Are you a craftsperson or hobbyist looking to perform impressive welding projects? Have you ever wanted to make durable repairs, create complex structures, and have the satisfaction of building something useful with your hands? We’d like to introduce you to one engineering process that lets you do just that – welding! With welding, the sky’s the limit for what can be achieved – and today we’ll be focusing on teaching you how to weld brass to steel.
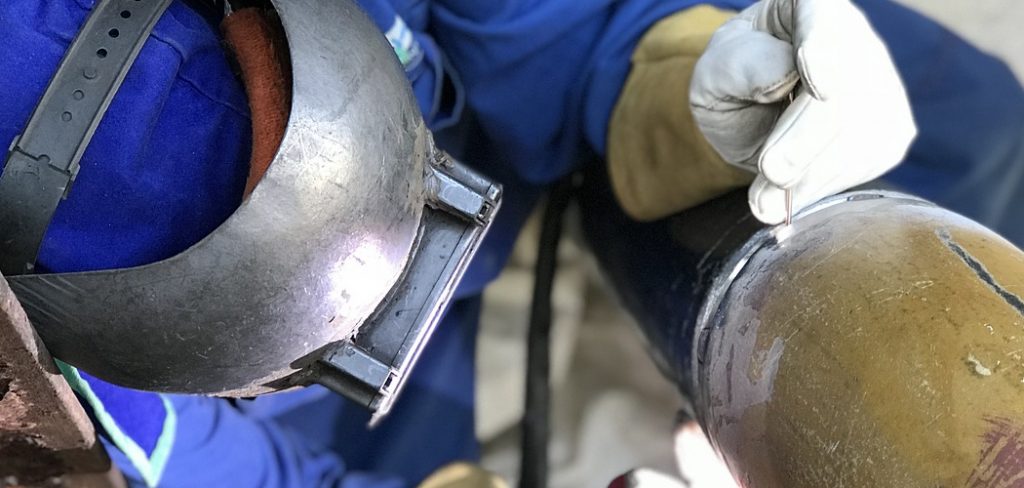
Regardless of whether this is your first time trying it out or if it’s been years since brushing up on certain techniques, our comprehensive guide will give all users an in-depth dive into understanding and implementing how this thought-provoking yet rewarding process works. Stick around because before long, you too will know all about successfully completing solid brass/steel welds!
Why Do We Need to Weld Brass to Steel?
Generally, you will be welding two pieces of metal together so that they are resistant to chemical and physical changes. Brass is an alloy made of copper and zinc, while steel is a mixture of iron with carbon. The reason for welding these two metals together is because it allows the combination of their unique properties – brass has superior corrosion resistance compared to steel, while steel is much stronger and harder than brass. This combination of properties makes it an ideal choice for various applications.
Preparing the Materials
Before starting any welding project, safety should always come first. Make sure you have all the necessary protective gear such as a welding helmet, heat-resistant gloves, and an apron. You should also have your welder machine in good condition with all its parts in place. Make sure you are working in a well-ventilated area with no flammable materials around.
Once you have taken all the necessary safety precautions, it’s time to prepare your materials for welding. For brass-to-steel welding, you will need a brass rod or filler metal that matches the composition of your brass, as well as a steel rod or filler metal that is compatible with your steel. A wire brush and an angle grinder may also be necessary to clean and prepare the metals for welding.
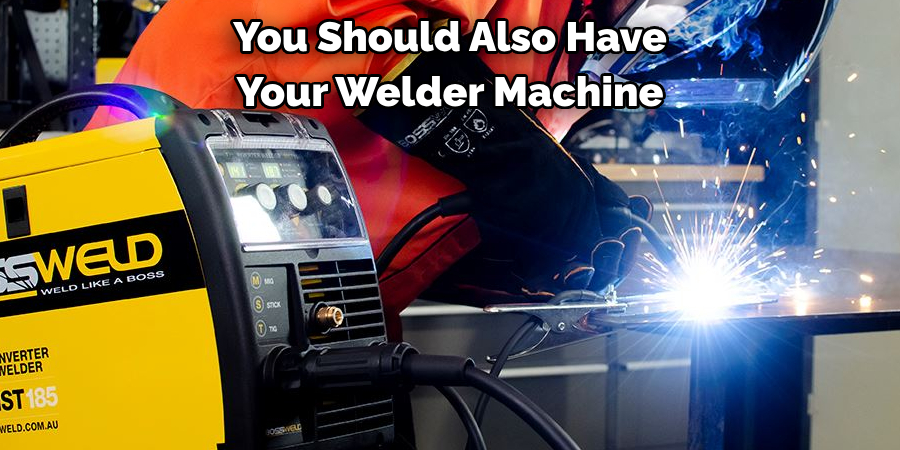
10 Step-by-step Guidelines on How to Weld Brass to Steel
Step 1: Choose the Right Welding Method
The most common welding method used for welding brass to steel is gas tungsten arc welding (GTAW), also known as TIG welding. This method provides the precise heat control and filler metal placement needed to effectively join these two dissimilar metals. It also produces clean and precise welds, making it ideal for decorative or precision welding. It is important to note that TIG welding requires a high level of skill and practice, so it may not be suitable for beginners. Other welding methods such as gas metal arc welding (GMAW) or stick welding can also be used, but they may not produce the same quality of results.
Step 2: Clean the Metals
Before starting to weld, make sure both the brass and steel surfaces are free from any rust, dirt, or debris. Use a wire brush or angle grinder to remove any impurities and ensure both surfaces are clean and shiny. It is crucial to have clean surfaces for the welding process to be successful. It is also recommended to use a degreaser or acetone to remove any oils from the surfaces, as they can cause welding defects.
Step 3: Clamp the Metals Together
Using clamps or vice grips, hold the brass and steel pieces firmly in place. This will help keep them stable during the welding process. You can also use magnets or metal clips to hold the pieces together if clamps are not available. But make sure they are located away from the welding area to avoid any interference. It is essential to have a tight and secure fit between the two materials for a successful weld.
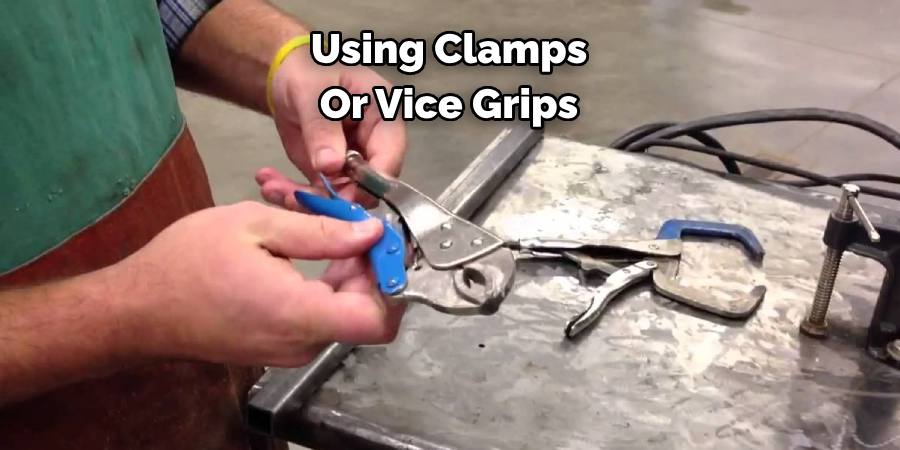
Step 4: Choose the Filler Metal
Select a filler metal that matches the composition of your brass. For example, if your brass alloy contains 70% copper and 30% zinc, then you should choose a filler metal with similar proportions. This will ensure compatibility and prevent any metallurgical issues. It is also recommended to use a brass filler metal with lower melting points than the steel rod, as it will allow the brass to melt and fuse with the steel without overheating or damaging it.
Step 5: Prepare the Filler Metal
Before using the filler metal, remove any oxidized layer by scraping it off or cleaning it with a wire brush. This will ensure that only clean and pure filler metal is used for welding, which promotes better fusion and reduces the chances of defects. If you are using a brass filler metal, it is also recommended to preheat it before welding by placing it in the oven at around 350-400 degrees Fahrenheit.
Step 6: Start Welding
Using your chosen welding method, start the process by creating an arc between the two materials. Move the torch or electrode in a circular motion to evenly distribute heat and add the filler metal in between the two materials. Remember to keep a steady hand and maintain proper arc length to prevent overheating, which can cause warping or burning of the materials. It is also crucial to maintain a clean and consistent weld pool for a successful fusion.
Step 7: Control Heat Input
As brass is a relatively softer metal compared to steel, it can quickly overheat and lose its structural integrity. To prevent this, control the heat input by welding in short intervals and allowing the materials to cool down between each pass. It is also recommended to use a lower amperage setting for brass compared to steel. You can also use copper heat sinks or wet rags to help dissipate excess heat and protect the brass.
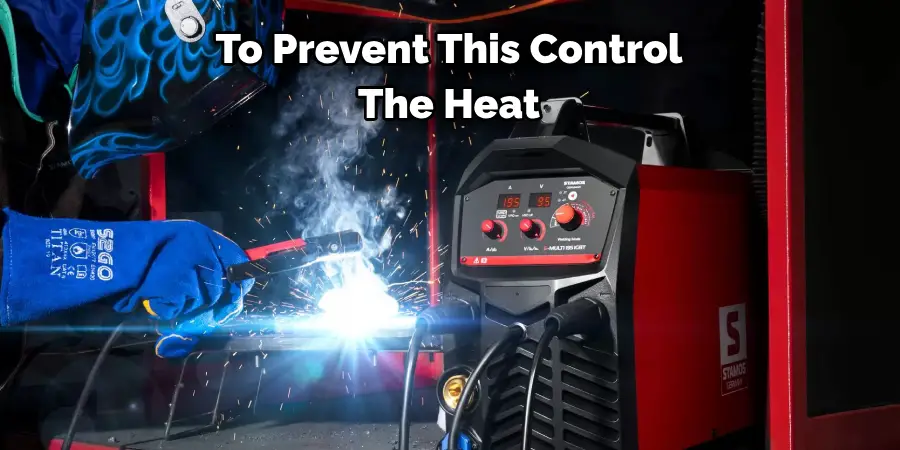
Step 8: Ensure Proper Fusion
As you weld, keep an eye on the color of the filler metal and the welded joint. A successful weld should have a smooth and consistent appearance with no cracks or voids. If there are any signs of poor fusion, stop and re-clean the materials before continuing. The fusion between the brass and steel should be strong and free from any porosity or inclusions.
Step 9: Post-Weld Cleaning
Once you have completed your weld, let the materials cool down before removing any clamps or magnets. Use a wire brush to remove any excess flux or slag that may have formed during welding. You can also use an angle grinder to clean and smooth out any rough edges or uneven areas. It is important to remove all debris from the weld area before moving on to any further finishing processes.
Step 10: Finishing Touches
After welding, you can finish the joint by polishing or buffing it to achieve a smooth and shiny appearance. You can also use a patina solution to add a decorative finish or to match the color of your brass and steel. Remember to always wear protective gear and follow safety precautions during all welding processes. It is also recommended to test the strength and integrity of the weld before using it for any load-bearing applications.
Following these step-by-step guidelines on how to weld brass to steel will help you successfully weld brass to steel and achieve strong and durable joints. With the right tools, materials, and techniques, you can create beautiful and functional pieces that combine the strength of steel with the elegance of brass. So go ahead and experiment with your welding skills to create unique and intricate designs that showcase the versatility of these two metals.
Frequently Asked Questions
Q1: Is It Possible to Weld Brass and Steel Together?
A1: Yes, with the right welding method and techniques, you can successfully join these two dissimilar metals. It requires skill and practice, but the results can be strong and durable joints.
Q2: Can I Use Any Welding Method?
A2: While TIG welding is the preferred method for brass to steel, other methods such as GMAW or stick welding can also be used. However, they may not produce the same quality of results.
Q3: How Do I Choose the Right Filler Metal?
A3: It is important to choose a filler metal that matches the composition of your brass. You should also consider using a lower melting point filler metal compared to the steel rod for better fusion and to prevent overheating.
Q4: What Safety Precautions Should I Take?
A4: Always wear protective gear such as gloves, goggles, and a welding helmet. Make sure the work area is well-ventilated and free from any flammable materials. Follow all safety precautions recommended by your welding machine’s manufacturer. So, these are some common queries that people have regarding welding brass to steel.
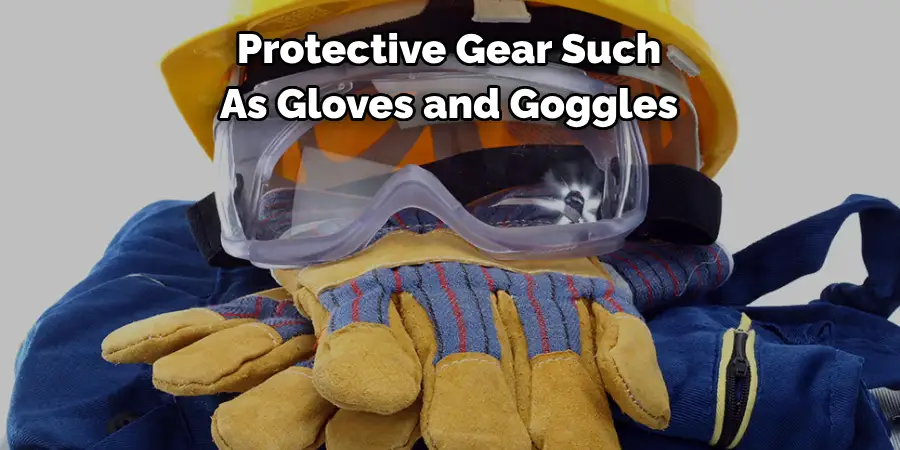
Conclusion
Whether you’re a welding novice or a long-time professional, when it comes to welding brass to steel there’s no denying that preparation is key. Taking the time to research and understand the materials, tools, and techniques can not only help you save time and energy in the short term but could prevent costly mistakes in the long run.
By considering all of these factors, you will be able to start your project confidently knowing that you will be successful in joining pieces of brass and steel together. Don’t forget to strive for precision during each step of the process so that your welds are more robust. Lastly, take your time with each weld as practice will help you improve your technique along the way. So don’t wait any longer; start planning today on how you will tackle this unique welding project and get ready to become a pro brass welder! Thanks for reading this article on how to weld brass to steel.
Edmund Sumlin is a skilled author for Metal Fixes, bringing 6 years of expertise in crafting a wide range of metal fixtures. With a strong background in metalwork, Edmund’s knowledge spans various types of fixtures, from decorative pieces to functional hardware, blending precision with creativity. His passion for metalworking and design has made him a trusted resource in the industry.
Professional Focus:
- Expert in Metal Fixtures : Edmund aesthetic specializes in creating durable and innovative metal fixtures, offering both appeal and functionality. His work reflects a deep understanding of metalworking techniques and materials.
- Sustainability Advocate : He is dedicated to using sustainable practices, ensuring that every fixture is crafted with eco-friendly methods while maintaining high-quality standards.
In his writing for Metal Fixes, Edmund provides valuable insights into the latest trends, techniques, and practical advice for those passionate about metal fixtures, whether they are professionals or DIY enthusiasts. His focus on combining artistry with engineering helps others discover the true potential of metal in design.