Are you seeking a reliable welding method with excellent energy efficiency and cost savings? If so, argon gas welding is one option that should be on your radar. With its high power levels and near-perfect welds, argon gas welding offers advantages over other types of arc welding techniques, making it an ideal choice for use in production line applications or for smaller craft projects.
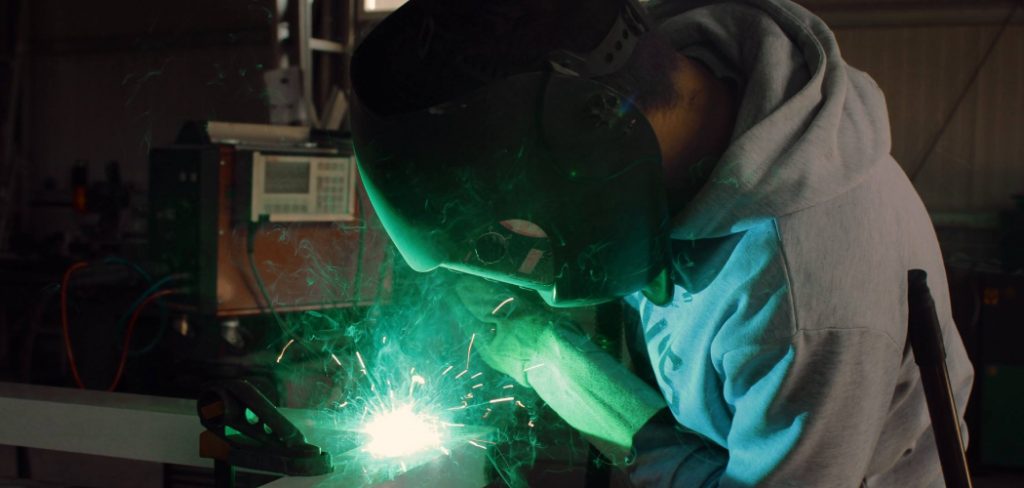
Argon gas welding, also known as gas tungsten arc welding (GTAW), is a process that involves using an electric arc between a non-consumable tungsten electrode and the workpiece. An inert shielding gas, such as argon or helium, protects the weld area from atmospheric contamination.
In this blog post, we’ll explore the basics of how to use argon gas welding – from what it is and how to use it correctly to maximizing safety during the process.
What Will You Need?
Before you can start using argon gas welding, it’s important to make sure you have all the necessary equipment and materials. Here are the basics:
- Argon gas tank
- Welder with appropriate amperage and voltage settings
- Gas regulator
- Tungsten electrode (usually 2% thoriated)
- Filler metal (if needed)
- Protective gear (gloves, helmet, goggles, etc.)
Now that you have all the necessary materials and equipment let’s dive into the process of using argon gas welding.
9 Easy Steps on How to Use Argon Gas Welding
Step 1: Safety First
Before you begin any welding process, you must prioritize safety. Ensure you’re wearing all of your protective gear – this includes gloves, a helmet with an appropriately shaded lens, safety glasses, and a flame-resistant jacket or apron. Ensure your workspace is well-ventilated, clear of any flammable materials, and has an accessible fire extinguisher. Safety should always be paramount when engaging in argon gas welding.
Step 2: Prepare Your Welder
The next step in the process is to set up your welder. Connect your argon gas tank to the welder using the gas regulator. Make sure the regulator is adequately secured to avoid any gas leaks. Insert the tungsten electrode into the torch and adjust the amperage on your welder according to the thickness of the material you will be welding.
As a general rule, use one amp for every thousandth of an inch. Always refer to the manufacturer’s manual for specific settings. Once you have the welder set up, you are ready to begin the argon gas welding process.
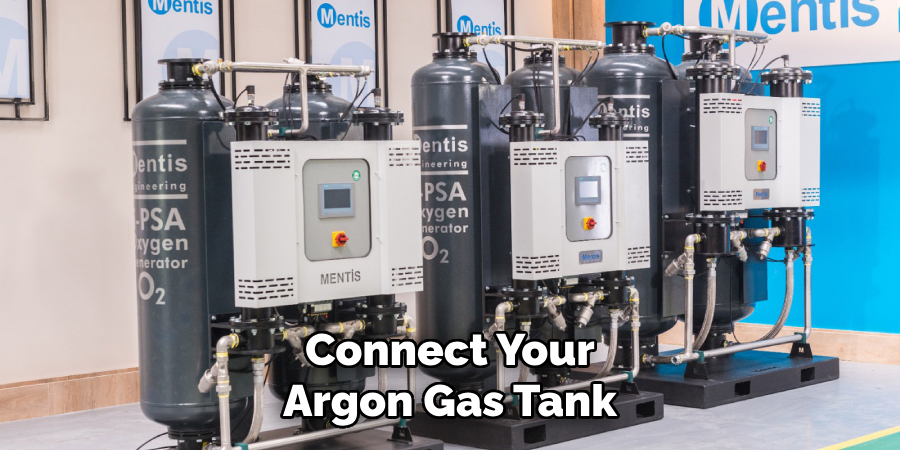
Step 3: Ignite the Arc
With your welder prepared and safety measures in place, you’re now ready to start the actual welding process. Initiate the arc by striking the tungsten electrode against the workpiece, much like striking a match, then quickly pulling it back to maintain a small gap.
The electric current will jump from the electrode to the workpiece, creating a high-temperature arc that melts the metal. Ensure that the arc is stable before proceeding to the next step. This might require a bit of practice if you’re new to argon gas welding.
Step 4: Start the Weld
Once the arc is stable, you can begin the welding process. Hold the torch in one hand and the filler metal in the other. Slowly feed the filler metal into the arc, creating a molten pool on the workpiece. Move the torch along the joint line consistently, ensuring that the molten pool remains at a constant size.
This will create a smooth and even weld seam. Remember to maintain a short and consistent distance between the torch and the workpiece to avoid overheating or underheating.
Step 5: Control the Heat
Controlling heat is a critical aspect of mastering argon gas welding. You can manage the heat input by adjusting the distance between the torch and the workpiece and the speed at which you’re moving the torch. If the weld pool appears too large or too small, you may need to adjust the amperage on your welder.
It’s important to remember that too much heat can lead to warping or burn-through, while too little can result in an incomplete weld. Therefore, finding the right balance is key to achieving a solid, high-quality weld.
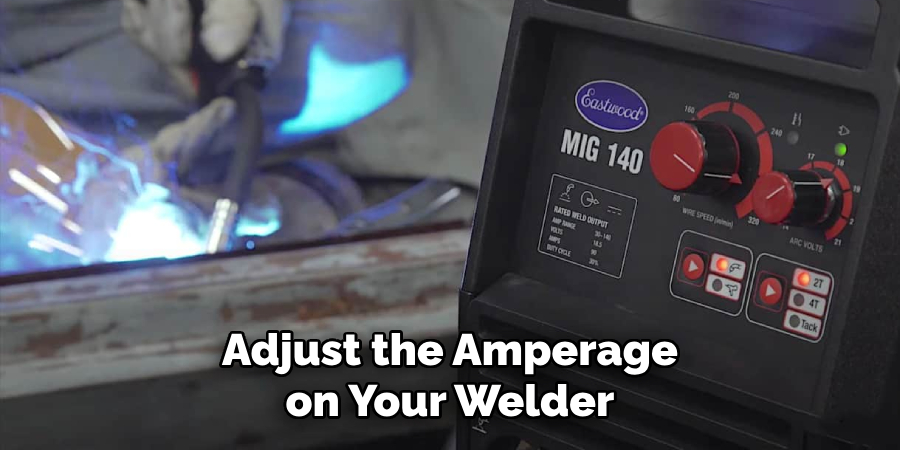
Step 6: Finish the Weld
As you near the weld’s end, slowly pull the torch away from the workpiece, reducing the heat input and allowing the weld pool to solidify. Once you’ve completed the weld, it’s essential to shield the work area with argon gas for a few more seconds to prevent oxidation.
After this, you can safely extinguish the arc by slowly pulling the torch away from the workpiece. Inspect your weld for any inconsistencies or defects. If you’re satisfied with the result, let the piece cool down before proceeding to post-welding operations.
Step 7: Post-Weld Clean-up
After the weld has completely cooled, you can begin the post-weld clean-up. Use a wire brush to remove residual slag or oxidation from the weld surface. This ensures that your weld is clean, which is essential for your workpiece’s aesthetic and structural integrity. Remember to wear your protective gear during this process to prevent any injury from flying debris.
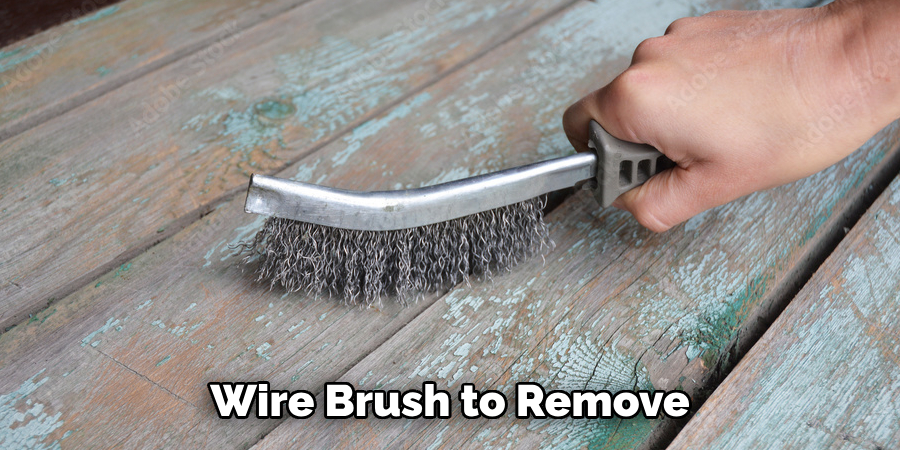
Step 8: Evaluate the Weld
Once you’ve cleaned up the weld, it’s time to evaluate the quality of your work. Look for defects such as cracks, porosity, or lack of fusion. An ideal weld should be smooth and even, with no obvious defects. You may need to grind down the weld and repeat the process if you notice any inconsistencies or issues.
Remember, achieving a high-quality weld requires practice and patience, so keep going even if you don’t get it perfect on the first try. It’s all part of the learning process when figuring out how to use argon gas welding.
Step 9: Practice, Practice, Practice
Argon gas welding is a skill that improves with practice. Don’t be disheartened if your first few attempts don’t yield perfect results. Try welding on scrap metal pieces first to hone your control over the heat and the filler metal feeding. Practice different welding positions and different material thicknesses to get a feel for how the process changes.
As with any skill, consistent practice and patience are the keys to mastering argon gas welding. Remember, everyone starts somewhere, and you’ll become proficient at it with enough time and dedication.
By following these nine easy steps, you can effectively use argon gas welding techniques for a wide range of welding projects.
5 Additional Tips and Tricks
- Proper Ventilation: Always ensure your workspace is well-ventilated. Argon gas is odorless and colorless, so a lack of proper ventilation can lead to a buildup without you noticing.
- Use the Right Equipment: Make sure you use a Tungsten Inert Gas (TIG) welder when working with argon, as this is the most appropriate equipment for such a task.
- Correct Gas Flow Rates: Adjusting your gas flow rate correctly is crucial. Too much flow can lead to turbulence, while too little can expose the weld to the atmosphere. Aim for a rate between 10-20 cubic feet per hour (CFH).
- Clean Your Materials: Argon gas welding works best with clean materials. Before beginning the process, eliminate any rust, dirt, or oil on your welding materials.
- Keep Your Gas Lines Clear: Make sure your gas lines have no kinks or obstructions. This can disrupt the argon gas flow and affect your welds’ quality.
Using argon gas welding may seem intimidating at first, but with practice and following these tips, you’ll soon become a pro.
5 Things You Should Avoid
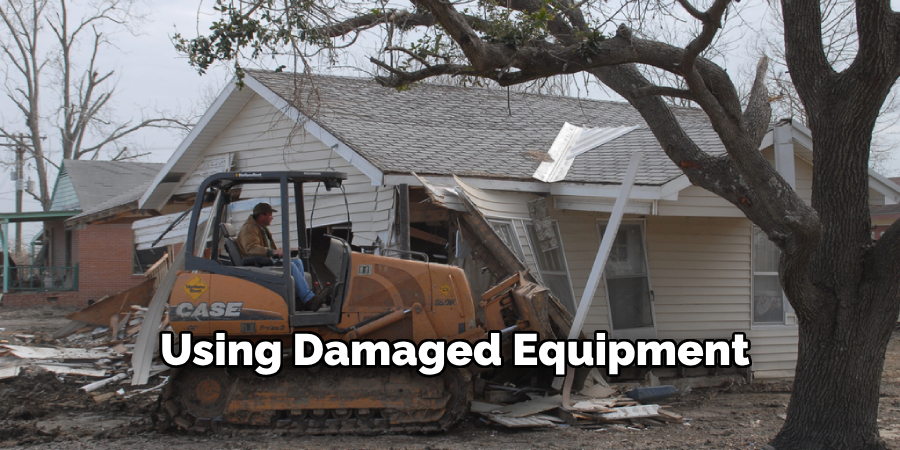
- Avoid Inadequate Safety Measures: Never compromise safety when using argon gas welding. Always wear appropriate protective gear such as welding helmets, gloves, and flame-resistant jackets.
- Avoid Using Damaged Equipment: Check your equipment regularly for faults or damage. Using damaged equipment can lead to poor quality welds and potential safety hazards.
- Avoid Rushing the Process: Quality welding requires patience. Rushing through the process can result in strong welds and consistency in your work.
- Avoid Ignoring the Manufacturer’s Instructions: Each welding machine and equipment comes with its specific manufacturer’s instructions. Ignoring these can lead to misuse of the equipment and poor welding results.
- Avoid Welding in Poorly Lit Areas: Good lighting is essential for precision in welding. Always ensure your workspace is adequately lit to avoid errors and potential accidents.
Avoiding these mistakes can ensure a safe and efficient argon gas welding process. Remember always to prioritize safety and follow the instructions provided by the manufacturer for the best results.
Conclusion
We’ve reviewed the basics of argon gas welding in this blog post, and hopefully, you will now feel more confident about using it on your next project. Remember always to wear protective gear when welding, as well as make sure your workspace is well-ventilated.
While trying something new can be intimidating, with a few practice runs, you’ll be an argon gas welding pro. Even if you don’t have an upcoming project that requires it, knowledge is power – so grab your tools and become familiar with this excellent welding method.
Hopefully, the article on how to use argon gas welding has provided you with the necessary information and tips to get started. Keep practicing and honing your skills, and soon, you’ll be able to tackle any welding project confidently!
Edmund Sumlin is a skilled author for Metal Fixes, bringing 6 years of expertise in crafting a wide range of metal fixtures. With a strong background in metalwork, Edmund’s knowledge spans various types of fixtures, from decorative pieces to functional hardware, blending precision with creativity. His passion for metalworking and design has made him a trusted resource in the industry.
Professional Focus:
- Expert in Metal Fixtures : Edmund aesthetic specializes in creating durable and innovative metal fixtures, offering both appeal and functionality. His work reflects a deep understanding of metalworking techniques and materials.
- Sustainability Advocate : He is dedicated to using sustainable practices, ensuring that every fixture is crafted with eco-friendly methods while maintaining high-quality standards.
In his writing for Metal Fixes, Edmund provides valuable insights into the latest trends, techniques, and practical advice for those passionate about metal fixtures, whether they are professionals or DIY enthusiasts. His focus on combining artistry with engineering helps others discover the true potential of metal in design.