Are you intrigued by the beauty and strength of aluminum welding? It can be intimidating to take on a new welding project, especially if it’s your first time trying out tig welding. But don’t let that stop you from grabbing a few essential tools and diving in headfirst!
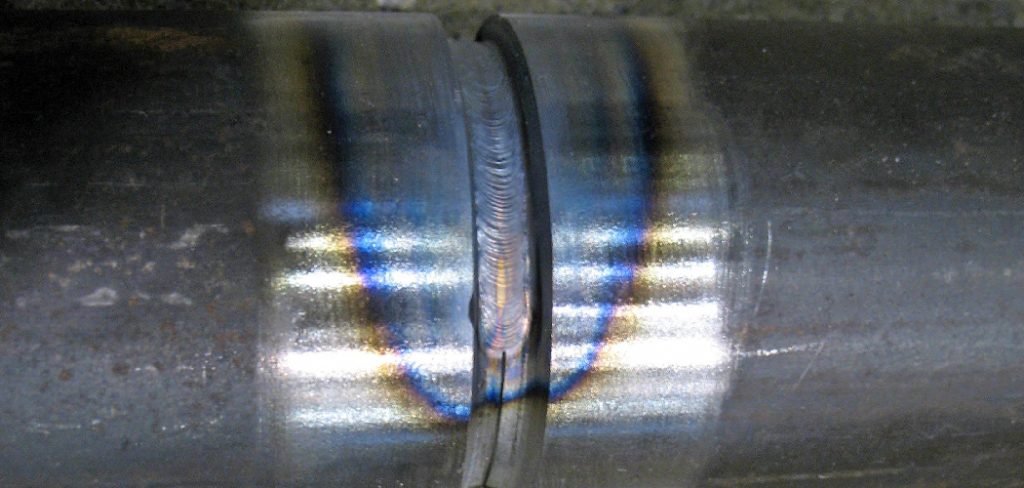
With our step-by-step guide on how to tig weld aluminum for beginners, we’ll teach you how to get started with tig welding aluminum in no time. Raising confidence levels so that novice welders can tackle any job is an important part of what we do here at Company Name. From gathering materials to finishing touches, this tutorial will give you everything you need for success.
Why Tig Welding?
Tig welding is known for its precision and clean welds, making it the go-to choice when working on aluminum projects. The tig welding process involves using heat from an electric arc to join two pieces of metal together.
This method allows for more control over the weld pool, resulting in less distortion and a cleaner finish. Thus, tig welding is an excellent option for beginners who want to achieve quality results.
Materials You Will Need
Before you begin your tig welding journey, it’s essential to gather all the necessary materials. Here’s a list of what you’ll need:
- A tig welder (AC/DC is preferable for aluminum)
- Tungsten electrode (2% thoriated works well with aluminum)
- Welding gloves
- Safety glasses or welding helmet
- A suitable filler rod (ER4043 for aluminum)
- Clean stainless steel wire brush
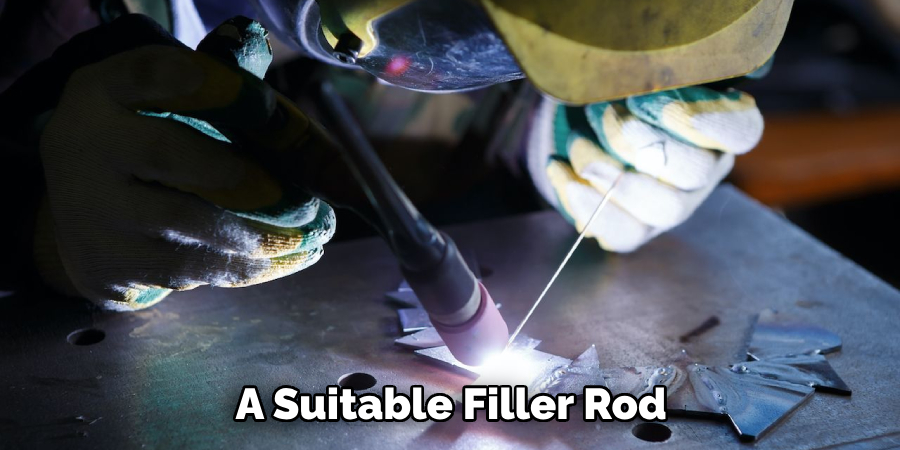
11 Step-by-step Guidelines on How to Tig Weld Aluminum for Beginners
Step 1: Prepare Your Workspace
Before starting any welding project, it’s essential to have a clean and safe workspace. Make sure there is no flammable material near your work area, and you have proper ventilation. It’s also crucial to have a sturdy work surface to hold your project securely. You can use a welding table or make one yourself using a thick metal plate. It’s also recommended to have a fire extinguisher nearby in case of emergencies.
Step 2: Clean Your Aluminum Pieces
Aluminum oxide can form on the surface of the metal, preventing proper welding. Use a clean stainless steel wire brush to remove any debris and oxidation from the aluminum pieces you’ll be working with. But be careful not to use the same brush on other metals, as it can contaminate them. This step is crucial to ensure a clean weld and avoid any potential issues.
Step 3: Set Up Your Welder
Make sure your tig welder is set up correctly for aluminum. This includes adjusting the amperage, welding mode (AC if available), and gas flow rate. We recommend practicing on scrap pieces of aluminum to find the right settings before starting your project.
You can also refer to the manufacturer’s manual for specific instructions on setting up your welder for aluminum welding. Although it may seem tedious, proper setup is crucial to achieving quality welds.
Step 4: Prepare Your Tungsten Electrode
Before inserting the tungsten electrode into your welder’s torch, make sure it’s clean and sharpened. A pointed tip is essential for tig welding aluminum as it produces a smaller, more precise arc. You can use a dedicated tungsten grinder or a plain sanding wheel to sharpen your electrode.
Once you have a sharp point, insert the electrode into the collet and tighten it. It’s also recommended to have a spare tungsten electrode on hand in case your current one becomes contaminated during welding.
Step 5: Begin Welding
Now it’s time to start welding! Make sure you’re in a comfortable position with a clear view of your workpiece. Start by creating an arc between the tungsten electrode and the aluminum, and then slowly move the torch to create a small puddle.
Use your other hand to guide the filler rod into the weld pool at a slight angle. Keep the torch steady, and use small circular movements to control the size of your puddle. Remember to pause occasionally to allow for proper cooling and avoid overheating.
Step 6: Add Filler Metal
As you move your torch along the joint, add filler metal as needed to create a continuous weld. It’s crucial to keep the welding rod at an angle and touching the top of the puddle.
You can also use a foot pedal or amperage control to adjust the heat as necessary. Make sure not to overheat or underheat, as this can result in poor weld quality. Otherwise, continue to move the torch and add filler metal until you reach the end of your project.
Step 7: Clean Up Your Welds
Once you’ve finished welding, let your project cool for a few minutes before cleaning up the welds. Use a wire brush to remove any excess filler metal and smooth out the surface of your weld.
You can also use sandpaper or a grinder to create a more refined finish. You can also use a weld cleaner to remove any discoloration from the heat. But be careful not to overdo it, as too much cleaning can weaken the weld.
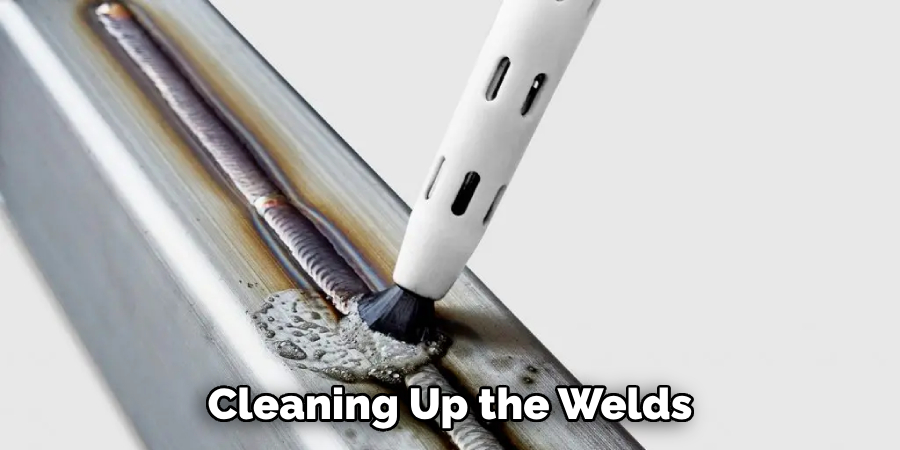
Step 8: Inspect Your Welds
Take a close look at your welds to ensure they are clean, smooth, and free of any defects. If needed, you can revisit the previous steps to fix any issues. You can also use dye penetrant or X-ray testing to check for any hidden defects. It’s essential to have strong and clean welds, especially if you’re working on structural projects. It’s better to take the time to fix any mistakes now than to have problems later.
Step 9: Remove Oxidation with an Etching Solution
Aluminum can develop an unsightly white coating after welding due to oxidation. To remove this, you can use a commercial etching solution designed for aluminum or make your own using citric acid and water. Follow the instructions carefully, and then rinse off the solution with clean water. It’s essential to remove this oxidation, as it can weaken the weld over time. But be sure to wear proper protective gear when handling any chemicals.
Step 10: Practice Makes Perfect
The key to becoming an expert tig welder is practice. Don’t be discouraged if your first few attempts don’t turn out as expected. Keep practicing, and you’ll soon develop the necessary skills to create clean and precise welds. Otherwise, keep referring back to this tutorial for tips and tricks along the way. You can also seek guidance from experienced welders or join a welding course to improve your skills.
Step 11: Safety First
Always remember to prioritize safety when working with welding equipment. Wear appropriate protective gear, work in a well-ventilated area, and exercise caution at all times. Never touch hot metal or operate machinery if you feel tired or unwell. Always follow safety guidelines and seek professional training if needed. It’s better to be safe than sorry.
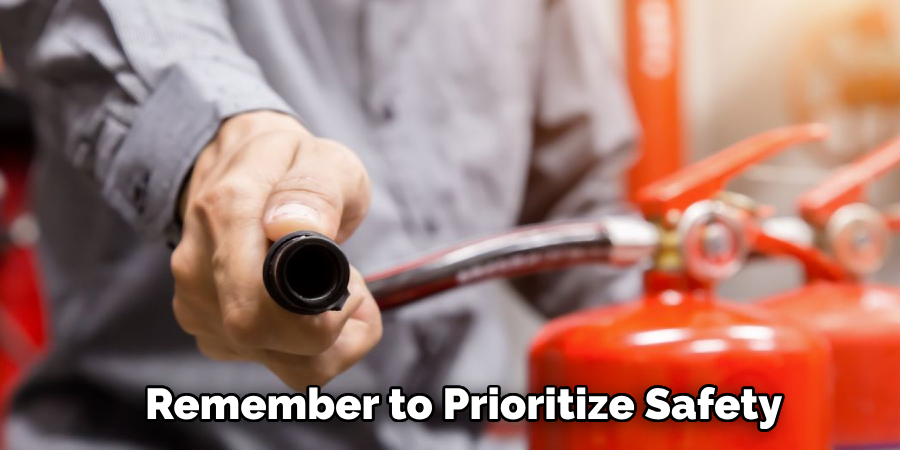
Following these step-by-step guidelines on how to tig weld aluminum for beginners , you’ll be well on your way to mastering the art of tig welding aluminum. With practice and proper technique, you can achieve high-quality welds that will impress even the most experienced welders.
So don’t be afraid to dive in and start your own tig welding journey! The process may seem intimidating at first, but with patience and determination, you’ll soon become a skilled tig welder. Remember to always prioritize safety, practice regularly, and have fun with it. Happy welding! End o
Frequently Asked Questions
Q: What Type of Electrode Should I Use for Tig Welding Aluminum?
A: You can use a 2% thoriated tungsten electrode or any other pure tungsten electrode with a pointed tip. It’s recommended to have a dedicated tungsten electrode for aluminum welding to avoid contamination.
Q: Can I Tig Weld Aluminum with AC or DC?
A: It’s possible to use both AC and DC current for tig welding aluminum. However, most professionals prefer using AC, as it provides better heat control and cleaner welds.
Q: How Thick Aluminum Can I Weld with Tig?
A: With the right equipment and technique, you can weld aluminum of any thickness. However, it’s recommended to start with thinner pieces (around 1/16 inch) and gradually work your way up to thicker material.
Q: Can I Use Flux When Tig Welding Aluminum?
A: No, flux is not necessary when tig welding aluminum. The welding process produces a shielding gas that protects the weld from oxidation, eliminating the need for flux.
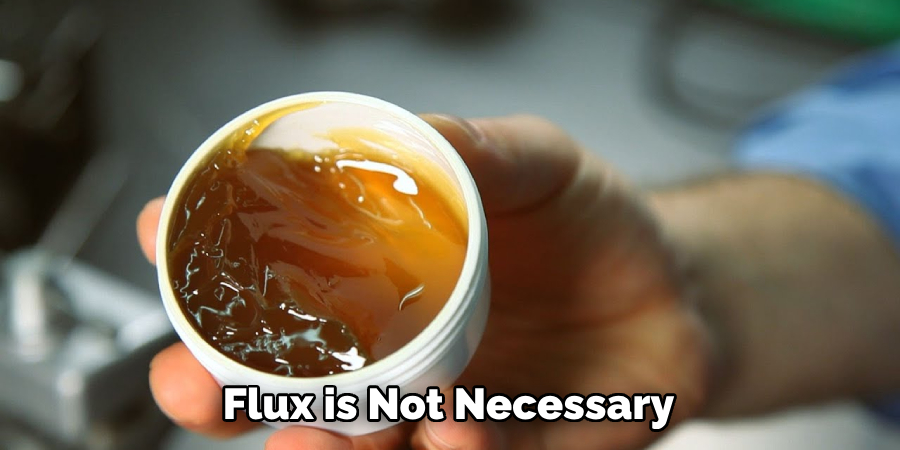
Conclusion
To wrap it up on how to tig weld aluminum for beginners, tig welding aluminum is an ultimately rewarding experience that requires patience and an understanding of the basic principles. With a bit of practice, tig welding aluminum can become second nature before you know it.
For those who have the correct equipment, including electrodes, gas sources, and power sources for welding aluminum—along with proper safety gear—you will soon understand that tig welding does not require as much strength as many think; it really comes down to precision and accuracy.
The guidance of a skilled teacher helps too—so if you are looking to learn more, take classes or attend workshops that teach tig welding techniques specifically on aluminum alloys! Afterward, you’ll wonder why you didn’t try tig welding sooner. Go forth now and apply your newfound knowledge—weld away!
Edmund Sumlin is a skilled author for Metal Fixes, bringing 6 years of expertise in crafting a wide range of metal fixtures. With a strong background in metalwork, Edmund’s knowledge spans various types of fixtures, from decorative pieces to functional hardware, blending precision with creativity. His passion for metalworking and design has made him a trusted resource in the industry.
Professional Focus:
- Expert in Metal Fixtures : Edmund aesthetic specializes in creating durable and innovative metal fixtures, offering both appeal and functionality. His work reflects a deep understanding of metalworking techniques and materials.
- Sustainability Advocate : He is dedicated to using sustainable practices, ensuring that every fixture is crafted with eco-friendly methods while maintaining high-quality standards.
In his writing for Metal Fixes, Edmund provides valuable insights into the latest trends, techniques, and practical advice for those passionate about metal fixtures, whether they are professionals or DIY enthusiasts. His focus on combining artistry with engineering helps others discover the true potential of metal in design.