Leveling a lathe is a critical step for ensuring accurate machining results.
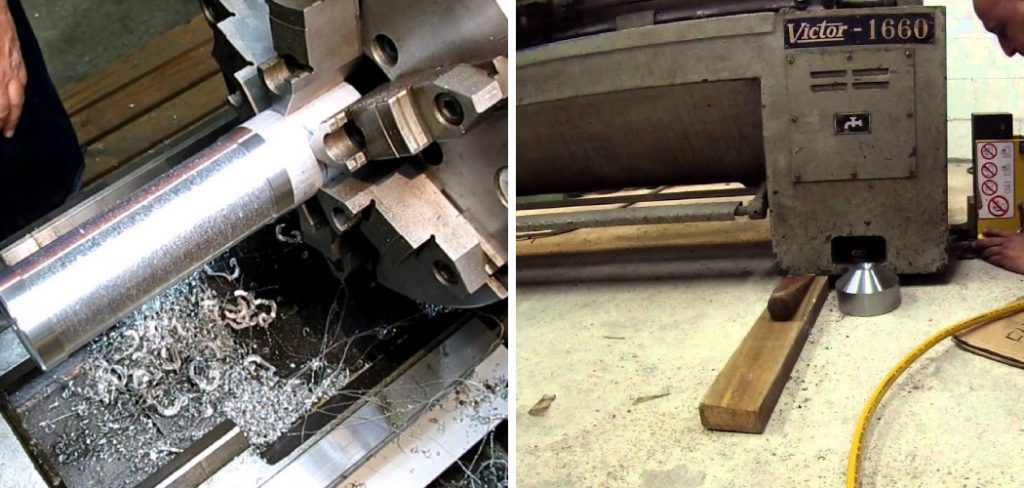
When a lathe is not properly leveled, it can lead to uneven cuts, increased tool wear, and compromised precision, ultimately affecting the quality of your workpieces. Understanding how to level a lathe correctly can save you time, money, and frustration in the long run.
The process involves several key steps: choosing an appropriate location, gathering necessary tools, adjusting leveling pads or feet, and confirming the lathe’s stability and alignment. During this process, it’s essential to observe safety precautions such as ensuring the lathe is powered off and cool and keeping the workspace clear.
By following these guidelines, you will achieve a properly leveled lathe, thus enhancing the machine’s performance, extending its life, and ensuring your projects meet high precision standards.
Understanding Lathe Leveling
A lathe must be level to ensure the precision and quality of machining operations. When a lathe is not correctly leveled, it can cause the machine bed to twist or warp slightly, which may lead to inconsistencies in the workpiece dimensions and surface finish.
Improper leveling can also result in uneven wear on the lathe’s components, significantly reducing the life of the cutting tools and the lathe itself. This misalignment affects the accuracy of cuts, potentially leading to costly mistakes and material waste.
There are various types of lathes, such as engine lathes, turret lathes, and CNC lathes, each with its own specific leveling requirements.
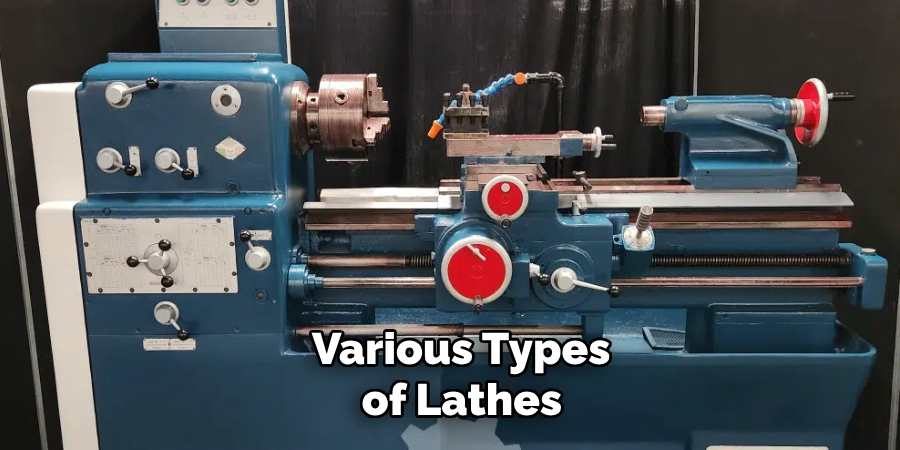
Common methods for leveling a lathe include using a precision spirit level to check and adjust the lathe bed’s longitudinal and transverse alignment.
Shims can be placed under the lathe feet if needed to achieve the perfect level. Some modern lathes may have adjustable leveling pads that make this process easier.
Regardless of the method, the goal is to ensure that the lathe bed remains flat and true, enabling the machine to produce accurate and repeatable results. Properly leveled lathes improve machining performance and extend the machine’s operational life.
Tools Needed
Leveling a lathe requires specific tools to achieve precision and accuracy. The essential tools you’ll need include a precision spirit level, an adjustable wrench, and shims.
The spirit level is crucial for measuring the lathe bed’s longitudinal and transverse alignment. It ensures that the bed remains perfectly horizontal, which is key for making accurate cuts.
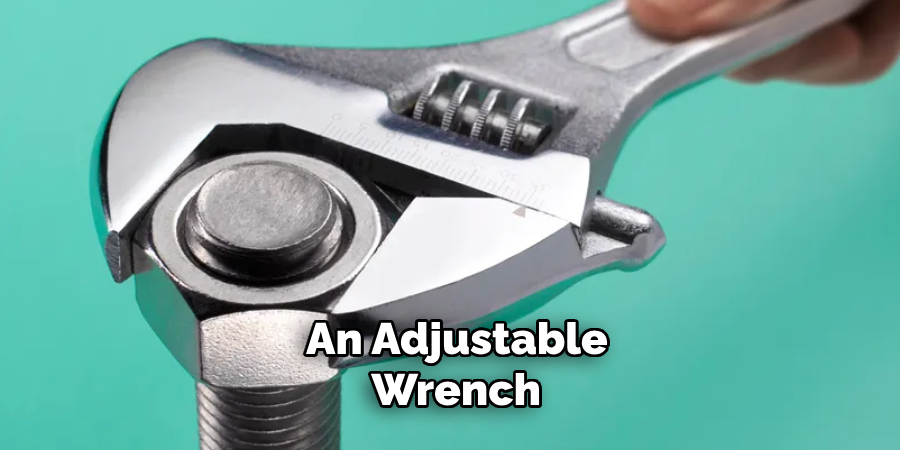
An adjustable wrench is used to adjust the lathe’s leveling pads or feet, allowing for fine-tuning of the machine’s position. Shims, small yet vital materials, are placed under the lathe’s feet to adjust and correct any discrepancies in leveling.
Using precision tools is paramount when leveling a lathe because even minor deviations can significantly impact machining quality. A high-quality spirit level can detect minute differences in the lathe bed’s alignment, enabling you to make precise adjustments.
Similarly, using a reliable adjustable wrench ensures you can securely tighten or loosen components without causing damage.
Shims, often made of durable materials like metal or plastic, provide a stable base for incremental adjustments. Employing these precise tools guarantees that your lathe will be leveled accurately, thereby enhancing its machining capabilities and prolonging its operational lifespan.
Preparation
Proper preparation is essential for effectively leveling a lathe. The first step is to choose a suitable location for the lathe. It’s important to place the lathe on a flat, stable surface to prevent any shifting or vibrations during operation, which can affect the machine’s performance and accuracy.
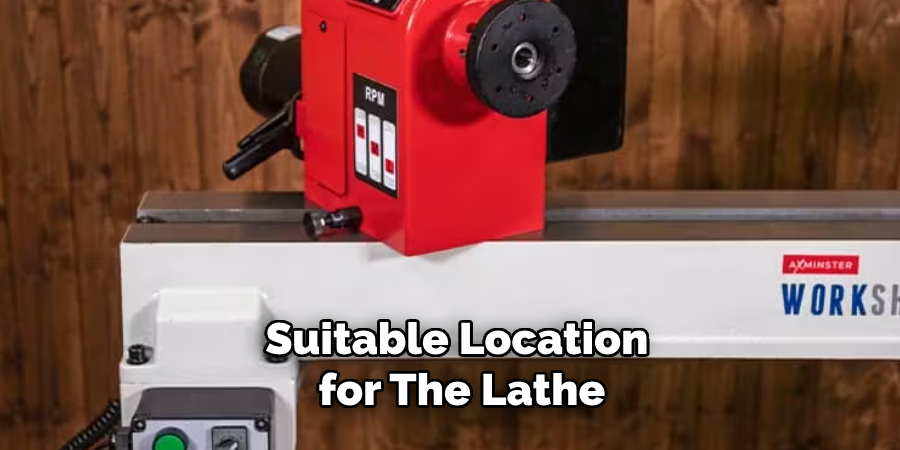
Ideally, the surface should be made of a solid material such as concrete, which offers excellent stability and minimizes the risk of movement. Avoid placing the lathe on wood or other softer materials that can compress over time, leading to misalignment.
Once you have identified an appropriate location, clear the area around the lathe to ensure unrestricted access.
This means removing any obstacles, such as tools, materials, or debris, that could impede your ability to maneuver around the lathe. Having a clean, organized workspace enhances safety and allows for more efficient adjustments and measurements. Ensure adequate lighting in the area facilitates clear visibility of the lathe bed and leveling tools.
Before beginning the leveling process, ensure the lathe is powered off and completely cool. This is crucial for your safety, as working on a powered or hot lathe poses significant risks. Switch off the power at the main supply and unplug the lathe to prevent accidental start-ups.
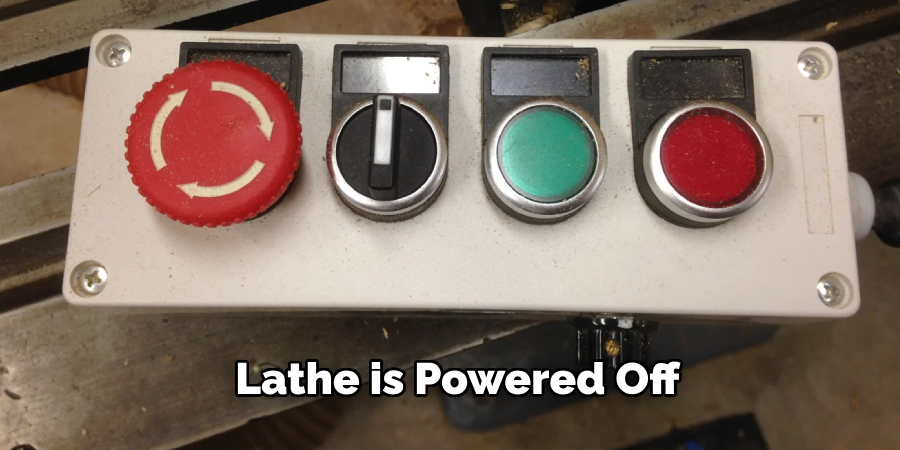
Check that all moving parts have come to a complete stop and allow sufficient time for the machine to cool down if it was recently used. Taking these precautions will help ensure a safe and effective leveling process, setting the stage for precise and accurate machining results.
How to Level a Lathe: Leveling Process
The leveling process begins with placing the precision spirit level on the lathe bed to measure its alignment. Start by positioning the level longitudinally along the length of the lathe bed.
This will help you determine if the bed is tilted forward or backward. Carefully observe the bubble in the spirit level’s vial to see if it is centered. If the bubble is offset to one side, it indicates that the lathe bed is not perfectly horizontal and adjustments are necessary.
Next, move the spirit level to a transverse position across the width of the lathe bed. This will allow you to check for any side-to-side tilt.
Again, observe the bubble and note any deviations from the center. Achieving longitudinal and transverse horizontal alignment is crucial to ensure precision in machining operations.
To make the necessary adjustments, locate the lathe feet or leveling pads. Using an adjustable wrench, turn the leveling screws or pads to raise or lower the corners of the lathe until the bubble in the spirit level is centered in both orientations. Make small, incremental adjustments and check the level frequently to avoid over-adjusting.
Sometimes, you may find that the lathe feet are insufficient to achieve perfect leveling. In such scenarios, use shims to make fine adjustments.
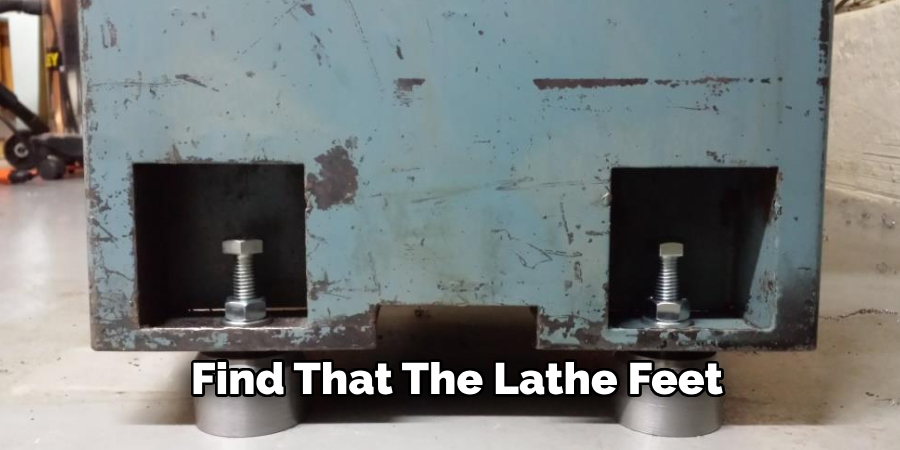
Shims are thin pieces of material that can be placed under the feet of the lathe to correct slight discrepancies in its horizontal alignment. Insert the shims under the appropriate feet and recheck the level.
Continue adjusting and adding shims as necessary until the lathe bed is perfectly level both longitudinally and transversely. This precise leveling process is essential for accurate and high-quality machining results, ensuring that the lathe operates optimally.
How to Level a Lathe: Checking and Rechecking
Verifying the lathe bed is level after adjustments is crucial to ensure accurate machining.
Once you have made initial adjustments and believe the lathe bed is leveled both longitudinally and transversely, recheck the bubble in the spirit level. Place the level in both orientations again and closely observe the bubble to confirm that it remains centered.
This double-check ensures that no mistakes were made during the initial adjustments and that the lathe bed truly is level.
If you notice any deviations, repeating the leveling process is essential. This repetition involves rechecking the lathe bed with the spirit level, adjusting the leveling screws or shims as needed, and continuously monitoring the bubble in the spirit level until it is consistently centered.
Be patient and meticulous during this step, as even minor deviations can significantly impact the quality of your machining work.
After leveling, test the lathe’s stability by gently rocking it from different angles. This gentle rocking helps identify any remaining instability that could affect machining precision. If the lathe rocks or moves, it indicates uneven contact with the surface, and further leveling adjustments are necessary.
You should consider the leveling process complete only when the lathe remains firmly stable. Ensuring both level and stability sets the stage for optimal lathe performance and precision in your projects.
Fine-tuning
Fine-tuning the lathe’s level involves making minor adjustments to achieve a perfect horizontal alignment. Start by revisiting each of the lathe’s feet or leveling pads and making slight tweaks with an adjustable wrench.
It’s important to make these adjustments incrementally to avoid overshooting the desired level. Place the precision spirit level on different sections of the lathe bed to confirm evenness across the entire surface.
Move the level longitudinally and transversely, ensuring that the bubble is consistently centered in all positions. Pay close attention to any slight deviations and make the necessary corrections.
Continue this process of fine-tuning and rechecking until the spirit level shows a perfectly centered bubble across every portion of the lathe bed.
Once this is achieved, carefully inspect all the lathe’s locking mechanisms and adjustments to ensure they are secure. Tighten any loose bolts, nuts, or screws to prevent any potential shifts during operation.
Confirm that all adjustments and shims are firmly in place and recheck the level one final time. This meticulous approach guarantees that the lathe is not only level but also stable and secure, laying the foundation for precise and high-quality machining.
Calibration and Verification
Once the lathe is level and stable, the next step is calibration and verification to ensure alignment precision. Use precision measuring tools such as dial indicators, test bars, and micrometers to check the alignment of the lathe’s components. Begin by mounting a dial indicator on the lathe’s carriage and run it along the length of the lathe bed.
This will help confirm the bed’s straightness and detect any high or low spots. Next, examine the headstock alignment using a test bar in the lathe spindle. Rotate the spindle slowly and observe the readings on a dial indicator to check for any runout.
If discrepancies are identified, recalibrate the lathe according to the manufacturer’s specifications. Refer to the lathe’s manual for specific guidelines on making these adjustments. After calibration, repeat the precision measurements to verify accuracy.
Finally, document the entire leveling and calibration process, noting the adjustments made and tools used. This record will be invaluable for future reference and maintenance, ensuring consistent machining accuracy.
Maintenance and Regular Checks
Establishing a schedule for regular lathe checks and re-leveling is paramount to maintaining optimal performance. It’s recommended that these checks be performed monthly or after completing significant machining projects.
For wear or damage, begin by cleaning and inspecting the leveling components, such as the feet, leveling pads, and shims. Dust, debris, and metal shavings can accumulate and interfere with the leveling process, so ensure all surfaces are clean and free of obstructions.
During these inspections, look for any signs of wear, corrosion, or damage on the leveling components. If any issues are found, address them promptly by replacing worn or damaged parts.
Regular maintenance not only prolongs the lifespan of the lathe but also ensures that it continues to produce accurate and high-quality results. Adhering to a consistent maintenance routine can prevent minor issues from escalating into major problems, ensuring your lathe remains in top operating condition.
Conclusion
In conclusion, understanding the importance of proper lathe leveling cannot be overstated. Following the outlined steps meticulously ensures that your “how to level a lathe” process leads to precise machining results.
Rechecking and fine-tuning the lathe bed is crucial, confirming that every adjustment yields a perfectly level surface.
Regular calibration and verification play a significant role in maintaining alignment precision, ensuring that your lathe operates at its peak performance. By adhering to a rigorous maintenance schedule, you can enhance the longevity of your lathe and the quality of your work.
Proper leveling is the foundation for accurate results and reliable machine operation, making it an essential practice for any machinist aiming for excellence. Remember, the time and effort invested in leveling your lathe will pay off in the durability and precision of your projects.
Edmund Sumlin is a skilled author for Metal Fixes, bringing 6 years of expertise in crafting a wide range of metal fixtures. With a strong background in metalwork, Edmund’s knowledge spans various types of fixtures, from decorative pieces to functional hardware, blending precision with creativity. His passion for metalworking and design has made him a trusted resource in the industry.
Professional Focus:
- Expert in Metal Fixtures : Edmund aesthetic specializes in creating durable and innovative metal fixtures, offering both appeal and functionality. His work reflects a deep understanding of metalworking techniques and materials.
- Sustainability Advocate : He is dedicated to using sustainable practices, ensuring that every fixture is crafted with eco-friendly methods while maintaining high-quality standards.
In his writing for Metal Fixes, Edmund provides valuable insights into the latest trends, techniques, and practical advice for those passionate about metal fixtures, whether they are professionals or DIY enthusiasts. His focus on combining artistry with engineering helps others discover the true potential of metal in design.