Are you interested in making your own steel? Carbon steel can be made using a simple process called smelting.
Carbon steel is a popular material known for its strength, durability, and versatility, making it an essential component in various industries, from construction to automotive manufacturing. The process of making carbon steel involves the combination of iron and carbon, with the latter typically comprising up to 2.1% of the alloy’s weight.
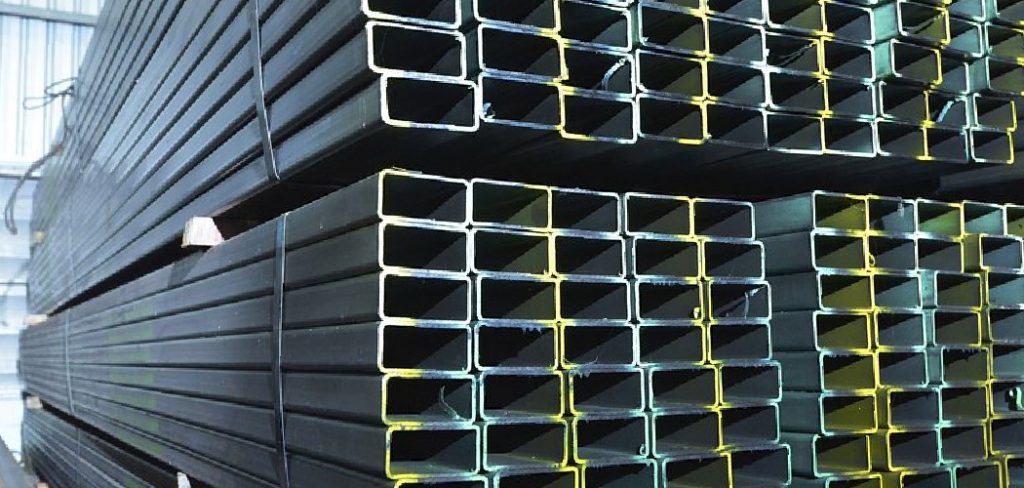
This mixture results in a metal that enjoys enhanced properties such as hardness and resistance to wear. Understanding the fundamental techniques of creating carbon steel, including smelting and refining, is crucial for producing high-quality alloys tailored to specific applications.
This guide on how to make carbon steel will cover the basics of the process, including the materials and equipment needed, as well as safety precautions to follow.
What Will You Need?
Before beginning the process of making carbon steel, gathering all the necessary materials and equipment is essential. Here are the items you will need to make carbon steel:
- Iron Ore: Iron ore is the main ingredient in making carbon steel. It is a naturally occurring mineral that contains iron oxides, and it is abundant in many parts of the world.
- Coal or Charcoal: Carbon steel is derived from carbon, which is added to iron during smelting. Coal or charcoal acts as a source of carbon for this process.
- Flux: This material helps remove impurities from the molten metal during smelting.
- Furnace: A furnace heats and melts iron ore and carbon sources. It can be a traditional charcoal-burning furnace or a modern electric furnace.
- Tongs: These are used to handle hot materials and move them from the furnace to the molds.
- Molds: Molds are used to shape the molten metal into desired forms. They can be made of sand, ceramic, or graphite.
- Safety Gear: Safety should always be a top priority when working with hot metals. Wear protective gear such as heat-resistant gloves, safety glasses, and an apron.
Once you have gathered all the necessary materials and equipment, it is time to start the process of making carbon steel.
8 Easy Steps on How to Make Carbon Steel
Step 1. Preparation:
Before starting the smelting process, ensure your workspace is clean and free from any debris or clutter that could pose safety risks. Organize all materials and equipment in an accessible manner to streamline the process. Begin by inspecting the iron ore to ensure it is free from excess impurities that could affect the quality of the carbon steel.
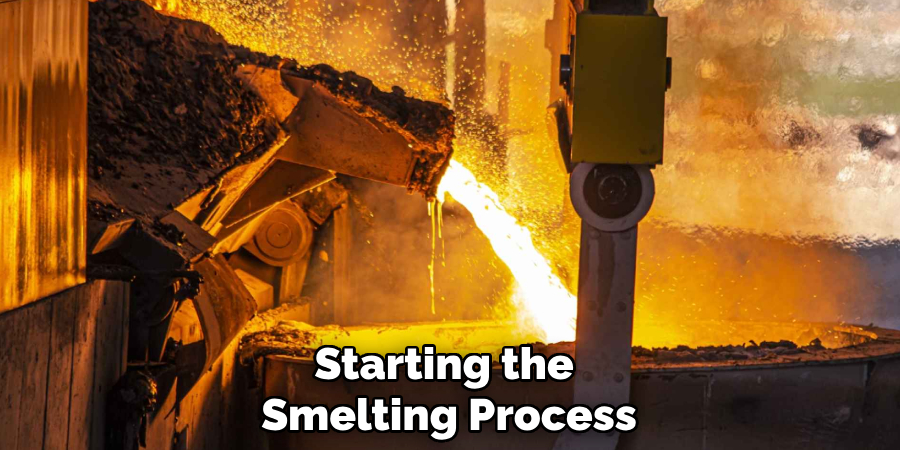
Crush the ore using a suitable tool to increase its surface area, facilitating faster and more efficient smelting. Check the condition of your furnace to ensure it is in proper working order and that you are familiar with its operation. Prepare your carbon source, whether coal or charcoal, by breaking it into smaller pieces, if necessary, to ensure an even burn.
Lay out your safety gear, including gloves, goggles, and an apron, and confirm their condition for optimal protection. Finally, preheat the furnace to the recommended temperature for melting iron, which is approximately 2,800°F (1,538°C), ensuring that it reaches the required heat to dissolve both the iron and carbon effectively. These preparatory steps will set the stage for a successful and safe carbon steel production process.
Step 2. Melting the Iron Ore and Carbon Source:
Once your furnace is preheated, carefully place the prepared iron ore into the furnace using tongs, ensuring the ore is evenly distributed for uniform melting. Gradually add the carbon source, such as coal or charcoal, to the stove. This carbon will combine with the molten iron, forming carbon steel.
Monitor the temperature closely, maintaining it around 2,800°F (1,538°C) to ensure efficient melting and alloy creation. It’s crucial to regularly check for adequate combustion, adding more fuel if necessary to maintain the desired heat levels. During this phase, keep an eye on the molten mixture’s consistency, stirring gently to promote uniformity and prevent clumping.
Step 3. Removing Impurities:
With the molten mixture of iron and carbon ready, the next crucial step is to remove any impurities that could compromise the quality of the carbon steel. This is where flux comes into play. Carefully add the flux to the molten mix; it will help to bind and float away impurities such as sulfur and phosphorus, which can adversely affect the metal’s strength and hardness. Keep the furnace at a steady temperature to ensure the flux works effectively.
As the flux interacts with the impurities, it forms a slag—a waste material layer—separating itself from the molten metal. Use a slag skimmer or similar tool to remove this slag from the surface, being cautious to minimize disturbance to the molten steel underneath. Consistently monitor the process and adjust as necessary to maintain the integrity of the steel. Removing these impurities will enhance the durability and performance of the resulting carbon steel.
Step 4. Refining for Desired Carbon Content:
After removing impurities, the next step is refining the molten metal to achieve the desired carbon content essential for specific types of carbon steel. This process involves carefully controlling the amount of carbon in the molten mixture, which in turn dictates the steel’s hardness and strength. Using a carbon meter, measure the current carbon content within the molten mix.
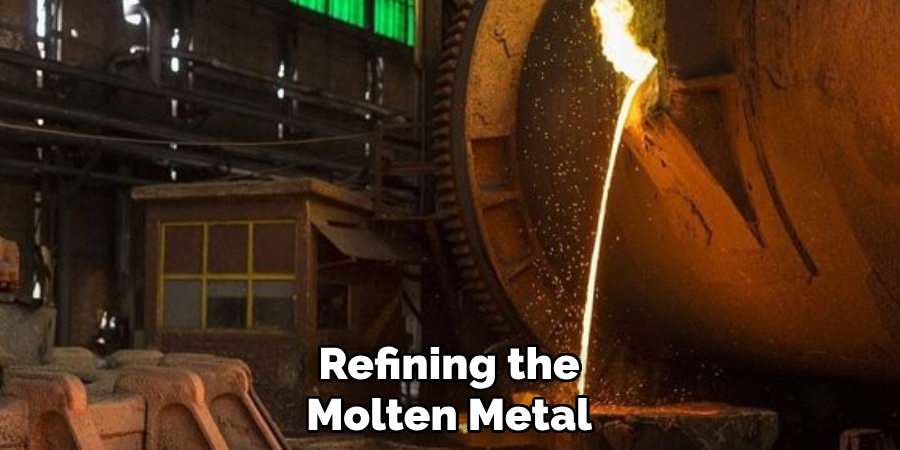
If the content is too high, introduce controlled amounts of oxygen or scrap steel to reduce it gradually. Conversely, if more carbon is necessary, incrementally add small portions of coal or charcoal, allowing time for it to dissolve completely. Stir the molten metal thoroughly after adjustments to ensure uniform distribution of the carbon. Consistently check the temperature throughout this step, maintaining the optimal thermal conditions for carbon absorption and distribution.
Step 5. Casting the Molten Steel:
Once the desired carbon content is achieved and the molten steel is refined, it is time to cast the steel into molds to shape it into usable forms. Carefully pour the molten steel into pre-prepared molds, which should be free from moisture to prevent explosive reactions. The molds can be made of sand, ceramic, or graphite according to the specific product requirements.
Ensure a steady and controlled pour to avoid splashing and allow the steel to fill the mold evenly. Once the molds are filled, let them cool gradually to prevent stress fractures. The cooling time may vary depending on the size and thickness of the casting. This step is crucial in determining the final shape and surface quality of carbon steel products.
Step 6. Heat Treatment:
After the carbon steel has been cast and allowed to cool, the next vital step in the process is heat treatment. This procedure involves reheating the steel to a specific temperature and then cooling it at a controlled rate to alter its physical and mechanical properties. This can include increasing hardness, improving elasticity, or relieving internal stresses within the metal. Depending on the desired properties of the carbon steel, various heat treatment methods may be used, such as annealing, quenching, or tempering.
During annealing, the steel is heated to a temperature where recrystallization can occur, then slowly cooled to make it more ductile and less brittle. In quenching, the steel is rapidly cooled from a high temperature by immersion in water or oil to increase hardness. Finally, tempering involves reheating quenched steel to a lower temperature before cooling it again, which reduces brittleness while retaining hardness.
Step 7. Finishing and Inspection:
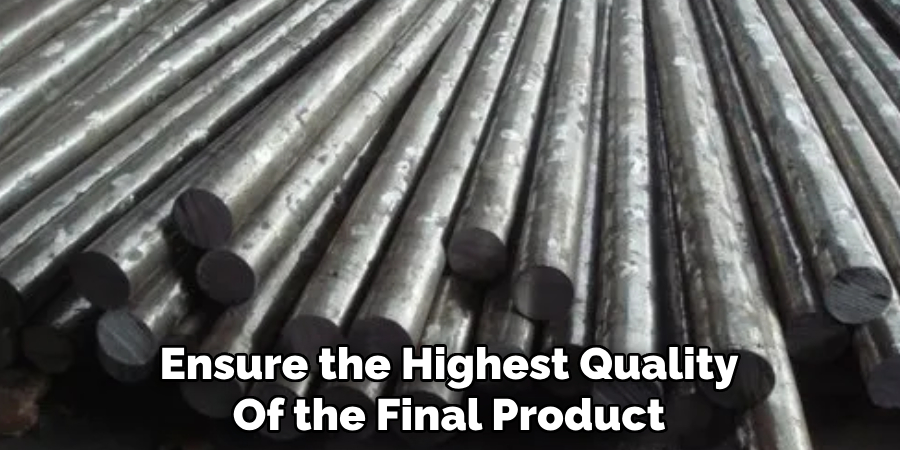
The final step in the carbon steel production process involves finishing and inspection to ensure the highest quality of the final product. Once the steel has undergone heat treatment, it is subjected to various finishing techniques such as grinding, sanding, or polishing to achieve the desired surface texture and appearance. These processes help remove surface imperfections and enhance the steel’s aesthetic appeal and functionality.
After finishing, a comprehensive inspection is conducted to verify the material’s compliance with industry standards and specifications. This includes checking for defects, measuring dimensions, and testing physical properties such as tensile strength and hardness. Non-destructive testing methods, such as ultrasound or radiography, may also detect internal flaws without damaging the steel.
Step 8. Packaging and Distribution:
After the carbon steel undergoes finishing and inspection, the next step is packaging and distributing the final products. Careful packaging is necessary to protect the steel from corrosion and damage during transit.
Depending on the type and size of the steel components, packaging may involve wrapping them in protective materials like oil-coated paper or using wooden crates to cushion them. Additionally, anti-corrosive treatments or coatings might be applied to extend the products’ shelf life.
By following these steps, we can ensure the production of high-quality carbon steel with specific properties tailored to various applications.
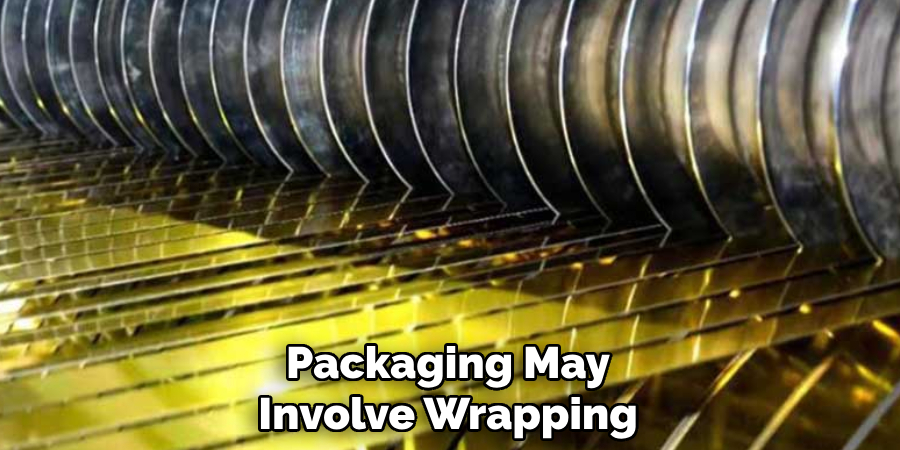
Conclusion
In conclusion, how to make carbon steel involves a meticulous and multi-step process that transforms raw materials into durable end products.
The journey begins with selecting high-quality raw materials and continues through stages of melting, impurity removal, careful refinement, and precise casting. Each step is critical in influencing the final product’s characteristics, such as strength, hardness, and flexibility. Heat treatment further optimizes these properties, tailoring the steel to meet specific requirements.
The process culminates in careful finishing, thorough inspection, and strategic packaging, ensuring that the carbon steel meets industry standards and arrives ready for use. Mastery of these stages ensures that the resulting carbon steel can effectively serve its intended purpose across various applications.
Edmund Sumlin is a skilled author for Metal Fixes, bringing 6 years of expertise in crafting a wide range of metal fixtures. With a strong background in metalwork, Edmund’s knowledge spans various types of fixtures, from decorative pieces to functional hardware, blending precision with creativity. His passion for metalworking and design has made him a trusted resource in the industry.
Professional Focus:
- Expert in Metal Fixtures : Edmund aesthetic specializes in creating durable and innovative metal fixtures, offering both appeal and functionality. His work reflects a deep understanding of metalworking techniques and materials.
- Sustainability Advocate : He is dedicated to using sustainable practices, ensuring that every fixture is crafted with eco-friendly methods while maintaining high-quality standards.
In his writing for Metal Fixes, Edmund provides valuable insights into the latest trends, techniques, and practical advice for those passionate about metal fixtures, whether they are professionals or DIY enthusiasts. His focus on combining artistry with engineering helps others discover the true potential of metal in design.