Are you experiencing corrosion on your aluminum and stainless steel surfaces? If yes, then you might be dealing with galvanic corrosion. This type of corrosion occurs when two dissimilar metals are in contact with each other in the presence of an electrolyte.
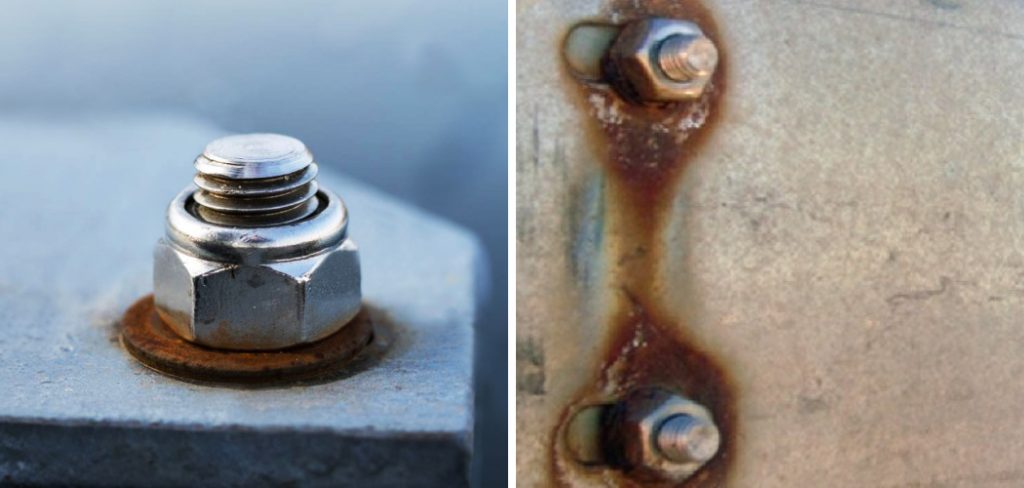
Galvanic corrosion is a common issue that occurs when two distinct metals, such as aluminum and stainless steel, come into contact in the presence of an electrolyte, typically water.
This electrochemical process can lead to the accelerated deterioration of the less noble metal, in this case, aluminum, causing critical failures in structural integrity and functionality.
Understanding how to prevent galvanic corrosion between aluminum and stainless steel is essential for engineers, architects, and maintenance professionals who work with these metals in various applications.
By implementing proper techniques and preventive measures, the longevity and reliability of metal structures and components can be significantly enhanced.
What are the Causes of Galvanic Corrosion between Aluminum and Stainless Steel?
The fundamental cause of galvanic corrosion is the difference in electrical potential between two dissimilar metals.
- Electrical Potential: Electrical potential refers to the voltage difference between two metals that are in contact with each other. Aluminum and stainless steel have significantly different electrical potentials, with aluminum being more anodic (less noble) than stainless steel.
- Electrolytes: Electrolytes, such as water or saltwater, act as a conductor for the flow of electrons between two dissimilar metals. This allows for the electrochemical reaction to occur, leading to galvanic corrosion.
- Surface Area: The larger the surface area of the anodic metal (aluminum), the greater the potential for galvanic corrosion. This is because a larger surface area provides more contact points for the electrolytes to come in contact with the metal, increasing the electrochemical reaction.
- Mechanical and Environmental Factors: Mechanical stress, as well as environmental factors such as humidity, temperature, and pollution levels, can also contribute to galvanic corrosion.
These causes highlight the importance of proper design, installation, and maintenance practices to prevent or minimize galvanic corrosion between aluminum and stainless steel.
What Will You Need?
To prevent galvanic corrosion between aluminum and stainless steel, you will need some basic tools and materials:

- Protective Equipment: Before handling any metal surfaces, it is essential to wear protective gear, such as gloves and goggles.
- Insulating Materials: Insulating materials, such as plastic or rubber washers or gaskets, can be used to create a barrier between the two dissimilar metals to prevent contact.
- Sealants and Coatings: Applying a non-conductive sealant or coating, such as paint, wax, or oil, can also help create a barrier and prevent contact between the two metals.
- Proper Installation Techniques: When installing aluminum and stainless steel together, it is crucial to use proper techniques and avoid any unintentional contact between the two metals. This includes using separate tools for each metal, avoiding metal shavings or particles from one metal to come in contact with the other, and using insulating materials when necessary.
- Regular Maintenance: Regular cleaning and maintenance of aluminum and stainless steel surfaces can help prevent galvanic corrosion by removing any built-up electrolytes that may cause the electrochemical reaction.
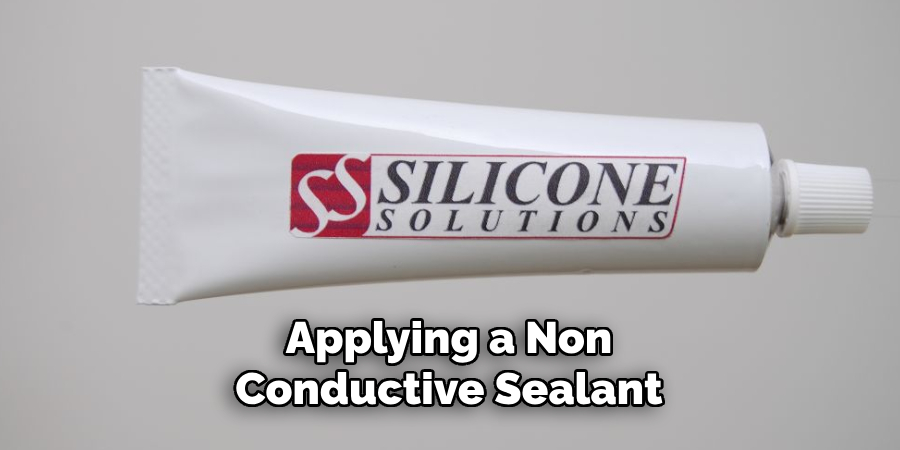
Once you have all the necessary tools and materials, you can start implementing preventive measures to avoid galvanic corrosion between aluminum and stainless steel.
10 Easy Steps on How to Prevent Galvanic Corrosion Between Aluminum and Stainless Steel
Step 1: Identify Contact Points
The first and most crucial step in preventing galvanic corrosion between aluminum and stainless steel is to identify all potential contact points where these two metals might come into direct physical association.
This includes examining the design and layout of the structure or machinery paying close attention to joints, fasteners, and areas where dissimilar metals are used together.
Begin by conducting a thorough inspection of the project, whether it is a building, a vehicle, or a piece of equipment. Look for locations where aluminum and stainless steel components are adjacent or fastened together.
This could include bolts, screws, and other fastening devices that might be made of one metal while connecting components of the other.
Document all identified contact points clearly, marking them on design schematics or physical components. This will serve as a roadmap for implementing protective measures.
It’s also important to consider potential indirect contacts where moisture or other electrolytes could bridge a gap between aluminum and stainless steel.
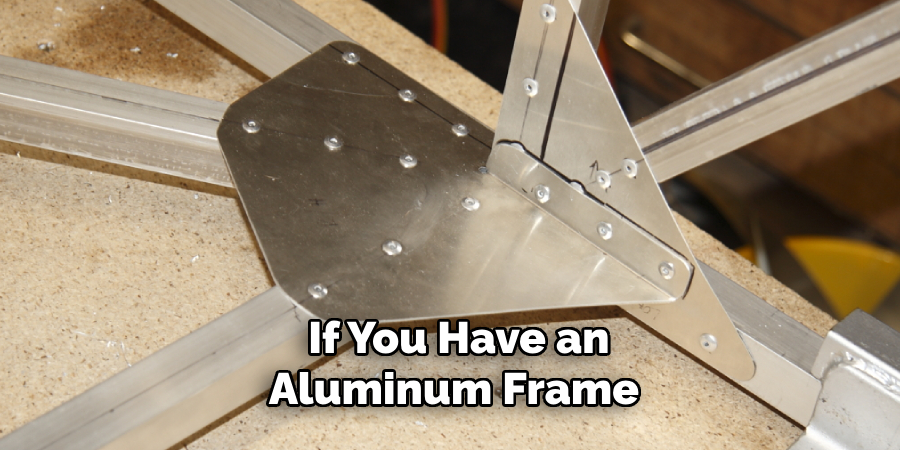
For example, if you have an aluminum frame with stainless steel mounting brackets, each point where a bracket is attached to the frame is a contact point.
Similarly, any stainless steel fasteners like screws or bolts that pass through aluminum parts need to be carefully noted.
This meticulous initial step ensures that no potential weak spots are missed, allowing for a comprehensive approach to corrosion prevention.
Step 2: Clean Metal Surfaces
Before applying any protective measures, it is vital to thoroughly clean the aluminum and stainless steel surfaces that will be in close proximity. Dirt, grease, and other contaminants can impede the effectiveness of insulating materials and coatings.
Begin by using a degreasing solution or a mild detergent to remove any oils and residues from the metal surfaces. For aluminum surfaces, avoid using strong alkaline cleaners as they can cause damage.
Instead, opt for a pH-neutral cleaner. Rinse thoroughly with clean water and ensure the surfaces are completely dry before proceeding to the next step.
By ensuring that the metal surfaces are impeccably clean, you create an optimal environment for the application of protective coatings or insulating materials, thereby enhancing their effectiveness in preventing galvanic corrosion.
Step 3: Apply Insulating Materials
Once the metal surfaces are clean and dry, the next step is to apply insulating materials to prevent direct contact between aluminum and stainless steel. These insulating materials can be in the form of plastic or rubber washers, gaskets, or sleeves.
Start by selecting the appropriate type of insulating material based on the specific application and environmental conditions. Rubber washers are ideal for damp environments as they provide excellent moisture resistance, while plastic components like polycarbonate gaskets are suitable for areas that require high mechanical strength.
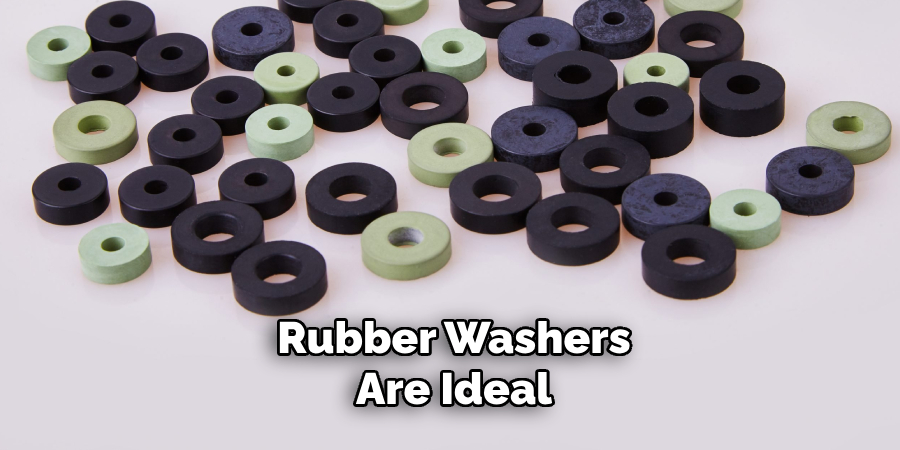
Carefully place the insulating material at all identified contact points. For bolts, screws, or other fasteners, use rubber or plastic washers to separate the head of the fastener from the metal surface. If possible, use insulating sleeves to cover the entire length of the fastener where it passes through the aluminum or stainless steel components.
Step 4: Apply Sealants and Coatings
After applying insulating materials, the next step is to use non-conductive sealants and coatings to provide an additional layer of protection against galvanic corrosion. These coatings act as a barrier to moisture and electrolytes, which are essential components for the electrochemical reaction causing corrosion.
Choose a suitable sealant or coating based on the environment and operational conditions of the project. For instance, epoxy or polyurethane coatings offer excellent chemical resistance and durability, making them ideal for harsh or marine environments. Paints, oils, and waxes can be used for less demanding applications.
Apply the sealant or coating according to the manufacturer’s instructions, ensuring even coverage over the entire surface area of both the aluminum and stainless steel components.
Pay close attention to edges and corners where the coating might be thinner or more prone to wear. Multiple layers may be required to achieve the desired level of protection.
Step 5: Use Compatible Fasteners
Utilizing compatible fasteners is essential in preventing galvanic corrosion between aluminum and stainless steel components.
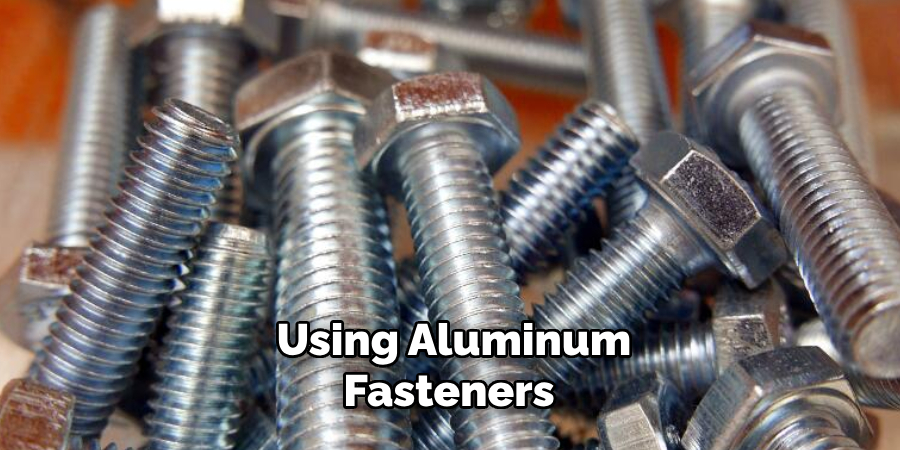
Where possible, opt for fasteners made of the same material as one of the components. For example, using aluminum fasteners with aluminum components can help minimize the potential for galvanic corrosion.
If using stainless steel fasteners with aluminum parts is unavoidable, consider using fasteners with a non-conductive coating or plating, such as zinc or cadmium.
These coatings act as a sacrificial barrier, preventing direct metal-to-metal contact and thus reducing the likelihood of electrolytic reactions.
Carefully select fasteners based on your project’s specific requirements, taking into account factors such as mechanical strength, environmental exposure, and temperature fluctuations.
Ensure that all fasteners are installed correctly, with any necessary insulating materials in place to maintain separation between dissimilar metals. Proper installation and maintenance of fasteners play a critical role in minimizing corrosion risks and prolonging the lifespan of the components.
Step 6: Regular Maintenance and Inspections
Continuous maintenance and regular inspections are vital for ensuring the long-term effectiveness of the implemented protective measures against galvanic corrosion.
Set up a maintenance schedule to periodically check the condition of the insulating materials, sealants, coatings, and fasteners. Look for signs of wear, damage, or degradation that could compromise the protective barriers.
During inspections, pay special attention to areas subjected to harsh environmental conditions, such as high humidity, salt exposure, or fluctuating temperatures. If any issues are identified, take prompt action to repair or replace damaged components to prevent corrosion from occurring.
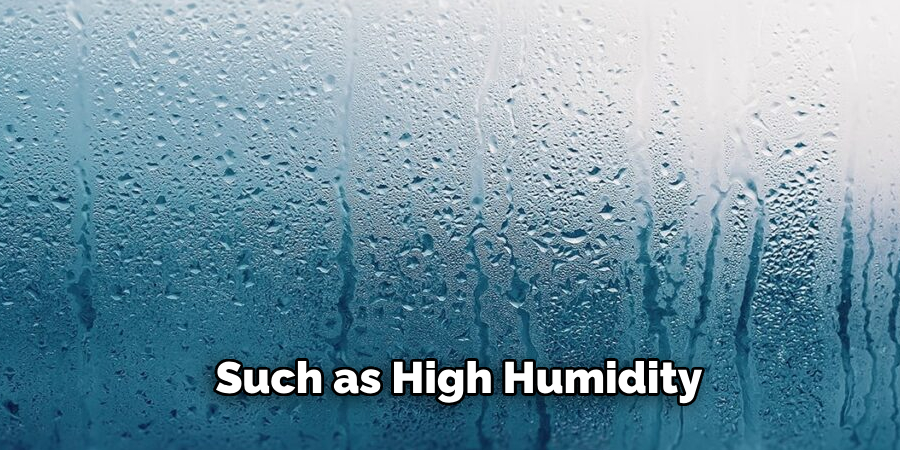
Step 7: Monitor Installed Systems
Monitoring installed systems is the final step in ensuring the long-term mitigation of galvanic corrosion between aluminum and stainless steel components. Automated monitoring systems, such as corrosion sensors and data loggers, can provide real-time information on the condition and performance of protective measures.
Implement a monitoring system that suits the specific needs and budget of your project. Basic systems may include visual inspections and manual readings, while advanced setups might involve wireless corrosion monitoring platforms that send alerts when potential issues are detected.
Step 8: Document and Report Findings
An essential part of the process is to thoroughly document and report all findings related to galvanic corrosion prevention efforts. Keeping detailed records of the materials used, methods applied, and inspection results contributes significantly to maintaining the longevity and integrity of the aluminum and stainless steel components.
Create a comprehensive log that includes:
- Material Specifications: Document the types and specifications of all insulating materials, sealants, coatings, and fasteners used in the project.
- Application Techniques: Record the application methods for each protective measure, including any specific manufacturer’s instructions followed.
- Inspection Reports: Maintain detailed inspection records noting the condition of protective measures, any issues identified, and actions taken to remedy them.
- Maintenance Activities: Log all routine maintenance activities carried out, including cleaning, reapplying coatings, and replacing worn or damaged components.
- Monitoring Data: If automated monitoring systems are in place, store all relevant data logs, sensor readings, and alert history for review.
By systematically documenting and reporting these findings, you ensure a clear historical record that can inform future maintenance and mitigation strategies. This practice not only aids in preventing galvanic corrosion but also enhances the overall reliability and safety of the project.
Step 9: Education and Training
Educating and training personnel involved in the project is crucial to preventing galvanic corrosion between aluminum and stainless steel components.
Ensure that all team members understand the principles behind galvanic corrosion, the importance of insulation and protective coatings, and the proper selection and installation of fasteners.
Provide comprehensive training on the maintenance and inspection techniques needed to sustain the protective measures.
Organize regular workshops and refresher courses to keep the team updated on best practices and emerging technologies in corrosion prevention. By fostering a well-informed and skilled team, you can significantly reduce the risk of corrosion-related failures and extend the lifespan of the components involved in your project.
Step 10: Develop a Contingency Plan
Despite the best efforts to prevent galvanic corrosion between aluminum and stainless steel components, unforeseen issues can still arise. Developing a contingency plan ensures that any corrosion-related problems can be swiftly and effectively addressed, minimizing damage and project downtime.
A robust contingency plan should include the following elements:
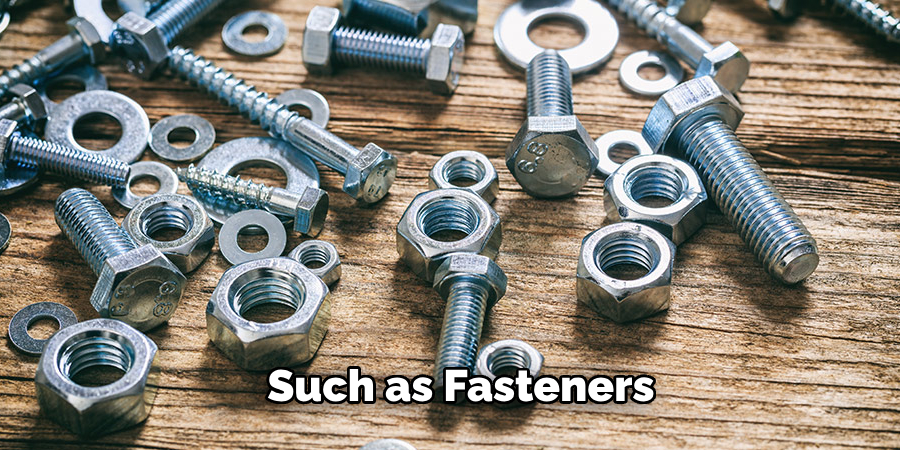
- Emergency Contacts: Maintain a list of key contacts, including corrosion specialists, materials engineers, and equipment suppliers, who can provide immediate assistance if a corrosion issue is detected.
- Replacement Parts Inventory: Keep an inventory of critical replacement parts, such as fasteners, insulating materials, and coatings, to enable quick repairs or replacements as needed.
- Predefined Response Procedures: Establish clear response procedures for identifying, assessing, and mitigating corrosion-related issues. These procedures should outline the steps to take from initial detection to resolution, including any temporary fixes that may be necessary to prevent further damage.
- Regular Drills and Simulations: Conduct regular drills and simulations to ensure all team members are familiar with the contingency plan and can respond efficiently in the event of an actual corrosion incident.
By having a well-developed contingency plan in place, you can effectively manage and mitigate the impact of corrosion-related challenges, ensuring the long-term success and reliability of your project.
***
5 Additional Tips and Tricks
- Utilize Barrier Coatings: Applying a coating such as paint, varnish, or a specialized barrier coating to both aluminum and stainless steel can help prevent direct contact and subsequent corrosion.
- Select Appropriate Fasteners: Using fasteners such as stainless steel bolts with non-conductive washers or sleeves can minimize direct contact between dissimilar metals and reduce the risk of galvanic corrosion.
- Add Insulating Materials: Insulators such as rubber, plastic, or other non-conductive materials can be placed between aluminum and stainless steel parts to physically separate them and prevent the galvanic reaction.
- Consider Environmental Factors: Control environmental conditions, such as humidity and exposure to saltwater, as these can accelerate galvanic corrosion. Employing dehumidifiers or desiccants in controlled environments can be beneficial.
- Don’t Neglect Maintenance: Regularly inspect and maintain all metal components to identify any signs of corrosion early on. This can help prevent further damage and extend the lifespan of your aluminum and stainless steel parts. Also, be sure to follow manufacturer recommendations for cleaning and maintenance to ensure the best protection against galvanic corrosion.
In addition to these tips, it is also important to educate yourself and your team on the properties and compatibility of different metals.
5 Things You Should Avoid
- Avoid Direct Contact: Never allow aluminum and stainless steel to come into direct contact without any barriers. This direct contact can accelerate galvanic corrosion, degrading aluminum components.
- Prevent Standing Water: Do not let water accumulate between aluminum and stainless steel parts. Standing water can create a conductive path for galvanic corrosion, especially in environments exposed to saltwater or rain.
- Omit Regular Inspections: Failing to routinely inspect and maintain metal components can result in overlooking early signs of corrosion. Regular inspections are crucial to identify and address potential issues before they escalate.
- Use Incorrect Fasteners: Avoid using fasteners that can promote galvanic corrosion, such as using aluminum fasteners with stainless steel parts. Ensure that all fasteners are made from compatible materials or are insulated properly.
- Ignore Environmental Controls: Do not disregard the importance of controlling environmental factors. Ignoring humidity levels, temperature variations, and exposure to corrosive elements like salt can significantly increase the risk of galvanic corrosion. Employing environmental controls such as dehumidifiers and proper ventilation is essential.
By avoiding these common mistakes and implementing preventative measures, you can effectively protect your aluminum and stainless steel components from galvanic corrosion.
Conclusion
How to prevent galvanic corrosion between aluminum and stainless steel requires a comprehensive approach involving both proactive and reactive strategies.
By utilizing barrier coatings, selecting appropriate fasteners, and adding insulating materials, you effectively reduce direct contact and mitigate the risk of galvanic reactions.
Considering environmental factors such as humidity and exposure to saltwater will further safeguard against corrosion, and regular maintenance ensures early detection and resolution of potential problems.
Additionally, it is imperative that both you and your team are well-educated about the properties and compatibility of different metals to make informed decisions.
By adhering to these best practices and avoiding common pitfalls, you can significantly extend the lifespan and integrity of your aluminum and stainless steel components, ensuring optimal performance and durability in diverse environments.
Edmund Sumlin is a skilled author for Metal Fixes, bringing 6 years of expertise in crafting a wide range of metal fixtures. With a strong background in metalwork, Edmund’s knowledge spans various types of fixtures, from decorative pieces to functional hardware, blending precision with creativity. His passion for metalworking and design has made him a trusted resource in the industry.
Professional Focus:
- Expert in Metal Fixtures : Edmund aesthetic specializes in creating durable and innovative metal fixtures, offering both appeal and functionality. His work reflects a deep understanding of metalworking techniques and materials.
- Sustainability Advocate : He is dedicated to using sustainable practices, ensuring that every fixture is crafted with eco-friendly methods while maintaining high-quality standards.
In his writing for Metal Fixes, Edmund provides valuable insights into the latest trends, techniques, and practical advice for those passionate about metal fixtures, whether they are professionals or DIY enthusiasts. His focus on combining artistry with engineering helps others discover the true potential of metal in design.