Welcome, welding enthusiasts! Are you tired of being unsure about the size of your fillet welds? Look no further, because in this blog post, we will take an in-depth look at how to accurately measure and determine the size of these critical components. Whether you are a novice welder or a seasoned professional, understanding fillet weld size is essential for achieving strong and high-quality welds.
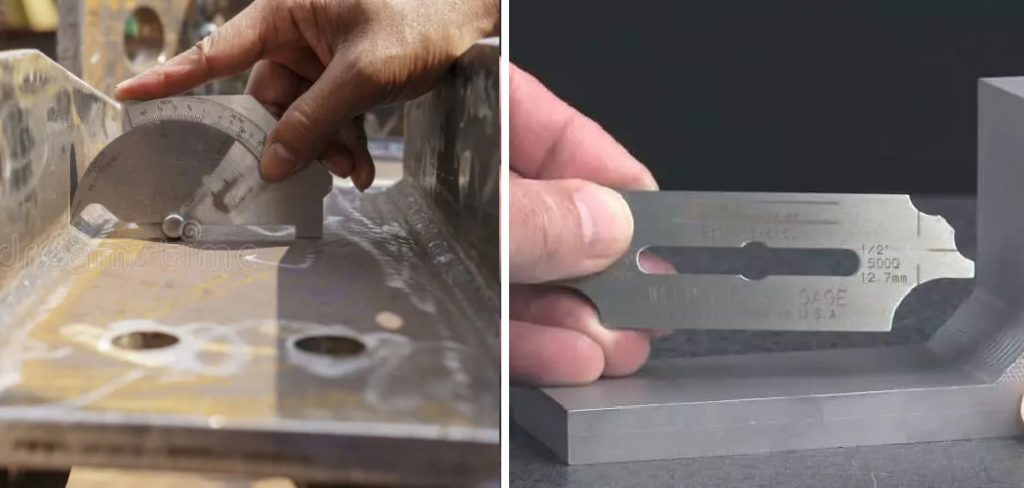
By the end of this post on how to measure fillet weld size, you will have all the information and techniques needed to confidently measure your fillet welds with precision. So grab your welding helmet and let’s dive into this topic together!
Why Measure Fillet Weld Size?
Before we dive into the methods of measuring fillet weld size, let’s first understand why it is important to do so. Fillet welds are one of the most commonly used types of welds and are vital for creating strong joints. A correctly sized fillet weld ensures that the desired strength and durability of the welded joint are achieved. Measuring fillet weld size allows you to ensure that the weld meets the requirements specified in welding codes and standards. It also helps in detecting any potential issues or defects in the weld, making it a crucial step in quality control.
Needed Materials
Given below is a list of materials you will need to measure fillet weld size:
- Welding Gauge
- Fillet Weld Size Gauge
- Magnifying Glass
- Vernier Caliper
- Digital Measuring Tape
- Ruler or Measuring Tape
11 Step-by-step Guidelines on How to Measure Fillet Weld Size
Step 1: Clean the Weld
Before measuring the fillet weld, make sure to clean any debris or spatter from its surface using a wire brush or grinding tool. This will enable you to get accurate measurements. You can also use a degreasing agent to remove any oil or dirt that may affect the accuracy of the measurements. If the weld is located in a tight or hard-to-reach area, use compressed air to blow away any debris. This will ensure that the surface is clean and ready for measurement.
Step 2: Identify the Weld
The next step is to identify the fillet weld you want to measure. This will help you focus on the particular weld and avoid any confusion or errors in measurement. It is also essential to determine the type of fillet weld, whether it is a convex or concave fillet weld. This information will be useful in selecting the right welding gauge and measuring technique.

Step 3: Select the Appropriate Welding Gauge
A welding gauge is a handy tool that helps in accurately measuring different aspects of a weld, including fillet weld size. Select a welding gauge with the right dimensions for your fillet weld size range. Make sure it has both convex and concave faces to measure different types of fillet welds. You can also use a fillet weld size gauge, which is specifically designed for measuring fillet welds.
Step 4: Determine the Size Range
Before taking measurements, determine the size range required based on the welding code or standard being followed. The size range is usually indicated in fractions of an inch or millimeters. It is essential to have this information beforehand so that you can select the correct welding gauge and avoid any errors in measurement. It is also crucial to take multiple measurements at different points along the weld to ensure consistency and accuracy.
Step 5: Use a Magnifying Glass
For smaller fillet weld sizes, it may be challenging to get an accurate measurement with the naked eye. In such cases, use a magnifying glass or a microscope to view the weld more closely. This will help you measure the fillet weld size more precisely. The use of a magnifying glass is also necessary to detect any potential defects or imperfections in the weld.
Step 6: Place the Gauge
Place the welding gauge on one side of the fillet weld and adjust it until both sides are flush against the base metal and the weld. Make sure that it is positioned perpendicular to the weld. If using a fillet weld size gauge, place it on the weld root in a similar manner. Otherwise, use the convex or concave face of the welding gauge depending on the type of fillet weld.
Step 7: Read the Measurement
Read the measurement indicated by the gauge, which will be the fillet weld size. If using a welding gauge, you can also use its sliding scale feature to get more accurate measurements between standard sizes. For fillet weld size gauges, the measurement is indicated by a notch or slot on the gauge that corresponds to a specific size range.
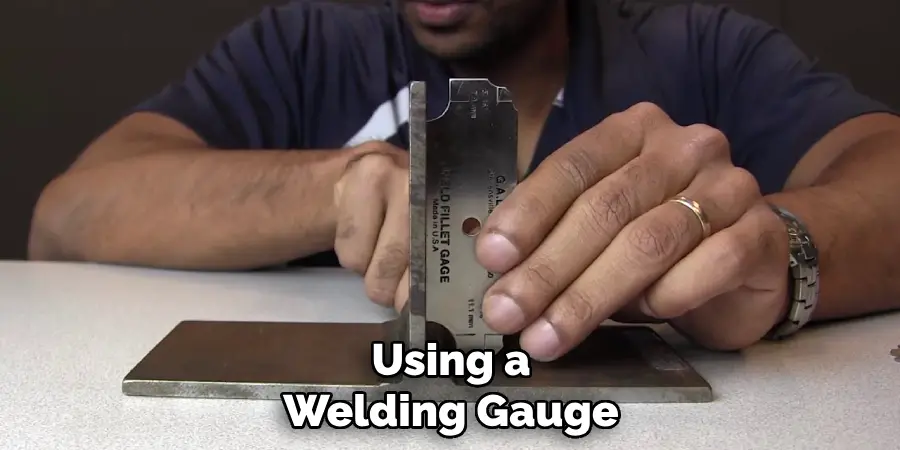
Step 8: Take Multiple Measurements
As mentioned earlier, it is crucial to take multiple measurements at different points along the fillet weld. This will help you ensure consistency and accuracy in your measurement. You can also average out the measurements to get a more precise value for the fillet weld size. If there are any significant variations in the measurements, it may indicate an issue with the weld that needs to be addressed.
Step 9: Measure Fillet Weld Length and Throat
Apart from measuring the size of the fillet weld, it is also essential to measure its length and throat. The length is the distance along the weld’s face or surface, while the throat is the distance from the root of the weld to its face. These measurements are necessary to ensure that the length and throat dimensions meet the standards specified in welding codes.
Step 10: Use Vernier Caliper or Digital Measuring Tape
For more accurate and precise measurements, you can use a Vernier caliper or digital measuring tape. These tools allow you to measure fillet weld size in fractions of an inch or millimeters, making them ideal for more stringent requirements. Place the caliper’s jaws or measuring tape on either side of the fillet weld and take the measurement as you would with a standard ruler. It is essential to note the units used in the welding code or standard being followed.
Step 11: Record and Verify Measurements
Finally, it is crucial to record all the measurements taken for each fillet weld and verify them against the required size range specified in the welding code. Make sure to note any significant variations or deviations from the standard. If needed, re-measure any questionable areas to ensure accuracy. This step is crucial for quality control and ensuring that the fillet weld meets all requirements. But most importantly, it is essential to follow all safety precautions and guidelines when handling any welding tools or equipment.
Following these steps on how to measure fillet weld size will help you accurately measure the fillet weld size and ensure that it meets all required standards. It is an essential part of quality control in welding processes, and should not be overlooked. Regularly checking fillet weld size also helps identify any potential defects or issues early on, preventing more significant problems down the line. By using the appropriate tools and techniques, you can ensure the quality and integrity of your fillet welds, resulting in stronger and more reliable structures.

Frequently Asked Questions
Q1. What is the Purpose of Measuring Fillet Weld Size?
A1. The measurement of fillet weld size is essential for quality control and ensuring that it meets the required standards specified in welding codes or standards. It also helps identify any potential defects or issues early on, preventing further problems down the line.
Q2. What Are Some Common Tools Used to Measure Fillet Weld Size?
A2. Some common tools used to measure fillet weld size include welding gauges, fillet weld size gauges, Vernier calipers, and digital measuring tapes.
Q3. Are There Different Types of Fillet Welds That Require Different Measuring Techniques?
A3. Yes, there are different types of fillet welds such as convex, concave, and straight that may require different measuring techniques. It is essential to follow the guidelines specified in the welding code or standard being followed. However, using a standard welding gauge can measure most types of fillet welds accurately.
Q4. Can I Use a Standard Ruler to Measure Fillet Weld Size?
A4. While you can use a standard ruler to get an approximate measurement, it is recommended to use more accurate tools such as welding gauges or Vernier calipers for precise measurements. These tools allow you to measure fillet weld size in fractions of an inch or millimeters, making them ideal for more stringent requirements.
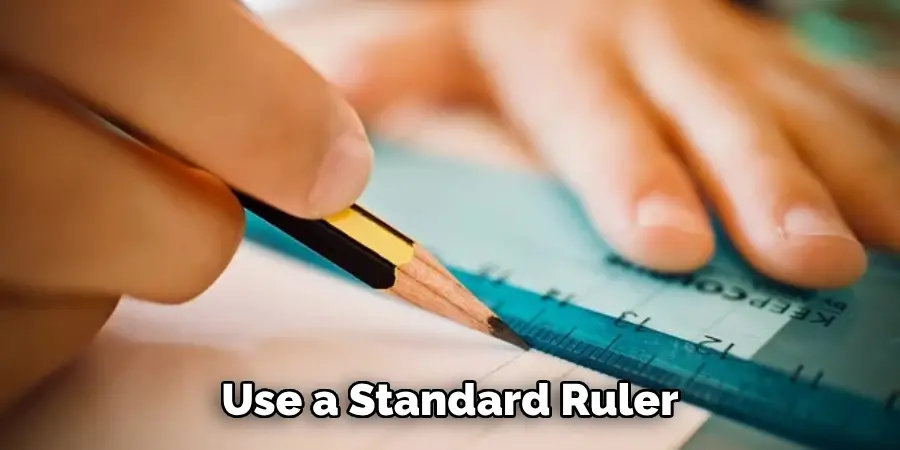
Conclusion
In conclusion on how to measure fillet weld size, measuring fillet weld size may seem like a daunting task, but with the right tools and knowledge, it can be easily achieved. Remember to always use the appropriate measurement tool and technique for accurate results. Don’t be afraid to seek help or ask questions if you’re unsure of anything – safety should always come first when working with welding equipment. Additionally, take the time to properly inspect and measure your welds, as they are crucial in ensuring the strength and integrity of your project. And finally, don’t forget to keep practicing and honing your skills – the more you measure, the better you become at it.
So go out there and confidently measure your fillet welds with precision and accuracy! As a final call to action, share this valuable information with others in the welding community and let’s continue to improve our skills together for a better future of construction and fabrication. Remember, no project is too big or too small – all fillet welds deserve proper measurement to ensure quality results. Happy welding!
Edmund Sumlin is a skilled author for Metal Fixes, bringing 6 years of expertise in crafting a wide range of metal fixtures. With a strong background in metalwork, Edmund’s knowledge spans various types of fixtures, from decorative pieces to functional hardware, blending precision with creativity. His passion for metalworking and design has made him a trusted resource in the industry.
Professional Focus:
- Expert in Metal Fixtures : Edmund aesthetic specializes in creating durable and innovative metal fixtures, offering both appeal and functionality. His work reflects a deep understanding of metalworking techniques and materials.
- Sustainability Advocate : He is dedicated to using sustainable practices, ensuring that every fixture is crafted with eco-friendly methods while maintaining high-quality standards.
In his writing for Metal Fixes, Edmund provides valuable insights into the latest trends, techniques, and practical advice for those passionate about metal fixtures, whether they are professionals or DIY enthusiasts. His focus on combining artistry with engineering helps others discover the true potential of metal in design.