Are you having trouble with electrolysis on your aluminum structures? Not to worry – there are actually several straightforward methods you can use to prevent corrosion and deterioration of all types of aluminum fixtures.
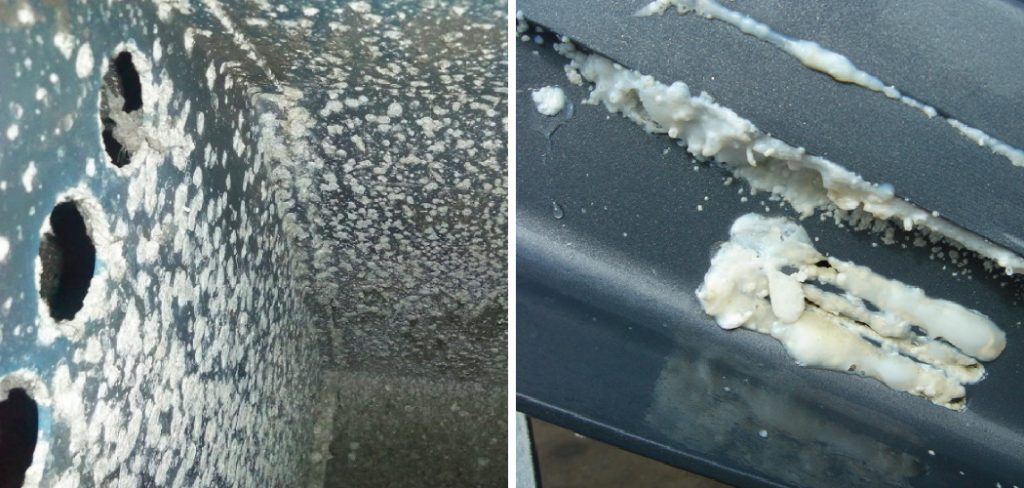
In this blog post on how to stop electrolysis on aluminum, we’ll go over exactly what electrolysis is, why it can be damaging for aluminum structures, and how to successfully implement preventive measures to keep your systems safe from corrosion in the long run. Read on for tips and tricks that will help you protect your investment by stopping electrolysis altogether!
What is Electrolysis?
Electrolysis is a process that occurs when two different metals are in contact with each other, and an electrical current flows between them. The flow of electricity results in the corrosion of one metal (in this case, aluminum) and the protection of the other metal. This kind of corrosion can be especially damaging for aluminum structures, as it weakens their integrity and can eventually lead to structural failure.
Why is Electrolysis a Problem for Aluminum?
Aluminum is a highly reactive metal, which means it is prone to corrosion when in contact with other metals. When aluminum is in contact with a more active metal (such as copper or steel), it becomes the anode in the electrochemical reaction and corrodes at a rapid rate.
This type of corrosion can be particularly problematic for aluminum structures that are exposed to harsh environments or are in constant contact with other metals, such as boats, pipelines, or electrical systems.
10 Simple Step-by-step Guidelines on How to Stop Electrolysis on Aluminum
Step 1: Identify the Problem
Before you can effectively stop electrolysis on your aluminum structures, it’s important to first identify the problem. Look for signs of corrosion such as discoloration, pitting, or flaking on your fixtures. It’s also a good idea to test for the presence of an electrical current using a multimeter. But keep in mind that even if you don’t see any visible signs of corrosion, it’s still possible for electrolysis to be occurring.
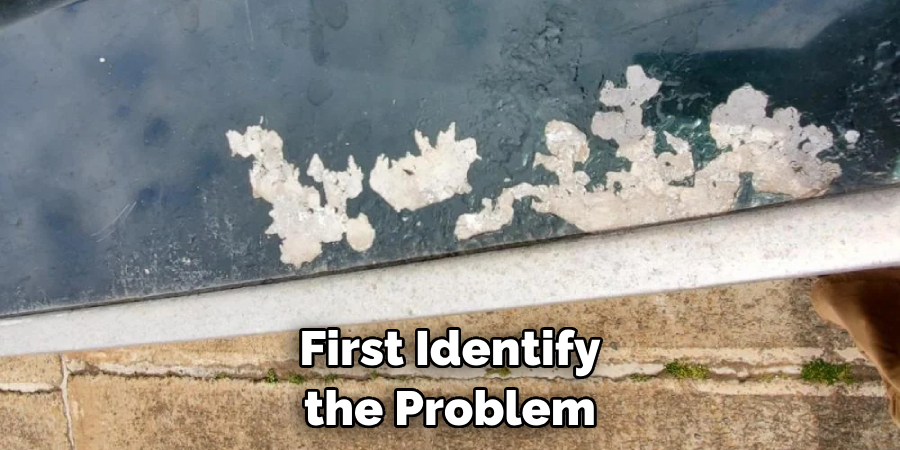
Step 2: Use Appropriate Materials
When repairing or replacing aluminum structures, be sure to use materials that are compatible with aluminum. This includes fasteners, adhesives, and protective coatings. Avoid using materials made from dissimilar metals as they can cause electrolysis even if the aluminum is properly protected. You can also use isolating pads or tapes to create a barrier between different metals.
Step 3: Properly Clean and Prep the Surface
Before applying any protective coatings or paints, be sure to properly clean and prep the surface of your aluminum structures. This includes removing any dirt, oils, or debris that could interfere with the adhesion of protective materials. Use a mild detergent and water for cleaning, followed by sanding or wire brushing for prepping.
Step 4: Utilize Cathodic Protection
Cathodic protection involves attaching a sacrificial metal (such as magnesium, zinc, or aluminum) to the structure that you want to protect. This sacrificial metal will corrode instead of the main structure, preventing electrolysis and corrosion from occurring. It’s important to regularly inspect and replace the sacrificial metal as needed.
Step 5: Apply Protective Coatings
For added protection against electrolysis, consider applying a protective coating to your aluminum structures. These coatings can be in the form of paints, sealants, or anodized finishes. Be sure to choose a coating that is specifically designed for use on aluminum and follow the application instructions carefully. Although these coatings will eventually wear off and need to be reapplied, they can significantly prolong the life of your aluminum fixtures.
Step 6: Avoid Galvanic Coupling
Galvanic coupling occurs when two dissimilar metals are connected in a wet or conductive environment, and an electrical current is created between them. To avoid this type of electrolysis, make sure to properly insulate and separate aluminum structures from other metals using materials such as rubber gaskets or plastic washers. You can also use dielectric unions to prevent contact between different metals.
Step 7: Use Dielectric Unions
Dielectric unions are specially designed fittings that prevent direct contact between two different metals. They are commonly used in plumbing and electrical systems to stop electrolysis and corrosion from occurring. Consider using these unions when connecting aluminum structures to other metal components.
Step 8: Implement Regular Maintenance
Regular maintenance is crucial for preventing electrolysis on aluminum structures. This includes regular inspections, cleanings, and repairs as needed. By catching any signs of corrosion early, you can prevent it from spreading and causing significant damage. It’s also important to replace any sacrificial metals or protective coatings that have worn off. You should also periodically test for electrical current using a multimeter.

Step 9: Monitor Water Quality
If your aluminum fixtures are in contact with water, it’s important to monitor the quality of the water to ensure it is not corrosive. High levels of chlorine, salinity, or acidity can accelerate the corrosion process and lead to electrolysis. Consider installing water filtration systems or using anti-corrosive additives to prevent this from happening. You should also regularly flush out any stagnant water to prevent the buildup of corrosive agents.
Step 10: Seek Professional Help
If you’re unsure about how to stop electrolysis on your aluminum structures, it’s always best to seek professional help. A certified corrosion specialist can provide guidance and assistance in identifying and stopping electrolysis. They can also recommend the best materials and techniques for protecting your aluminum fixtures from corrosion. With their expertise, you can ensure the longevity and safety of your structures.
Overall, by following these simple guidelines on how to stop electrolysis on aluminum, you can effectively stop electrolysis on aluminum and prevent costly damage to your structures. Remember that prevention is key when it comes to electrolysis, so be proactive in maintaining and protecting your aluminum fixtures.
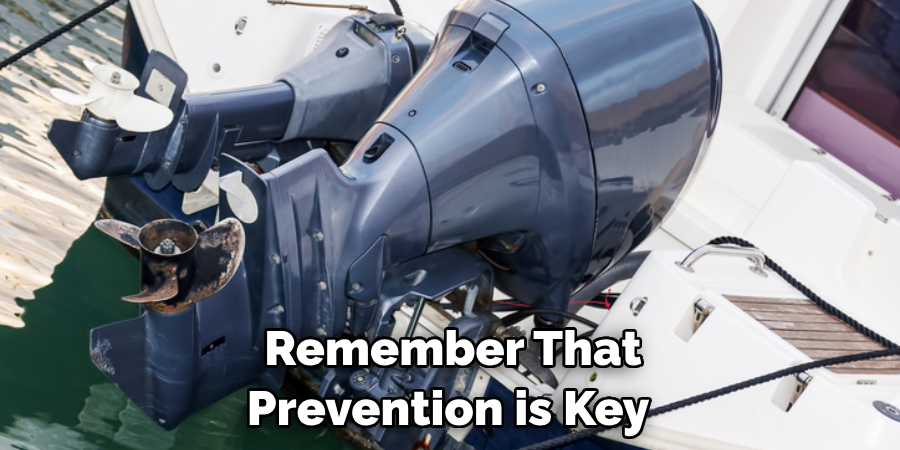
With proper care and maintenance, you can enjoy the benefits of this lightweight and versatile metal for years to come. So don’t let electrolysis be a problem for aluminum any longer – take action now!
Do You Need to Get Help From Professionals?
If you are still experiencing electrolysis issues with your aluminum structures, or need assistance in identifying and stopping the problem, don’t hesitate to seek help from a certified corrosion specialist.
These professionals have extensive knowledge and expertise in dealing with electrolysis and can provide tailored solutions for your specific situation. They can also offer advice on preventative measures to ensure long-term protection against electrolysis.
Don’t let electrolysis ruin your aluminum structures – seek professional help and ensure their longevity. So if you’re struggling with electrolysis, don’t hesitate to reach out for help and protect your investment! With the right guidance and care, you can keep your aluminum fixtures in top shape for years to come.
Frequently Asked Questions
Q1: What is Electrolysis?
A1: Electrolysis is a chemical reaction that occurs when two dissimilar metals are in contact with each other in the presence of an electrolyte (such as water). This can cause corrosion and damage to one or both of the metals involved. In the case of aluminum, electrolysis can lead to pitting or white powdery deposits on the surface.
Q2: How does Cathodic Protection work?
A2: Cathodic protection involves attaching a sacrificial metal (such as magnesium, zinc, or aluminum) to the structure that you want to protect. This sacrificial metal will corrode instead of the main structure, preventing electrolysis and corrosion from occurring.
Regular maintenance and replacement of the sacrificial metal is necessary for effective cathodic protection.
Q3: Can I prevent electrolysis on aluminum structures?
A3: Yes, it is possible to prevent or minimize electrolysis on aluminum structures by following proper preventative measures such as utilizing cathodic protection, applying protective coatings, and avoiding galvanic coupling. Regular maintenance and monitoring of water quality can also help prevent electrolysis. Seeking professional help is recommended for more severe cases of electrolysis.
Q4: How do I know if my aluminum structure is experiencing electrolysis?
A4: Signs of electrolysis on aluminum structures may include pitting or white powdery deposits on the surface, discoloration, and corrosion at connection points with other metals. Regular inspections and testing for electrical current can help identify and address electrolysis early on. If you suspect electrolysis, it is best to seek professional help for proper diagnosis and treatment.
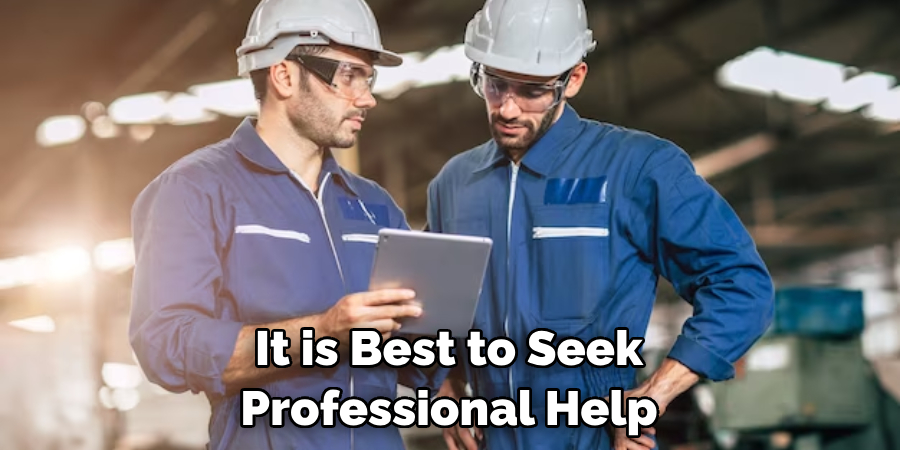
Conclusion
With all the available options, there is no excuse for allowing electrolysis on aluminum to go unchecked. Through vigilance and prompt action, you can ensure that your aluminum components last as long as you need them.
So make sure you pay attention to any corrosion that may arise and address it in a timely manner; it may help add years to the life of your assets. Whether you choose chemical corrosion inhibitors, sacrificial anodes or any other mitigation option, take preventive measures before electrolysis becomes a large issue with costly consequences.
Don’t wait: start protecting your aluminum components from electrolysis today! Thanks for reading this article on how to stop electrolysis on aluminum.
Edmund Sumlin is a skilled author for Metal Fixes, bringing 6 years of expertise in crafting a wide range of metal fixtures. With a strong background in metalwork, Edmund’s knowledge spans various types of fixtures, from decorative pieces to functional hardware, blending precision with creativity. His passion for metalworking and design has made him a trusted resource in the industry.
Professional Focus:
- Expert in Metal Fixtures : Edmund aesthetic specializes in creating durable and innovative metal fixtures, offering both appeal and functionality. His work reflects a deep understanding of metalworking techniques and materials.
- Sustainability Advocate : He is dedicated to using sustainable practices, ensuring that every fixture is crafted with eco-friendly methods while maintaining high-quality standards.
In his writing for Metal Fixes, Edmund provides valuable insights into the latest trends, techniques, and practical advice for those passionate about metal fixtures, whether they are professionals or DIY enthusiasts. His focus on combining artistry with engineering helps others discover the true potential of metal in design.