Are you having trouble measuring the size of the nuts? Look no further, as we have a guide on how to measure nut size accurately and easily. As nuts come in various shapes and sizes, it can be challenging to determine their size accurately.
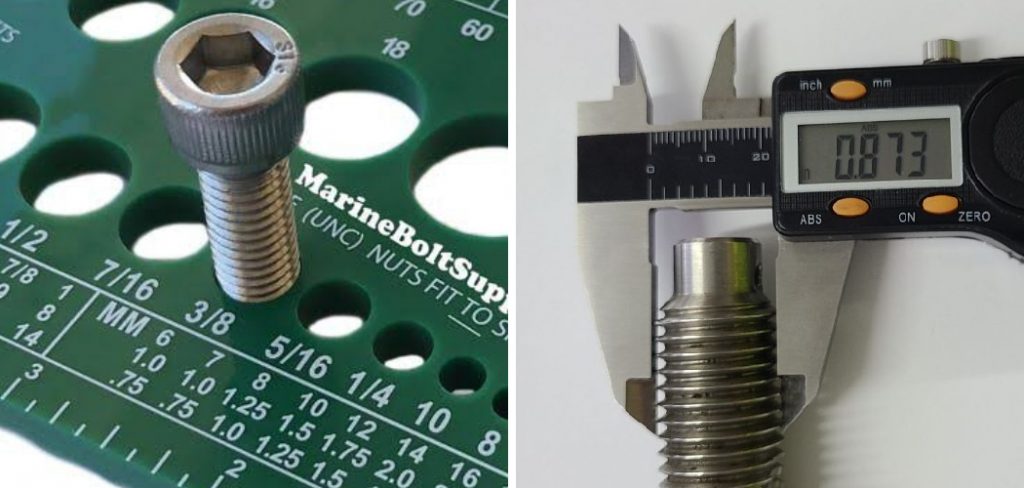
Measuring the nut size accurately is crucial for ensuring the proper fit and function of nuts and bolts in various applications, from simple household repairs to complex machinery maintenance. Misjudging the size can lead to improper fitting, potentially causing mechanical failures or safety hazards.
This guide will walk you through different methods and tools for measuring nut size effectively. This will enable you to select the correct hardware for your projects and maintain operational efficiency and safety.
What Will You Need?
Before we begin, we must have the right tools and materials on hand to ensure accurate measurements. Here are the things you will need:
- A set of precision measuring tools such as calipers or a ruler
- A nut size chart or guide for reference
- Optional: Thread gauge or thread pitch gauge (if measuring threaded nuts)
- Optional: Nut/bolt sizing template (for a more visual approach)
It’s also important to have good lighting and a flat surface to work on for easier measurement.
10 Easy Steps on How to Measure Nut Size
Step 1. Identify the Type of Nut:
Begin by determining the type of nut you are dealing with. Nuts can vary widely in design, such as hex nuts, square nuts, wing nuts, and cap nuts.
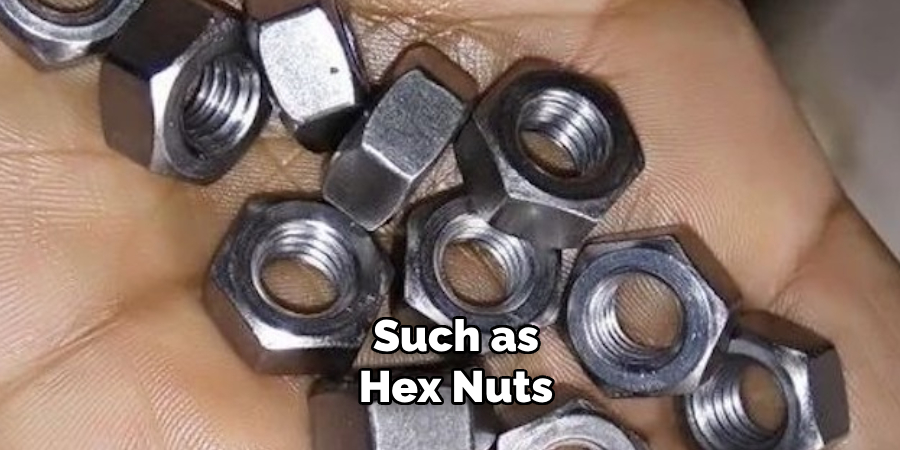
Each type of nut has unique features and uses, and recognizing these differences can streamline your measurement process. For example, a hex nut has a six-sided shape, which may require different handling and measuring techniques than a wing nut, which includes protruding wings for hand-tightening.
Knowing the specific type of nut will help you select the appropriate tools and reference charts for accurate measurement, ensuring that you get a precise and reliable reading.
Step 2. Clean the Nut:
Before taking any measurements, it’s crucial to ensure the nut is clean and free of debris, rust, or other contaminants. Dirt and grime can affect the accuracy of your measurements.
Use a wire brush or a cloth to thoroughly clean the nut’s surface. For persistent rust or grease, consider using a specialized cleaning solution.
A clean nut offers a smooth surface for your measuring tools, thus improving the precision of your results. Once the nut is clean, you’re ready to measure its size.
Step 3. Measure the Width Across Flats (WAF):
Using a caliper or a ruler, measure the distance across the nut’s flats, which are the parallel sides.
This dimension is often referred to as the width across flats (WAF) and is one of the most critical measurements for determining the correct nut size. For a hex nut, you will measure the distance between two opposite flats.
Ensure that the caliper or ruler is held perpendicular to the flats for an accurate reading. Record the measurement.
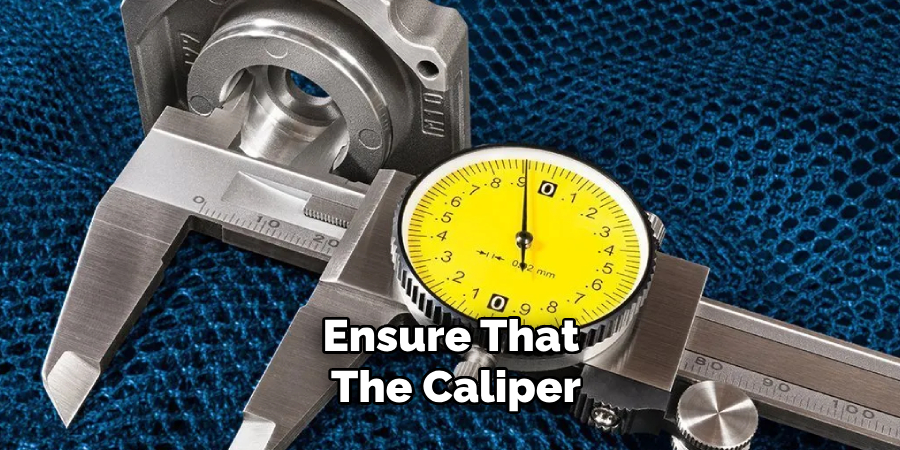
Step 4. Measure the Diameter:
When dealing with a threaded nut, you must also measure its inside diameter. Using a caliper, measure the distance across the inside of the nut from one inner edge to the opposite inner edge.
This measurement is crucial when matching the nut to a specific bolt diameter. Be precise and take your time to get an accurate reading, as even small discrepancies can affect the fit and function of the nut and bolt assembly.
Step 5. Measure the Height:
To ensure a perfect fit, measure the nut’s height. Place the nut on a flat surface, and use the caliper to measure the distance from the base to the top of the nut. This height is essential, especially when working with nuts that must fit into specific machinery or assembly spaces.
The height can also influence the grip and stability of the nut when fastened.
Step 6. Measure the Thread Pitch (if applicable):
For threaded nuts, measuring the thread pitch, which is the distance between threads is also necessary.
To do this, use a thread pitch gauge and match its teeth with the nut’s threads. This measurement is important to ensure the nut properly fits onto the corresponding bolt with matching threads.
Step 7. Record Your Measurements:
Once you have taken all the necessary measurements, ensure to record them accurately. Note down the Width Across Flats (WAF), diameter, height, and thread pitch (if applicable).
Keeping these records will assist you in finding the exact replacement or compatible components, ensuring that you avoid any guesswork in the future.
Step 8. Compare with a Nut Size Chart:
With your recorded measurements in hand, it’s time to reference a nut-size chart or guide.
These charts provide standard dimensions for various nut sizes and types, allowing you to match your measurements with the corresponding standard size. Locate the Width Across Flats (WAF), diameter, height, and thread pitch in the chart to find the exact specifications of your nut.
This comparison ensures that you have an accurate understanding of the nut’s size and can select the right replacement or compatible parts for your project.
Step 9. Use a Nut/Bolt Sizing Template (optional):
For a more visual approach, you can also use a nut/bolt sizing template to match your nut with the correct bolt diameter.
These templates usually have holes of various sizes that correspond to standard bolt diameters. By fitting the nut into the appropriate hole, you can quickly determine its size without referring to charts or taking measurements manually.
Step 10. Double Check Your Measurements:
Accuracy is paramount when measuring nut sizes, as even minor discrepancies can lead to improper fits and potential failures in mechanical assemblies. Therefore, it’s essential to double-check your measurements.
Start by remeasuring the Width Across Flats (WAF) to confirm your initial reading, ensuring the caliper or ruler is placed perpendicular to the flats every time.
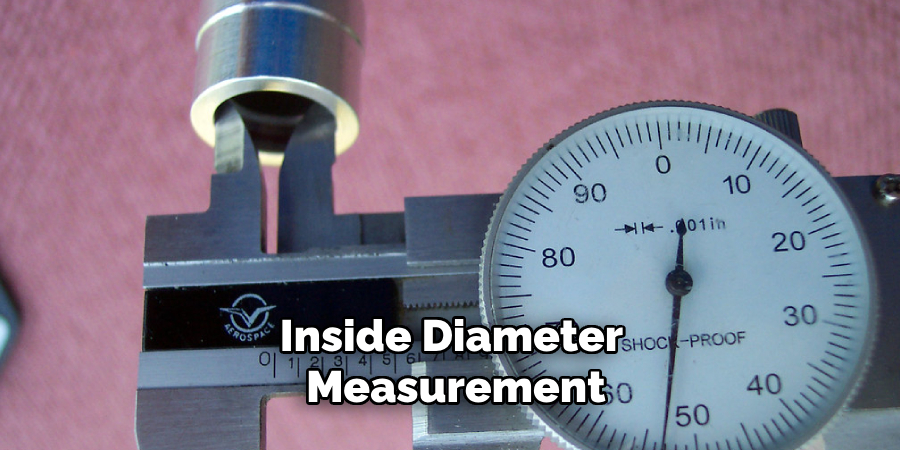
Next, verify the inside diameter measurement of any threaded nut by recalibrating your caliper and repeating the measurement process, ensuring all tools are clean and debris-free.
If thread pitch is part of your measurements, revisit this using your thread pitch gauge, aligning the teeth precisely with the nut’s threads and checking for a consistent match. When confirming the nut’s height, ensure it is placed flat on a stable surface and the caliper or ruler is aligned perfectly perpendicular to avoid parallax errors.
Comparing these rechecked measurements against your recorded data can help identify any inconsistencies and ensure that your dimensions are exact.
This final step reinforces the reliability of your measurements, providing peace of mind that the nut will fit perfectly into your intended application. Taking the extra time for this verification can save you from future complications and assure the integrity of your mechanical assemblies.
By following these steps, you’ll be able to accurately measure nut sizes and confidently select the correct replacement or compatible parts for your project.
5 Things You Should Avoid
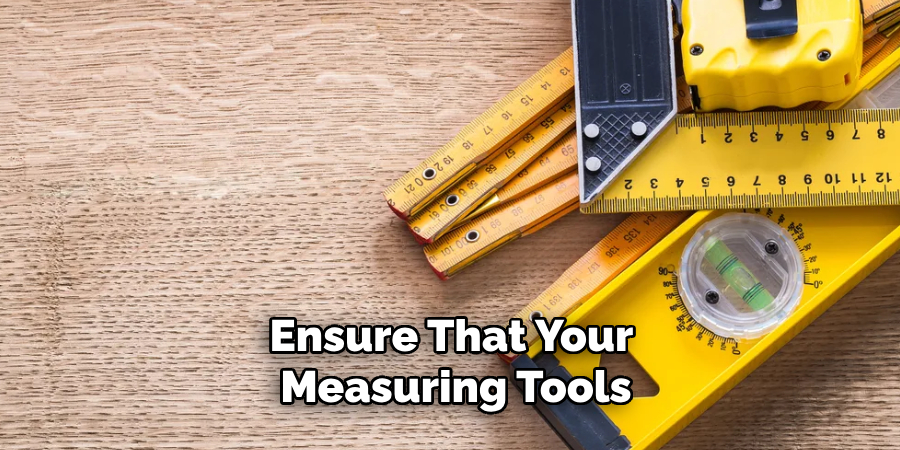
- Using Improper Tools: One of the most common mistakes is using inappropriate or imprecise tools to measure nut dimensions. Tools such as a ruler with faded markings or a worn-out caliper can lead to inaccurate readings. Always ensure that your measuring tools are in good condition and appropriate for the task at hand.
- Ignoring Cleanliness: Dirt, grease, or other contaminants on the nut can interfere with accurate measurements. Avoid measuring a nut that hasn’t been cleaned properly, as debris can cause incorrect readings. A clean nut ensures a smooth and accurate surface for your tools to work on.
- Not Verifying Calibration: Measuring instruments like calipers and thread pitch gauges need to be calibrated regularly to ensure precision. Relying on uncalibrated tools can lead to incorrect measurements, affecting the overall fit and function of the nut and bolt assembly. Always check and calibrate your tools before use.
- Measuring at Angles: When measuring dimensions such as Width Across Flats (WAF) or diameter, it is crucial to keep your measuring tool perpendicular to the nut’s flats. Measuring at an angle can result in inaccurate dimensions and mislead you when selecting or replacing the correct nut size.
- Rushing the Process: Measuring nut size requires patience and attention to detail. Rushing through the process can cause errors in reading and recording measurements. Take your time to ensure each dimension is measured accurately and double-check your work to avoid any potential issues.
By avoiding these mistakes, you can ensure accurate and reliable measurements every time, making your projects run smoothly.
Conclusion
How to measure nut size is a vital skill for anyone working with mechanical assemblies or needing to replace or match nuts and bolts.
Following a systematic approach ensures precision and reliability in your measurements.
By using appropriate tools such as calipers, thread pitch gauges, and nut sizing templates, you can determine the critical dimensions of Width Across Flats (WAF), diameter, height, and thread pitch.
Recording and cross-referencing these measurements with standard-size charts further enhances accuracy.
Additionally, double-checking your measurements and avoiding common pitfalls like using improper tools, ignoring cleanliness, and rushing the process will help prevent errors.
Mastering these techniques guarantees that you will select the correct replacement parts, ensuring seamless and efficient project execution.
Edmund Sumlin is a skilled author for Metal Fixes, bringing 6 years of expertise in crafting a wide range of metal fixtures. With a strong background in metalwork, Edmund’s knowledge spans various types of fixtures, from decorative pieces to functional hardware, blending precision with creativity. His passion for metalworking and design has made him a trusted resource in the industry.
Professional Focus:
- Expert in Metal Fixtures : Edmund aesthetic specializes in creating durable and innovative metal fixtures, offering both appeal and functionality. His work reflects a deep understanding of metalworking techniques and materials.
- Sustainability Advocate : He is dedicated to using sustainable practices, ensuring that every fixture is crafted with eco-friendly methods while maintaining high-quality standards.
In his writing for Metal Fixes, Edmund provides valuable insights into the latest trends, techniques, and practical advice for those passionate about metal fixtures, whether they are professionals or DIY enthusiasts. His focus on combining artistry with engineering helps others discover the true potential of metal in design.