Angle iron is a versatile structural material commonly employed in various fields such as construction, manufacturing, and DIY projects due to its strength and durability. Characterized by its L-shaped cross-section, angle iron provides excellent support and stability, making it an ideal choice for frameworks, bracing, and reinforcing. The precise measurement of angle iron is crucial to ensure proper fit and structural integrity in any application. Accurate dimensions guarantee that components will cooperate seamlessly, preventing potential issues such as misalignment or instability.
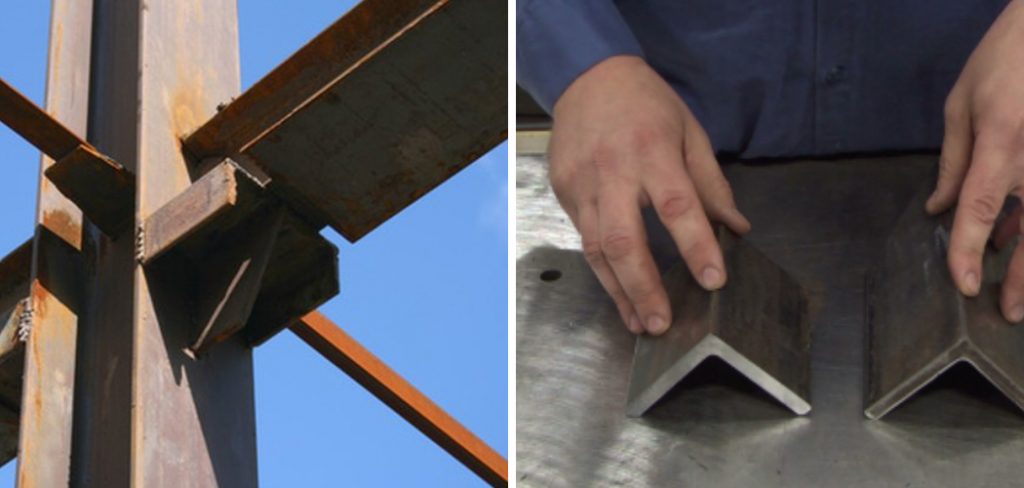
This article aims to guide readers through the detailed process of how to measure angle iron accurately, ensuring success in diverse applications. From understanding its anatomy to utilizing appropriate tools and techniques, readers will learn essential skills for precise measurement, ultimately leading to more efficient and successful projects.
Understanding the Anatomy of Angle Iron
Explanation of the L-shaped Profile
Angle iron is defined by its characteristic L-shaped profile, comprised of two perpendicular flanges, often called “legs.” These legs converge at a precise 90-degree angle, offering the structural stability integral to many engineering and support applications. While the dimensions of these legs can vary, understanding the specific measurements needed for each is crucial for project success. Whether each leg is of equal or different lengths depends on the application’s requirements, and knowing the correct dimensions ensures that the angle iron fits seamlessly where needed, provides optimal support, and maintains structural integrity.
Types and Sizes of Angle Iron
Angle iron comes in a range of common sizes and materials, including steel, aluminum, and stainless steel. The choice of material often depends on the application, with considerations for load-bearing capacity and environmental factors. Standard angle iron shapes are widely used due to their predefined and regular dimensions, making them suitable for typical projects. However, custom angle iron shapes are sometimes necessary to match unique project specifications, and these non-standard sizes require precise measurements. The ability to measure both standard and custom profiles accurately ensures that the material performs effectively within its intended structural context.
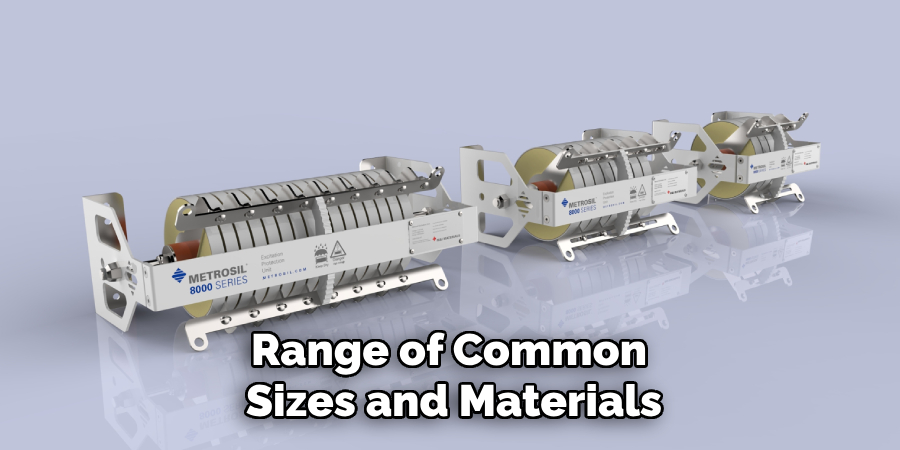
Tools Required for Measuring Angle Iron
Essential Measuring Tools
Utilizing the right tools is imperative to achieving precise measurements of angle iron. A tape measure is essential for determining general length and width, while calipers offer more detailed dimensional accuracy. A protractor and an angle gauge are crucial for confirming the correct angles and ensuring structural integrity. A straightedge assists in assessing alignment and evenness. Selecting high-accuracy tools is fundamental to prevent errors, as even slight deviations can impact the fit and stability of the project.
Safety Gear and Workspace Setup
Ensuring a safe and efficient workspace is as important as the measurement itself. Wearing protective gloves guards against sharp edges, reducing the risk of injury. A clear workspace with adequate lighting enhances visibility and accuracy during the measurement process. Proper lighting ensures all measurements are visible and precise. Stabilizing the angle iron on a flat surface before measuring can also help achieve more accurate readings, as movement or instability can lead to measurement errors. You can ensure a successful measuring process by prioritizing safety and accuracy.
How to Measure Angle Iron: Measure the Dimensions
Measuring the Length of the Angle Iron
To accurately measure the length of an angle iron, use a tape measure along the edge of one of its legs. Start by firmly anchoring the tape measure at one end, making sure it lies flush against the surface. Carefully extend the tape along the contour of the leg to capture its full length, ensuring the tape remains taut without sagging for the most precise result. This method provides a reliable measure of the total length, which is crucial for fitting the angle iron into its designated structural application.
Measuring the Leg Dimensions
To determine the dimensions of each leg, position a ruler or calipers along its outer edge. Begin by aligning the tool precisely at the outermost boundary of one leg, noting its width. Repeat this procedure for the other leg to ascertain whether they are equal or unequal in size. An accurate assessment of leg dimensions ensures the angle iron fulfills its intended load-bearing or structural function, fitting seamlessly into any construction or fabrication project.
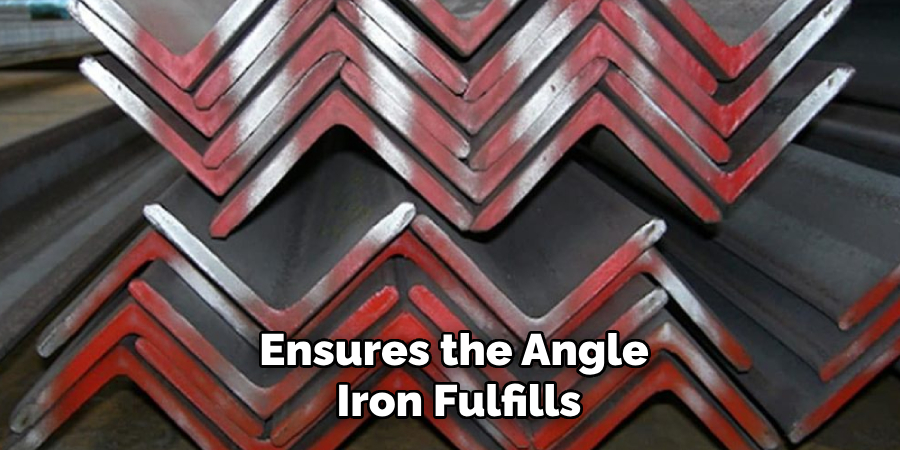
Measuring the Thickness
The thickness of the angle iron is a critical parameter best measured using calipers or a micrometer. Begin by positioning the measuring tool at an accessible point along the edge of one leg, ensuring it is perpendicular to the surface. Close the calipers carefully until they make firm contact with both surfaces, then read the measurement. An accurate thickness measurement is vital for understanding the angle iron’s strength and capacity within structural applications, ensuring it meets the necessary specifications for stability and durability.
How to Measure Angle Iron: Measure the Angle and Radius
Measuring the 90-degree Angle
The integrity of an angle iron greatly relies on the precision of its 90-degree angle between the two legs. To ensure this, an angle gauge or protractor is essential. Begin by firmly placing the angle iron on a stable surface. Position the angle gauge at the legs’ meeting point, ensuring it is flush against both surfaces. The protractor’s baseline should align perfectly at the corner, covering both legs equally. If the tool shows any deviation from 90 degrees, it is crucial to note this variance. Even minor deviations can significantly affect applications requiring precise angles, such as structural frameworks and engineered joints.
If discrepancies occur, corrections may need to be applied by reassessing the iron’s position or considering adjustments in the project’s parameters to maintain integrity and functionality.
Measuring the Inside Radius
The inside radius of the angle iron is critical, as it affects how well the component fits within its intended application. The curved corner where the legs converge can be measured using calipers. Start by locating a point on the curve that you can easily access. Open the calipers to span the curve and adjust until they contact both pathway edges smoothly, capturing the radius measurement. This value is important for ensuring the angle iron meets compatibility requirements, particularly in applications involving smooth transitions or additional support structures. Confirming the radius assures a seamless fit and functioning within the larger assembly.
Measuring Custom or Non-Standard Angle Iron Shapes
Measuring Custom or Non-Standard Angle Iron
Measuring custom or non-standard angle iron shapes requires a tailored approach to accurately record their unique dimensions. Begin by identifying whether the angle iron has equal or unequal leg angles, as this will dictate the measuring tools and methods used. For angle irons with unequal leg designs, an adjustable protractor becomes essential. Place the protractor at the junction where the legs meet, and adjust it to accurately measure angles that deviate from the typical 90 degrees. This ensures that tailored cuts or fits for your projects maintain precision and structural integrity.
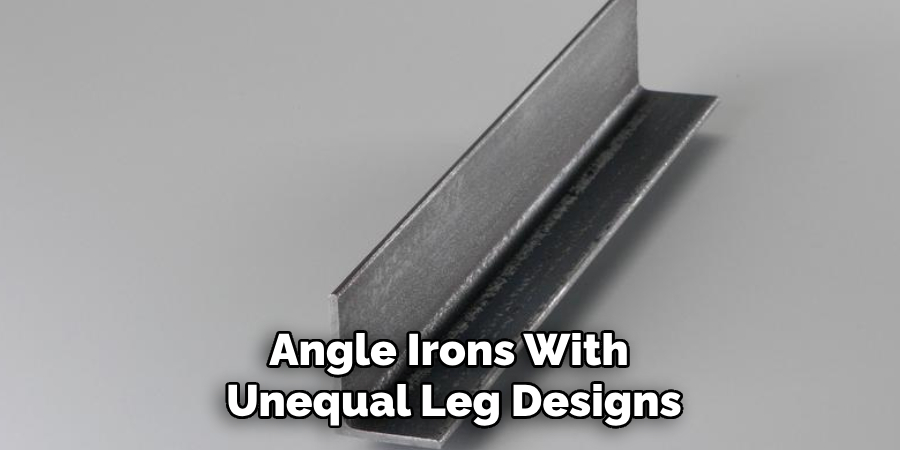
It is crucial to document each leg’s dimensions and the angle, as accurate records facilitate the fabrication process and help achieve precise assemblies in complex builds. Ensuring reliable measurements for these custom profiles can significantly enhance their integration into bespoke structures or projects.
Adjusting Techniques for Unequal Leg Angles
In instances where angle irons have unequal leg angles, the use of an adjustable protractor is critical for measurement. This tool allows for precisely capturing angles differing from the standard 90 degrees, providing essential data for fitting irregular components. Documenting both leg dimensions alongside the varied angles is vital, as this information supports precise cutting or fitting processes, ensuring the bespoke angle iron correctly fits within the intended application. Recording these details is fundamental to avoiding misalignment and maintaining design accuracy.
Measuring Tapered or Irregular Angle Iron
When dealing with tapered or irregular-angle irons, careful assessment is required to capture all varying dimensions accurately. Employing flexible measuring tools like calipers and adjustable gauges can assist in recording the diverse profiles of these components. For such specialized angle irons, noting each variance in dimension ensures the capability to reproduce or fit the component within its intended architectural or industrial application. Accurate measurements and thorough documentation are crucial for these custom angles, as errors can result in costly adjustments or failures in structural applications.
Tips for Ensuring Accuracy in Measurements
Double-Checking Measurements
Ensuring precision in measuring angle iron is vital, particularly in applications requiring exact specifications. One effective method is the practice of taking multiple measurements to confirm consistency. By measuring several times, you minimize the potential for errors due to misalignment or tool manipulation. Additionally, employing a combination of measurement tools, such as a tape measure alongside calipers, provides an opportunity to cross-verify results. This approach enhances accuracy by confirming that each measurement aligns, thereby increasing confidence in the data gathered and ensuring precision in subsequent fabrication or construction processes.
Avoiding Common Errors
To avoid common errors in measuring angle iron, start by ensuring that all tools are fully calibrated and in optimal condition. Regular maintenance of calipers and protractors helps maintain their accuracy and reliability. Additionally, keep the angle iron stable during measurement to prevent slippage or movement, which can lead to inaccurate readings. Using clamps or positioning aids can secure the component in place, facilitating more accurate measurements. Attention to these details is crucial for maintaining the desired tolerances and ensuring successful integration into the larger project, thereby avoiding costly rework or misfits.
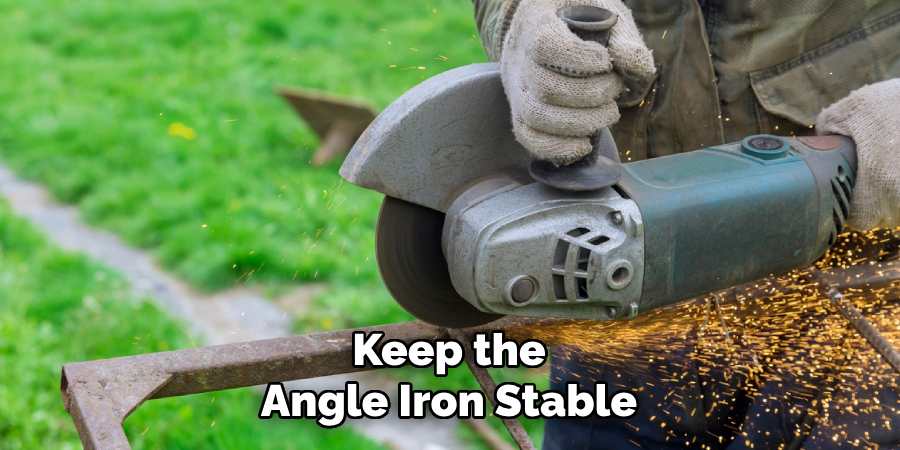
Applications of Accurate Angle Iron Measurements
Importance of Precision in Construction and Fabrication
Accurate angle iron measurements are crucial in construction and fabrication, as they ensure components fit together seamlessly, maintaining the structural integrity and safety of the finished build. Precise measurements are essential to achieving the desired architectural style, complying with tight tolerances, and ensuring the durability of the construction. For fabrication, accurate angle iron measurements lead to smooth assembly processes, minimizing adjustments and aligning with design specifications. This precision supports the successful completion of projects without unnecessary rework or fitting issues.
Examples of How Incorrect Measurements Can Lead to Improper Fits, Instability, or Project Delays
Incorrect angle iron measurements can cause components to fit improperly, leading to structural gaps or misalignments that compromise a build’s stability and safety. Such inaccuracies can also translate to project delays, as adjustments or replacements may be required to meet the intended design specifications. Time lost in addressing these issues can lead to increased labor costs and disruption in project timelines, ultimately impacting overall project delivery and effectiveness.
Benefits of Proper Measurement Techniques
Proper measurement techniques ensure efficient material use, which directly reduces waste and associated costs. Accurate measurements prevent overcutting or excess material usage, promoting responsible material management and project sustainability. In addition, precise measurement underpins effective inventory control, as components are ordered in correct quantities, minimizing surplus. These techniques streamline construction and fabrication processes, enhancing project efficiency and supporting long-term success.
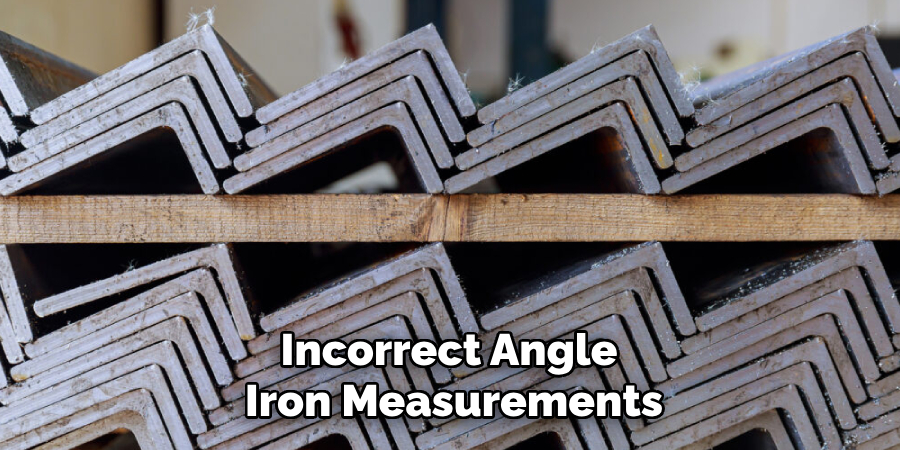
Conclusion
Accurate measurement of angle iron is vital for the success of any construction or fabrication project. Essential steps include assessing the dimensions and angles using tools like calipers, adjustable protractors, and tape measures. Ensuring tool calibration and employing double-checking techniques enhance precision. Practicing these careful measurement strategies helps maintain structural integrity and project timelines, avoiding costly errors. By understanding “how to measure angle iron” correctly, builders and fabricators can achieve seamless component integration, supporting robustness and durability in final builds. Emphasizing accuracy ultimately leads to efficient, successful project outcomes.
Edmund Sumlin is a skilled author for Metal Fixes, bringing 6 years of expertise in crafting a wide range of metal fixtures. With a strong background in metalwork, Edmund’s knowledge spans various types of fixtures, from decorative pieces to functional hardware, blending precision with creativity. His passion for metalworking and design has made him a trusted resource in the industry.
Professional Focus:
- Expert in Metal Fixtures : Edmund aesthetic specializes in creating durable and innovative metal fixtures, offering both appeal and functionality. His work reflects a deep understanding of metalworking techniques and materials.
- Sustainability Advocate : He is dedicated to using sustainable practices, ensuring that every fixture is crafted with eco-friendly methods while maintaining high-quality standards.
In his writing for Metal Fixes, Edmund provides valuable insights into the latest trends, techniques, and practical advice for those passionate about metal fixtures, whether they are professionals or DIY enthusiasts. His focus on combining artistry with engineering helps others discover the true potential of metal in design.