Are you tired of warping your body panels while trying to weld them? Welding body panels can be tricky, but with the proper techniques and tools, you can achieve a seamless and professional finish. Here, we will discuss how to weld body panels without warping, so you can confidently tackle any welding project on your vehicle.
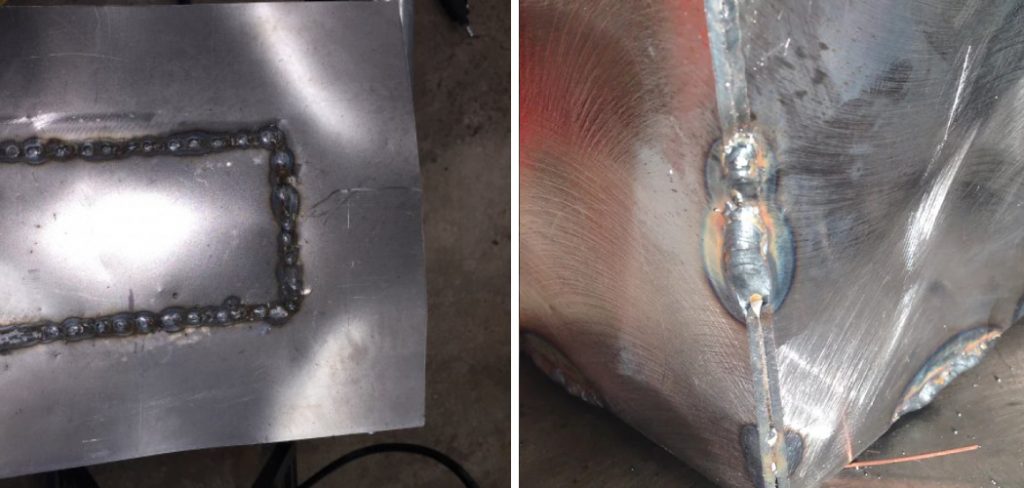
If you’re interested in undertaking body repairs on your vehicle, the task of welding is a crucial part of any build. As fun and challenging as it can be to weld body panels, if not done correctly, the result may leave them misshapen or warped beyond repair. Fortunately, there are approaches that auto enthusiasts can take to ensure that every cut looks pristine.
In this post, we will dive into welding techniques to help you preserve the integrity of your car’s body panels and avoid warping.
What Will You Need?
Before diving into the welding process, it’s essential to have all the necessary tools and equipment available to achieve the best results.
- Welding Machine: A welder is the most crucial tool for welding body panels. Using a MIG welder with the appropriate settings for thin sheet metal is recommended, as it provides better control and reduces the risk of warping.
- Angle Grinder: An angle grinder will help smooth out any rough edges or imperfections before welding.
- Clamps or Magnets: These tools help hold the panels in place and reduce movement while welding.
- Protective Gear: Always wear protective gear, including a welding helmet, gloves, and apron, to protect yourself from sparks and potential burns.
Once you have all the necessary tools, let’s get started on how to weld body panels without warping.
8 Easy Steps on How to Weld Body Panels Without Warping
Step 1: Clean the Panels
Before starting to weld, ensure the body panels are free of any dirt, rust, or paint. You can use a wire brush or sandpaper to clean the surface. This step is crucial as contaminants can affect the quality of the weld and increase the chances of warping. Once clean, wipe the panel with a degreasing agent to remove any residual oil or grease.
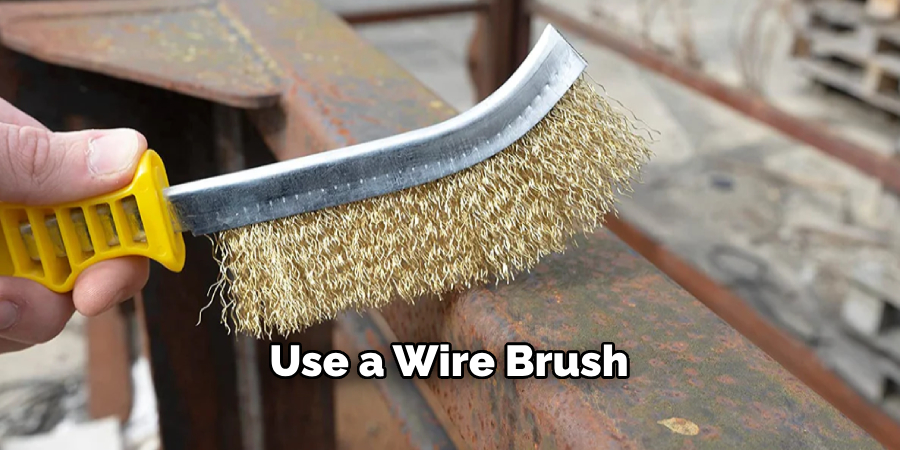
Step 2: Align the Panels
Proper alignment of the panels is crucial in preventing warping. Use clamps or magnets to firmly hold the panels in place, ensuring they’re lined up correctly.
It’s important to remember that any gaps between the panels may lead to excessive heat buildup, contributing to warping. Using a butt welding clamp can help maintain the proper alignment and gap. Once the panels are perfectly aligned, you’re ready to start the welding process.
Step 3: Begin the Welding Process
Start welding at the lowest setting that will still allow for a solid weld. This is typically referred to as tack welding. Aim to create a series of small welds, or “tacks,” about an inch apart along the length of the panel.
The key to preventing warping is to distribute the heat evenly across the panel, and by tack welding, you can avoid concentrating too much heat in one area. After making each tack, let the panel cool before moving on to the next spot. Patience during this process is critical to preventing warping and ensuring a high-quality result.
Step 4: Continue the Welding Process
Now that you have your first series of tacks, you can continue the welding process. It’s important to rotate your welding locations to ensure heat is evenly distributed and prevent warping. For example, if you start welding at the top of the panel, make your next weld at the bottom.
This alternating pattern will help maintain a balanced temperature across the panel. Remember to allow enough cooling time between each weld to reduce the risk of warping further.
Step 5: Inspect and Grind the Welds
After you have completed the welding, it’s time to inspect your work. Look for any inconsistencies or gaps in the welds. If there are any, you may need to add more weld to these areas, remembering to allow for cooling time to avoid warping.
Once you’re satisfied with the welding, use your angle grinder to grind down any excess material from the welds. This step will ensure a smooth, seamless finish to your panel. Be careful not to grind too much, as this could weaken the welds. After sanding, clean the panel to prepare it for priming and painting.
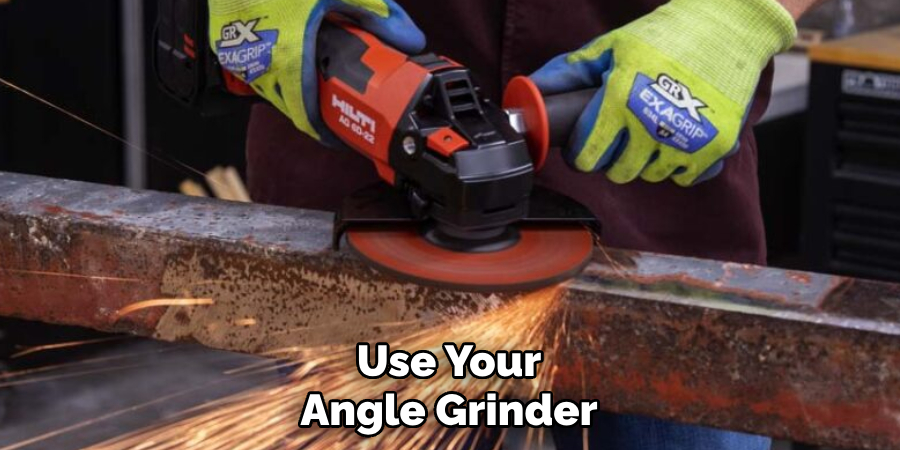
Step 6: Apply Primer and Paint
Once your panel is smooth and clean, it’s time to apply primer. This step is essential as it provides a base for the paint to adhere to, preventing rust and ensuring a smooth finish. Remember to apply multiple thin layers of primer, allowing each layer to dry before applying the next.
Once the primer is dry, you can start painting. As with the primer, it’s best to use the paint in several thin layers, allowing each layer to dry before applying the next. This process ensures a smooth, even finish. With the paint used and dried, you have completed welding a body panel without warping.
Step 7: Final Inspection and Polishing
After the paint has dried completely, it’s time for the final inspection. Scrutinize the panel, checking for any uneven areas of paint or small imperfections. If you find any, you can use fine-grit sandpaper to lightly smooth these areas.
Once satisfied with your paint job, apply a quality car wax to the panel. This step will preserve the paint and give your panel a glossy, professional finish. Using a soft cloth, apply the wax in circular motions, covering the entire panel. Allow the wax to dry, and then buff it with a clean cloth until you achieve a shiny finish.
Step 8: Regular Maintenance
After successful welding and painting, regular maintenance is crucial to keep your car’s body panels in the best condition. Make sure to keep the panels clean and free from dust or grime that could damage the paintwork.
Also, consider applying a paint protection film or wax regularly to preserve the shine and protect the panel from environmental elements. Regular checks for any signs of warping or damage are also essential, as early detection can prevent further complications and expensive repairs.
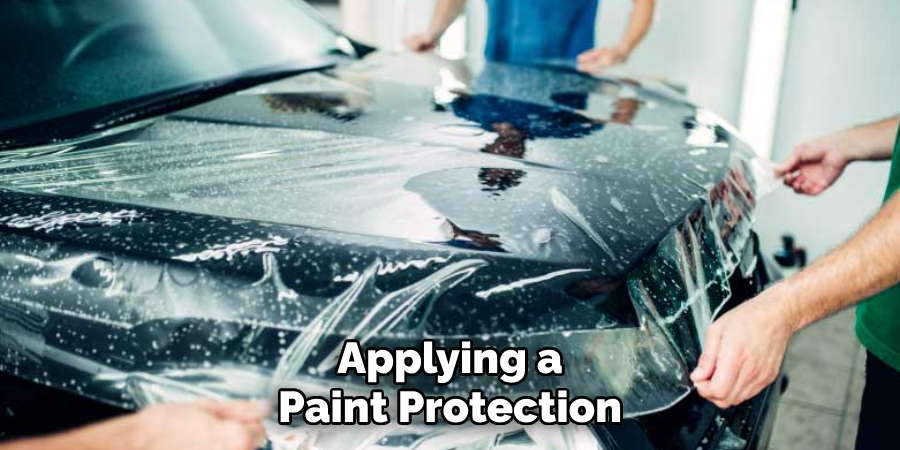
By following these steps, you now know to weld body panels without warping. Remember that patience, proper technique, and the right tools are essential in achieving a flawless result.
5 Additional Tips and Tricks
Tip 1: Practice Makes Perfect
Like any skill, welding takes time and practice to master. Start by practicing on scrap metal before moving onto car panels to develop your skills and gain confidence.
Tip 2: Use the Right Equipment
Having the right equipment can make a significant difference in your welding results. Invest in high-quality welding tools, such as a MIG or TIG welder, and use the appropriate settings for the type of metal you are working with.
Tip 3: Avoid Thick Metal
Welding thick metal can increase the risk of warping due to the higher heat required. If possible, use thinner metal for body panels as it will be easier to weld and less likely to warp.
Tip 4: Keep an Eye on Heat Buildup
Continuously monitor the temperature of your welds and take breaks if necessary to allow the panel to cool down. Excessive heat buildup can lead to warping, so it’s essential to take breaks and give the panel enough time to cool.
Tip 5: Seek Professional Help
If you are unsure about your welding abilities or have a particularly challenging project, don’t hesitate to seek help from a professional. They can offer valuable advice and ensure that your body panels are welded correctly without any risk of warping. Remember, it’s better to be safe than sorry about your car’s appearance and safety.
With these additional tips and tricks, you now have all the knowledge and skills to successfully weld body panels without warping.
5 Things You Should Avoid
Avoid 1: Rushing the Process
Avoid rushing the welding process. Patience and time are crucial to prevent warping. Allow enough time for each weld to cool before proceeding to the next.
Avoid 2: Skipping the Clean-Up
Do not skip the clean-up. Remove all rust, dirt, or oil from the panel before beginning to weld, as these can interfere with the quality and effectiveness of your weld.
Avoid 3: Inadequate Safety Measures
Never underestimate the importance of safety. Always use proper safety equipment, including gloves, a welding helmet, and a welding jacket, to protect yourself from sparks, UV radiation, and intense heat.
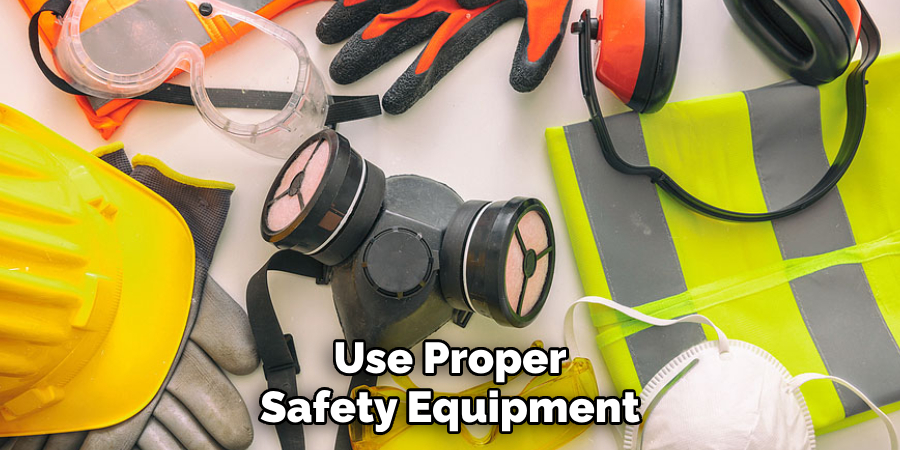
Avoid 4: Ignoring the Machine’s Settings
Avoid ignoring your welding machine’s settings. Ensure to use the appropriate settings for the type of metal and thickness you are working with to avoid damaging the panel or creating weak welds.
Avoid 5: Use of Incorrect Welding Technique
Avoid using incorrect welding techniques, such as pushing the weld instead of dragging it. This can lead to uneven and weak welds, which may result in warping or other issues down the line.
By avoiding these common mistakes, you can ensure a successful welding job without any risk of warping.
Conclusion
With this knowledge, you will be able to confidently weld any body panels without worrying about warping! Don’t let any of these techniques intimidate you; welding body panels takes practice and know-how, but following our guidelines can achieve superior results.
The challenge is worth undertaking when done with skill and flair, as it will mean your next car project is sure to turn heads. If you take the time to practice your welding tasks, soon you’ll be an expert at creating strong joints with perfect alignment.
Hopefully, the article on how to weld body panels without warping has equipped you with the necessary knowledge and skills to tackle any body panel welding job. Remember to be patient, use proper techniques and safety measures, and take your time to achieve a flawless result.
So what are you waiting for? Get out there and start welding up some unique body panels today!
Edmund Sumlin is a skilled author for Metal Fixes, bringing 6 years of expertise in crafting a wide range of metal fixtures. With a strong background in metalwork, Edmund’s knowledge spans various types of fixtures, from decorative pieces to functional hardware, blending precision with creativity. His passion for metalworking and design has made him a trusted resource in the industry.
Professional Focus:
- Expert in Metal Fixtures : Edmund aesthetic specializes in creating durable and innovative metal fixtures, offering both appeal and functionality. His work reflects a deep understanding of metalworking techniques and materials.
- Sustainability Advocate : He is dedicated to using sustainable practices, ensuring that every fixture is crafted with eco-friendly methods while maintaining high-quality standards.
In his writing for Metal Fixes, Edmund provides valuable insights into the latest trends, techniques, and practical advice for those passionate about metal fixtures, whether they are professionals or DIY enthusiasts. His focus on combining artistry with engineering helps others discover the true potential of metal in design.