tubing without welding, you have access to a range of sizes so that your setup will be tailored precisely to your project’s needs. Make sure to take advantage of all the options available with square-tube riveting and dial in on the perfect solution for your upcoming project!
Edmund Sumlin is a skilled author for Metal Fixes, bringing 6 years of expertise in crafting a wide range of metal fixtures. With a strong background in metalwork, Edmund’s knowledge spans various types of fixtures, from decorative pieces to functional hardware, blending precision with creativity. His passion for metalworking and design has made him a trusted resource in the industry.
Professional Focus:
- Expert in Metal Fixtures : Edmund aesthetic specializes in creating durable and innovative metal fixtures, offering both appeal and functionality. His work reflects a deep understanding of metalworking techniques and materials.
- Sustainability Advocate : He is dedicated to using sustainable practices, ensuring that every fixture is crafted with eco-friendly methods while maintaining high-quality standards.
In his writing for Metal Fixes, Edmund provides valuable insights into the latest trends, techniques, and practical advice for those passionate about metal fixtures, whether they are professionals or DIY enthusiasts. His focus on combining artistry with engineering helps others discover the true potential of metal in design.