MIG welding, also known as Gas Metal Arc Welding (GMAW), is a popular welding technique used in various industries, including automotive repairs. When it comes to repairing exhaust systems, MIG welding offers several advantages. Its ability to create strong, leak-free welds and its versatility makes it an ideal choice for ensuring the durability and performance of exhaust pipes.
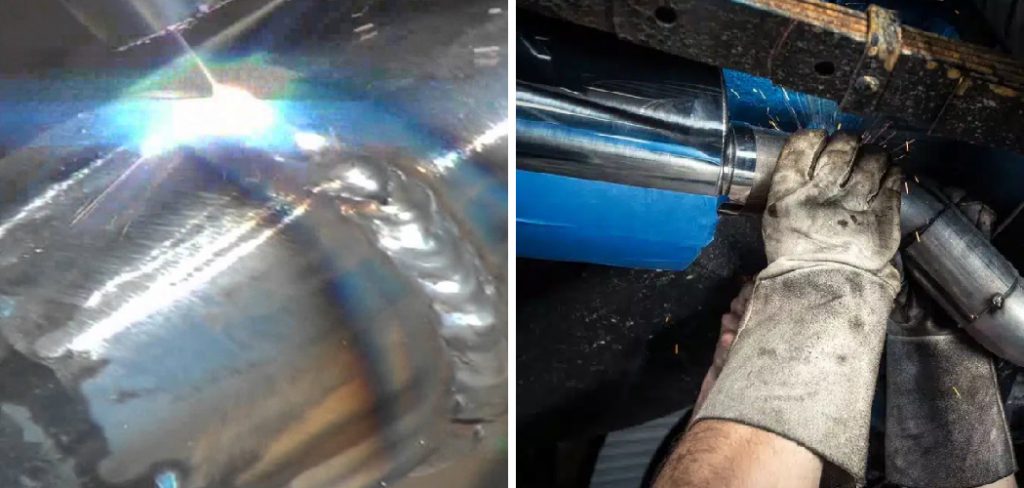
However, achieving a successful MIG weld on an exhaust pipe requires proper techniques and attention to detail. This comprehensive step-by-step guide will walk you through MIG welding an exhaust pipe effectively. From preparation to post-weld maintenance, we will provide you with valuable tips and insights to ensure safety, quality, and long-lasting repair.
Following this guide will give you the knowledge and confidence to perform exhaust pipe repairs with MIG welding. Let’s dive in and learn how to MIG weld an exhaust pipe step by step, ensuring a strong and reliable weld for your automotive needs.
Keyword: “how to mig weld exhaust pipe”
Understanding the Basics of MIG Welding
What is MIG Welding?
MIG welding, or Metal Inert Gas welding, is a versatile and widely used welding technique. It uses a continuous wire electrode, typically made of steel, and a shielding gas to create heat and combine metal pieces. The shielding gas, usually a mixture of argon and carbon dioxide, protects the weld from atmospheric contaminants.
Explanation of MIG Welding
In MIG welding, the wire electrode is continuously fed through a welding gun, which also releases the shielding gas. An electrical arc generates intense heat as the wire electrode contacts the metal workpiece. This heat melts both the wire electrode and the metal pieces being joined, creating a pool of molten metal. As the pool solidifies, it forms a strong and durable weld.
Why MIG Welding is Ideal for Exhaust Pipes
MIG welding is particularly well-suited for exhaust pipe repairs due to its several advantages. Firstly, it allows for fast and efficient welding, making it a preferred choice for automotive repairs. Secondly, MIG welding is relatively easy to learn and use, making it accessible to both professionals and DIY enthusiasts. Lastly, MIG welding produces clean and precise welds, which ensures exhaust pipes’ integrity and leak-free performance. This welding technique is especially effective on thin sheet metal, like that used in exhaust pipes, providing a reliable and long-lasting repair solution.
Tools and Materials Needed for MIG Welding an Exhaust Pipe
To successfully MIG weld an exhaust pipe, you will need the following tools and materials:
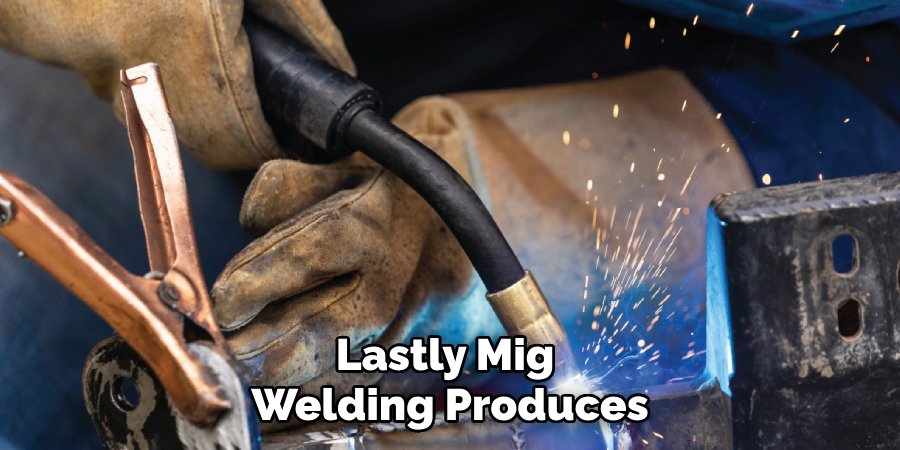
Welding Machine and Supplies
Choosing the right MIG welder is crucial for achieving professional welds on your exhaust pipe. Look for a welder with a power rating suitable for the thickness of the pipe. Typically, a 220V machine with a gas supply capability is recommended for exhaust welding. Additionally, you will need the following supplies:
- Shielding Gas: Usually, a mixture of 75% argon and 25% carbon dioxide (CO2) is recommended for MIG welding exhaust pipes.
- Welding Wire: It is essential to select the appropriate welding wire. ER70S-6 wire is commonly used for steel exhaust pipes.
Personal Safety Gear
Ensuring personal safety is paramount when MIG welding. The following safety gear is essential for protecting yourself during the welding process:
- Welding Helmet: Invest in a welding helmet with an appropriate shade for MIG welding. This will shield your eyes and face from intense light and sparks.
- Protective Gloves, Clothing, and Boots: Wear heat-resistant gloves, long-sleeve clothing, and safety boots to protect your hands, arms, and feet from sparks and heat.
- Respirator or Welding Fume Extractor: Proper ventilation is crucial when welding. Consider using a respirator or a welding fume extractor to protect yourself from harmful fumes and gases produced during welding.
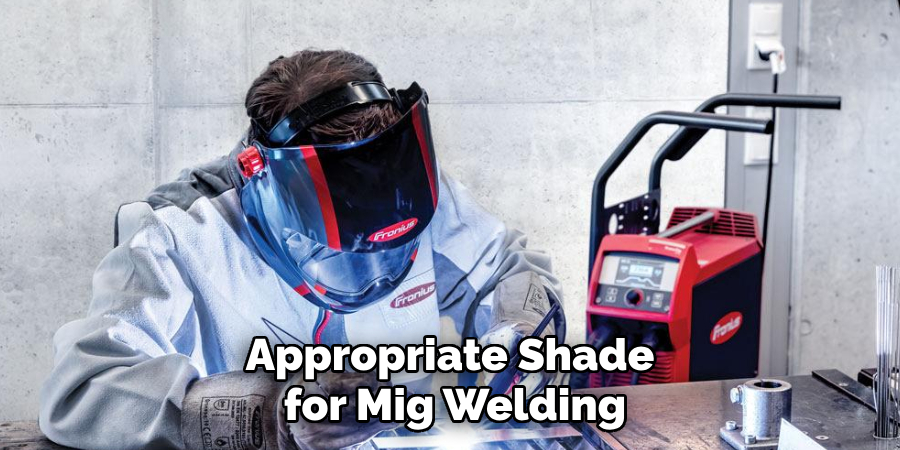
You can confidently proceed with MIG welding an exhaust pipe by ensuring you have the necessary tools, supplies, and safety gear, achieving secure and durable welds for effective repairs.
Preparing the Exhaust Pipe and Work Area
Before starting the MIG welding process on the exhaust pipe, it is crucial to adequately prepare both the pipe and the work area. Proper preparation ensures a clean surface for welding and creates a safe and efficient environment.
Cleaning the Exhaust Pipe
Cleaning the exhaust pipe is essential to prevent weld contamination and ensure a strong and durable bond. Here are some important points to consider when cleaning the pipe:
- Importance of Cleaning: Cleaning the exhaust pipe removes rust, dirt, and oil, which can interfere with the welding process and compromise the quality of the weld. A clean surface promotes better adhesion and weld penetration.
- Methods for Cleaning: There are several methods for cleaning the exhaust pipe. One common approach is using a wire brush to remove loose rust and dirt. Sandpaper or a grinder can be used to eliminate more stubborn rust or corrosion. Additionally, wipe down the surface with a suitable cleaner or solvent to ensure that it is free from any oils or contaminants.
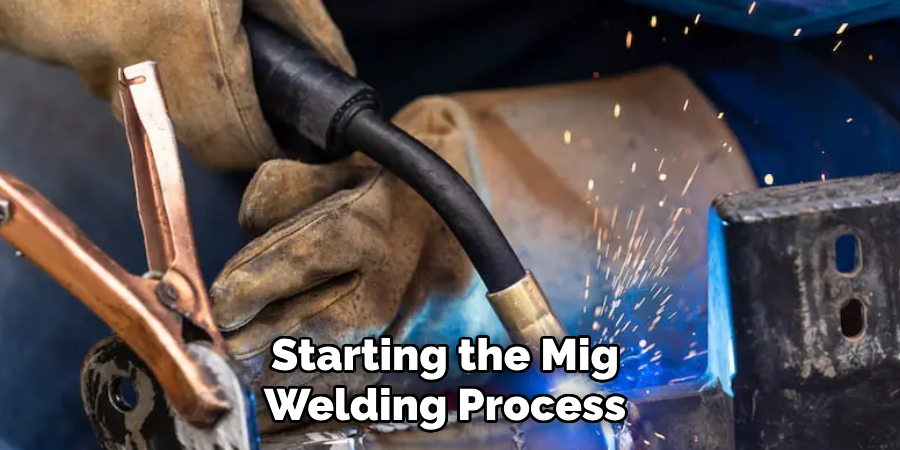
Preparing the Work Area
In addition to preparing the exhaust pipe, it is essential to set up a well-ventilated work area for welding. Consider the following points when preparing the work area:
- Ventilation: MIG welding produces fumes and gases that can be harmful if inhaled. To minimize exposure to these byproducts, working in a well-ventilated area is crucial. Ensure proper ventilation in your workspace, either by welding in a well-ventilated garage or using a fume extraction system.
- Securing the Exhaust Pipe: To ensure stability and ease of welding, securing the exhaust pipe in position is important. This can be done using clamps or a welding jig. Securely fastening the pipe prevents unwanted movement during welding, ensuring accurate and precise welds.
Properly cleaning the exhaust pipe and preparing the work area creates an optimal environment for successful MIG welding. These steps contribute to the quality and durability of the weld, ensuring effective repairs and a long-lasting exhaust system.
Setting Up the MIG Welder for Exhaust Pipe Welding
To successfully weld an exhaust pipe, it is crucial to set up your MIG welder properly. The following steps will guide you in preparing the welder for optimal performance and ensuring high-quality welds.
Choosing the Correct Settings
When welding exhaust pipes, selecting the right settings on your MIG welder is vital to achieving strong and clean welds. Consider the following factors for setting up your welder:
Wire Feed Speed and Voltage: One key setting to adjust is the wire feed speed. For thinner exhaust pipe thickness, typically around 0.030″, using a thinner wire like 0.030″ is recommended. Adjusting the voltage settings ensures proper penetration without burning through the thin metal.
Amperage Adjustment: Adjusting the machine for the appropriate amperage is crucial to prevent overheating and burning through the exhaust pipe. Ensure that the amperage is set to a level that provides sufficient heat for welding but not excessive to avoid damaging the metal.
Gas Settings and Flow Rate: Shielding gas protects the weld from oxidation and ensures a clean weld. Adjust the shielding gas flow rate to a suitable level, typically around 20-25 CFH (cubic feet per hour) for MIG welding on exhaust pipes. This ensures proper gas coverage during the welding process.
You can achieve precise and durable welds on exhaust pipes by carefully setting up your MIG welder and choosing the correct wire feed speed, voltage, amperage, and gas flow rate. These settings contribute to the overall quality and longevity of the exhaust system.
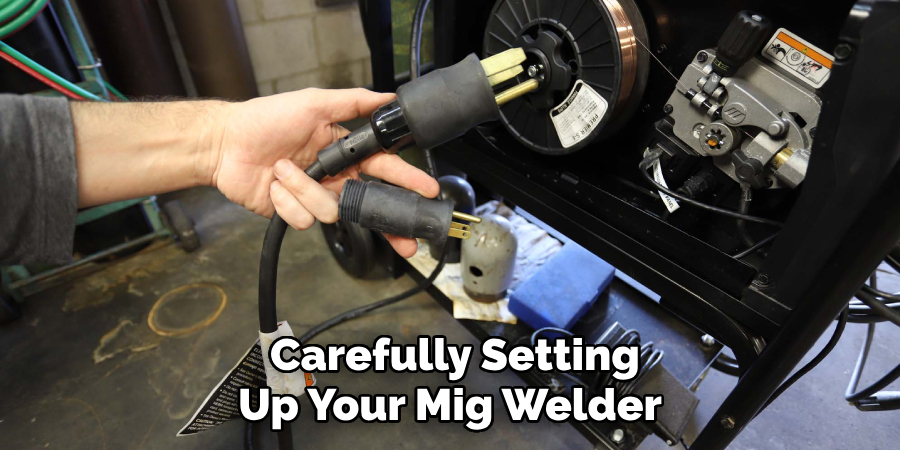
How to Mig Weld Exhaust Pipe: MIG Welding the Exhaust Pipe
When it comes to MIG welding the exhaust pipe, following proper techniques and strategies is vital to ensure a strong and durable weld. Here is a step-by-step guide to help you achieve excellent results.
Making the First Pass:
To start, position the MIG welder at one end of the exhaust pipe, maintaining a consistent arc length. This helps ensure proper heat control and prevents burn-through. As you weld, move the MIG welder in a steady pattern, such as a “C” or circular motion, to create a strong and continuous weld. Be sure to work in sections to avoid overheating the metal and causing distortion or burn-through.
Welding Technique:
Maintaining the proper torch angle is crucial for effective penetration and control. Hold the torch at a 15-20 degree angle from the vertical position, allowing the wire to penetrate the joint fully. Additionally, controlling the speed of the weld is essential to ensure uniformity and strength. Move the torch at a steady pace, neither fast nor slow, to achieve consistent bead formation and proper fusion.
Checking Weld Quality:
After completing the weld, visually inspect the weld bead to ensure smoothness and uniformity. A well-executed weld should have a consistent width and penetration. Look for improper fusion or undercut signs that can weaken the weld. If any issues are detected, address them promptly by re-welding or making necessary adjustments to the welding parameters.
Following these techniques and inspecting the weld quality, you can achieve reliable and long-lasting welds on exhaust pipes. Remember to practice proper safety precautions, such as wearing appropriate protective gear and working in a well-ventilated area, to ensure a successful and safe welding process.
Post-Weld Inspection and Cleaning
After completing the welding process, it is crucial to conduct a thorough post-weld inspection to ensure the quality and integrity of the weld. This involves checking for porosity, cracks, and incomplete fusion in the weld. One method is to lightly tap the weld with a hammer and listen for hollow sounds, which can indicate a weak weld.
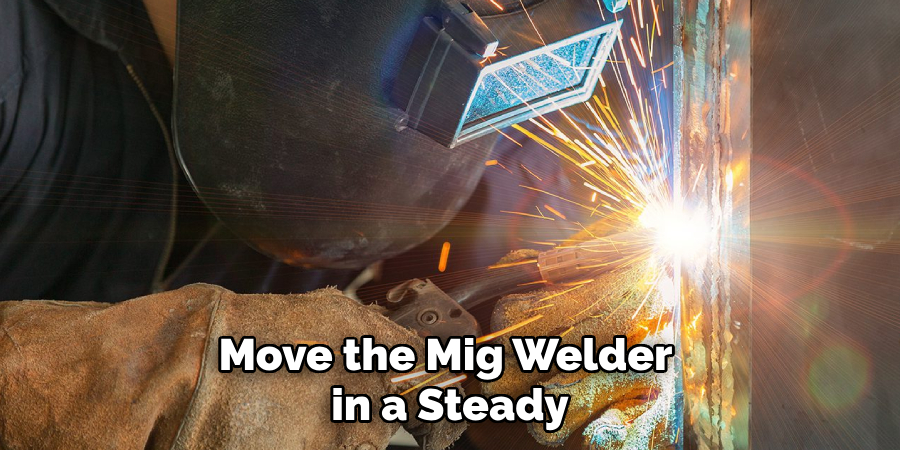
Inspecting the Weld:
To ensure a strong and reliable weld, visually examine the weld bead for any signs of defects or irregularities. Look for indications of porosity, which are small holes caused by gas entrapment and cracks that may compromise the weld’s strength. Additionally, check for incomplete fusion, where the weld did not fully bond with the base metal. Identifying these issues early allows for prompt re-welding or adjustments to the welding parameters.
Cleaning the Weld Area:
It is essential to clean the weld area after inspection to ensure optimal functionality and appearance. Use a wire brush or grinder to remove any slag or excess weld material from the surface. This helps create a clean surface for further processing or coating. If necessary, use a grinder to smooth and clean the weld bead, improving its appearance and functionality.
By performing a diligent post-weld inspection and properly cleaning the weld area, you can ensure the weld’s quality, strength, and longevity on your exhaust pipes. Remember to prioritize safety by wearing appropriate protective gear and working in a well-ventilated area during the inspection and cleaning process.
Troubleshooting Common Issues When MIG Welding Exhaust Pipes
When MIG welding exhaust pipes, several common issues can arise, requiring troubleshooting to ensure a high-quality weld. Here are two key issues and their respective solutions:
Burn-Through or Weak Welds
Burn-through or weak welds can occur due to excessive heat buildup or improper welding parameters. To fix this issue, you can:
- Adjust the welding speed, voltage, or wire feed to achieve better control over the heat input.
- Weld in short bursts while moving at a steady pace to avoid excessive heat buildup.
- Consider using a lower wire feed speed or thinner gauge material to reduce the risk of burn-through.
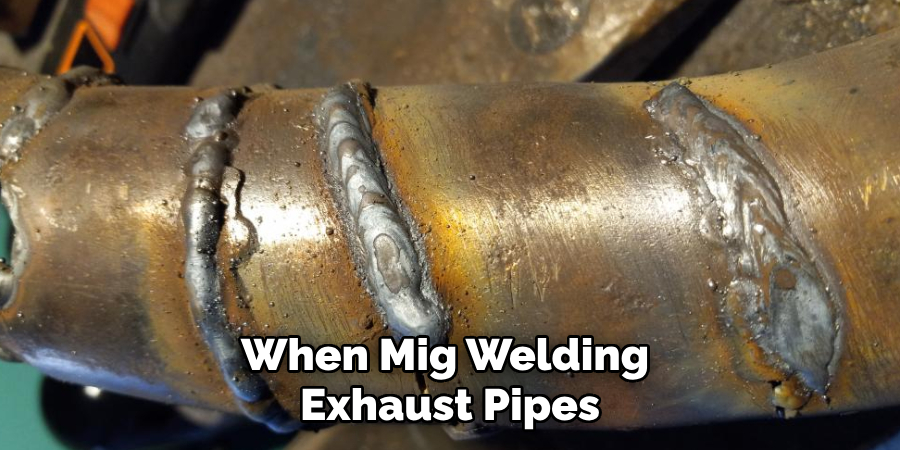
Inconsistent Gas Flow or Poor Shielding
Poor shielding gas flow or leakage can result in oxidation or contamination of the weld, leading to weak joints. To address this, follow these steps:
- Check for any signs of gas leakage or poor flow, such as hissing sounds or visible gas escaping.
- Ensure the gas supply is properly connected and the flow rate is set correctly.
- Clean the gas nozzle and contact tip to remove any debris obstructing the gas flow.
- Verify that the shielding gas used is appropriate for the specific welding process and materials being welded.
You can achieve robust and reliable welds when MIG welding exhaust pipes by troubleshooting these common issues and implementing the suggested solutions. Remember to prioritize safety throughout the welding process to ensure a successful outcome.
Final Steps and Maintenance After Welding
After completing the welding process, a few important steps must be taken to ensure the longevity and quality of the weld on the exhaust pipe.
Cooling and Checking the Weld
Allow the exhaust pipe to cool naturally before handling to prevent warping or cracking. Once cooled, double-check the weld to ensure there are no signs of defects or further issues that may have developed during the cooling process.
Post-Weld Maintenance
Clean up the welding area by removing any debris or leftover materials. Properly dispose of consumables like welding wire and empty shielding gas cylinders according to local regulations. Finally, store the welder and tools in a safe and secure location, ready for future use.
By following these final steps and practicing regular maintenance, you can ensure the weld on your exhaust pipe remains strong and reliable for years to come.
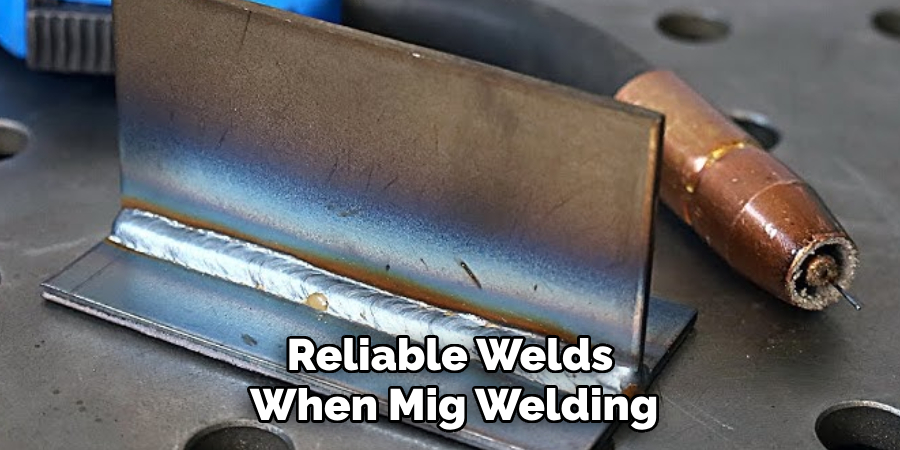
Conclusion
In conclusion, MIG welding an exhaust pipe requires proper preparation, attention to detail, and adherence to safety measures. You can achieve a strong and durable weld by following the step-by-step process of cleaning, fitting, tacking, and welding. Remember to maintain proper ventilation, use the appropriate safety gear, and be mindful of the specific requirements of your exhaust pipe material. After welding, allow the pipe to cool naturally and inspect the weld for any defects. Also, perform post-weld maintenance by properly cleaning the area and storing your tools. MIG welding your exhaust pipe not only ensures a reliable repair but also offers the satisfaction of a job well done and cost-saving benefits. So, equip yourself with the necessary knowledge and technique to confidently tackle exhaust pipe repairs with MIG welding. Thanks for reading our post about how to mig weld exhaust pipe.
Edmund Sumlin is a skilled author for Metal Fixes, bringing 6 years of expertise in crafting a wide range of metal fixtures. With a strong background in metalwork, Edmund’s knowledge spans various types of fixtures, from decorative pieces to functional hardware, blending precision with creativity. His passion for metalworking and design has made him a trusted resource in the industry.
Professional Focus:
- Expert in Metal Fixtures : Edmund aesthetic specializes in creating durable and innovative metal fixtures, offering both appeal and functionality. His work reflects a deep understanding of metalworking techniques and materials.
- Sustainability Advocate : He is dedicated to using sustainable practices, ensuring that every fixture is crafted with eco-friendly methods while maintaining high-quality standards.
In his writing for Metal Fixes, Edmund provides valuable insights into the latest trends, techniques, and practical advice for those passionate about metal fixtures, whether they are professionals or DIY enthusiasts. His focus on combining artistry with engineering helps others discover the true potential of metal in design.