Are you curious about how stainless steel products are made? This type of steel is used in a wide range of industries, from food production to construction. In this guide, we will take you through the process of how to produce stainless steel.
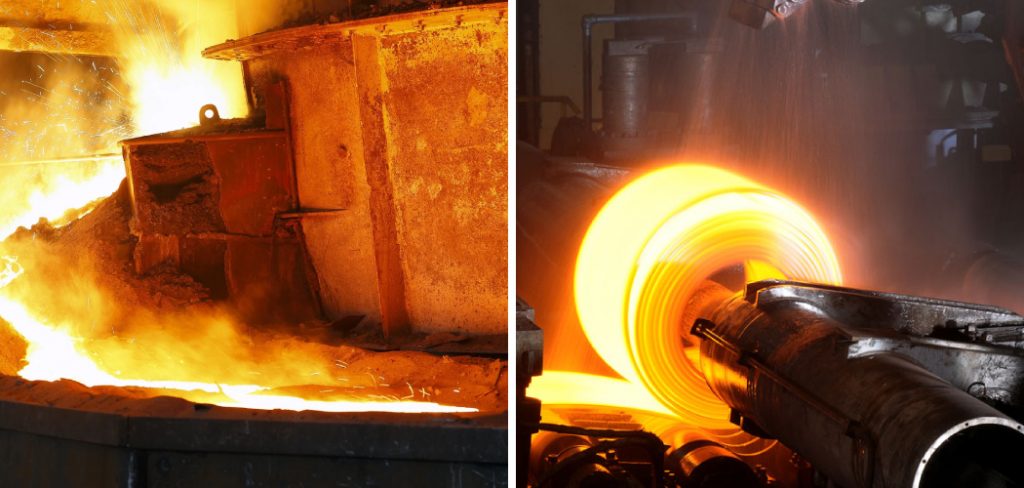
Stainless steel production is a sophisticated process that combines various raw materials and employs advanced techniques to create a robust, versatile alloy renowned for its corrosion resistance, strength, and aesthetic appeal.
The production of stainless steel involves several key stages, including the selection and preparation of raw materials, melting and refining in an electric arc furnace, casting into desired shapes, and further processing such as rolling, annealing, and finishing.
This introduction will provide an overview of the fundamental steps in the manufacturing process, highlighting the importance of precise control and technological advancements that ensure consistent quality and performance in stainless steel products.
What are the Use Cases for Stainless Steel?
Before delving into the production process, let’s briefly touch on the various use cases for stainless steel. This durable alloy is valued for its exceptional properties that make it well-suited for a wide range of applications.
Stainless steel is commonly used in construction and architecture due to its strength and resistance to corrosion, making it ideal for building facades, roofing, and structural components. It is also widely used in the transportation industry for parts such as exhaust systems, fuel tanks, and train cars.
Stainless steel’s non-porous surface makes it easy to clean and maintain hygiene standards in the food production industry. It is commonly used in commercial kitchens, food processing equipment, and even kitchen appliances in households.
The medical and pharmaceutical industries rely on stainless steel for its biocompatibility and ability to withstand harsh sterilization processes. It is used in medical devices, surgical tools, and implants.
These are just a few examples of the many use cases for stainless steel. Its versatility and unique properties make it an indispensable material in numerous industries.
What Will You Need?
To produce high-quality stainless steel, you will need a variety of raw materials and specialized equipment. Some of the key components include:
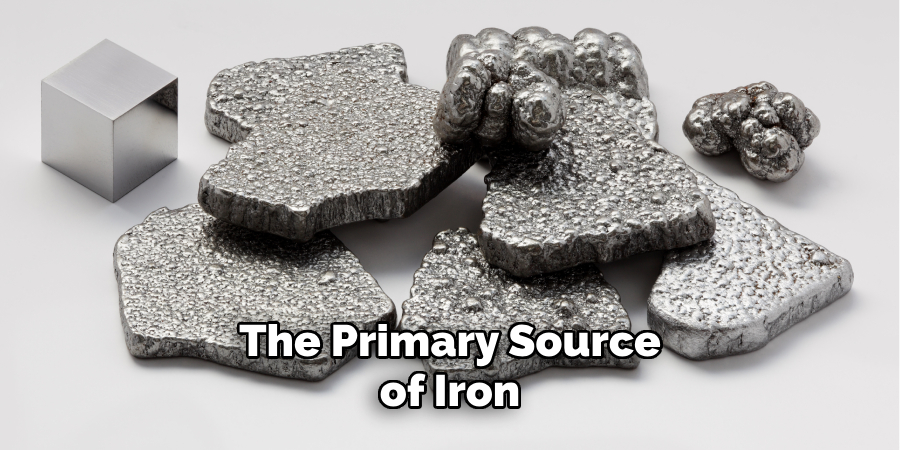
- Iron Ore: The primary source of iron that is essential for creating stainless steel.
- Scrap Metal: Recycled steel that can be used in place of iron ore to reduce costs and environmental impact.
- Chromium: The element responsible for giving stainless steel its corrosion-resistant properties.
- Nickel: An alloying element that adds strength and toughness to stainless steel.
- Manganese: Another essential alloying element that improves the workability and hardenability of stainless steel.
- Electric Arc Furnace: The main equipment used in melting and refining raw materials into stainless steel.
- Casting Molds: These molds shape the molten steel into various forms, such as sheets, bars, and tubes.
- Rolling Mill: A machine that compresses and stretches the stainless steel into thinner or larger dimensions.
- Annealing Furnace: Used to heat treat the steel and improve its strength and ductility.
- Finishing Equipment: This includes grinding machines, sandblasters, and polishers used to achieve the desired surface finish.
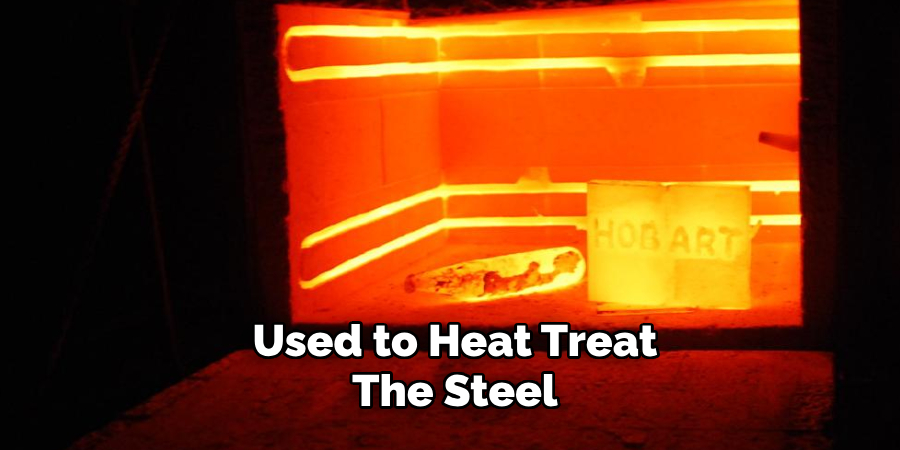
Additional items such as flux, refractories, and cooling systems are also necessary for the production process. It’s crucial to have high-quality materials and equipment to ensure the final product meets industry standards.
9 Easy Steps on How to Produce Stainless Steel
Step 1. Gathering Raw Materials
The first step in producing stainless steel is collecting raw materials such as iron ore, scrap metal, chromium, nickel, and manganese.
These materials are chosen for their specific properties, which contribute to the strength, durability, and corrosion resistance of the final product. It is essential to source high-quality raw materials to ensure that the stainless steel produced meets industry standards and performance requirements.
Step 2. Preparing the Raw Materials
Once the raw materials have been gathered, the next step involves preparing them to ensure they are ready for the melting process. This stage includes cleaning the scrap metal to remove contaminants such as oil, rust, and paint that could negatively affect the quality of the stainless steel.
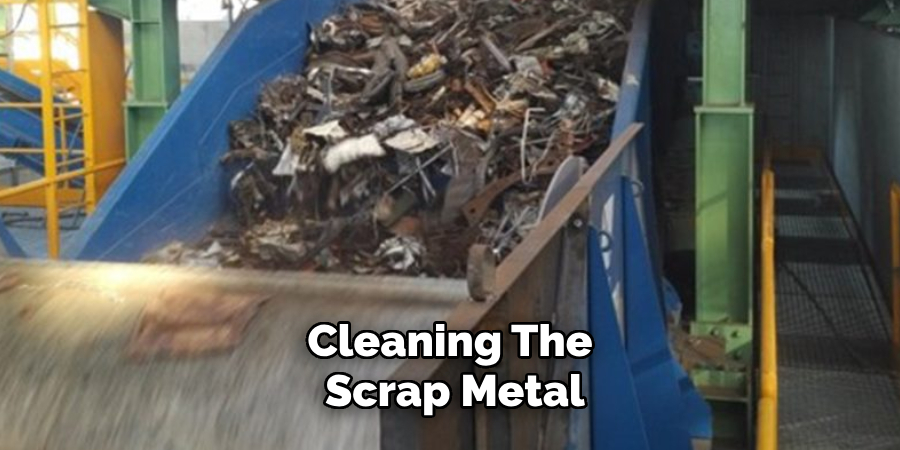
Similarly, iron ore and other raw materials may undergo a beneficiation process involving crushing, grinding, and various methods of separation to increase their purity and concentration.
Alloying elements like chromium, nickel, and manganese need to be accurately weighed and measured according to the specific grade of stainless steel being produced.
This precision is pivotal to achieving the desired properties in the final product. The prepared raw materials are then pre-mixed in controlled proportions to create a homogeneous blend, ensuring consistency and uniformity in the melting process.
At this stage, the materials may also be pre-heated to remove any moisture content and to facilitate easier melting once they enter the electric arc furnace. This thorough preparation is crucial for maintaining the integrity and quality of the stainless steel, setting the foundation for the subsequent melting and refining phases.
Step 3. Melting the Raw Materials
The prepared raw materials are then charged into an electric arc furnace (EAF), where they are subjected to intense heat to melt them into a molten state. The EAF uses high-power electric arcs from carbon electrodes to reach the necessary temperatures, often exceeding 2,800°F (1,540°C).
During this stage, the precise control of the furnace environment, including temperature and slag formation, is critical to ensure the proper mixing and alloying of the metals.
To enhance the melting process, oxygen is often blown into the furnace, which helps to oxidize impurities and reduce the steel’s carbon content.
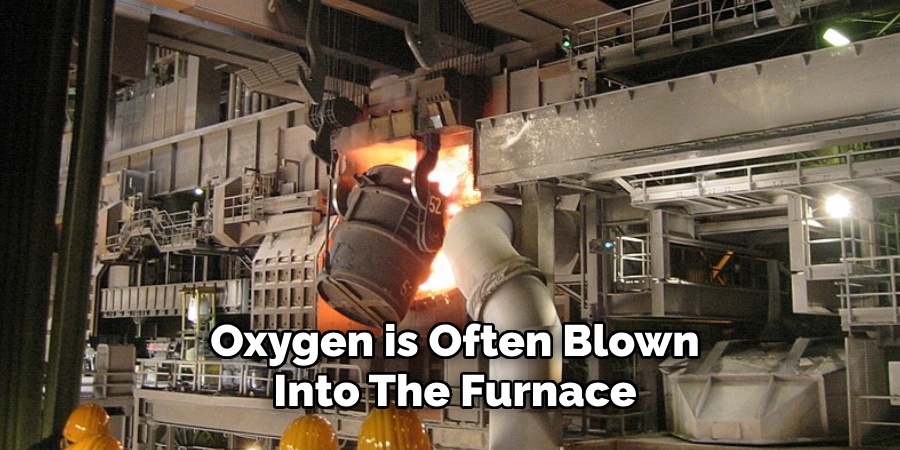
This step is crucial for achieving the desired chemical composition of the stainless steel. The molten metal undergoes further refining to remove any remaining impurities through the addition of fluxes, which bind with unwanted elements to form a slag that can be easily removed.
Throughout the melting process, samples of the molten steel are taken and analyzed to monitor its composition and make any necessary adjustments.
This ensures that the final product meets the exact specifications required for its intended application. Once the melting and refining process is complete, the molten steel is ready for the next step—casting.
Step 4. Casting the Molten Steel
Once the molten steel has achieved the desired composition and quality, it is ready for the casting process.
The molten steel is carefully poured into casting molds, which can shape the steel into various forms such as slabs, billets, or blooms, depending on the final product requirements. The casting process needs to be meticulously controlled to prevent any defects and ensure a uniform structure within the solidified steel.
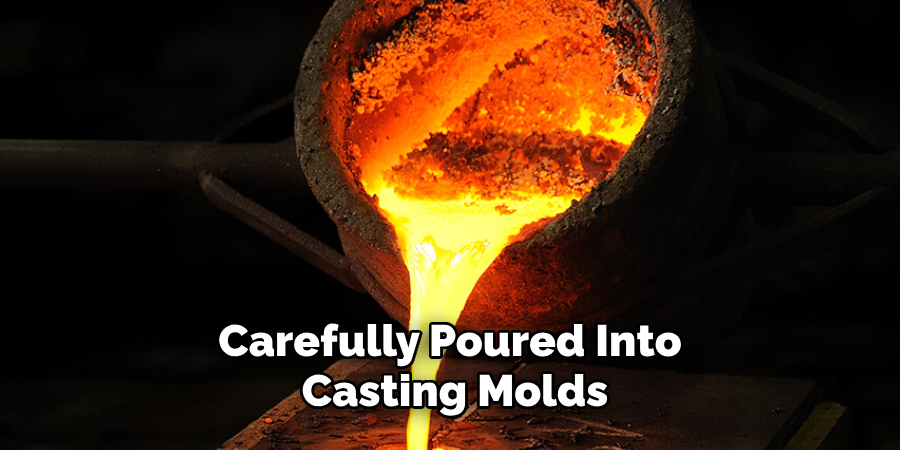
In continuous casting, the molten steel is poured into a water-cooled mold and is continuously drawn out from the bottom as it solidifies. This method allows for the production of long strands of metal that can be cut to the desired lengths.
Continuous casting is renowned for its efficiency and ability to produce high-quality steel with fewer inclusions and a more consistent composition.
For certain applications, ingot casting is preferred, where the molten steel is poured into individual molds. Although this process can be less efficient, it is often used for producing large, high-quality pieces of steel.
Throughout the casting stage, temperature control is crucial to avoid cracking or other defects during solidification.
Step 5. Forming the Steel
Once the molten steel has been cast and solidified, the resulting steel shapes undergo a series of forming processes to achieve the desired dimensions and mechanical properties. Forming primarily involves hot rolling, although cold rolling may be used for specific applications to achieve tighter tolerances and smoother surfaces.
In hot rolling, the steel slabs, billets, or blooms are reheated to a temperature above their recrystallization point, allowing them to be easily deformed. The heated steel is then passed through a series of rolling stands where it is progressively reduced in thickness and elongated.
This process not only shapes the steel but also refines its grain structure, enhancing its strength and ductility.
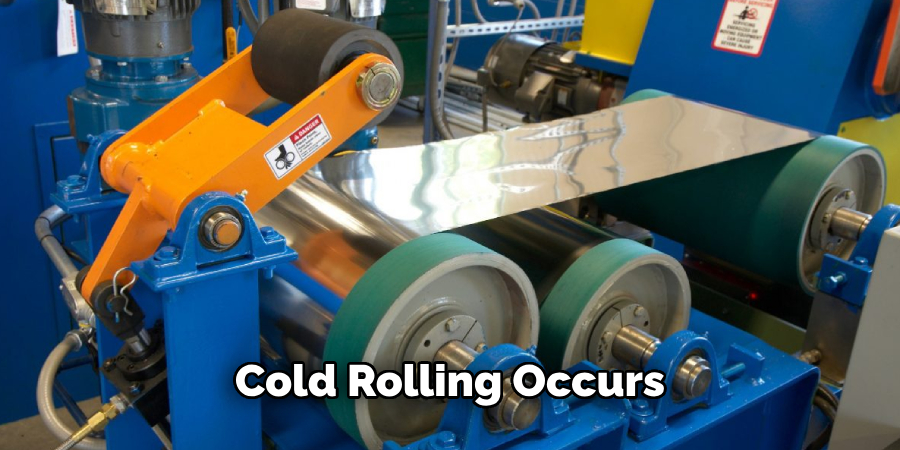
Cold rolling occurs at or near room temperature and results in a more precise, smoother finish. Though cold rolling doesn’t significantly alter the overall dimensions as hot rolling does, it increases the yield strength and hardness of the steel through work hardening.
During both hot and cold rolling, it is crucial to monitor and control the rolling process parameters, including temperature, speed, and reduction ratios, to ensure the final product meets the specific dimensional and mechanical requirements for its intended use. This step prepares the steel for further processing such as heat treatment or surface finishing.
Step 6. Heat Treatment
After forming, the stainless steel often undergoes heat treatment to enhance its mechanical properties, relieve internal stresses, and improve its overall performance in service.
The heat treatment process involves heating the steel to a specific temperature and then cooling it at a controlled rate. Several types of heat treatments can be applied, depending on the desired properties of the final product.
One common heat treatment is annealing, which involves heating the steel to a high temperature and then slowly cooling it.
This process softens the steel, increasing its ductility and making it easier to work with in subsequent manufacturing processes. Annealing also helps to homogenize the steel’s microstructure, improving its overall consistency.
Another important heat treatment is quenching, followed by tempering. Quenching involves rapidly cooling the steel at a high temperature, typically in water or oil, to increase its hardness and strength.
However, quenching can make the steel brittle, so it is often followed by tempering. Tempering involves reheating the quenched steel to a lower temperature and then cooling it gradually, which reduces brittleness while retaining the increased strength.
Similarly, solution treatment for certain grades of stainless steel involves heating to a high temperature to dissolve any precipitates that may form during the solidification and forming processes.

The steel is then rapidly cooled to retain the dissolved elements in a supersaturated solution, enhancing its corrosion resistance.
The precise control of temperature, heating duration, and cooling rate during heat treatment is crucial to achieving the desired balance of hardness, ductility, and other mechanical properties in the final stainless steel product.
Step 7. Surface Finishing
The final step in the production of stainless steel involves surface finishing, which enhances both the appearance and performance of the material.
Surface finishing encompasses a variety of processes, including grinding, polishing, and coating, each tailored to meet specific aesthetic or functional requirements.
Grinding is often the first stage, used to remove any surface imperfections or irregularities left from earlier manufacturing stages. This process ensures a smooth, even surface that is ready for further finishing.
Polishing follows grinding and involves using finer abrasives to achieve the desired level of shine. High-polished finishes not only look more attractive but also improve the steel’s resistance to corrosion by reducing surface roughness where contaminants can accumulate.
For additional protection and functionality, coatings can be applied to the stainless steel.
These coatings range from simple paint and lacquer to more technical applications such as electroplating, which deposits a thin layer of another metal—like chromium or nickel—onto the surface. These coatings enhance the material’s corrosion resistance, durability, and aesthetic appeal.
Step 8. Quality Control and Inspection
The final step in the production of stainless steel is quality control and inspection. This critical phase ensures that the finished product meets all specified standards and performance criteria. Thorough inspections detect any defects or deviations from the desired specifications.
Quality control involves a range of techniques, including visual inspections, dimensional measurements, and mechanical testing. Visual inspections are carried out to identify any surface defects, such as cracks, pits, or inclusions that could compromise the steel’s integrity and aesthetics.
Dimensional measurements are performed using precise instruments to verify that the steel components conform to the required dimensions and tolerances.
Mechanical testing, such as tensile tests, hardness tests, and impact tests, evaluates the material’s mechanical properties. These tests confirm that stainless steel exhibits the necessary strength, ductility, and toughness for its intended applications.
In addition, non-destructive testing methods, like ultrasonic testing and radiographic inspection, examine the internal structure of the steel and ensure there are no hidden flaws.
The information gathered during the quality control process is documented meticulously, and any non-conformities are addressed promptly.
If a batch of stainless steel does not meet the required quality standards, it may be reprocessed or discarded to ensure that only the highest-quality products are delivered to customers.
Step 9. Packaging and Distribution
Once the stainless steel has passed all quality control inspections, it is prepared for packaging and distribution.
The packaging process is designed to protect the steel from damage during transportation and storage, ensuring that it reaches customers in pristine condition. Depending on the form and size of the stainless steel products, various packaging materials and methods are used.
For instance, stainless steel sheets and plates may be stacked and secured with protective coverings such as plastic films or wooden pallets, while coils are often wrapped in protective layers and secured with metal bands.
Smaller components or shaped products might be packaged in boxes or crates with appropriate padding to prevent any movement that could lead to damage.
After packaging, the products are labeled with important information, including the grade, dimensions, and any special handling instructions. This labeling ensures that customers receive the correct materials and allows for easy identification and inventory management.
Finally, the packaged stainless steel products are transported to distribution centers or directly to customers using reliable shipping methods that match the delivery requirements.
Throughout the distribution process, careful attention is paid to handling practices to maintain the integrity and quality of the stainless steel.
By following these steps, stainless steel manufacturers can produce high-quality, durable and versatile products that meet the diverse needs of numerous industries.
5 Things You Should Avoid
- Using Low-Quality Raw Materials: The quality of stainless steel production starts with the raw materials. Using low-quality ores or recycled materials with contaminants can lead to inferior end products that fail to meet industry standards.
- Skipping Proper Heat Treatment: Heat treatment is crucial for achieving the desired mechanical properties of stainless steel. Omitting or incorrectly performing this step can result in a product that lacks the necessary hardness, ductility, or resistance to corrosion. Precise control of the heating and cooling processes is essential for producing high-quality stainless steel.
- Neglecting Quality Control Measures: Quality control is necessary at every stage of production to ensure the final product meets all specifications. Neglecting or cutting corners on quality control measures can result in subpar products with defects or inconsistencies that could compromise their performance.
- Ignoring Proper Cleaning and Finishing Techniques: Stainless steel is known for its resistance to corrosion, but this does not mean it is completely impervious. Proper cleaning and finishing techniques are crucial for preventing contamination and preserving its corrosion-resistant properties.
- Not Designating Appropriate Grades for Specific Applications: Stainless steel comes in a variety of grades, each with different compositions and properties suitable for specific applications. Not designating the appropriate grade can result in a product that is not optimized for its intended use, leading to potential performance issues or failure.
By following these five tips, you can ensure that the stainless steel products you produce are of the highest quality.
Conclusion
How to produce stainless steel is a multifaceted process that necessitates careful attention to detail at every stage. From selecting and preparing high-caliber raw materials to employing precise melting, casting, and forming techniques, each step is critical to achieving a superior final product.
Following proper heat treatment protocols ensures the steel possesses the desired mechanical properties, while meticulous finishing and rigorous quality control procedures safeguard against any defects that could compromise performance.
By adhering to these thorough and exacting steps, manufacturers can produce stainless steel that not only meets but exceeds industry standards, delivering reliable and versatile materials suitable for a wide array of applications.
The continuous improvement and innovation within the production process guarantee that stainless steel remains a cornerstone material in industries ranging from construction to medical instruments.
Edmund Sumlin is a skilled author for Metal Fixes, bringing 6 years of expertise in crafting a wide range of metal fixtures. With a strong background in metalwork, Edmund’s knowledge spans various types of fixtures, from decorative pieces to functional hardware, blending precision with creativity. His passion for metalworking and design has made him a trusted resource in the industry.
Professional Focus:
- Expert in Metal Fixtures : Edmund aesthetic specializes in creating durable and innovative metal fixtures, offering both appeal and functionality. His work reflects a deep understanding of metalworking techniques and materials.
- Sustainability Advocate : He is dedicated to using sustainable practices, ensuring that every fixture is crafted with eco-friendly methods while maintaining high-quality standards.
In his writing for Metal Fixes, Edmund provides valuable insights into the latest trends, techniques, and practical advice for those passionate about metal fixtures, whether they are professionals or DIY enthusiasts. His focus on combining artistry with engineering helps others discover the true potential of metal in design.