Removing a compression fitting from a copper pipe is a task that many homeowners and DIY enthusiasts encounter during plumbing repairs or modifications. Compression fittings are widely used for their ease of installation and reliable sealing, making them a popular choice in various plumbing applications.
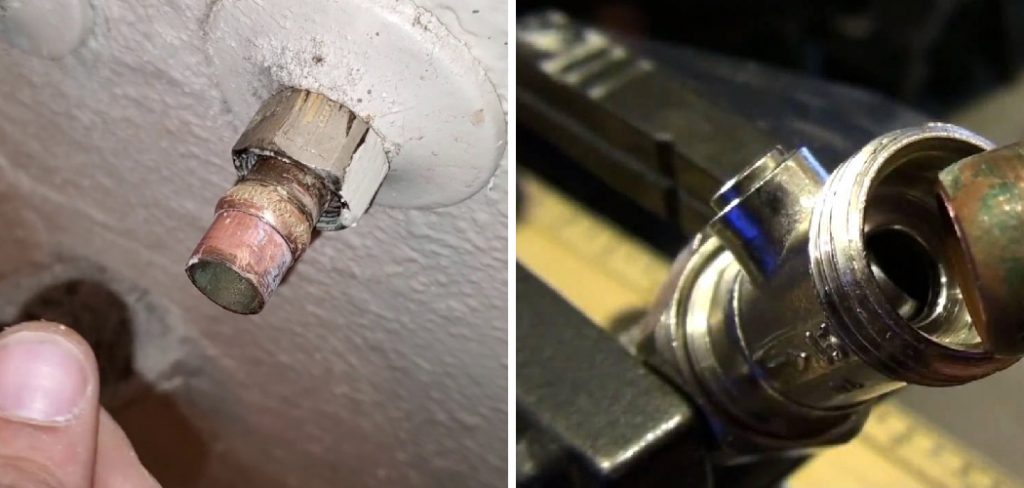
However, when a fitting needs to be replaced or adjusted, knowing how to remove it without damaging the copper pipe is essential. The process involves loosening the compression nut, carefully extracting the ferrule, and ensuring the pipe remains intact for future use.
This guide will provide a step-by-step phow to remove a compression fitting from a copper pipe, detailing the necessary tools and techniques to ensure a smooth and successful removal.
Additionally, we will cover tips for troubleshooting common issues and advice on preparing the pipe for new fittings. By mastering this skill, you’ll enhance your plumbing capabilities and maintain the integrity of your copper piping system.
Understanding Compression Fittings
Compression fittings are a crucial component in many plumbing systems, known for their simplicity and effectiveness in creating secure connections.
These fittings consist of three main parts: the compression nut, the compression ring (or ferrule), and the fitting body. The compression nut is threaded onto the fitting body, and the ferrule is positioned between the nut and the pipe.
As the nut is tightened, it compresses the ferrule against both the fitting body and the pipe, forming a tight seal that can withstand various pressures and temperatures.
This mechanism not only makes installation straightforward but also allows for easy disassembly and reassembly, which is particularly useful in situations where the plumbing system may need to be adjusted or repaired.
Understanding how these components work together is essential for both installation and removal.
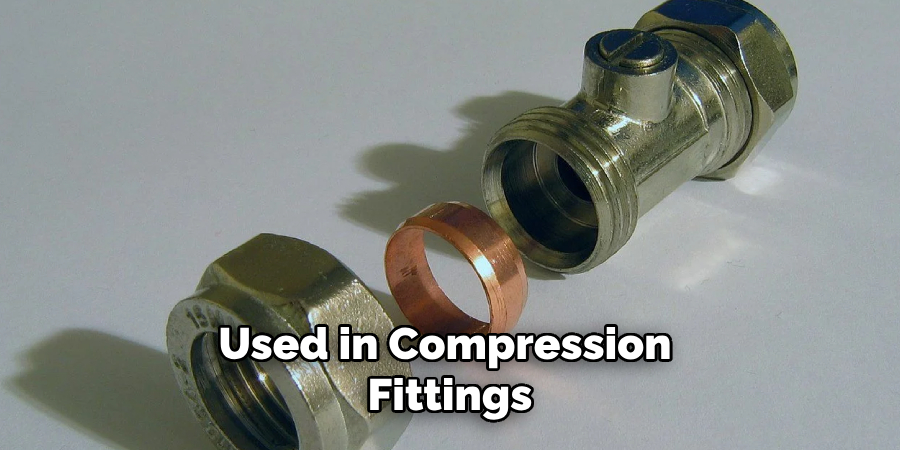
The materials used in compression fittings, typically brass or stainless steel, contribute to their durability and corrosion resistance, ensuring a long-lasting connection. Additionally, they are versatile and can be used with copper, plastic, and other types of pipes.
By comprehending the fundamental principles of compression fittings, you can confidently tackle both installation and removal tasks, ensuring the reliability and efficiency of your plumbing system.
10 Methods How to Remove a Compression Fitting from a Copper Pipe
1. Using Compression Fitting Removal Tool
The most straightforward method to remove a compression fitting from a copper pipe involves using a compression fitting removal tool. This tool is specifically designed to make the task easy and efficient.
To start, ensure the water supply to the pipe is turned off. Place a bucket or towel under the pipe to catch any residual water. Loosen the compression nut using an adjustable wrench or pliers by turning it counterclockwise.
Slide the removal tool onto the pipe and align it with the compression ring (ferrule). The tool’s jaws will grip the pipe and the ferrule. Tighten the tool’s handle to apply pressure and pull the ferrule away from the pipe.
2. Cutting the Pipe and Removing the Fitting
In situations where the compression fitting is difficult to remove, cutting the pipe may be necessary.
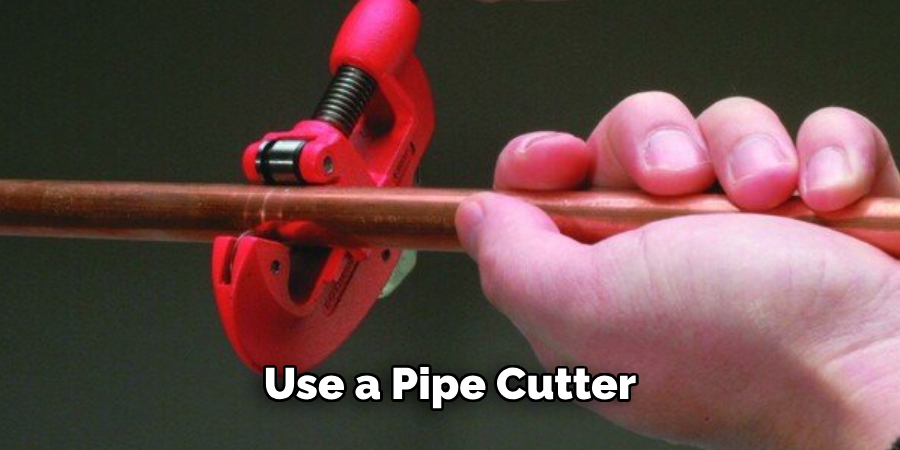
Begin by turning off the water supply and draining any remaining water from the pipe. Use a pipe cutter to make a clean cut a few inches away from the compression fitting. Ensure the cut is straight and smooth to facilitate the installation of a new fitting later.
Once the pipe is cut, you can remove the compression fitting by loosening the compression nut with an adjustable wrench. Slide the nut and compression ring off the cut section of the pipe.
3. Applying Heat
Applying heat to the compression fitting can help loosen it, making removal easier. Begin by turning off the water supply and draining the pipe. Use a propane torch to gently heat the compression nut and fitting. Heat will cause the metal to expand, loosening the compression ring’s grip on the pipe.
Once the fitting is heated, use an adjustable wrench to turn the compression nut counterclockwise. Be cautious when applying heat, as excessive heating can damage the pipe or fitting. It is important to heat the fitting evenly and avoid direct contact with the flame to prevent overheating.
4. Using Penetrating Oil
Penetrating oil can help loosen a compression fitting that is stuck due to corrosion or mineral buildup. Turn off the water supply and drain the pipe. Apply penetrating oil generously around the compression nut and fitting.
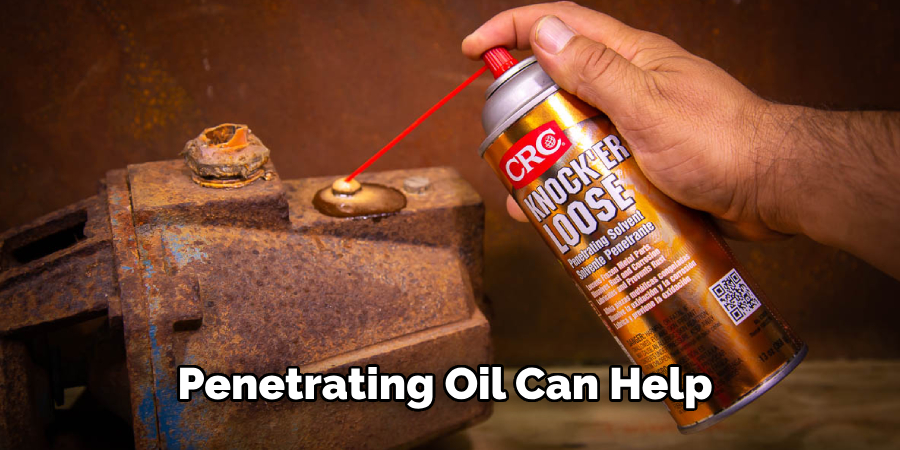
Allow the oil to seep into the fitting for several minutes, or as recommended by the oil’s manufacturer. The oil will penetrate and lubricate the threads, making it easier to turn the compression nut. Use an adjustable wrench or pliers to loosen the nut by turning it counterclockwise.
5. Using Two Wrenches
The two-wrench method provides additional leverage for removing a compression fitting. Begin by turning off the water supply and draining the pipe. Use one wrench to hold the compression fitting body steady. Place the second wrench on the compression nut and turn it counterclockwise.
The first wrench prevents the fitting from turning and ensures that all the force is applied to loosening the nut. This method is particularly effective for fittings that are tightly secured and require extra force to remove.
Using two wrenches helps distribute the force evenly and reduces the risk of damaging the pipe or fitting. Ensure that the wrenches are properly positioned to avoid slipping and causing injury.
6. Cutting the Compression Nut
If the compression fitting is particularly stubborn, cutting the compression nut may be necessary. Begin by turning off the water supply and draining the pipe. Use a hacksaw or rotary tool with a cutting wheel to carefully cut through the compression nut.
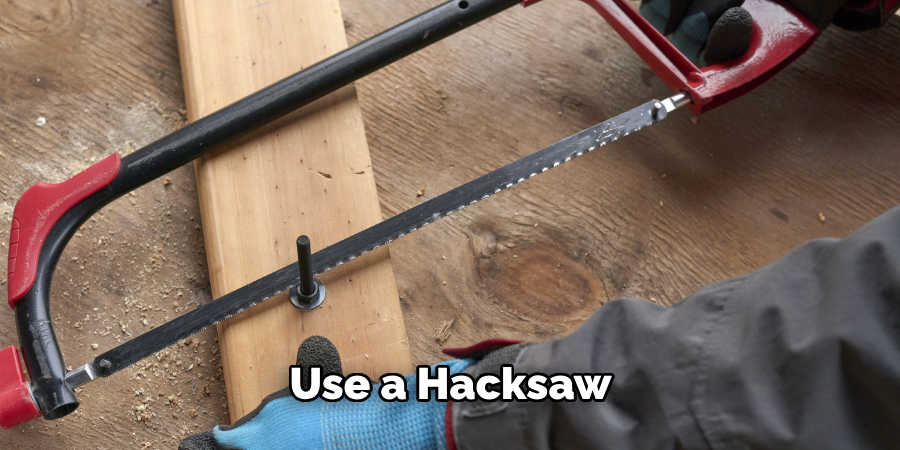
Make two parallel cuts on opposite sides of the nut, being careful not to damage the pipe. Once the nut is cut, use a flathead screwdriver to pry it apart and remove it from the pipe.
7. Tapping with a Hammer
Gently tapping the compression fitting with a hammer can help loosen it by breaking the bond between the nut, ferrule, and pipe.
Turn off the water supply and drain the pipe. Use an adjustable wrench to hold the compression nut steady. Lightly tap the fitting with a hammer, focusing on the nut and ferrule. The vibrations from the tapping can help break any corrosion or mineral deposits that may be causing the fitting to stick.
Once the fitting is loosened, use the wrench to turn the nut counterclockwise and remove it. This method is effective for fittings that are stuck but not heavily corroded. Be careful not to use excessive force, as this can damage the pipe or fitting.
8. Using a Pipe Freezer Kit
A pipe freezer kit can temporarily freeze the water inside the pipe, creating a solid plug and allowing you to remove the compression fitting without draining the entire system.
Follow the manufacturer’s instructions to set up the pipe freezer kit. Once the water inside the pipe is frozen, use an adjustable wrench to loosen the compression nut by turning it counterclockwise. The frozen water plug prevents any residual water from leaking while you work on the fitting.
9. Using a Vice Grip
A vice grip, or locking pliers, can provide a secure hold on the compression fitting, making it easier to remove. Turn off the water supply and drain the pipe. Adjust the vice grip to fit tightly around the compression nut.
Lock the pliers in place to hold the nut securely. Use an adjustable wrench or another pair of pliers to turn the fitting body counterclockwise. The vice grip holds the nut steady, allowing you to apply more force to the fitting body.
10. Using a Screw Extractor
A screw extractor can be used to remove a damaged or stripped compression fitting nut. Begin by turning off the water supply and draining the pipe. Drill a small pilot hole into the center of the compression nut.
Insert the screw extractor into the hole and turn it counterclockwise. The extractor’s threads will bite into the metal, allowing you to turn and remove the nut.
Conclusion
Removing a compression fitting from a copper pipe can be achieved through various methods, each suited to different situations and levels of difficulty.
The use of a compression fitting removal tool is the most straightforward and efficient, ensuring minimal damage to the pipe. Cutting the pipe and removing the fitting is a reliable method for stubborn fittings, while applying heat or penetrating oil can help loosen corroded or seized fittings.
Using two wrenches provides additional leverage, and cutting the compression nut is a last resort for particularly stubborn fittings. Tapping with a hammer, using a pipe freezer kit, or employing a vice grip can also facilitate the removal process.
Finally, a screw extractor can be used for damaged or stripped fittings. Now that you know how to remove a compression fitting from a copper pipe. While it does take a few steps each time, hopefully now you understand the process and why it’s worth taking the extra step to make sure your floor is properly cared for. So don’t wait any longer, take action today!
Edmund Sumlin is a skilled author for Metal Fixes, bringing 6 years of expertise in crafting a wide range of metal fixtures. With a strong background in metalwork, Edmund’s knowledge spans various types of fixtures, from decorative pieces to functional hardware, blending precision with creativity. His passion for metalworking and design has made him a trusted resource in the industry.
Professional Focus:
- Expert in Metal Fixtures : Edmund aesthetic specializes in creating durable and innovative metal fixtures, offering both appeal and functionality. His work reflects a deep understanding of metalworking techniques and materials.
- Sustainability Advocate : He is dedicated to using sustainable practices, ensuring that every fixture is crafted with eco-friendly methods while maintaining high-quality standards.
In his writing for Metal Fixes, Edmund provides valuable insights into the latest trends, techniques, and practical advice for those passionate about metal fixtures, whether they are professionals or DIY enthusiasts. His focus on combining artistry with engineering helps others discover the true potential of metal in design.