Are you struggling with spatter when flux core welding? It’s a common issue for many welders, and it can lead to wasted material, time spent dealing with messes, and diminished product quality. However, you don’t have to accept spatter as part of the process. There are several techniques that professional welders use to reduce the amount of spatter produced during flux core welding.
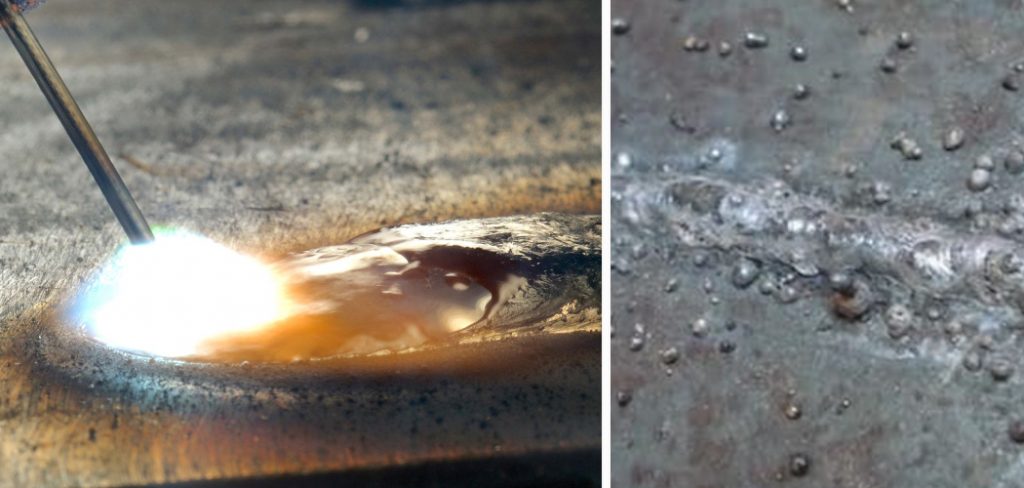
Flux-core welding, also known as flux-cored arc welding (FCAW), is a type of arc welding that uses a continuously fed tubular electrode containing flux to create the weld. Flux core welding is popular due to its ability to produce high-quality welds quickly and easily, making it a common choice for industrial applications. Read on to learn more about how to reduce spatter when flux core welding!
What Will You Need?
Before we get into the techniques for reducing spatter, let’s first go over what you will need:
- A welding machine designed explicitly for flux core welding
- Flux core welding wire (self-shielding or gas-shielded)
- Protective gear including gloves, helmet, and safety glasses
- Welding surface and clamps
Now that you have everything ready to go let’s dive into the techniques for minimizing spatter when flux core welding!
10 Easy Steps on How to Reduce Spatter When Flux Core Welding
Step 1. Ensure Proper Machine Set-up:
Start by setting up your welding machine correctly. Check the manufacturer’s guidelines for the appropriate voltage and wire speed settings for the specific material and thickness you are working with. Incorrect settings can result in excessive spatter.
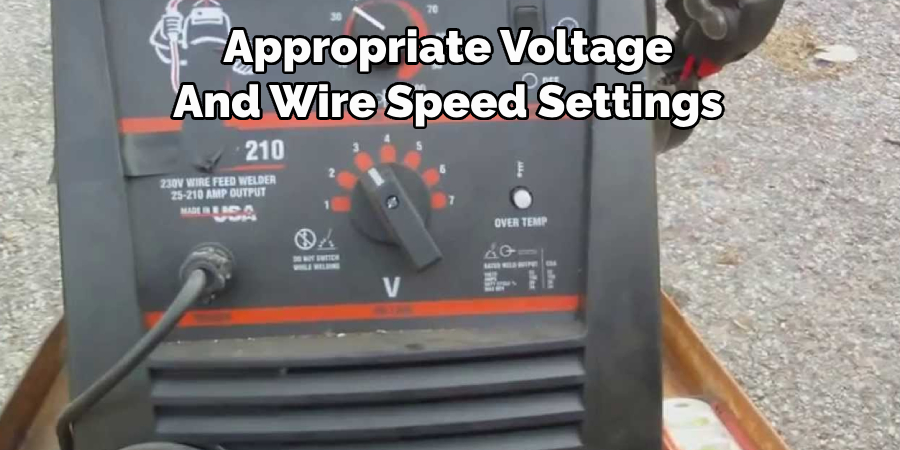
Step 2. Clean Your Work Surface:
Spatter can be exacerbated by a dirty, rusted, or painted surface. Before welding, ensure the work surface is clean and free of any debris or substances that might interfere with the weld. Use a wire brush or grinder to clean the area you will be welding on. A clean surface allows for better wire contact and can significantly reduce spatter.
Step 3. Choose the Right Wire:
The kind of wire you use can also influence the spatter produced. Ensure you’re using a quality flux core wire suitable for your welding material. Low-quality wires often lead to higher spatter levels. Further, make sure the wire diameter matches your machine’s specifications and the thickness of your material.
Step 4. Maintain the Proper Stick-Out Length:
The stick-out length, or the length of the wire that extends from the end of the contact tip, can significantly influence the amount of spatter during flux core welding. Too long or too short a stick-out can lead to excessive spatter. Generally, a stick-out length of 3/4 inch to 1 inch is recommended for flux core welding. However, this can vary depending on the wire size and type of flux core wire used. Always refer to the wire manufacturer’s guidelines for the best results.
Step 5. Use the Correct Angle:
The angle at which you hold the torch is crucial in spatter control. For Flux Core welding, a drag or pull technique is often recommended. This means you should angle the gun opposite to your welding path. A good rule of thumb is to maintain a 10 to 15-degree angle. Too steep of an angle can increase the likelihood of a spatter.
Step 6. Control Your Travel Speed:
Maintaining a consistent travel speed is crucial in reducing spatter when flux core welding. Moving too quickly can cause the weld to become unstable, thereby increasing the spatter. On the other hand, moving too slowly can lead to excessive heat, which can also result in increased spatter. The optimal travel speed varies depending on the material thickness, type of wire, and machine settings. It’s beneficial to practice on scrap material to find the travel speed that produces the least amount of spatter for your specific setup.
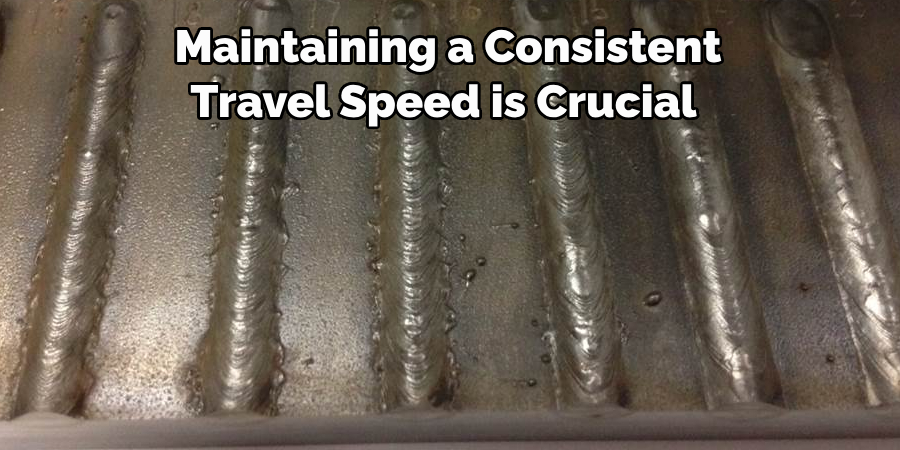
Step 7. Adjust Wire Feed Speed and Voltage:
Wire feed speed and voltage are crucial factors impacting the spatter produced during flux core welding. If your wire feed speed is too fast or your voltage setting is too high, it can lead to more spatter. Conversely, if the wire feed speed is too slow or the voltage too low, it can lead to incomplete penetration and still cause a spatter. It’s essential to find the right balance for your specific welding conditions. Start with the manufacturer’s recommended settings and adjust as needed based on your observations and results.
Step 8. Use Anti-Spatter Spray:
Anti-spatter spray is a useful tool that can help reduce spatter in flux core welding. This spray forms a protective layer on the surface of the metal, preventing the spatter from sticking. Before you begin welding, spray the anti-spatter solution onto the weld area. However, it’s crucial not to spray it directly onto the welding wire or torch, as it can interfere with the electrode. Remember, this spray is not a substitute for proper welding techniques and settings, but it can be a helpful addition in your efforts to reduce spatter.
Step 9. Regularly Check and Replace Contact Tips:
Contact tips are susceptible to wear and tear over time. Old or worn-out contact tips can negatively impact the wire feed and welding arc, increasing spatter. Regular inspections and timely replacements of contact tips can help maintain optimal welding conditions and reduce spatter. Always ensure that the hole in the contact tip aligns with the diameter of the welding wire for the best performance.
Step 10. Practice and Experiment:
Lastly, practice and experiment with different settings and techniques. Each welding job is unique and may require slight adjustments to produce the least spatter. Practice on scrap material before starting the actual welding job to understand how different variables — like wire speed, voltage, angle, and travel speed — affect the spatter. Remember, achieving a spatter-free weld requires patience and skill, which are developed with time and practice.
Following these ten easy steps can significantly reduce spatter when flux core welding. Remember always to prioritize safety and wear the necessary protective gear, including a welding helmet and safety glasses.
5 Additional Tips and Tricks
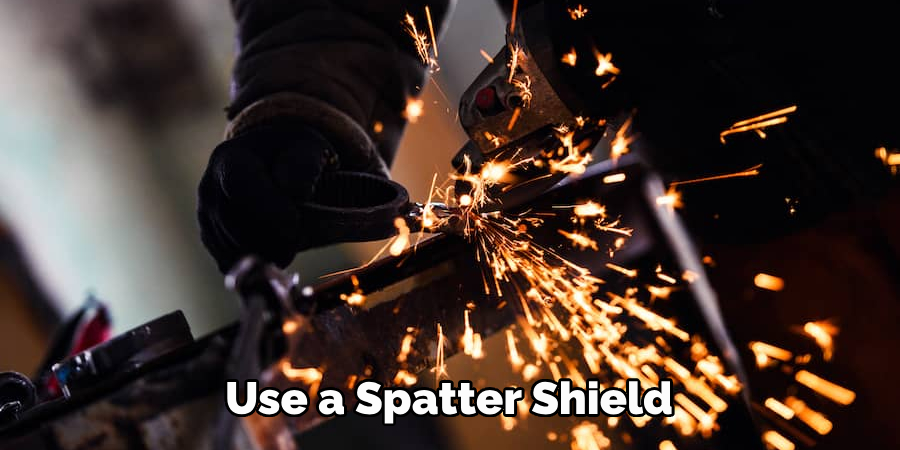
- Use a Spatter Shield: A spatter shield can help reduce the spatter that sticks to your gun and work surface. It acts as a barrier, preventing spatter from reaching unwanted areas.
- Invest in a High-Quality Welder: High-quality welders often have advanced technology that can help reduce spatter. Features like adjustable inductance control can help fine-tune your arc characteristics and minimize spatter.
- Check Gas Quality and Flow: If using gas-shielded flux core welding, ensure you have the correct gas type and flow rate. Incorrect gas or flow rate can lead to increased spatter.
- Keep Your Welding Station Organized: An organized welding station can help reduce any unnecessary errors that might lead to excessive spatter. Keep your wires, tools, machine parts, and other equipment neatly arranged and easily accessible.
- Attend Professional Training: If you’re new to flux core welding or have persistent issues with spatter, consider attending a professional welding workshop or training session. You’ll learn valuable tips and tricks from experienced welders and understand the factors that affect spatter more comprehensively.
Remember, reducing spatter in flux core welding is about understanding the various factors that contribute to it and making the necessary adjustments.
5 Things You Should Avoid
- Avoid Poor Preparation: Improper preparation of your workpiece can lead to excessive spatter. Always clean your workpieces thoroughly to remove rust, paint, oil, or dirt. These contaminants can adversely affect your weld and cause a spatter.
- Avoid Welding with Damaged Equipment: Using damaged or worn-out equipment can lead to unstable arcs and increased spatter. Always inspect your welding equipment for any damage before you begin, and replace or repair parts as needed.
- Avoid Incorrect Welding Techniques: Incorrect welding techniques, such as using the wrong torch angle or travel speed, can contribute to excessive spatter. Always use the recommended techniques for your specific welding job.
- Avoid Ignoring Manufacturer Recommendations: Ignoring the wire manufacturer’s guidelines on voltage, wire feed speed, or stick-out length can lead to a spatter. Start with the manufacturer’s recommended settings and fine-tune them as necessary based on your results.
- Avoid Forgoing Safety Measures: While this may not directly cause spatter, forgoing safety measures can lead to severe injuries. Always wear personal protective equipment (PPE), such as a welding helmet and safety glasses. Remember, safety should always be your top priority when welding.
By avoiding these common mistakes, you can significantly reduce spatter and produce high-quality welds consistently.
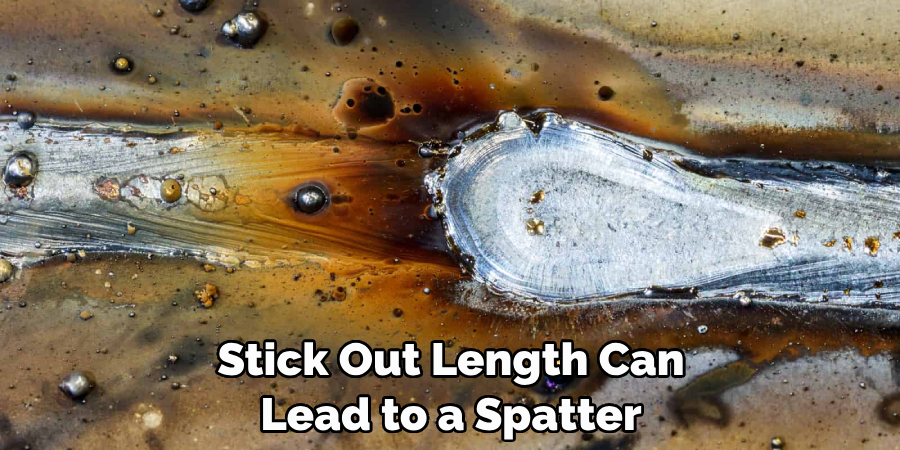
Conclusion
Ultimately, understanding how to reduce spatter when flux core welding is an invaluable skill that can help you craft a more professional-looking finished piece. Taking the time to practice your technique and using the equipment correctly are both essential steps in the process. Keeping your aluminum clean, using the right flux core wire size, choosing a lower voltage setting with higher amperage, and adjusting your stick out will all help you reduce spatter.
Hopefully, the article on reducing spatter when flux core welding has provided you with helpful information and tips that will help you achieve spatter-free welds. Remember always to prioritize safety, practice regularly, and experiment with different techniques and settings.
So get out there and start practicing today!
Edmund Sumlin is a skilled author for Metal Fixes, bringing 6 years of expertise in crafting a wide range of metal fixtures. With a strong background in metalwork, Edmund’s knowledge spans various types of fixtures, from decorative pieces to functional hardware, blending precision with creativity. His passion for metalworking and design has made him a trusted resource in the industry.
Professional Focus:
- Expert in Metal Fixtures : Edmund aesthetic specializes in creating durable and innovative metal fixtures, offering both appeal and functionality. His work reflects a deep understanding of metalworking techniques and materials.
- Sustainability Advocate : He is dedicated to using sustainable practices, ensuring that every fixture is crafted with eco-friendly methods while maintaining high-quality standards.
In his writing for Metal Fixes, Edmund provides valuable insights into the latest trends, techniques, and practical advice for those passionate about metal fixtures, whether they are professionals or DIY enthusiasts. His focus on combining artistry with engineering helps others discover the true potential of metal in design.