Machining alumina ceramic presents unique challenges due to its exceptional hardness and brittleness.
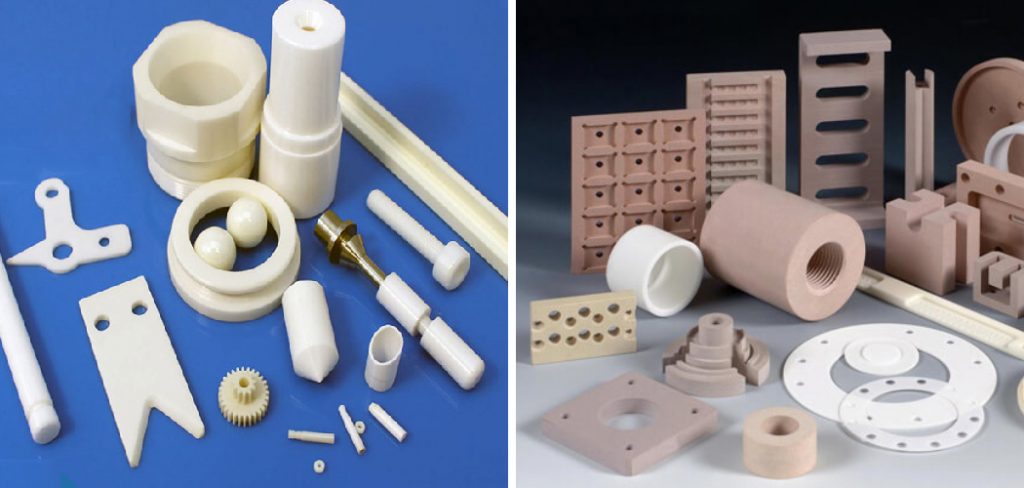
Alumina ceramics, primarily composed of aluminum oxide (Al2O3), are valued for their high thermal stability, electrical insulation properties, and mechanical strength. These attributes make alumina ceramics suitable for a wide range of industrial applications, from electronics to aerospace.
However, achieving precise and efficient machining of this material requires specialized techniques and tools. This guide on how to machine alumina ceramic will provide an overview of the methods and best practices for successfully machining alumina ceramic, ensuring high-quality results while minimizing tool wear and material loss.
Why Machine Alumina Ceramic?
Before diving into the specifics of how to machine alumina ceramic, it is essential to understand why this material is worth machining in the first place. While alumina ceramics possess impressive properties, they are not always easy to work with due to their extreme hardness and brittleness.
So why bother machining it at all? The answer lies in the unique properties of alumina ceramic and its wide range of applications.
It is often necessary to machine alumina ceramic in order to achieve the desired shape, size, and surface finish for a particular application. This can include creating intricate components for use in electronics, precision parts for medical devices, or high-strength components for aerospace applications.
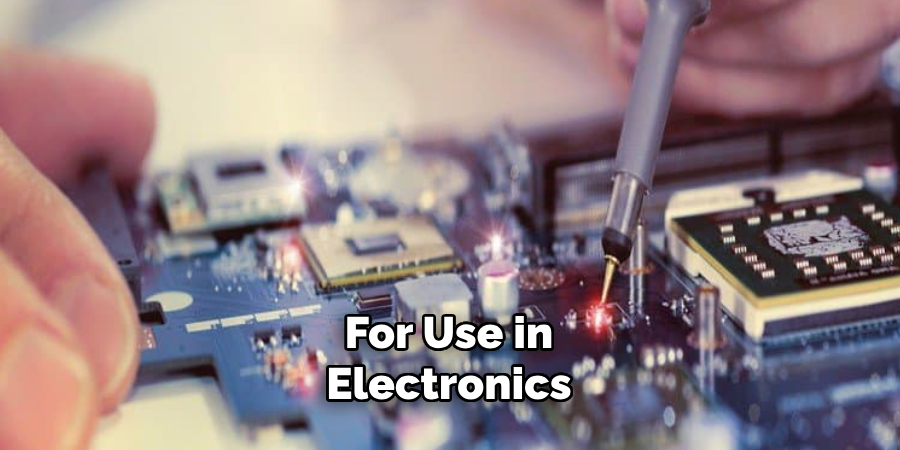
Furthermore, machining allows for greater control over the final product compared to other forming methods such as casting or powder processing. This makes it possible to create custom-designed parts with tight tolerances and complex geometries that would be impossible to achieve through other means.
Needed Materials
In order to successfully machine alumina ceramic, there are a few essential materials that you will need. These include specialized tools and equipment designed for working with hard and brittle materials, as well as proper safety gear to protect yourself from potential hazards.
Diamond Cutting Tools:
Due to its extreme hardness, conventional cutting tools like carbide or high-speed steel will not be effective for machining alumina ceramic. Instead, diamond-cutting tools are necessary to achieve precise cuts and avoid excessive wear on the tool.
Coolant:
The high heat generated during machining can cause thermal shock in alumina ceramic, leading to cracks and breakage. To prevent this, it is crucial to use a coolant during the machining process. Water-based coolants with rust inhibitors are recommended for alumina ceramic.
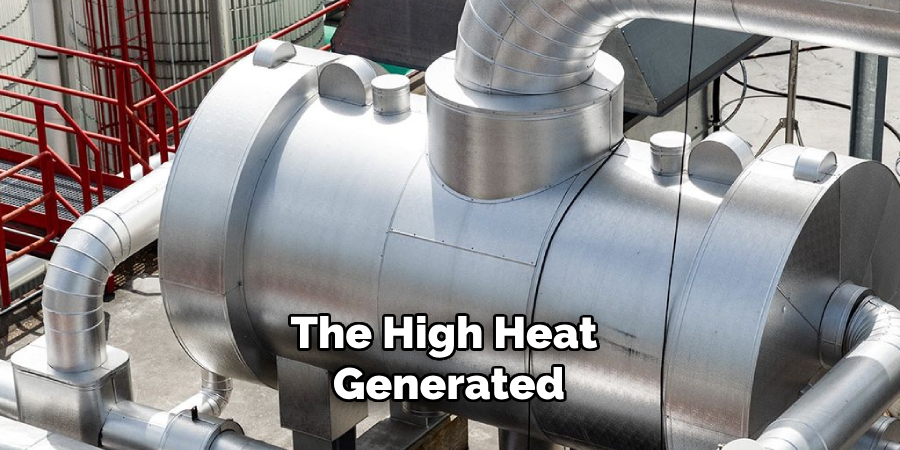
Safety Gear:
When working with any type of material, safety should always be a top priority. However, machining alumina ceramic is even more critical.
The material can produce fine dust particles that can be harmful if inhaled, and the high speed of cutting tools can also pose a safety risk. It is essential to wear proper eye protection, gloves, and a respirator mask when machining alumina ceramic.
6 Simple Step-by-step Guidelines on How to Machine Alumina Ceramic
Step 1: Design and Plan
The first and most critical step in machining alumina ceramic is to thoroughly design and plan the machining process.
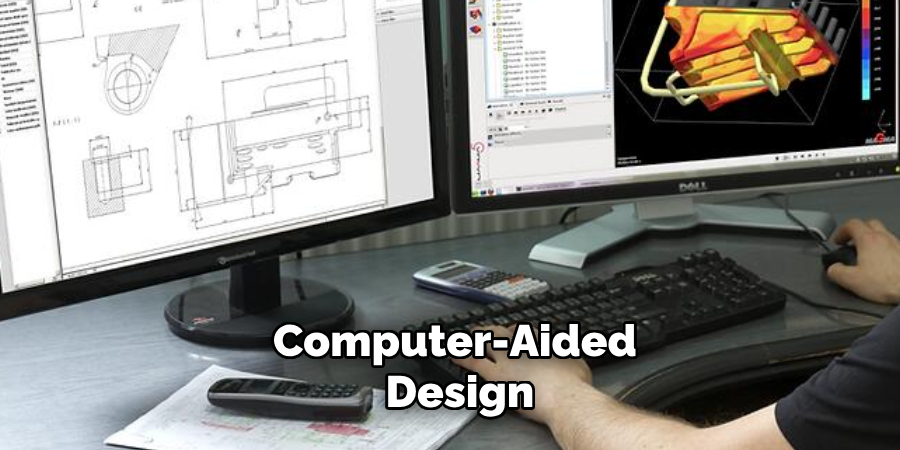
Begin by creating detailed drawings or computer-aided design (CAD) models of the desired component, specifying all critical dimensions and tolerances. Consider factors such as the component’s application, mechanical stresses, and thermal conditions it will encounter.
Next, choose the appropriate machining method based on the component’s complexity and the required precision.
Some common methods for machining alumina ceramic include grinding, drilling, milling, and laser cutting. Each method has its limitations and advantages, so selecting the right technique is crucial for achieving optimal results.
Additionally, consider the tooling and the type of diamond-cutting tools that will be used, ensuring they are suited for the specific tasks at hand. Plan the tooling paths and machining parameters, such as feed rates and cutting speeds, to minimize tool wear and prevent damage to the ceramic material.
Lastly, ensure you have all the necessary materials, tools, and safety equipment prepared before beginning the machining process. Adequate planning and design will set the foundation for a successful machining operation and high-quality finished components.
Step 2: Set Up the Machine
Setting up the machine is a crucial step to ensure precision and prevent damage during the machining of alumina ceramic.
Begin by thoroughly cleaning the machine to remove any dust or debris that could interfere with the machining process or cause defects in the final product. After cleaning, install the diamond cutting tools, ensuring they are securely fastened and properly aligned to achieve precise cuts.
Next, the workpiece is set up by securely clamping the alumina ceramic material in place. It is vital to ensure the material is stable and will not move during machining, as any displacement can lead to inaccuracies and potential breakage of the brittle ceramic. Using appropriate fixtures and clamps designed for hard materials is recommended.
Step 3: Use Proper Cutting Techniques
When it comes to machining alumina ceramic, it is crucial to use the right cutting techniques to achieve optimal results.
This includes using sharp and properly aligned diamond cutting tools, as well as selecting the appropriate feed rates and cutting speeds for the specific material and component being machined.
It is also essential to use a coolant throughout the machining process to prevent thermal shock and reduce tool wear. The coolant should be directed at the point of contact between the tool and material to dissipate heat and lubricate the cutting surface.
Step 4: Monitor Progress
Continuously monitoring the machining process is crucial for ensuring precision and identifying any potential issues that may arise. This can include regularly checking the tool wear, monitoring cutting speeds and feed rates, and inspecting the workpiece for any defects.
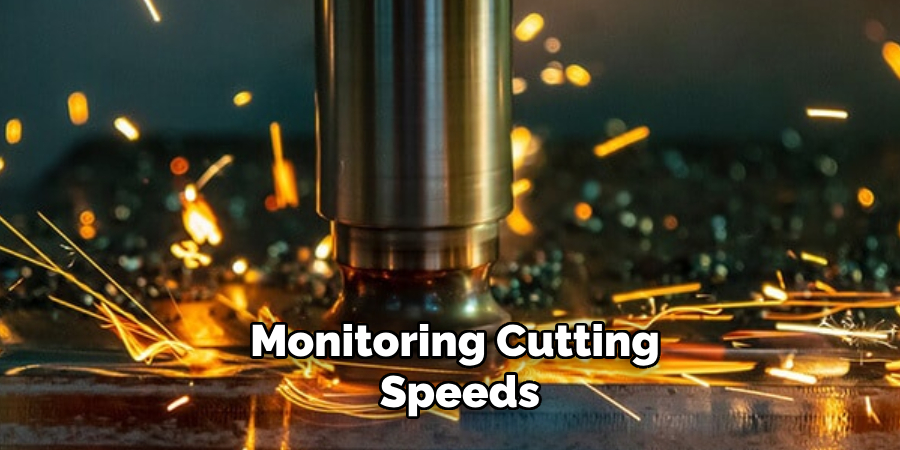
If any problems are encountered, adjustments to the cutting parameters or tooling may be necessary. In some cases, it may also be helpful to take intermittent breaks during the machining process to allow both the machine and material to cool down.
Step 5: Finish with Precision
The final step in machining alumina ceramic is to carry out finishing operations with utmost precision to achieve the desired surface quality and dimensional accuracy.
Utilize fine-grit diamond tools for finishing, as these are capable of producing smooth surfaces and minimizing microscopic imperfections. Additional grinding or polishing may also be necessary, depending on the component’s requirements.
During the finishing process, maintain consistent coolant application to prevent any heat buildup that could lead to thermal shock or surface cracking. Monitor the cutting tools closely and replace them if they begin to lose their sharpness to ensure continued precision.
Step 6: Clean and Inspect
After completing the machining process, it is essential to thoroughly clean the machine and work area to remove any residual dust or debris. This will not only help maintain a safe working environment but also prevent contamination of future components.
Inspect the finished component for any defects or imperfections before final use. If necessary, perform additional finishing operations to achieve the desired results. Proper cleaning and inspection after machining will ensure high-quality, precise components that are free from any damage or defects caused by the machining process.
Following these simple step-by-step guidelines on how to machine alumina ceramic will help ensure a successful and efficient machining process for alumina ceramic. Remember to always prioritize safety, precision, and attention to detail when working with this delicate yet versatile material.
With proper planning, setup, cutting techniques, monitoring, finishing, and inspection, you can achieve high-quality components that meet your design requirements. Happy machining!
Frequently Asked Questions
Q: Can Alumina Ceramic Be Machined With Traditional Machining Methods?
A: No, due to its hardness and brittleness, alumina ceramic requires specialized machining techniques using diamond cutting tools. Traditional methods such as turning or drilling are not suitable for this material.
Q: Is Alumina Ceramic Difficult to Machine?
A: Yes, alumina ceramic is a very hard and brittle material, making it challenging to machine. However, with proper planning and technique, it can be machined successfully.
Q: What Are the Advantages of Machining Alumina Ceramic?
A: Machining alumina ceramic allows for high precision and tight tolerances, making it suitable for various applications in industries such as aerospace, automotive, and electronics.
It also has excellent wear resistance and can withstand extreme temperatures. Overall, machining alumina ceramic offers a durable and versatile solution for complex component designs.
Q: What Precautions Should I Take When Machining Alumina Ceramic?
A: It is crucial to prioritize safety and wear proper protective equipment when machining alumina ceramic.
Additionally, carefully plan and design the machining process, use appropriate coolant and cutting techniques, and regularly monitor progress to ensure precision and prevent damage to the material.
Always refer to the manufacturer’s guidelines for specific precautions and recommendations when working with alumina ceramic.
Conclusion
Machining alumina ceramic can be a challenging yet rewarding process when executed with precision and care.
By following the outlined steps on how to machine alumina ceramic, from preparation to finishing, and paying close attention to the nuances of the material, you can achieve high-quality components that meet stringent design specifications.
Utilizing specialized diamond-cutting tools, maintaining proper coolant application, and continuously monitoring the process is key to mitigating issues and enhancing the machining results.
Through diligent practice and adherence to best practices, machining alumina ceramic can offer robust, precise, and durable solutions for a wide array of industrial applications.
Edmund Sumlin is a skilled author for Metal Fixes, bringing 6 years of expertise in crafting a wide range of metal fixtures. With a strong background in metalwork, Edmund’s knowledge spans various types of fixtures, from decorative pieces to functional hardware, blending precision with creativity. His passion for metalworking and design has made him a trusted resource in the industry.
Professional Focus:
- Expert in Metal Fixtures : Edmund aesthetic specializes in creating durable and innovative metal fixtures, offering both appeal and functionality. His work reflects a deep understanding of metalworking techniques and materials.
- Sustainability Advocate : He is dedicated to using sustainable practices, ensuring that every fixture is crafted with eco-friendly methods while maintaining high-quality standards.
In his writing for Metal Fixes, Edmund provides valuable insights into the latest trends, techniques, and practical advice for those passionate about metal fixtures, whether they are professionals or DIY enthusiasts. His focus on combining artistry with engineering helps others discover the true potential of metal in design.