Operating a metal lathe is a fundamental skill in machining and manufacturing, essential for creating precise cylindrical shapes and threads in metalwork.
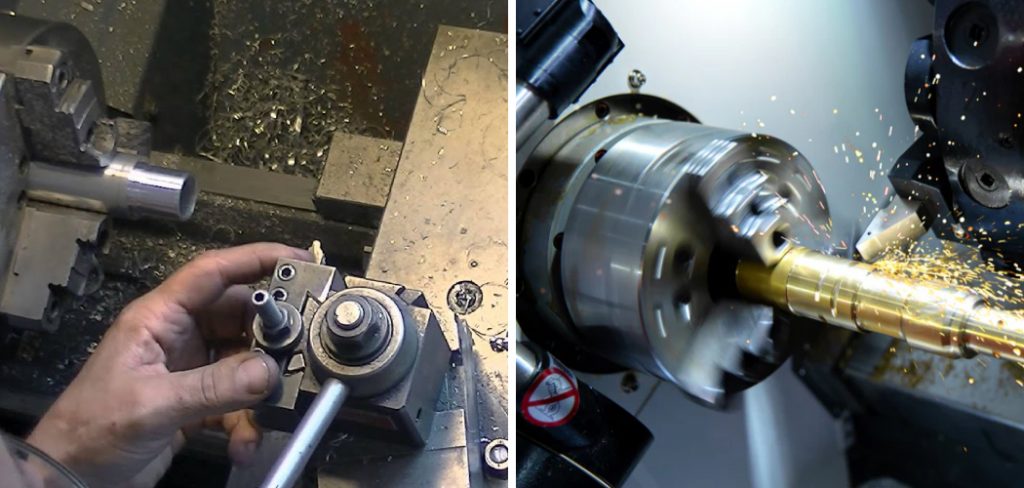
Whether you’re a hobbyist or a professional machinist, mastering the operation of a metal lathe opens doors to crafting intricate parts and components with accuracy and efficiency.
This versatile machine tool uses cutting tools to remove material from a rotating workpiece, allowing for a wide range of operations from turning and facing to grooving and drilling. Understanding the lathe’s components, such as the spindle, chuck, tool post, and carriage, is crucial for safe and effective operation.
This guide will provide a comprehensive introduction to operating a metal lathe, covering setup procedures, tool selection, basic turning techniques, and safety precautions. Whether you’re starting from scratch or looking to refine your skills, learning how to operate a metal lathe will empower you to tackle diverse machining projects with confidence.
Understanding the Metal Lathe
A metal lathe is a highly versatile machine tool designed for precisely shaping metal. At its core, the lathe operates by rotating the workpiece around a stationary cutting tool, which can be adjusted to achieve the desired cut.
To effectively use a metal lathe, it is essential to understand its key components and their functions.
Key Components
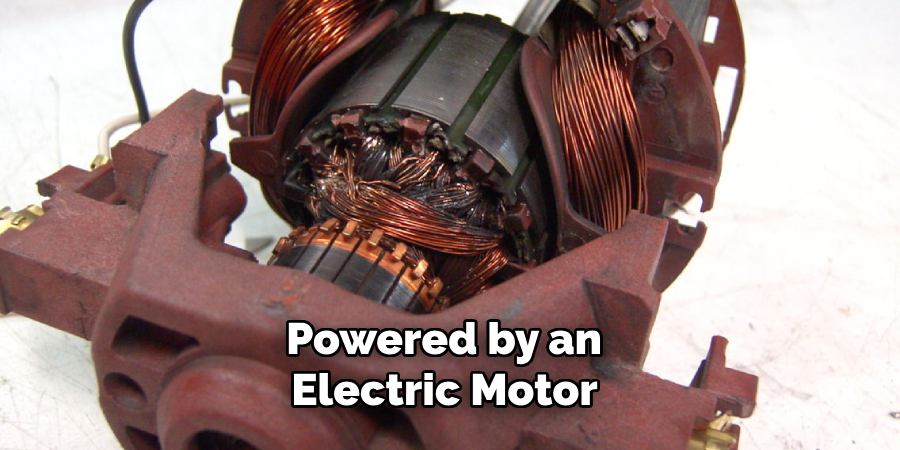
- Spindle: The spindle is the heart of the lathe, responsible for holding and rotating the workpiece. It is typically powered by an electric motor and can vary in speed to suit different machining operations.
- Chuck: Attached to the spindle, the chuck is a clamping device that securely holds the workpiece in place. Chucks may come in various forms, including three-jaw and four-jaw types, each suited for different precision requirements.
- Tool Post: The tool post is a fixture that holds the cutting tool in position. It allows for quick and precise adjustments, ensuring that the tool is correctly aligned with the workpiece.
- Carriage: The carriage slides along the lathe bed and supports the tool post and cutting tools. It can move longitudinally to perform cutting operations along the length of the workpiece.
- Lead Screw and Feed Rod: These components control the movement of the carriage. The lead screw is used for threading operations, while the feed rod is primarily for general cutting tasks.
10 Methods How to Operate a Metal Lathe
1. Understanding the Components of a Metal Lathe
Before operating a metal lathe, it’s essential to familiarize yourself with its components and functions. A typical metal lathe consists of the bed, headstock, tailstock, carriage, and tool post.
The bed is the base of the lathe, providing support and alignment for the other components. The headstock houses the motor and spindle, which rotates the workpiece. The tailstock supports the end of the workpiece and can hold tools such as drills.
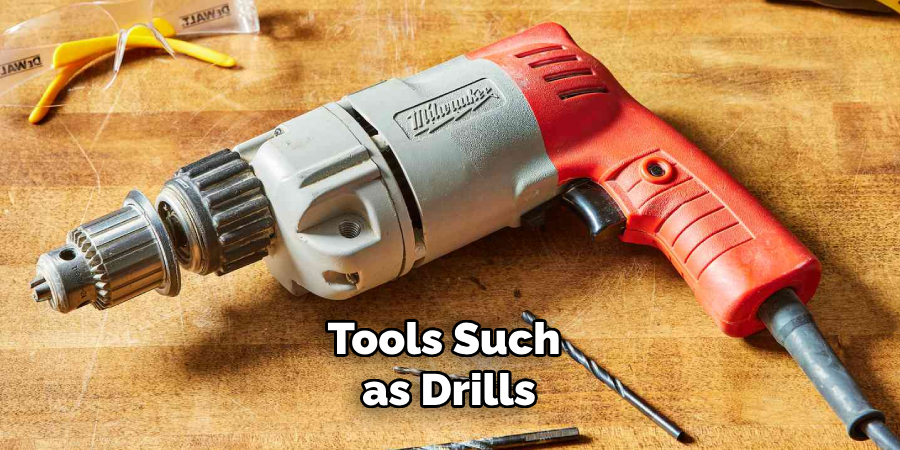
The carriage moves along the bed and holds the cutting tool, while the tool post allows for quick tool changes. Understanding these components and their functions is crucial for effective and safe operation.
2. Ensuring Safety Precautions
Safety is paramount when operating a metal lathe. Always wear safety goggles to protect your eyes from metal shavings and debris.
Use hearing protection if the machine is loud, and wear appropriate clothing, avoiding loose sleeves or jewelry that could get caught in the machinery. Before starting the lathe, ensure all guards are in place and the work area is free from obstructions. Familiarize yourself with the location of the emergency stop button.
Additionally, never leave the lathe unattended while it is running. Adhering to these safety precautions helps prevent accidents and injuries, ensuring a safe working environment.
3. Setting Up the Workpiece
Properly setting up the workpiece is essential for precision and safety. Begin by securing the workpiece in the lathe’s chuck or collet, ensuring it is centered and tightly clamped.
Use a dial indicator to check for runout and adjust the workpiece until it is properly aligned. For longer workpieces, support the free end with the tailstock to prevent deflection and vibration.
If the workpiece is irregularly shaped, use a faceplate or a steady rest for additional support. Ensuring the workpiece is securely and accurately mounted helps prevent errors and ensures smooth operation.
4. Selecting and Installing Cutting Tools
Choosing the right cutting tool is crucial for achieving the desired outcome. Common tools used on a metal lathe include turning tools, parting tools, threading tools, and boring bars.
Select a cutting tool appropriate for the material and type of cut you wish to make. Install the tool in the tool post, ensuring it is securely clamped and positioned correctly. The cutting edge should be at the center height of the workpiece to ensure proper cutting action.
Use a tool height gauge or a simple steel ruler to check and adjust the tool height. Proper tool selection and installation are vital for achieving accurate and clean cuts.
5. Setting the Cutting Parameters
Setting the appropriate cutting parameters, such as speed, feed, and depth of cut, is essential for efficient and precise machining. The cutting speed depends on the material and the type of cutting tool.
Consult the manufacturer’s recommendations or reference charts for the correct speed settings. Adjust the lathe’s speed control to the desired RPM. The feed rate, which determines the speed at which the tool moves along the workpiece, should be set according to the material and desired finish.
The depth of cut depends on the rigidity of the setup and the material’s machinability. Begin with light cuts and gradually increase the depth to avoid tool deflection and chatter. Proper cutting parameters ensure smooth and accurate machining.
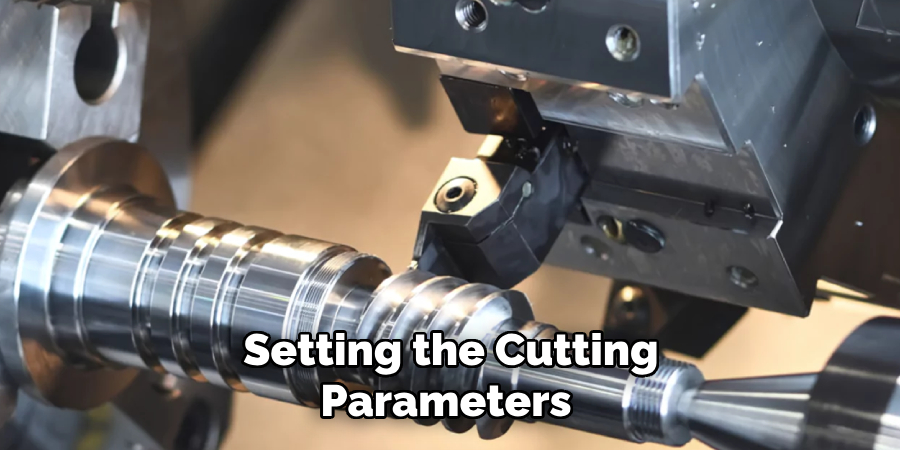
6. Performing Facing Operations
Facing is a fundamental operation used to create a flat surface perpendicular to the workpiece’s axis. To perform facing, secure the workpiece in the chuck and position the cutting tool near the outer edge of the workpiece. Set the lathe to a suitable speed and feed rate.
Engage the power feed or manually advance the carriage towards the center of the workpiece. Ensure the tool cuts evenly across the surface, removing a thin layer of material with each pass. Stop the lathe and measure the surface for flatness and squareness.
Adjust the tool and make additional passes if necessary. Proper facing techniques ensure a precise and flat surface, essential for subsequent operations.
7. Turning the Outside Diameter
Turning the outside diameter is a common operation to reduce the workpiece to the desired diameter.
Secure the workpiece in the chuck and position the cutting tool at the starting point. Set the lathe to the appropriate speed and feed rate. Engage the power feed or manually advance the carriage along the workpiece, making light cuts to remove material evenly.
Use a micrometer or caliper to measure the diameter and make adjustments as needed. For large diameter reductions, make multiple passes, gradually increasing the depth of cut. Proper turning techniques ensure a smooth and accurate cylindrical surface.
8. Drilling and Boring
Drilling and boring operations are used to create or enlarge holes in the workpiece. To drill a hole, secure the workpiece in the chuck and position the drill bit in the tailstock or a drill chuck.
Align the drill bit with the workpiece’s center and advance the tailstock quill to start drilling. Use cutting oil to reduce friction and heat. For boring, use a boring bar mounted in the tool post.
Position the boring bar at the hole’s opening and set the lathe to the appropriate speed and feed rate. Engage the power feed or manually advance the carriage to enlarge the hole. Proper drilling and boring techniques ensure accurate and clean holes.
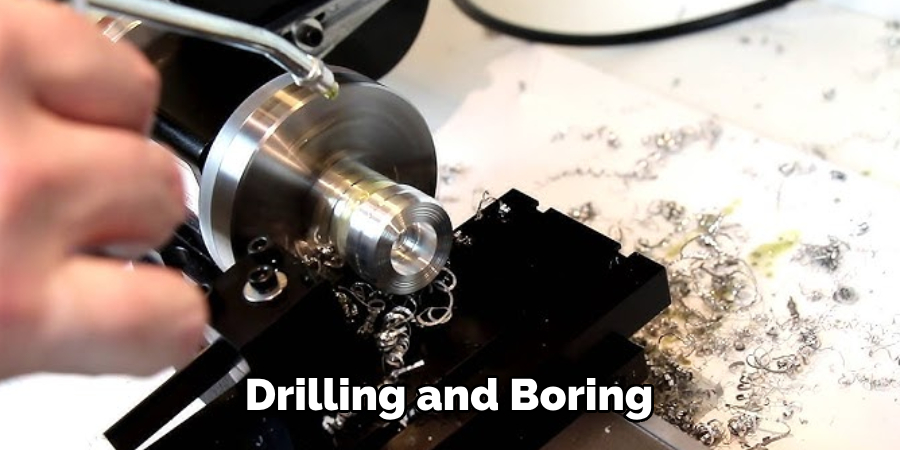
9. Thread Cutting
Thread cutting on a metal lathe is a precise operation used to create screw threads. Secure the workpiece in the chuck and install the threading tool in the tool post. Set the lathe to the appropriate speed and feed rate, and engage the lead screw to synchronize the tool’s movement with the spindle rotation.
Position the tool at the starting point and make a series of light cuts to form the thread profile. Use a thread pitch gauge to check the thread’s accuracy and make adjustments as needed. Proper thread cutting techniques ensure precise and functional threads for various applications.
10. Finishing and Polishing
Finishing and polishing operations enhance the surface quality and appearance of the workpiece.
After completing the primary machining operations, use a fine cutting tool to make light finishing passes, removing any remaining tool marks and achieving the desired surface finish. For polishing, use abrasive cloth or polishing compounds applied to a polishing wheel. Secure the workpiece in the chuck and set the lathe to a low speed.
Gently apply the abrasive cloth or polishing compound to the rotating workpiece, achieving a smooth and shiny surface. Proper finishing and polishing techniques ensure a high-quality final product with excellent surface finish.
Conclusion
Operating a metal lathe involves a combination of knowledge, skill, and attention to detail. From understanding the machine’s components to performing various machining operations, each method outlined in this guide plays a crucial role in achieving precision and safety.
By mastering these techniques, you can confidently operate a metal lathe, producing high-quality workpieces for various applications. Thanks for reading our blog post on how to operate a metal lathe! We hope you found it helpful and informative.
Edmund Sumlin is a skilled author for Metal Fixes, bringing 6 years of expertise in crafting a wide range of metal fixtures. With a strong background in metalwork, Edmund’s knowledge spans various types of fixtures, from decorative pieces to functional hardware, blending precision with creativity. His passion for metalworking and design has made him a trusted resource in the industry.
Professional Focus:
- Expert in Metal Fixtures : Edmund aesthetic specializes in creating durable and innovative metal fixtures, offering both appeal and functionality. His work reflects a deep understanding of metalworking techniques and materials.
- Sustainability Advocate : He is dedicated to using sustainable practices, ensuring that every fixture is crafted with eco-friendly methods while maintaining high-quality standards.
In his writing for Metal Fixes, Edmund provides valuable insights into the latest trends, techniques, and practical advice for those passionate about metal fixtures, whether they are professionals or DIY enthusiasts. His focus on combining artistry with engineering helps others discover the true potential of metal in design.