Self-tapping bolts are specialized fasteners designed to create their own threads as they are driven into materials, making them essential for quick and efficient assembly.
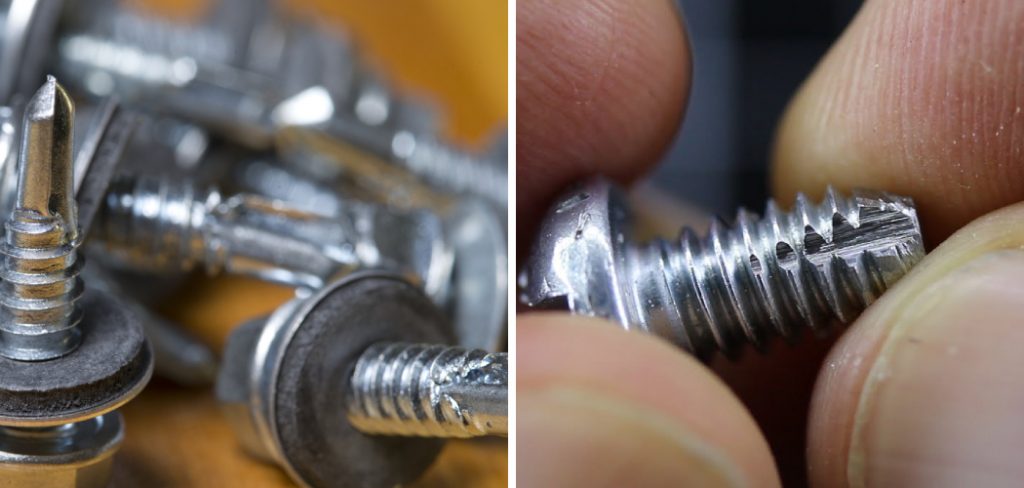
These bolts come in two main types: thread-cutting, which removes material to form threads, and thread-forming, which reshapes the material to create threads.
Typically used in applications involving metal, plastic, and wood, self-tapping bolts are prevalent in automotive, construction, and DIY projects due to their ability to create strong and secure joints without needing pre-tapped holes. Understanding how to use self tapping bolts is crucial for achieving durable and reliable connections in various materials.
This article will guide you through the steps of preparing the material, drilling pilot holes, inserting the bolts, using lubricant if necessary, and securing the joint. By following these steps meticulously, you can ensure your projects’ successful and robust assembly.
Understanding Self-Tapping Bolts
Self-tapping bolts are unique fasteners that have the ability to create or form their own threads as they are driven into materials.
They come in two primary types: thread-cutting and thread-forming. Thread-cutting bolts have cutting edges that remove material to form threads, making them suitable for harder materials like metals.
On the other hand, thread-forming bolts displace the material to create threads, which is ideal for softer substrates such as plastic and softer metals. Both types eliminate the need for pre-tapped holes, simplifying and speeding up assembly processes.
In terms of applications, self-tapping bolts are widely used across various industries. In the automotive sector, they are indispensable for assembling different vehicle components.
In construction, these bolts are favored for joining metal frameworks, roofing, and cladding. Due to their versatility and ease of use, DIY enthusiasts often employ self-tapping bolts for home projects.
The benefits of using self-tapping bolts extend beyond convenience. They provide strong and secure threading in materials, ensuring durability and stability. Additionally, they reduce the risk of thread stripping and offer a tight fit, which is crucial for the integrity of assembled structures.
Understanding these bolts’ characteristics and applications is essential for effective and reliable material joining.
Tools and Materials Needed
To ensure a successful and efficient assembly, it’s crucial to have the proper tools and materials when working with self-tapping bolts. Here’s a comprehensive list of the essentials you’ll need:
Tools:
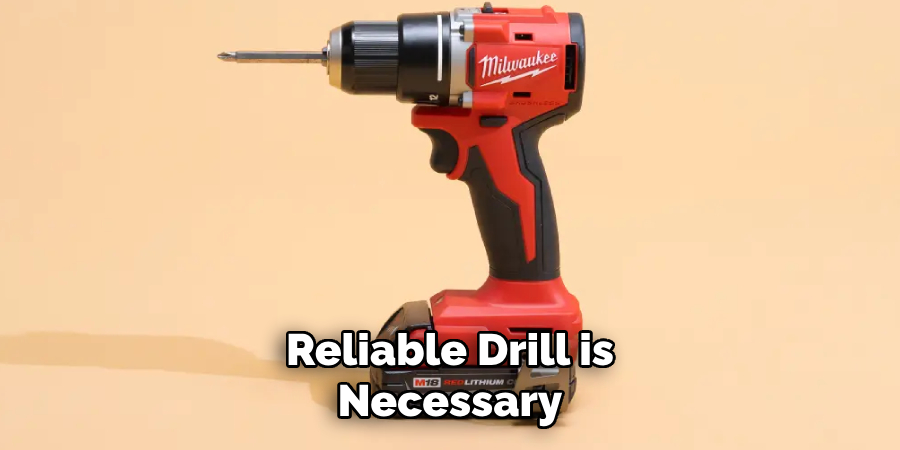
- Drill: A reliable drill is necessary for creating the pilot holes in your material, which will facilitate the insertion of the self-tapping bolts.
- Appropriate Drill Bits: Ensure you have drill bits that match the size requirements for your pilot holes, typically slightly smaller than the bolt diameter.
- Screwdriver or Wrench: Depending on the type of self-tapping bolts you’re using, a screwdriver or wrench will be necessary for driving and securing the bolts.
- Measuring Tape: Accurate measurements are crucial for precise hole placement, so a measuring tape is necessary.
- Marker: Use a marker to clearly indicate the spots where the holes will be drilled, ensuring consistency and accuracy.
Materials:
- Self-Tapping Bolts: Select the appropriate self-tapping bolts for your project in terms of size and type (thread-cutting or thread-forming).
- Materials to be Joined: Prepare the specific materials you intend to join, such as metal, plastic, or wood.
Optional:
- Lubricant for Metal Applications: Applying lubricant to the self-tapping bolts can make the insertion process smoother, especially when working with metal. This reduces friction and heat, enhancing the longevity and performance of the bolts and materials.
Having these tools and materials readily available will streamline the assembly process and ensure strong, secure joints when using self-tapping bolts.
Preparing the Material
Proper preparation of the materials is a critical step in ensuring a successful assembly with self-tapping bolts. Begin by measuring and marking the spots where the bolts will be inserted.
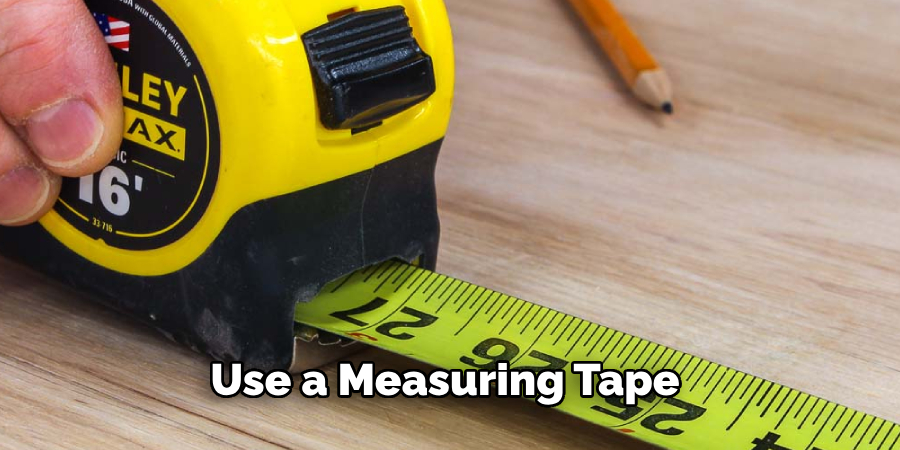
Use a measuring tape for precise measurements and a marker to indicate the drilling points clearly. Accuracy at this stage is vital; even slight misalignments can weaken the joint and compromise the integrity of the assembled pieces.
Next, align the materials to ensure they fit together tightly and correctly. Place the pieces in the intended final position and check the alignment against your markings. Misalignment can lead to an inefficient joint and may even cause the material to split or the bolts to strip.
Before proceeding, carefully inspect the materials for any defects or imperfections that could affect the joint. Look for cracks, chips, or other damages around the marked spots. Defective materials can lead to weak points in the joint, reducing your assembly’s overall strength and durability.
If any issues are found, address them by replacing the damaged sections or reinforcing weak areas to avoid compromising the quality of the final product.
By meticulously preparing the materials, you set the foundation for a robust and durable connection, ensuring success in your assembly endeavors.
Drilling Pilot Holes
Drilling pilot holes is a key step when using self-tapping bolts. It ensures that the bolts can be driven smoothly and create strong threads. The success of this process hinges on selecting the correct drill bit size and executing precise drilling techniques.
Selecting the Correct Drill Bit Size
The drill bit used for creating pilot holes should generally be slightly smaller than the diameter of the self-tapping bolt. This allows the bolt to bite into the material and form or cut threads effectively.
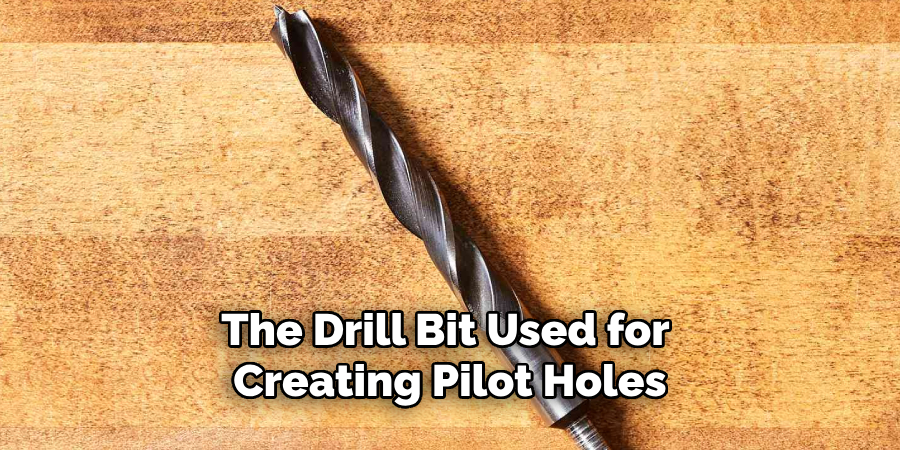
For example, if you’re using a 1/4-inch self-tapping bolt, a 3/16-inch drill bit might be appropriate. It’s always a good idea to refer to the manufacturer’s recommendations for the exact drill bit size, as this can vary depending on the material and type of bolt.
Drilling Pilot Holes
Once you’ve selected the correct drill bit, it’s time to drill the pilot holes. Attach the drill bit to your drill and ensure that it is securely fastened. Position the drill at the designated marking, keeping it perpendicular to the material’s surface. Drilling straight and accurate holes is crucial to avoid misalignment, which could compromise the joint’s integrity.
Drill steadily to the required depth, ensuring you do not go too shallow or too deep. This depth is typically just shorter than the length of the self-tapping bolt to allow the bolt to engage fully and securely within the material.
Importance of Accuracy
The straightness and accuracy of the pilot holes are vital for a secure fit. Angled or misaligned holes can lead to uneven stress distribution when the bolts are inserted, potentially causing the material to crack or the bolt to strip its threads.
By paying close attention to drill bit selection and drilling technique, you can create pilot holes that facilitate the smooth insertion of self-tapping bolts and ensure a strong, durable connection in your assembly projects.
How to Use Self Tapping Bolts: Inserting the Self-Tapping Bolts
01.Aligning the Self-Tapping Bolt with the Pilot Hole
Once the pilot holes are drilled, inserting the self-tapping bolts is time. Begin by aligning the bolt with the pilot hole, ensuring that it is perfectly centered. Misalignment at this stage can lead to uneven thread formation and potentially compromise the joint’s strength.
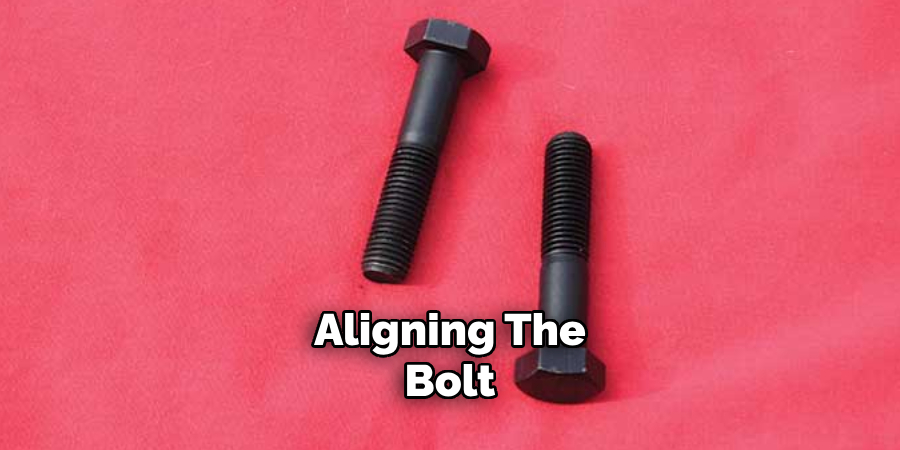
Hold the bolt steady and perpendicular to the material’s surface to achieve a smooth and precise insertion.
02.Applying Consistent Pressure and Using a Screwdriver or Wrench
Start the insertion process by applying consistent pressure to the bolt. Depending on the type of head on your self-tapping bolt, use a screwdriver or wrench to begin turning it into the pilot hole.
Maintaining a steady and even pressure is essential to allow the bolt to bite into the material and start forming or cutting threads. Avoid sudden or jerky movements, which can misalign the bolt or damage the pilot hole.
03.Ensuring the Bolt Cuts or Forms Threads as It Is Driven Into the Material
As you turn the bolt, it will start cutting or forming threads within the pilot hole. This is a critical phase, as the threads provide the bolt with the necessary grip to hold the materials together securely.
Ensure that the bolt progresses smoothly and the threads form evenly. If you encounter resistance, it might be helpful to back the bolt out slightly and then continue driving it in to clean out any debris and ensure proper thread formation.
04.Avoiding Overtightening to Prevent Stripping or Damaging the Threads
It’s important to avoid overtightening the bolt once it is fully seated. Overtightening can strip the threads that have been formed, reducing the bolt’s holding power and potentially damaging the material.
Once the bolt is snug and the materials are securely joined, stop turning to prevent unnecessary stress on the joint. By carefully inserting the self-tapping bolts and avoiding overtightening, you can ensure a strong, durable connection that will stand the test of time.
Using Lubricant
Applying Lubricant to the Self-Tapping Bolt for Easier Insertion
Applying a lubricant to the self-tapping bolt is optional but can be particularly beneficial when working with metal materials. Lubricants such as machine oil, grease, or specialty thread lubricants can be applied to the bolt’s threads before insertion.
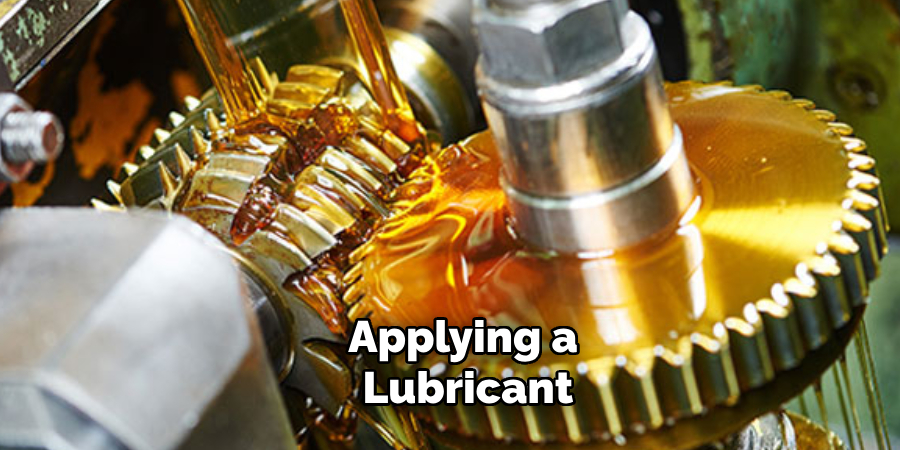
This reduces the torque required to drive the bolt into the material, making the insertion process smoother and less labor-intensive.
Reducing Friction and Heat Generation During the Threading Process
One of the primary advantages of using a lubricant is reducing friction between the bolt and the material. High friction can generate significant heat, which may make the threading process more difficult and weaken both the bolt and the material through thermal expansion and contraction.
By minimizing friction, lubricant helps maintain the structural integrity of your assembly.
Enhancing the Longevity and Performance of the Bolt and Material
Lubricants serve another crucial function by preventing potential galling (a form of wear caused by adhesion) and reducing the corrosion rate. This is especially important in harsh environments where the assembly might be exposed to moisture or chemicals
. By providing a corrosion-resistant barrier and ensuring that the threading process is as smooth as possible, lubricants can extend the lifespan and improve the overall performance of both the bolt and the material.
Thus, incorporating lubricants into your assembly practice can significantly enhance the durability and reliability of the final product.
Securing the Joint
Checking the Alignment and Tightness of the Joint
After the self-tapping bolts are inserted, it is crucial to check the alignment and tightness of the joint. Ensure all components are properly aligned and the joint sections flush against each other.
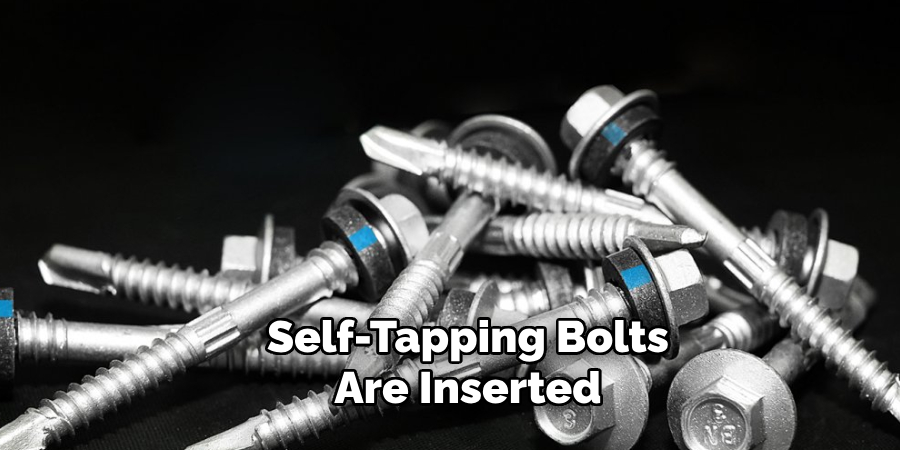
A misaligned joint can lead to structural weaknesses and potential failure of the assembly. Use a torque wrench or manual inspection to verify that each bolt is tightened adequately without causing undue stress to the material.
Using Additional Washers or Nuts if Necessary for Extra Security
Consider using washers or nuts for applications requiring additional security. Flat washers can help distribute the load evenly, preventing the bolt head from embedding into the material and reducing the risk of loosening over time.
On the other hand, lock washers provide an anti-vibration function by maintaining tension. In some cases, using a nut in combination with a self-tapping bolt can offer extra stability, particularly in high-stress or high-vibration environments.
Ensuring the Bolt Head is Flush with or Slightly Above the Material Surface
To achieve a professional and secure finish, ensure the heads of the self-tapping bolts are flush with or slightly above the material surface. A flush or slightly raised bolt head ensures that the bolt is fully seated and provides maximal holding power without over-penetrating the material.
This attention to detail prevents surface damage and contributes to the overall integrity and appearance of the finished assembly.
Tips for Successful Use
Ensuring Accurate Measurements and Drilling for Strong Joints
Accurate measurements are the foundation of a strong joint. Double-check dimensions and mark the pilot hole locations precisely. Using a center punch can help prevent the drill bit from wandering.
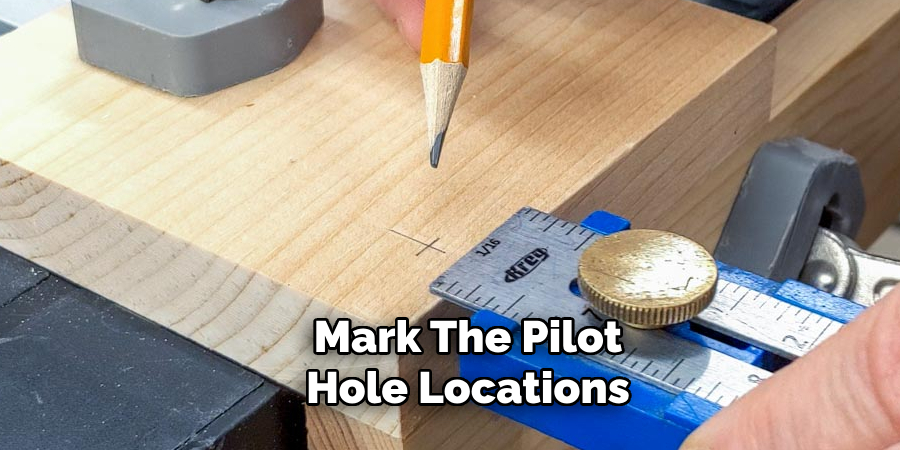
For best results, ensure the pilot holes are correctly sized and drilled perpendicular to the material’s surface, minimizing the risk of misalignment.
Using Quality Self-Tapping Bolts and Tools to Avoid Stripping or Breakage
Investing in high-quality self-tapping bolts and appropriate tools is essential. Quality bolts are less likely to strip or break under torque. Use tools designed for self-tapping bolts, such as drills with torque settings, to ensure controlled insertion and reduce the likelihood of damaging the bolt or material.
Practicing on Scrap Material to Perfect Technique Before the Final Project
Before tackling your main project, practice using scrap material. This allows you to perfect your technique, test your tools, and make any necessary adjustments. Practicing helps build confidence and ensures a flawless execution when working on the final assembly.
Common Mistakes to Avoid
Not Drilling Pilot Holes Deep Enough, Causing Material Splitting
One frequent error is failing to drill pilot holes to the appropriate depth. Shallow pilot holes can cause the material to split when the self-tapping bolt is inserted, compromising the assembly’s integrity.
Ensure pilot holes are deep enough to accommodate the entire bolt length without undue resistance.
Misaligning the Materials, Resulting in Weak Joints
Misaligned materials during assembly can lead to weak joints and structural instability. This often occurs when components are not properly clamped or marked before drilling. Always verify the alignment before fastening to ensure a robust and secure connection.
Over-Tightening the Self-Tapping Bolts, Leading to Stripped Threads
Overtightening self-tapping bolts is another common mistake that can strip threads and weaken the joint. Once the bolt is secure and the materials are tightly joined, stop tightening to avoid damaging the threads and reducing the bolt’s holding power.
Conclusion
Successfully learning how to use self tapping bolts involves a series of meticulous steps that ensure reliability and durability. Begin by accurately measuring and marking the pilot hole locations, and ensure these holes are properly sized and drilled perpendicularly to the material’s surface.
Utilize high-quality bolts and tools to prevent stripping or breakage, and check for alignment and tightness after inserting the bolts. Additional washers or nuts may be required for extra security, especially in high-stress scenarios.
Finally, ensure the bolt heads are flush with or slightly above the material surface to maintain a professional finish. Precision and proper technique are paramount in achieving strong, durable joints.
Practicing on scrap material will build your confidence and hone your skills, ensuring that your final project is flawlessly executed. By adhering to these guidelines and understanding how to use self tapping bolts correctly, you can achieve superior results in your assembly projects.
Edmund Sumlin is a skilled author for Metal Fixes, bringing 6 years of expertise in crafting a wide range of metal fixtures. With a strong background in metalwork, Edmund’s knowledge spans various types of fixtures, from decorative pieces to functional hardware, blending precision with creativity. His passion for metalworking and design has made him a trusted resource in the industry.
Professional Focus:
- Expert in Metal Fixtures : Edmund aesthetic specializes in creating durable and innovative metal fixtures, offering both appeal and functionality. His work reflects a deep understanding of metalworking techniques and materials.
- Sustainability Advocate : He is dedicated to using sustainable practices, ensuring that every fixture is crafted with eco-friendly methods while maintaining high-quality standards.
In his writing for Metal Fixes, Edmund provides valuable insights into the latest trends, techniques, and practical advice for those passionate about metal fixtures, whether they are professionals or DIY enthusiasts. His focus on combining artistry with engineering helps others discover the true potential of metal in design.