Do you have a passion for repairing old machinery or restoring vintage cars? If so, then you probably know the challenges that come with welding cast iron. This material has been used in various industries for decades and is known for its durability and strength.
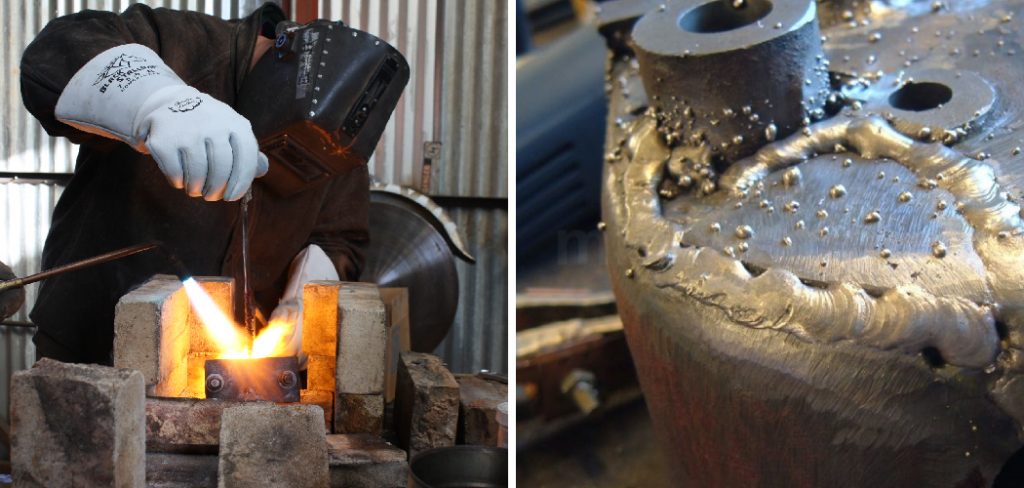
However, when it comes to welding, cast iron can be a tricky beast to tame. With its high carbon content and low melting point, traditional welding methods such as stick or TIG may lead to cracking and distortion. But fear not!
In this blog post on how to weld cast iron with mig welder, we will explore how to effectively weld cast iron with a MIG welder – an affordable and versatile tool that can deliver strong and clean welds on this complex metal. So grab your safety gear and let’s dive into the fascinating art of welding cast iron!
What is a MIG Welder?
MIG (Metal Inert Gas) welding, also known as Gas Metal Arc Welding (GMAW), is a semi-automated welding process that uses a consumable wire electrode and an inert gas to melt the workpiece and create a weld pool. The wire acts as both the filler metal and the electrode, while the gas protects the weld pool from atmospheric contamination.
MIG welding is widely used in various industries due to its ease of use, high welding speed, and ability to create strong joints. It is also the preferred method for welding cast iron.
11 Step-by-step Guidelines on How to Weld Cast Iron With Mig Welder
Step 1: Safety First
As with any welding project, safety should be your top priority. Welding cast iron produces a lot of heat and sparks, so make sure to wear a welding helmet, gloves, and protective clothing.
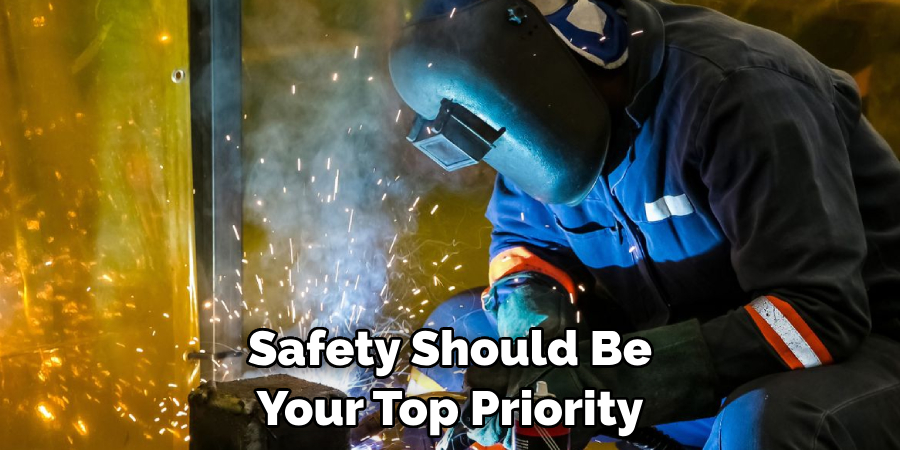
You should also have a fire extinguisher nearby in case of any accidents. But most importantly, make sure to work in a well-ventilated area to avoid inhaling harmful fumes. The use of a respirator is also recommended.
Step 2: Prepare the Workpiece
Before you start welding, make sure to clean the cast iron surface thoroughly. Use a wire brush or sandpaper to remove any rust, dirt, or paint. This will ensure a clean and smooth welding surface.
You can also preheat the cast iron to around 500°F (260°C) to reduce the chances of cracking. it is essential to clean the workpiece both before and during welding to prevent contamination and ensure a strong weld.
Step 3: Set Up Your MIG Welder
Next, set up your MIG welder according to the manufacturer’s instructions. This includes selecting the right wire electrode and gas mixture for welding cast iron. You will need a high nickel alloy wire, such as ENiFe-CI or ENiCl-A, and a shielding gas with a high argon content (around 95%) to shield the weld pool from oxygen and moisture.
Use a smaller wire diameter for thinner cast iron pieces and increase it for thicker ones. If your MIG welder has pulse settings, make sure to use them for better control and heat input.
Step 4: Choose the Right Welding Technique
When welding cast iron with a MIG welder, the recommended technique is short-circuiting transfer. This means that the wire electrode makes brief contact with the workpiece before retracting, creating a series of small welds. This technique produces less heat and helps prevent cracking. However, if you are welding thicker sections, you may need to use a spray arc method.
Step 5: Tack Weld if Necessary
If you are joining two pieces of cast iron, it is recommended to tack weld them in place before starting the main weld. This will hold the pieces together and prevent distortion during welding. The tacks should be small and spaced evenly to avoid creating stress points.
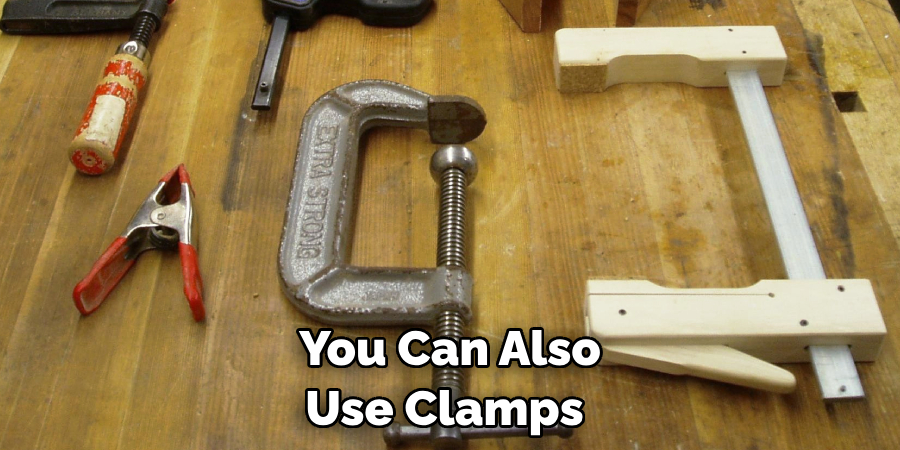
You can also use clamps or magnets to hold the pieces in place. The tacks can be ground down after the main weld is completed. It is crucial to use the same welding technique for tacking and main welding.
Step 6: Start Welding
Position the MIG gun at a 15-45 degree angle and aim it at the edge of the joint. Press the trigger to start welding, and make sure to maintain a consistent travel speed. Avoid weaving or pausing in one spot, as this can lead to uneven welds and potential cracking. Use a push or drag technique, depending on your preference and the thickness of the cast iron. It is also crucial to keep the weld pool small to avoid overheating the material.
Step 7: Monitor the Heat
As mentioned earlier, cast iron is prone to cracking due to its low melting point. Therefore, it is crucial to keep an eye on the heat buildup during welding. You can use a temperature-indicating pen or a heat gun to monitor the temperature. If it exceeds 1400°F (760°C), stop welding and let the piece cool down before continuing. But remember, preheating the cast iron can help prevent this issue.
Step 8: Make Multiple Passes
To create a strong and clean weld, you may need to make multiple passes on thicker sections of cast iron. This ensures that the weld penetrates deep into the workpiece and creates a solid joint.
Make sure to clean the weld between passes to remove any slag or debris. You can also use a chipping hammer or wire brush to remove any excess weld metal. The final weld should be smooth and uniform.
Step 9: Peen the Weld
Once you have completed all your passes, let the weld cool down before peening it. This process involves using a hammer to tap lightly on the welded joint, helping relieve stress and preventing cracking. The peening should be done while the weld is still warm but not too hot to touch. The peening should be continuous and evenly distributed. You can also use a peen hammer or vibrating tool for this step.
Step 10: Post-Weld Cleaning
After welding, let the piece cool down before cleaning it. Use a wire brush or grinder to remove any slag or spatter from the weld surface. You can also use a solvent or degreaser to remove any remaining contaminants.
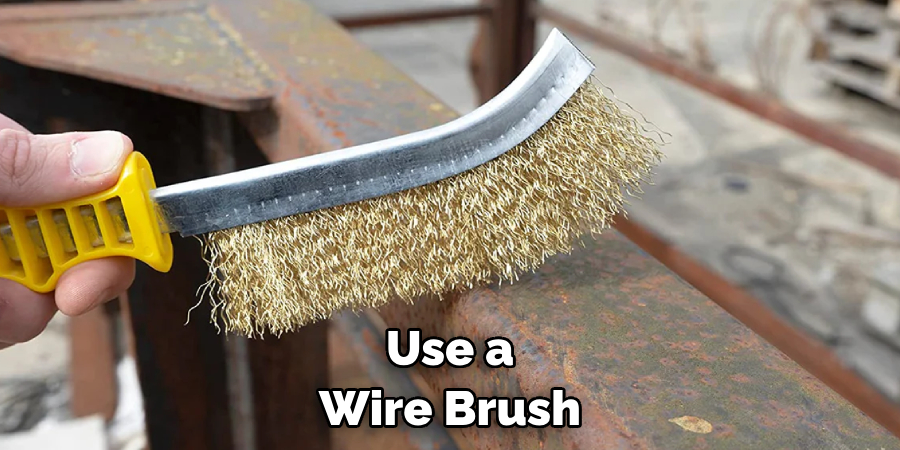
This will ensure a smooth and clean weld that is ready for further finishing. It is also essential to clean the weld to prevent rusting and maintain its strength. It is also crucial to inspect the weld for any defects that may need further repair.
Step 11: Post-Weld Heat Treatment
For the best results, it is recommended to subject the welded cast iron piece to post-weld heat treatment. This involves heating the piece in an oven or using a gas torch until it reaches around 1300°F (704°C) and then slowly cooling it down.
This process helps relieve any residual stresses and increases the weld’s strength and ductility. But if you preheated the cast iron before welding, post-weld heat treatment may not be necessary.
Following these 11 steps on how to weld cast iron with mig welder will allow you to successfully weld cast iron with a MIG welder. However, it is important to note that welding cast iron can be challenging and may require some practice.
Do You Need to Use Professionals?
While welding cast iron with a MIG welder is possible, it may be best to leave this task to professionals. Cast iron is a delicate and challenging material to work with, and improper welding can cause damage or even break the piece.
Therefore, if you are not experienced in welding or do not have the necessary equipment, it is recommended to seek professional help for this type of project. They have the expertise and experience to ensure a successful weld without compromising the integrity of the cast iron piece.
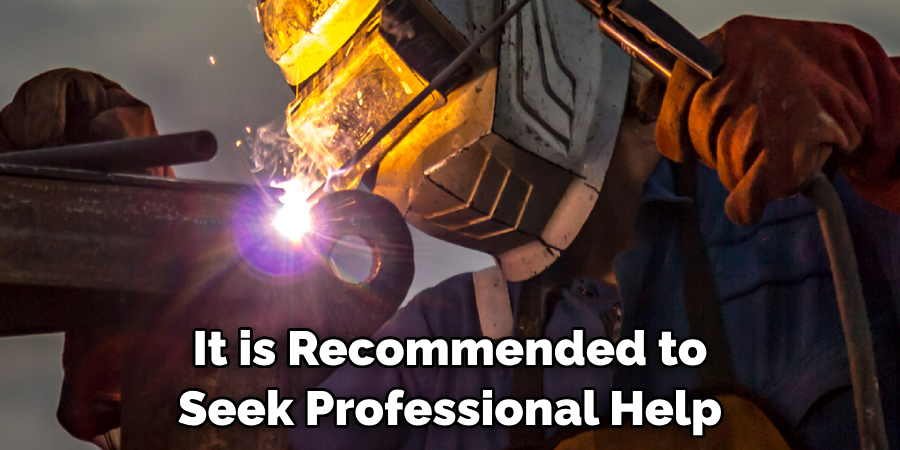
How Much Will It Cost?
The cost of welding cast iron with a MIG welder can vary depending on the size and complexity of the project, as well as the expertise of the professional you hire. It is best to get quotes from different professionals to compare prices and ensure that you are getting a fair deal. Keep in mind that the cost may also include additional steps such as preheating and post-weld heat treatment, as well as any necessary repairs.
Frequently Asked Questions
Q: Can I Weld Cast Iron With a Mig Welder if It is Not Specifically Designed for It?
A: It is not recommended to use a MIG welder that is not specifically designed for welding cast iron. This can lead to poor weld quality, cracking, and other issues. You should always consult with the manufacturer’s recommendations before attempting to weld cast iron with a MIG welder.
Q: What Causes Cast Iron to Crack During Welding?
A: Cast iron has a low melting point and is prone to cracking due to the high heat produced during welding. This can also be caused by improper preheating, using the wrong filler material or technique, or welding on a contaminated surface. It is essential to follow the correct procedures and techniques when welding cast iron.
Q: Can I Weld Different Types of Cast Iron Together?
A: Yes, you can weld different types of cast iron together as long as they have similar compositions and are compatible with the same filler material and technique. However, it is recommended to consult with a professional welder or the manufacturer’s recommendations before attempting to weld different types of cast iron together.
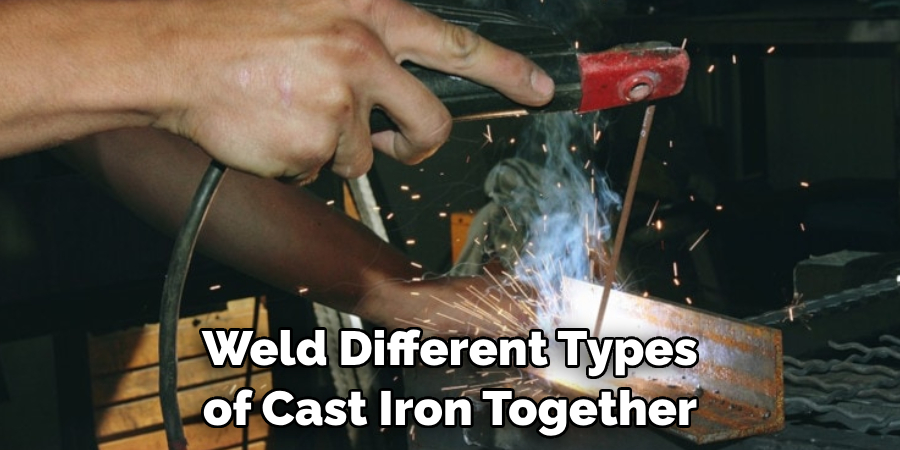
Q: Is It Possible to Weld Cracked Cast Iron?
A: Yes, it is possible to weld cracked cast iron. However, this can be challenging and may require special techniques such as preheating, post-weld heat treatment, and peening to ensure a successful weld. It is recommended to consult with a professional welder for the best approach to repairing cracked cast iron.
Conclusion
In conclusion, welding cast iron with a MIG welder may seem like a daunting task, but with the right techniques and equipment, it can be done effectively and efficiently. By following the steps outlined in this post on how to weld cast iron with mig welder, you can not only save yourself time and money by repairing damaged cast iron pieces yourself, but also ensure that the welded joint is strong and durable.
Remember to always take the necessary safety precautions and never rush through the process. As the saying goes, “measure twice, cut once” applies here too – taking your time to properly clean and prepare the surface before welding will result in a stronger bond.
And don’t be afraid to practice on scrap pieces before attempting a repair on an important or expensive object. With patience and practice, you’ll soon become a pro at welding cast iron with a MIG welder. So go ahead and put these tips into action – your broken cast iron tools and machinery will thank you!
Edmund Sumlin is a skilled author for Metal Fixes, bringing 6 years of expertise in crafting a wide range of metal fixtures. With a strong background in metalwork, Edmund’s knowledge spans various types of fixtures, from decorative pieces to functional hardware, blending precision with creativity. His passion for metalworking and design has made him a trusted resource in the industry.
Professional Focus:
- Expert in Metal Fixtures : Edmund aesthetic specializes in creating durable and innovative metal fixtures, offering both appeal and functionality. His work reflects a deep understanding of metalworking techniques and materials.
- Sustainability Advocate : He is dedicated to using sustainable practices, ensuring that every fixture is crafted with eco-friendly methods while maintaining high-quality standards.
In his writing for Metal Fixes, Edmund provides valuable insights into the latest trends, techniques, and practical advice for those passionate about metal fixtures, whether they are professionals or DIY enthusiasts. His focus on combining artistry with engineering helps others discover the true potential of metal in design.