Achieving a successful aluminum weld requires meticulous preparation to contend with the unique challenges posed by this lightweight and highly conductive metal. Properly prepping aluminum surfaces is a critical step that can make the difference between a robust, structurally sound weld and a flawed connection. In this comprehensive guide, we delve into how to prep aluminum for welding.
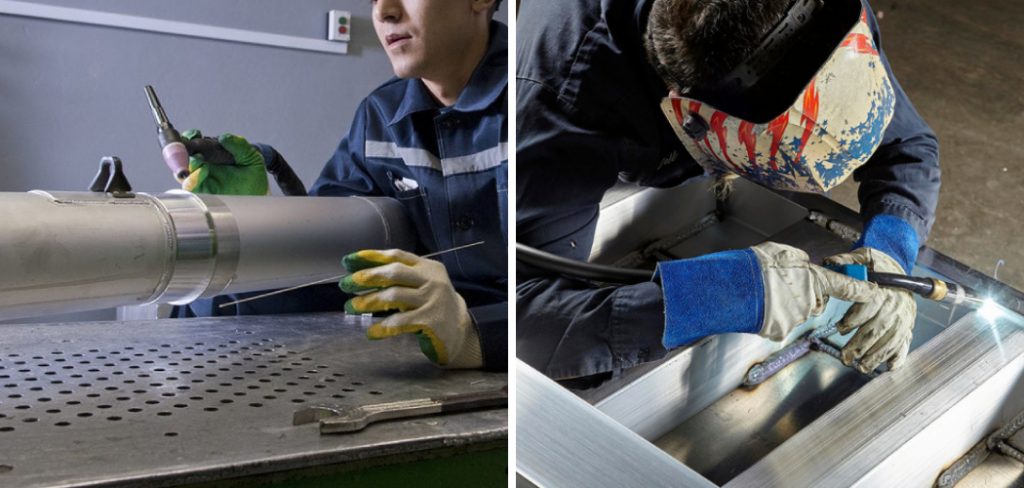
From cleaning and degreasing to addressing oxide layers and selecting the appropriate filler material, readers will gain valuable insights into the nuances of aluminum welding preparation. Whether you are a novice welder or a seasoned professional, understanding the intricacies of pre-welding procedures is paramount to ensure a strong and reliable bond.
Join us as we explore the key techniques and considerations involved in prepping aluminum for welding, laying the foundation for successful and enduring metal joins.
Importance of Proper Aluminum Preparation for Welding
As with any welding process, proper preparation is critical for achieving high-quality welds. This is especially true when working with aluminum, which has unique properties that require special attention. In this section, we will discuss the importance of preparing aluminum for welding and provide tips on how to properly prep your aluminum before beginning the welding process.
One of the main reasons why proper preparation is crucial when welding aluminum is because it is a highly reactive metal. Aluminum readily oxidizes when exposed to air, forming a thin layer of oxide on its surface, which can inhibit the formation of strong welds. This oxide layer must be removed before welding to ensure proper fusion and bonding between the base metal and the filler material.
In addition to removing the oxide layer, proper preparation also involves cleaning the aluminum surface to remove any dirt, oil, or other contaminants that could compromise the integrity of the weld. These contaminants can lead to porosity, cracking, and other defects in the weld if not removed beforehand.
Another important aspect of preparing aluminum for welding is ensuring that it is free from moisture. Aluminum has a low melting point, and as such, any moisture present on its surface can quickly turn into steam when exposed to high heat. This can result in splatter, porosity, and other welding defects.
10 Methods How to Prep Aluminum for Welding
1. Clean the Aluminum
Before welding aluminum, it is important to clean the surface of any dirt, dust, oil or grease. This can be done using a wire brush or sandpaper. The aluminum should also be inspected for any cracks or defects that may need to be repaired before welding. Once the surface is clean and free of debris, it is ready for prepping.
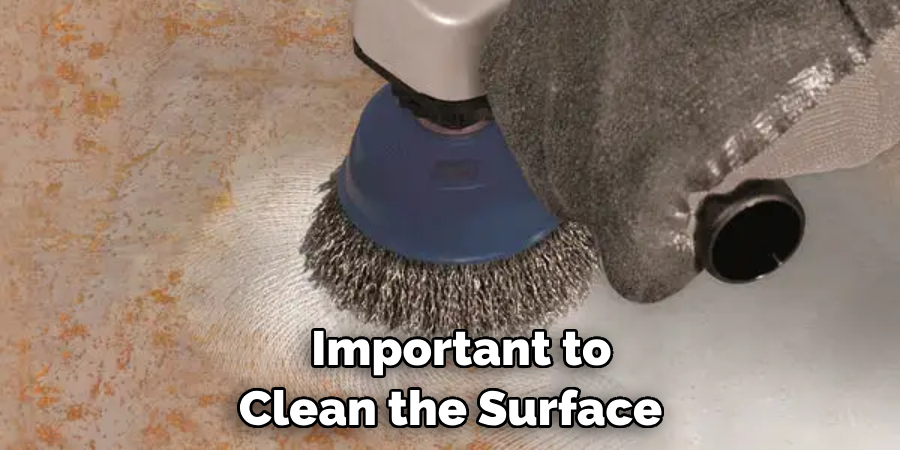
2. Use a Grinder
Using a grinder to remove any rust or corrosion from the aluminum surface is an effective method of prepping for welding. Be sure to use a grinding wheel that is designed specifically for aluminum, as other types may cause damage to the material. Additionally, use caution when grinding, as too much pressure can lead to warping and distortion of the metal.
3. Brush Away Oxide
Aluminum oxide can form on the surface of aluminum during welding and can interfere with the weld’s quality if not removed prior to welding. To remove oxide buildup, use a stainless steel wire brush in combination with compressed air or water spray to ensure all oxide particles are removed from the surface of the aluminum before welding begins.
4. File Rough Edges
If there are any rough edges on the aluminum that will be in contact with the weld, it is important to file them down prior to welding. Filing down rough edges helps ensure that there will be good contact between the two pieces being welded together which will result in a stronger weld overall.
5. Sandblast
Sandblasting can be used to prepare large areas of aluminum for welding by removing dirt, debris and contaminants from its surface without damaging its integrity. It is important however that only abrasive materials designed specifically for sandblasting aluminum are used otherwise damage may occur due to improper blasting media selection and/or incorrect blast pressures being used during sandblasting operations.
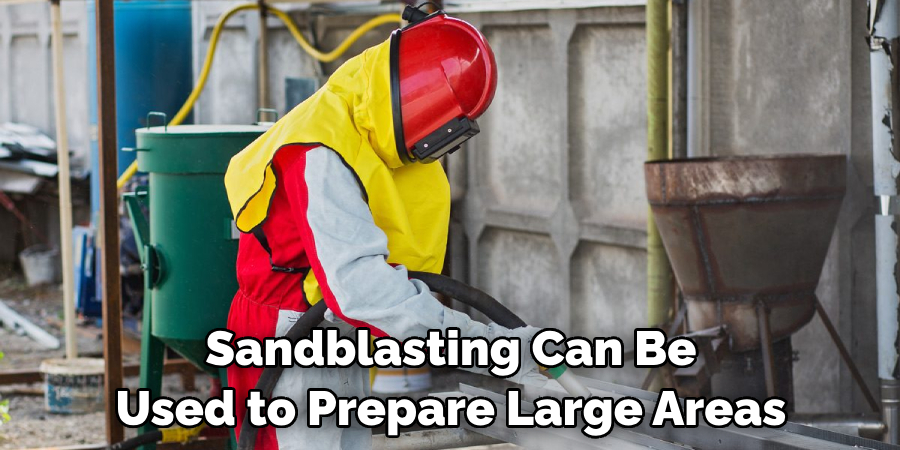
6. Cleaning With Solvents
Cleaning with solvents such as acetone or alcohol can help remove oils and greases from surfaces prior to welding operations but should not be used on metals that have been painted or treated with chemicals because these solvents could damage these coatings and finishes over time if they come into contact with them repeatedly during cleaning operations. It is also important when using solvents that proper ventilation and safety protocols are followed at all times as these chemicals can pose health risks if inhaled in large quantities over long periods of time.
7. Degrease Aluminum Parts
Degreasing parts prior to welding helps ensure that no contaminants remain on their surfaces before beginning work which could interfere with weld quality once operations begin. Degreasing solutions such as trichloroethylene (TCE) can be used in combination with compressed air or water sprays but should always be done in well-ventilated areas away from open flames as TCE has been known to ignite under certain conditions.
8. Heat Treating Aluminum
Heat treating aluminum before welding helps reduce stress within its structure which can lead to better weld quality overall. Heat treating involves heating up an area just prior to where you plan on making your weld and then allowing it to cool down slowly afterward. This helps relieve some of the internal stresses within an area so that when you eventually make your weld, it will have less chance of cracking due to residual stress within its structure.
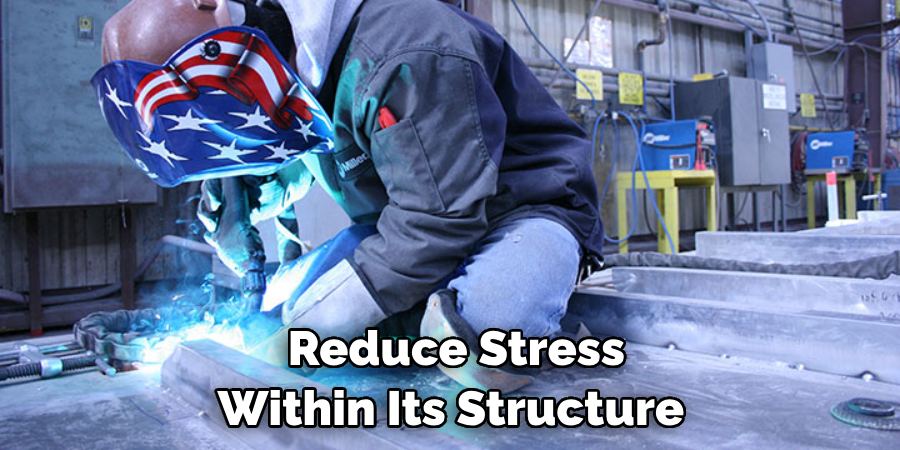
9. Use Masking Tape
Masking tape can help prevent contamination from occurring during prepping by covering areas around where you plan on making your welds. This ensures that no dirt, dust, oils, grease, etc… come into contact with your workpiece while you’re prepping it for welding operations which could lead to poor quality results once you start working on it.
10. Use Protective Gear
When prepping aluminum for welding operations, it’s important that protective gear, such as gloves, goggles, respirators, etc… are worn at all times as exposure to fumes created during prepping processes could lead to serious health issues if inhaled over long periods of time without proper protection being worn.
Things to Consider When Preparing Aluminum for Welding
Aluminum is a widely used material in various industries due to its light weight, high strength-to-weight ratio, and corrosion resistance properties. However, when it comes to welding aluminum, proper preparation is crucial for successful results. Failing to adequately prepare aluminum before welding can result in weak welds, defects, and even damage to the base material.
In this guide, we will discuss the key things to consider when preparing aluminum for welding. This knowledge will not only help you achieve high-quality welds but also ensure the safety of your workpiece and yourself.
Material Selection
Before starting the preparation process, it is essential to select the right type of aluminum for your project. There are various grades and alloys of aluminum available, each with different properties and characteristics. Some are more suitable for welding than others due to their composition and structure.
For instance, 5xxx series aluminum alloys (e.g., 5052 and 5083) are widely used in marine applications because of their excellent corrosion resistance. However, they can be challenging to weld compared to the more common 6xxx series (e.g., 6061 and 6063) due to their high magnesium content.
Things to Consider When Preparing Aluminum for Welding
When it comes to welding aluminum, proper preparation is key. This is because aluminum can be a tricky material to work with, and without the right preparation, the end result may not be as strong or durable as desired.
Before diving into the process of preparing aluminum for welding, here are some things to consider that will help ensure a successful weld.
Cleanliness is crucial
Aluminum is highly reactive and easily forms an oxide layer on its surface, which can hinder the welding process. Therefore, it is essential to thoroughly clean the aluminum before attempting to weld it. This can be done using a degreaser or solvent to remove any oils, dirt, or other contaminants from the surface.
Remove any surface oxide layer
As mentioned before, aluminum readily forms an oxide layer on its surface. This layer must be removed to allow for proper welding. One way to do this is by using a stainless steel wire brush or an abrasive wheel to scrub away the oxide layer.
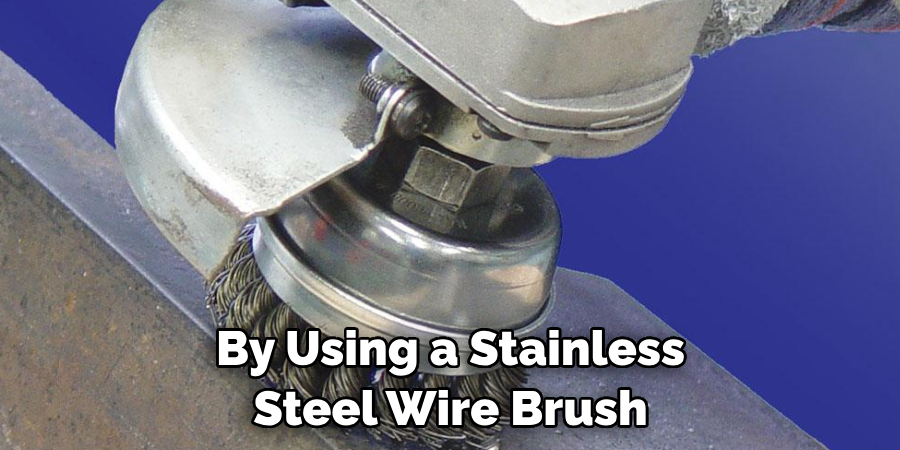
Conclusion
From cleaning and polishing the aluminum alloy to be welded to degreasing and sanding the area, prepping your aluminum for welding is an essential step for a successful and safe weld. Make sure not to forget your protective equipment, like safety glasses and a face shield, as well as proper ventilation of the work area. When prepping your aluminum for welding, take your time so that all steps are completed properly.
After each procedure has been finished successfully then you can be sure of a successful weld. Now that you know how to prep aluminum for welding, why not put it into action? A clean welding surface will guarantee a perfect weld every time – so don’t waste any time and get started on prepping your aluminum today!
Edmund Sumlin is a skilled author for Metal Fixes, bringing 6 years of expertise in crafting a wide range of metal fixtures. With a strong background in metalwork, Edmund’s knowledge spans various types of fixtures, from decorative pieces to functional hardware, blending precision with creativity. His passion for metalworking and design has made him a trusted resource in the industry.
Professional Focus:
- Expert in Metal Fixtures : Edmund aesthetic specializes in creating durable and innovative metal fixtures, offering both appeal and functionality. His work reflects a deep understanding of metalworking techniques and materials.
- Sustainability Advocate : He is dedicated to using sustainable practices, ensuring that every fixture is crafted with eco-friendly methods while maintaining high-quality standards.
In his writing for Metal Fixes, Edmund provides valuable insights into the latest trends, techniques, and practical advice for those passionate about metal fixtures, whether they are professionals or DIY enthusiasts. His focus on combining artistry with engineering helps others discover the true potential of metal in design.