Are you looking to expand your welding skills and learn how to work with aluminium? While most welders use specialized TIG or MIG equipment for welding this lightweight metal, it is also possible to achieve strong and durable welds using a stick welder.
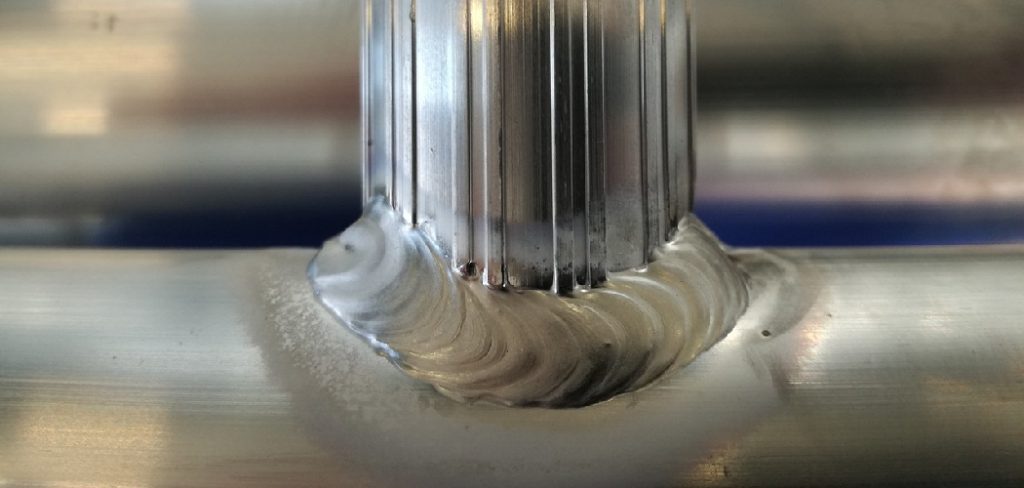
However, the key is to understand the properties of aluminium and adjust your technique accordingly. In this blog post, we will delve into the world of stick welding with aluminium and provide you with all the essential tips and tricks on how to weld aluminium with a stick welder needed to master this technique. Whether you are a beginner or an experienced welder, read on as we share our expert advice on how to create high-quality aluminum welds using just a simple stick welding machine.
Needed Materials
To weld aluminium with a stick welder, you will need the following materials:
- A Stick Welding Machine Capable of at Least 200 Amps.
- Aluminium Electrode Rods (Also Known as “Alumina” or “Cellulose” Type Electrodes)
- Aluminium Filler Metal
- Wire Brush and Grinder for Cleaning and Preparing the Surfaces to Be Welded
- Protective Gear, Including Welding Helmet, Gloves, and Apron
- Aluminium-specific Flux or Rod Oven (Optional)
10 Simple Step-by-step Guidelines on How to Weld Aluminium With a Stick Welder
Step 1: Prepare the Workpiece
The first step to successful stick welding with aluminium is proper preparation. Begin by cleaning the metal surface to be welded using a wire brush or grinder. This will ensure that there are no impurities, such as oils or dirt, on the surface which can negatively affect the weld quality. Next, use acetone or another degreaser to completely remove any remaining contaminants.
Step 2: Select the Right Electrode
Choosing the right electrode is crucial for a successful weld. For aluminium, you will need to use either alumina or cellulose type electrodes, which are specifically designed for this metal.
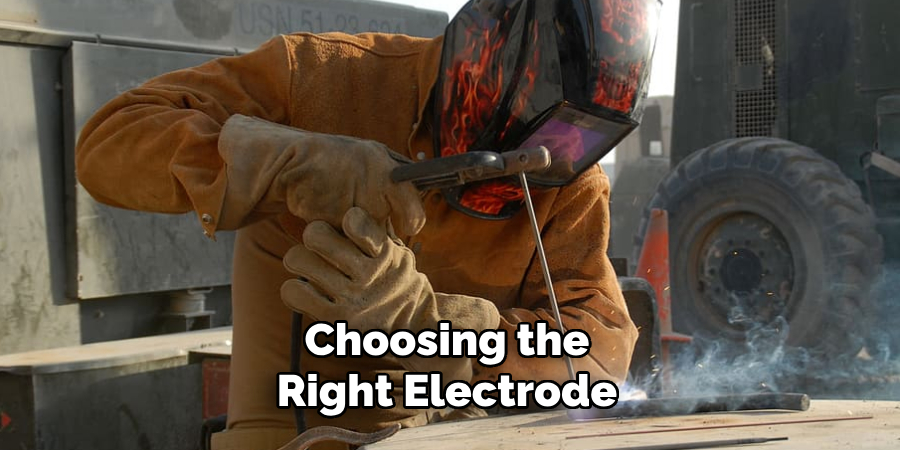
These electrodes have a high amount of potassium and sodium in their flux coating, which helps break down the oxide layer on the surface of aluminium and allows for better weld penetration.
Step 3: Set Up Your Welding Machine
Set your welding machine to DC positive polarity, which will produce a smooth arc and allow you to control the heat input better. The recommended amperage for stick welding with aluminium is at least 200 amps. It is also essential to have a good ground connection and clean cable connections for optimal performance. You may also need to increase the voltage setting for thicker aluminium pieces.
Step 4: Keep Your Electrode Dry
One of the crucial factors when welding aluminium with a stick welder is keeping your electrode dry. Moisture in the flux can cause porosity in the weld, leading to weak spots and potential failure. You can either use an oven specifically made for aluminium rods or store them in a sealed container with a desiccant. The electrodes should be baked at 250 degrees Fahrenheit for about an hour before use.
Step 5: Tack Weld
Start by tack welding the pieces together to secure and align them before making the final weld. This will help prevent warping and ensure a straight and even seam. You can use a copper backing plate behind the weld to further reduce warping, especially for thicker aluminium pieces. The tacks should be no more than 4 inches apart.
Step 6: Strike the Arc
Using proper arc striking techniques is essential when stick welding with aluminium. Instead of dragging or scratching the electrode on the surface, quickly lift and strike it against the workpiece’s edge. This will help create an intense heat in a concentrated area, giving you better control over the weld and reducing the chances of sticking or splattering.
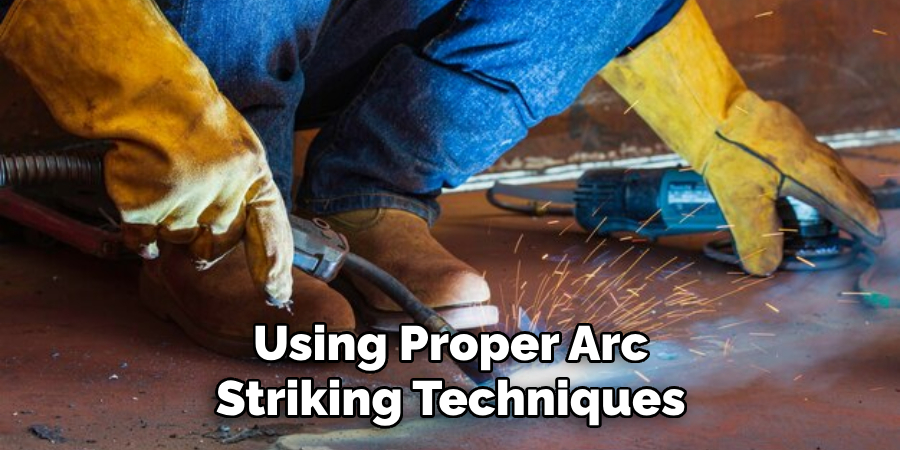
Step 7: Maintain a Short Arc
Unlike welding with steel, where you can use a longer arc length, stick welding with aluminium requires a short arc. This is because aluminium has high thermal conductivity, and too much heat can cause distortion and burn through the metal. Keep the electrode at a 60-degree angle and maintain a distance of about 1/8 inch between the tip of the electrode and the workpiece.
Step 8: Control Your Travel Speed
It is also crucial to control your travel speed when welding aluminium with a stick welder. A slower speed is recommended, as it allows for better penetration and a more consistent weld. However, be careful not to linger in one spot for too long, as this can lead to burn-through. Move in a steady and even motion while maintaining the correct arc length.
Step 9: Use Backhand Technique
The backhand technique is preferred when stick welding with aluminium as it allows better penetration and control over the weld pool. This technique involves pushing the electrode with a slight tilt in the direction of travel. However, if you are more comfortable using forehand or drag techniques, you can still achieve quality welds by adjusting your angle and travel speed accordingly.
Step 10: Clean and Inspect Your Weld
After completing the weld, use a wire brush or grinder to clean off any flux residue and inspect the weld for any defects, such as porosity or cracks. If necessary, you can make additional passes to fill in any gaps or reinforce weak areas. Once satisfied with the weld quality, let it cool down before handling it. You can also perform a dye penetrant test to ensure the weld is free of any defects.
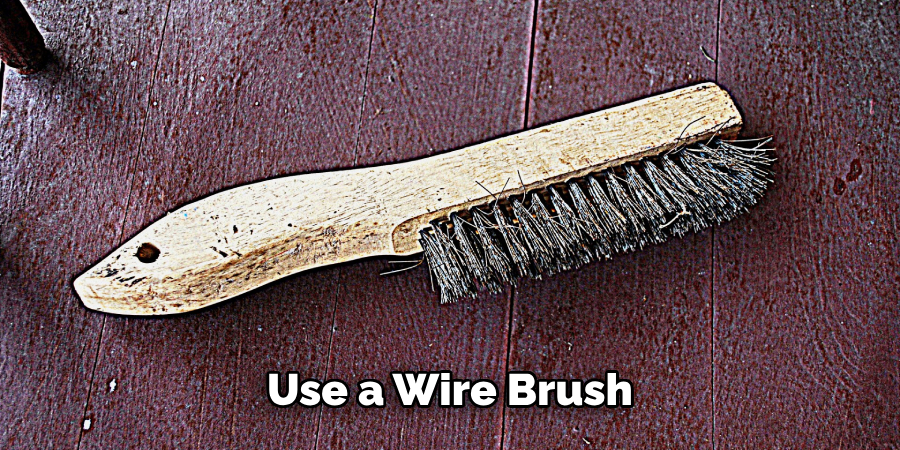
Tips and Tricks for Welding Aluminium With a Stick Welder
- Use Ac Welding Mode if Your Stick Welding Machine Has It Available, as It Provides Better Arc Stability and Reduces the Chances of Sticking.
- Practice on Scrap Pieces of Aluminium Before Attempting a Real Project to Get Comfortable With the Technique.
- Keep a Steady Hand and Maintain Good Posture While Welding to Create Consistent and Strong Welds.
- Use a Larger Diameter Electrode (3/32 or 1/8 Inch) for Thicker Aluminium Pieces, as It Will Provide More Heat Input and Better Penetration.
- Be Mindful of Your Environment When Stick Welding With Aluminium, as Wind or Drafts Can Affect the Weld Quality and Make It More Challenging to Maintain a Short Arc Length.
- Always Wear Proper Protective Gear, Including a Welding Helmet With a Shade Suitable for Aluminium (10 or Higher), Gloves, and an Apron, to Protect Yourself From Harmful Uv Rays and Molten Metal Spatter.
- Preheat Thicker Pieces of Aluminium Before Welding to Improve Penetration and Reduce the Chances of Cracking.
- If You Are Using Cellulose Type Electrodes, Make Sure to Scrape Off the Flux Coating Before Welding to Prevent Contamination and Achieve a Cleaner Weld.
- After Completing the Weld, Allow It to Cool Down Gradually, as Rapid Cooling Can Cause Distortion and Weaken the Metal’s Structure.
- Finally, Make Sure to Also Clean and Maintain Your Stick Welding Machine Regularly to Ensure Optimal Performance and Avoid Any Issues While Welding.
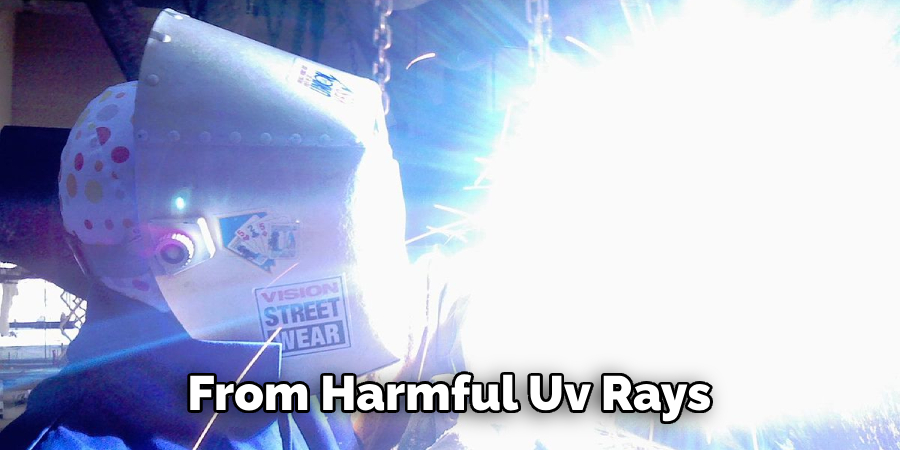
By following these tips and tricks on how to weld aluminium with a stick welder, you can successfully weld aluminium with a stick welder and create strong, durable, and high-quality welds. Remember to always prioritize safety and proper techniques to achieve the best results. Happy welding!
Frequently Asked Questions
Q1: Can I Weld Aluminium With a Regular Stick Welding Machine?
A1: Yes, it is possible to weld aluminium with a standard stick welding machine. However, it requires specific techniques and adjustments for optimal results.
Q2: Can I Weld Different Thicknesses of Aluminium With the Same Electrode?
A2: It is recommended to use different electrode sizes for different thicknesses of aluminium. A larger diameter electrode provides more heat input, which is necessary for thicker pieces, while a smaller diameter may not provide enough heat for proper penetration.
Q3: Why Do I Need to Preheat Aluminium Before Welding?
A3: Preheating helps reduce the chances of cracking and improves penetration for a stronger weld. It is particularly crucial for thicker pieces of aluminium.
Conclusion
In conclusion on how to weld aluminium with a stick welder, learning how to weld aluminum with a stick welder may seem like a daunting task at first, but with the right technique and equipment, it can be accomplished successfully. As we’ve discussed throughout this post, there are several key steps that you need to follow in order to achieve clean and strong welds on aluminum using a stick welder.
From proper preparation and cleaning of the metal to selecting the correct electrode and maintaining the right amperage and speed, each step plays an important role in the overall welding process. It’s also crucial to take safety precautions seriously when working with extreme heat and electricity.
With practice and patience, you’ll be able to master this skill and confidently take on any aluminum welding project. And who knows, it might even become your new favorite welding method!
So don’t be afraid to give it a try and expand your welding repertoire. Let us know in the comments how your aluminum welding journey goes, we’d love to hear about your success stories or any challenges you faced along the way. Remember, practice makes perfect and with determination, you’ll become an aluminum stick welding pro in no time!
Edmund Sumlin is a skilled author for Metal Fixes, bringing 6 years of expertise in crafting a wide range of metal fixtures. With a strong background in metalwork, Edmund’s knowledge spans various types of fixtures, from decorative pieces to functional hardware, blending precision with creativity. His passion for metalworking and design has made him a trusted resource in the industry.
Professional Focus:
- Expert in Metal Fixtures : Edmund aesthetic specializes in creating durable and innovative metal fixtures, offering both appeal and functionality. His work reflects a deep understanding of metalworking techniques and materials.
- Sustainability Advocate : He is dedicated to using sustainable practices, ensuring that every fixture is crafted with eco-friendly methods while maintaining high-quality standards.
In his writing for Metal Fixes, Edmund provides valuable insights into the latest trends, techniques, and practical advice for those passionate about metal fixtures, whether they are professionals or DIY enthusiasts. His focus on combining artistry with engineering helps others discover the true potential of metal in design.