Do you want to take on a new DIY project that will allow you to keep your vehicle running in top condition? Then welding a catalytic converter is the perfect way to make sure your car stays safe, efficient, and compliant with emissions regulations. Welding a catalytic converter might seem intimidating at first, but it’s actually quite easy once you get the hang of it.
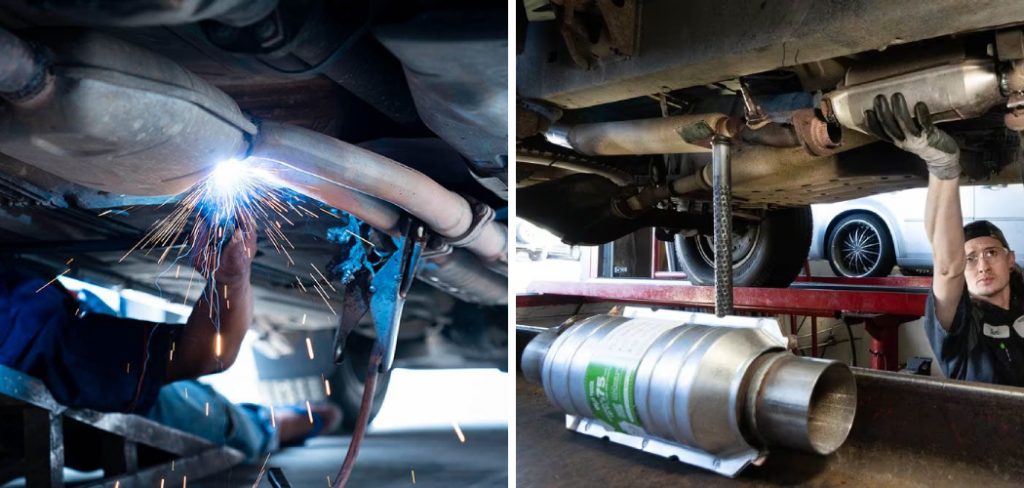
Here we’ll provide step-by-step instructions on how to weld a catalytic converter so that anyone can give this project a try. So grab your safety gear and get ready for an exciting welding adventure!
Tools and Materials You Will Need to Weld a Catalytic Converter
- Oxygen-acetylene or MIG welding equipment
- Welding goggles and gloves
- Safety mask and clothing
- Fire extinguisher
- Jack stands (if you need to remove the converter from your vehicle)
Step-by-step Guidelines on How to Weld a Catalytic Converter
Step 1: Prepare Your Workspace and Equipment
Before starting any welding project, it’s important to set up a safe and comfortable workspace. Make sure your welding equipment is in good working condition and that you have all the necessary tools and materials. It’s also important to have a fire extinguisher nearby, just in case. Preparing your workspace and equipment beforehand will save you time and hassle later on.
Step 2: Remove the Catalytic Converter from Your Vehicle
If your catalytic converter is already damaged and needs to be replaced, you can skip this step. But if it’s still in good condition, then you’ll need to remove it from your vehicle before welding. This can usually be done easily with the help of jack stands. While removing the converter, make sure to keep track of its orientation so that you can reattach it correctly after welding.
Step 3: Clean the Catalytic Converter
Before welding, it’s crucial to clean the surface of the catalytic converter thoroughly. Any grease, oil, or dirt on the surface can prevent a strong weld from forming. Use a wire brush or sandpaper to clean the surface, and then wipe it down with a degreaser. Let it dry completely before moving on to the next step.
Step 4: Heat up and Weld the Catalytic Converter
Now it’s time to fire up your welding equipment! If you’re using an oxygen-acetylene torch, set the flame to a neutral flame with equal amounts of oxygen and acetylene. For MIG welding, make sure to adjust your voltage and wire speed settings according to the thickness of the metal. Once you have a good weld, carefully weld the damaged area of the converter back together. You may need to make multiple passes to create a strong and durable weld.
Step 5: Reinstall the Catalytic Converter
After welding, let the catalytic converter cool down before reinstalling it in your vehicle. Make sure to reattach it correctly based on its orientation. Double-check that all connections are secure and tightened properly. Make sure to also inspect the surrounding area for any potential damage caused by the welding process.
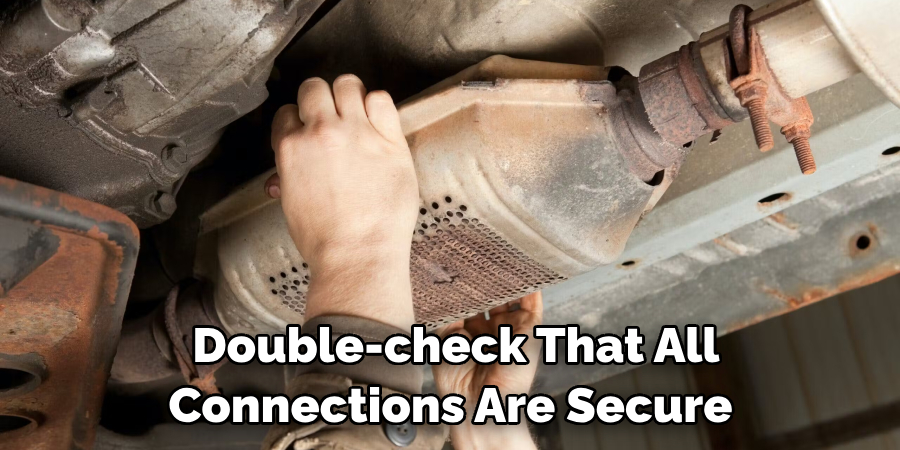
Congrats! You have successfully welded your catalytic converter and saved yourself some money in the process. Remember to always follow safety protocols when welding and take proper precautions to avoid any accidents. With these step-by-step guidelines, you can tackle this project with confidence and keep your vehicle running smoothly. Happy welding!
Additional Tips and Tricks to Weld a Catalytic Converter
- When welding a catalytic converter, always wear protective gear such as gloves and a welding helmet to avoid any accidents or injuries.
- Make sure the area around the catalytic converter is clear of any flammable materials before beginning the welding process. This includes removing any plastic parts or fuel lines that may be near the area.
- Clean the surface of the catalytic converter thoroughly before welding to ensure proper adhesion.
- Start with small tack welds and work your way around the edges of the converter to prevent warping or damaging the delicate inner components.
- Use a low heat setting on your welding torch, as high heat can cause damage to the catalytic converter and affect its performance.
- It’s important to use a specific type of welding rod designed for use with catalytic converters. These rods have a high nickel content and can withstand the extreme heat generated during the welding process.
- Practice proper ventilation when welding a catalytic converter, as harmful fumes may be released during the process. Welding in an open or well-ventilated area is recommended.
- If possible, it’s best to remove the catalytic converter from the vehicle before welding. This will allow for easier access and prevent any damage to other parts of the vehicle.
- After welding, allow the catalytic converter to cool down completely before reinstalling it in the vehicle.
- It’s always a good idea to have a professional inspect your welding work after completing the process, as they can ensure it is done correctly and safely. Overall, welding a catalytic converter requires precision and caution to avoid any potential damage or hazards.
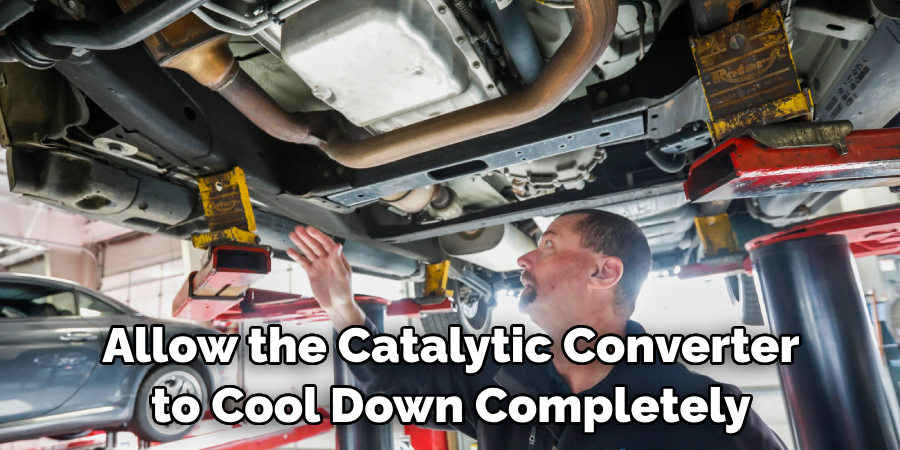
Following these additional tips and tricks will help ensure a successful welding process and extend the lifespan of your catalytic converter. Remember to always follow safety precautions and take your time during the welding process for the best results. Happy welding!
Safety Precautions Need to Be Followed for Welding a Catalytic Converter
- First and foremost, disconnect the car battery so that there is no risk of electrocution. Wearing safety gloves and goggles is also crucial to avoid any burns or eye injuries.
- Make sure that the vehicle is on a flat, stable surface and is securely supported with jack stands to prevent it from falling.
- It is important to have proper ventilation in the work area as welding produces harmful fumes. Work in a well-ventilated area or use an exhaust fan to remove the fumes.
- Before starting the welding process, remove the catalytic converter from the vehicle and clean it thoroughly. Any dirt or debris left on the surface can affect the welding process.
- Keep a fire extinguisher nearby in case of any sparks or accidental fires. It is also recommended to have someone else present while welding, in case of an emergency.
- Ensure that you are using the correct type of welding rod and welding machine for the specific metal of your catalytic converter. Using the wrong equipment can lead to poor-quality welds or even damage the converter.
- When welding, always wear appropriate clothing that covers exposed skin to protect yourself from any sparks or hot metal fragments.
- Take breaks in between welding to inspect the progress and make sure that everything is going smoothly. This will also give the welding machine a chance to cool down and prevent overheating.
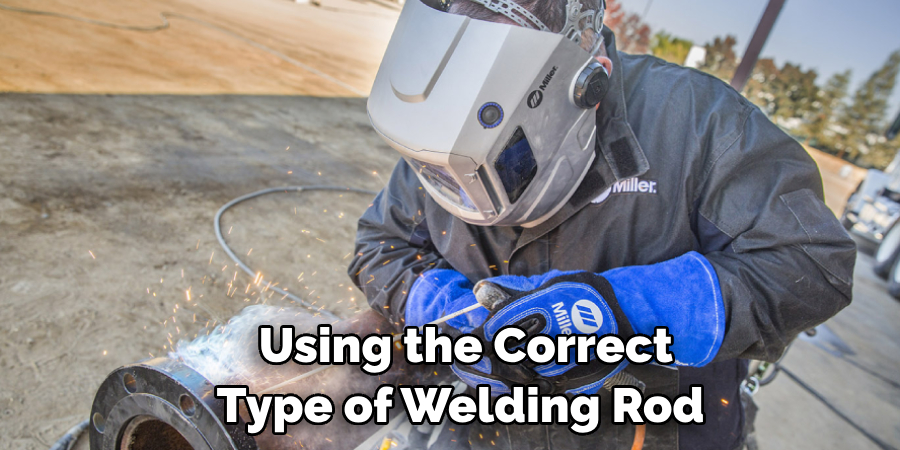
Following these safety precautions is crucial to ensure a successful and safe welding process for your catalytic converter. Remember to always prioritize safety when working with any type of welding equipment.
Frequently Asked Questions
Is It Safe to Weld a Catalytic Converter?
Yes, it is safe to weld a catalytic converter as long as the proper precautions are taken. Welding on a catalytic converter can be hazardous due to the high temperatures and fumes given off during the process. It is important to wear protective gear and work in a well-ventilated area when welding a catalytic converter.
Why Would I Need to Weld a Catalytic Converter?
Welding a catalytic converter is typically done for one of two reasons. The first reason is to repair a damaged or cracked catalytic converter. Welding can be used to seal any holes or cracks in the casing, which will help the converter function properly. The second reason for welding a catalytic converter is to install an aftermarket performance exhaust system. In this case, welding is necessary to attach the new exhaust system to the existing catalytic converter.
Can I Weld a Catalytic Converter Myself?
It is possible to weld a catalytic converter yourself if you have the proper equipment and knowledge of welding techniques. However, it is recommended to seek professional help from a certified mechanic or exhaust specialist. This ensures that the welding is done correctly and safely, as well as complying with any local emissions regulations.
What Type of Welding Method Should I Use?
The most common method for welding a catalytic converter is Tungsten Inert Gas (TIG) welding. This method allows for precise control of the heat and weld penetration, which is important when working on delicate components like a catalytic converter. Other methods such as Metal Inert Gas (MIG) welding can also be used, but may not provide the same level of control and precision.
Are There Any Risks Associated with Welding a Catalytic Converter?
Welding on a catalytic converter does come with some risks, mainly from the high temperatures and fumes produced during the process. Inhaling these fumes can be harmful to your health, so it is important to wear proper protective gear and work in a well-ventilated area. Additionally, if the welding is not done correctly or the correct materials are not used, it can damage the catalytic converter and potentially cause it to fail.
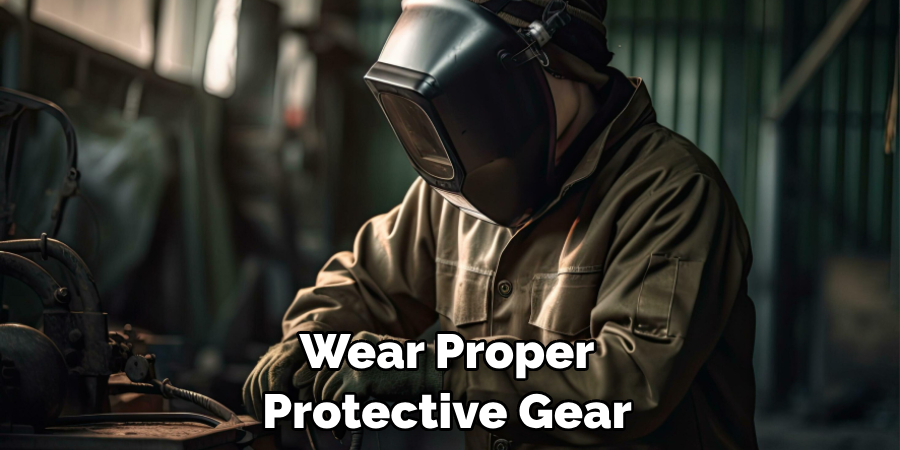
Conclusion
Now you know how to weld a catalytic converter safely and effectively. Whether you need to repair a damaged converter or install an aftermarket exhaust system, welding can be a useful skill to have. However, always remember to take the necessary precautions and seek professional help if needed.
Properly maintained and functioning catalytic converters are important for reducing harmful emissions from your vehicle and protecting the environment. So, it is important to handle them with care and ensure they are in good working condition. Happy welding!
Edmund Sumlin is a skilled author for Metal Fixes, bringing 6 years of expertise in crafting a wide range of metal fixtures. With a strong background in metalwork, Edmund’s knowledge spans various types of fixtures, from decorative pieces to functional hardware, blending precision with creativity. His passion for metalworking and design has made him a trusted resource in the industry.
Professional Focus:
- Expert in Metal Fixtures : Edmund aesthetic specializes in creating durable and innovative metal fixtures, offering both appeal and functionality. His work reflects a deep understanding of metalworking techniques and materials.
- Sustainability Advocate : He is dedicated to using sustainable practices, ensuring that every fixture is crafted with eco-friendly methods while maintaining high-quality standards.
In his writing for Metal Fixes, Edmund provides valuable insights into the latest trends, techniques, and practical advice for those passionate about metal fixtures, whether they are professionals or DIY enthusiasts. His focus on combining artistry with engineering helps others discover the true potential of metal in design.