How to make bronze sculpture is an intricate and fascinating process that combines artistic creativity with technical skill.
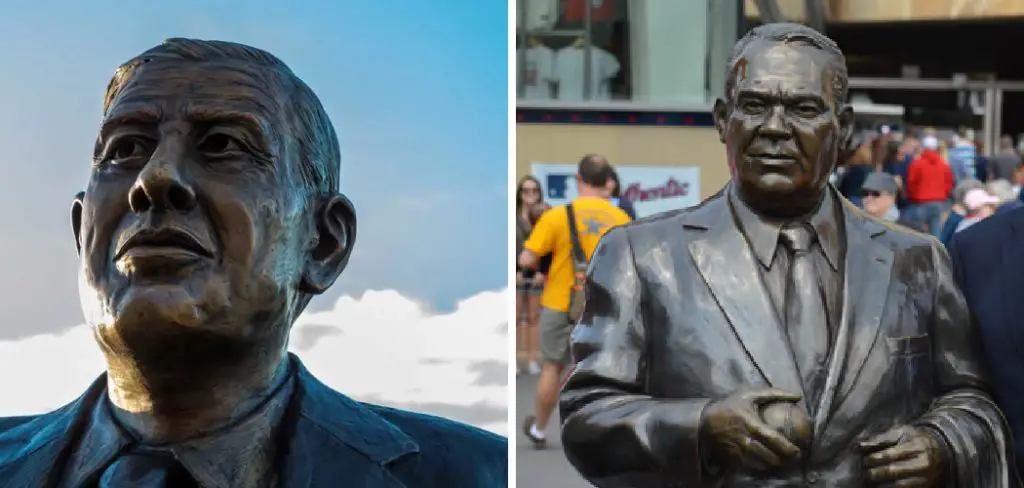
Bronze, an alloy typically consisting of copper and tin, has been a favored medium for sculptors for thousands of years due to its strength, durability, and the beautiful patina it develops over time. The art of bronze sculpture involves several key steps, from the initial conceptual sketch to the finishing touches that bring the piece to life.
This guide will walk you through the essential stages of making bronze sculptures, providing insights and tips to help you transform a block of wax or clay into a stunning work of art.
Whether you are a novice sculptor looking to learn the basics or an experienced artist seeking to refine your techniques, this comprehensive overview will assist you in mastering the traditional and modern methods of bronze sculpture creation.
What Will You Need?
Before you begin your bronze sculpture journey, gathering all the necessary tools and materials is important. This will ensure you have everything you need to create a successful piece without any interruptions or delays. Here are some of the essential items you’ll need:
- A block of wax or clay for sculpting
- Sculpting tools such as chisels, rasps, and knives
- A heat source for melting the wax or clay (a hot plate or candle can work)
- Plaster or silicone rubber mold-making material
- A crucible for melting the bronze (can be made of steel, graphite, or ceramic)
- A furnace or kiln for heating the bronze
- Protective gear such as gloves and goggles
- Bronze metal (typically sold in ingots or bars)
- Various finishing tools and materials such as sandpaper, patina chemicals, and polishing cloths
Remember that these are just the basic materials needed for a traditional bronze sculpture.
10 Easy Steps on How to Make Bronze Sculpture
Step 1: Creating the Sculpture Model
The first step in making a bronze sculpture is to create the original model, which serves as the template for the final piece. This model can be sculpted from wax or clay, both of which are pliable materials that allow for detailed work.
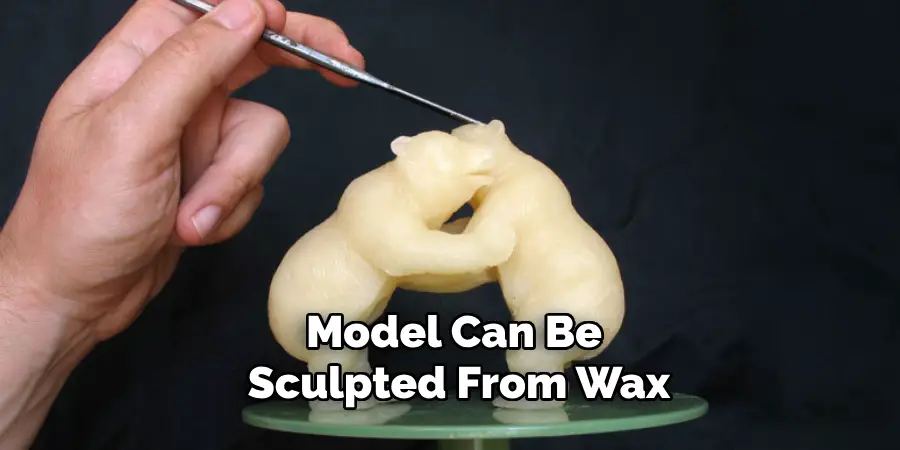
Start by sketching your design on paper to have a clear vision of your sculpture. Once you have a design, use the block of wax or clay to begin sculpting.
Step 2: Making the Mold
Once you have completed the sculpture model, the next step is to create a mold. The mold captures your model’s details and will be used to form the final bronze piece. Begin by covering your sculpture model with plaster or silicone rubber mold-making material. Cover the entire surface evenly and thoroughly to capture every intricate detail.
If you are using a two-part mold, you must create a mold box to hold the silicone rubber and construct a separation seam down the middle. After the mold material has fully cured, carefully remove the original model from it. You should be left with a hollow cavity in the shape of your sculpture, ready for the next step.
Step 3: Wax Casting
After you have your mold, the next step is to create a wax replica of your sculpture. This is done by pouring molten wax into the mold, coating the entire interior surface. Rotate the mold as you pour to ensure an even layer of wax, typically around 1/8 to 1/4 inch thick.
Once the wax has cooled and solidified, carefully remove it from the mold. This wax model should have all the fine details of the original sculpture and will be used to create the ceramic shell in the next step.
Step 4: Gating System
The wax model needs a gating system consisting of wax rods or sprues attached to it. These channels will allow molten bronze to flow into every part of the mold. Attach the sprues to areas that complement the design and won’t hinder the final appearance. Add a main pouring cup, which will be the entry point for the molten bronze. This setup ensures that the bronze flows seamlessly and captures the details of the sculpture.
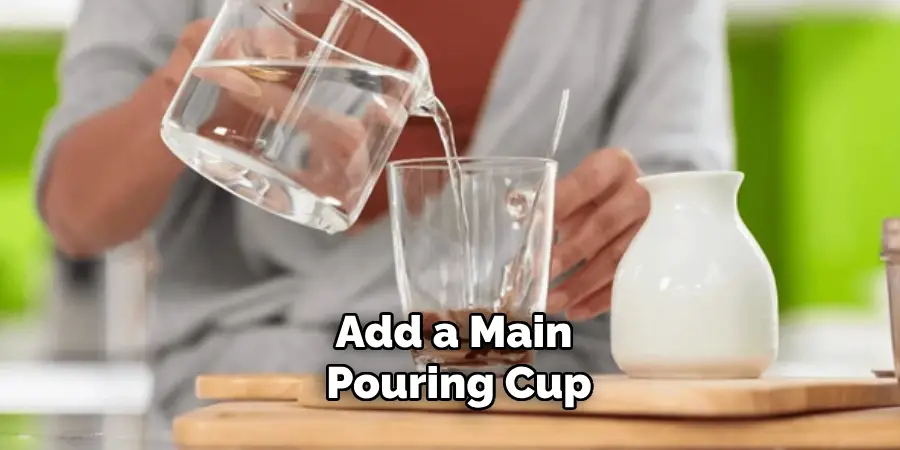
Step 5: Ceramic Shell Mold
Now that the gating system is in place, applying a ceramic shell to the wax model is next. This involves repeatedly dipping the model into a ceramic slurry and then into a fine sand mixture. Allow each layer to dry before applying the next. The process is repeated multiple times until a thick, durable ceramic shell is formed. This mold must be sturdy enough to hold the molten bronze without breaking.
Step 6: Wax Burnout
Once the ceramic shell mold is complete and has dried fully, it is necessary to remove the wax model from inside. This is achieved by placing the ceramic mold into a kiln or furnace, where the heat will melt the wax, causing it to drain out. This process is known as “lost wax casting,” leaving behind a hollow ceramic mold ready to be filled with bronze.
Step 7: Melting the Bronze
Melting the bronze is a crucial step that requires precise temperature control. Load bronze ingots into a crucible and place them in a furnace or kiln capable of reaching temperatures between 1,700 and 2,000 degrees Fahrenheit. Once the bronze has melted to a liquid state, carefully skim any impurities from the surface to ensure the highest-quality metal for casting.
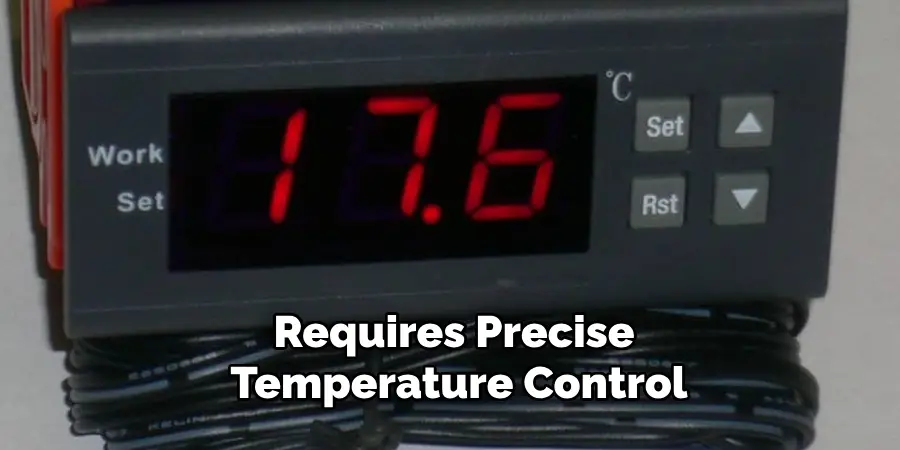
Step 8: Pouring the Bronze
With the bronze now molten and impurities removed, the next step is to pour it into the prepared ceramic mold. This must be done carefully and steadily to avoid splashing and ensure the bronze fills all parts of the mold completely. Allow the bronze to cool and solidify inside the mold before proceeding.
Step 9: Breaking the Mold
Once the bronze has cooled and hardened, the ceramic shell mold must be broken away to reveal the bronze sculpture inside. Use hammers and chisels to carefully remove the ceramic without damaging the bronze. This step requires patience and precision to avoid harming the delicate details of the sculpture.
Step 10: Finishing Touches
The final step involves cleaning and finishing the bronze sculpture. This may include removing any remnants of the gating system, polishing the surface, and applying a patina if desired. Various tools such as files, grinders, and sandpaper can be used to refine details and achieve the desired finish. A protective coating is often applied to preserve the sculpture’s appearance over time.
By following these ten steps, you can transform your creative vision into a magnificent bronze sculpture, ready to be admired for generations.
5 Additional Tips and Tricks
- Detailed Clay Model: Start with a highly detailed clay model of your sculpture. This will serve as the blueprint for your bronze casting, so the more intricate the model, the more detailed your final piece will be.
- Use High-Quality Molds: Invest in high-quality silicone molds for your wax models. This ensures that every fine detail is captured, reducing potential defects in the final bronze casting.
- Proper Venting: Ensure proper venting in your wax model to allow gases to escape during the bronze pouring process. This minimizes the risk of air pockets forming in your sculpture.
- Consistent Heating: Maintain a consistent heating temperature throughout the entire bronze casting process. Uneven heating can cause the bronze to cool at different rates, leading to cracks or warping in the sculpture.
- Patination Techniques: Experiment with different patination techniques to give your bronze sculpture a unique finish. Patinas can add color, texture, and character to your piece, enhancing its overall visual appeal.
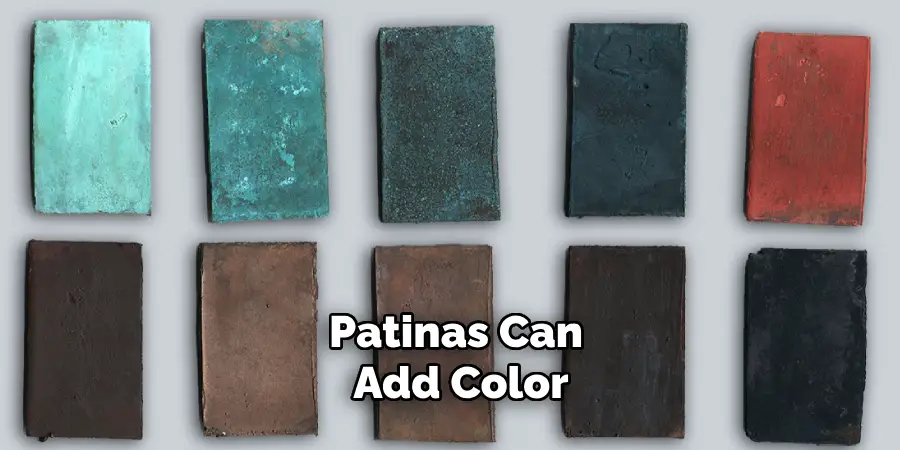
5 Things You Should Avoid
- Rushing the Wax Model: Avoid rushing the creation of your wax model. Hasty or sloppy work can lead to imperfections in the final bronze sculpture, such as surface bubbles or rough textures.
- Ignoring Safety Protocols: Never ignore safety protocols when working with hot materials. Proper safety gear, including gloves and eye protection, prevents injuries during the bronze casting process.
- Using Inadequate Venting: Do not neglect the importance of adequate venting in your molds. Insufficient venting can trap gases, leading to defects such as blowouts or porous surfaces in the final sculpture.
- Skipping Mold Cleaning: Always clean your molds thoroughly between casts. Residue or debris left in the mold can affect the quality of the next pour and lead to undesirable marks or imperfections.
- Neglecting Cooling Times: Avoid rushing the cooling process. Allow the bronze ample time to cool down slowly and evenly to prevent stress fractures, warping, or other structural issues.
Conclusion
How to make bronze sculpture is a meticulous yet rewarding process that requires attention to detail, patience, and adherence to specific techniques.
Beginning with a detailed clay model and using high-quality molds lays the groundwork for a successful cast.
Ensuring proper venting and maintaining consistent heating during the bronze pouring process is essential to achieving a structurally sound sculpture. Additionally, experimenting with patination techniques allows artists to add a unique finish to their work.
By avoiding common pitfalls such as rushing the wax model, ignoring safety protocols, and neglecting cooling times, one can prevent defects and enhance the overall quality of the final piece. With dedication and careful execution, anyone can master the art of bronze sculpture, creating timeless works of art.
You can check it out Keep Bronze From Tarnishing
Edmund Sumlin is a skilled author for Metal Fixes, bringing 6 years of expertise in crafting a wide range of metal fixtures. With a strong background in metalwork, Edmund’s knowledge spans various types of fixtures, from decorative pieces to functional hardware, blending precision with creativity. His passion for metalworking and design has made him a trusted resource in the industry.
Professional Focus:
- Expert in Metal Fixtures : Edmund aesthetic specializes in creating durable and innovative metal fixtures, offering both appeal and functionality. His work reflects a deep understanding of metalworking techniques and materials.
- Sustainability Advocate : He is dedicated to using sustainable practices, ensuring that every fixture is crafted with eco-friendly methods while maintaining high-quality standards.
In his writing for Metal Fixes, Edmund provides valuable insights into the latest trends, techniques, and practical advice for those passionate about metal fixtures, whether they are professionals or DIY enthusiasts. His focus on combining artistry with engineering helps others discover the true potential of metal in design.